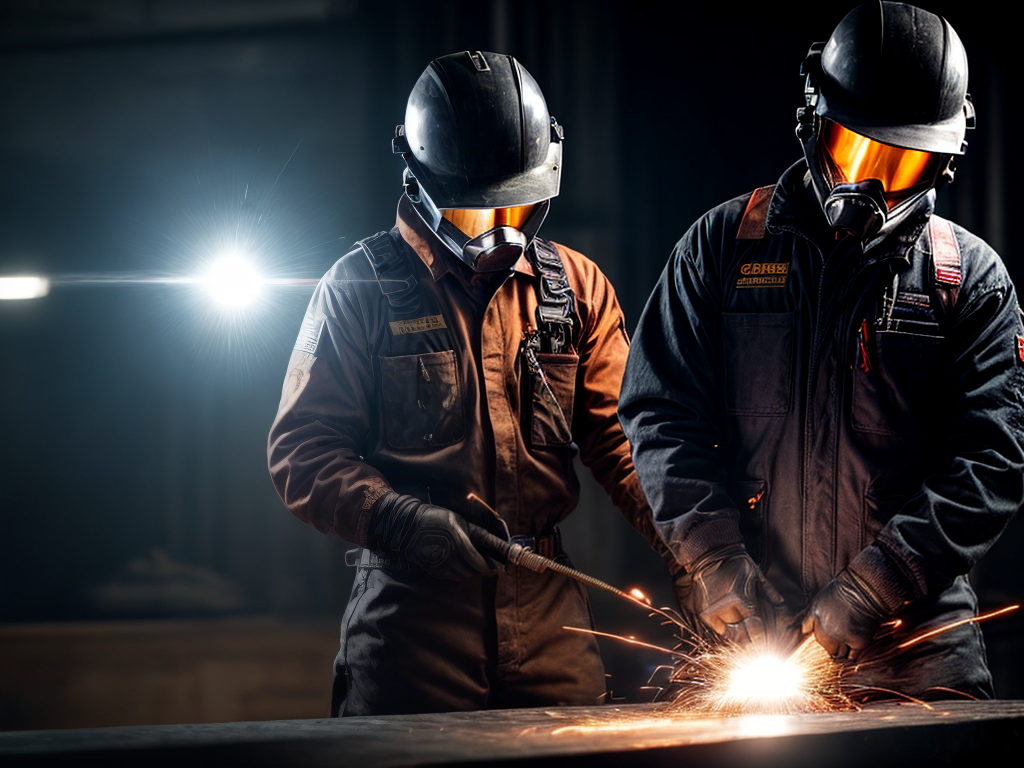
As a seasoned welder, I understand the importance of safety when it comes to my craft. That’s why I have compiled a list of the top 10 welding safety checklists that every welder should know and follow. These checklists cover a wide range of areas, including personal protective equipment, welding area safety, pre-welding equipment inspection, fire prevention measures, electrical safety precautions, proper handling and storage of welding materials, safe welding techniques, emergency preparedness and first aid, and regular equipment maintenance and calibration. By adhering to these checklists, you can ensure a safe and secure welding environment, protecting yourself and those around you. So let’s dive in and make safety our top priority in the world of welding.
Personal Protective Equipment (PPE)
As a welder, I rely on personal protective equipment (PPE) to ensure my safety during welding operations. PPE regulations play a crucial role in maintaining a safe working environment. These regulations outline the specific types of PPE that must be worn, such as welding helmets, gloves, and protective clothing. Adhering to these regulations is essential to prevent potential injuries or accidents. Additionally, proper maintenance of PPE is of utmost importance. Regular inspections and cleaning of PPE ensure that it is in good working condition and provides the necessary protection. Any damaged or worn-out PPE should be immediately replaced to maintain its effectiveness. By following PPE regulations and conducting regular maintenance, I can confidently perform my welding tasks while prioritizing my safety.
Welding Area Safety
One important aspect of welding safety is ensuring a clean and organized welding area. A well-organized welding area not only promotes efficiency but also reduces the risk of accidents and injuries. To maintain a safe welding area, it is crucial to have a proper welding area layout. This includes having designated spaces for different welding processes and equipment, as well as clear pathways to prevent tripping hazards. Additionally, it is important to adhere to hot work permits. Hot work permits help identify potential hazards and ensure that necessary precautions are taken before starting any welding activities. By following proper welding area layout and obtaining hot work permits, welders can create a safe and productive environment for themselves and their colleagues.
Pre-Welding Equipment Inspection
Before starting any welding activities, it is crucial for me to conduct a thorough inspection of the equipment. Proper welding equipment maintenance is essential to ensure safety and efficiency during the welding process. To begin, I check the cables and connections for any signs of damage or wear. Next, I inspect the welding machine for any loose or damaged parts. It is also important to verify that the machine is properly grounded. Additionally, I inspect the welding helmet to ensure it is in good condition and provides adequate protection. Lastly, I check the gas cylinders for leaks and verify that they are securely fastened. By following this pre-welding safety checklist, I can minimize the risk of accidents and ensure a successful welding operation.
Fire Prevention Measures
After conducting a thorough pre-welding equipment inspection, I implement essential fire prevention measures to further ensure the safety of the welding process. One crucial measure is having a fire extinguisher readily available at all times. This allows me to quickly extinguish any fires that may occur during welding operations. Additionally, obtaining hot work permits before starting any welding activities is vital. These permits ensure that proper safety precautions are in place, such as fire-resistant barriers and fire watch personnel. By following these measures, I can minimize the risk of fires and protect both myself and those around me. Fire prevention is a critical aspect of welding safety that should never be overlooked.
Electrical Safety Precautions
To ensure my safety and minimize the risk of electrical hazards, I take necessary precautions when working with welding equipment. Electrical safety is crucial in welding, as it involves working with high voltage power sources. By using the right electrical safety equipment and being aware of common electrical hazards, I can protect myself and others from potential accidents. Here are some key electrical safety precautions to follow:
Electrical Safety Equipment | Common Electrical Hazards |
---|---|
Insulated gloves | Electrical shock |
Safety glasses | Short circuits |
Insulated tools | Overloading circuits |
Grounding devices | Arc flash incidents |
Lockout/tagout procedures | Faulty wiring |
Ventilation and Fume Extraction
Maintaining proper ventilation and implementing effective fume extraction is crucial for ensuring a safe welding environment. Indoor air quality can be significantly impacted by the fumes and gases generated during the welding process. These fumes can contain hazardous substances like manganese, chromium, and nickel, which can pose serious health risks if inhaled. To protect myself from these harmful fumes, I must prioritize respiratory protection. This can include wearing a properly fitted respirator that is specifically designed for welding applications. Additionally, I should ensure that the welding area is well-ventilated by using exhaust fans or opening windows and doors. Regularly monitoring and maintaining the ventilation system is also important to ensure its effectiveness in removing welding fumes and maintaining a healthy work environment.
Proper Handling and Storage of Welding Materials
I handle and store welding materials with care to ensure safety. When it comes to handling precautions, I always wear proper personal protective equipment, such as gloves, goggles, and a welding helmet, to protect myself from potential hazards. I also make sure to handle materials with clean and dry hands, as moisture or grease can affect the quality of the weld. As for material storage guidelines, I store them in a cool, dry, and well-ventilated area to prevent moisture absorption and minimize the risk of fire. I keep flammable materials away from heat sources and ensure proper labeling and segregation of different types of materials. Following these handling precautions and material storage guidelines helps me maintain a safe working environment and prevent accidents.
Safe Welding Techniques
When handling and storing welding materials safely, it is essential to also employ safe welding techniques. To ensure a secure welding environment, it is crucial to receive proper welding safety training and adhere to the recommended guidelines. One key aspect of safe welding is maintaining proper body positioning. This involves positioning yourself in a way that provides maximum stability and reduces the risk of injury. By keeping your body balanced and your feet shoulder-width apart, you can enhance your stability and prevent unnecessary strain on your body. Additionally, maintaining a comfortable stance and keeping your head and body aligned with the welding area will enable better control and accuracy during the welding process. Practicing safe welding techniques not only protects you from potential hazards but also enhances the quality of your work.
Emergency Preparedness and First Aid
In case of emergencies, it is crucial for every welder to be prepared and equipped with the necessary first aid knowledge and supplies. As a welder, being trained in emergency response and injury prevention is essential to ensure the safety and well-being of yourself and others in the workplace. Accidents can happen at any time, and having the proper skills and resources can make a significant difference in the outcome. It is important to have a well-stocked first aid kit readily available, as well as knowing how to administer basic first aid techniques. Below is a table outlining some key first aid supplies and techniques that every welder should be familiar with:
First Aid Supplies | First Aid Techniques |
---|---|
Bandages | CPR |
Antiseptic ointment | Control bleeding |
Burn cream | Splinting fractures |
Regular Equipment Maintenance and Calibration
To ensure optimal performance and safety, I regularly maintain and calibrate my welding equipment. Equipment troubleshooting is an essential part of my routine, as it helps me identify and address any issues that may affect the quality of my welds. By conducting regular inspections, I can detect signs of wear and tear, loose connections, or faulty components. This allows me to take immediate action and prevent any potential accidents or equipment failures. Additionally, I make sure to follow the manufacturer’s guidelines for welding machine maintenance, which includes cleaning, lubrication, and replacing consumables as needed. By dedicating time to regular equipment maintenance and calibration, I can rely on my equipment to perform at its best, ensuring both my safety and the quality of my welds.