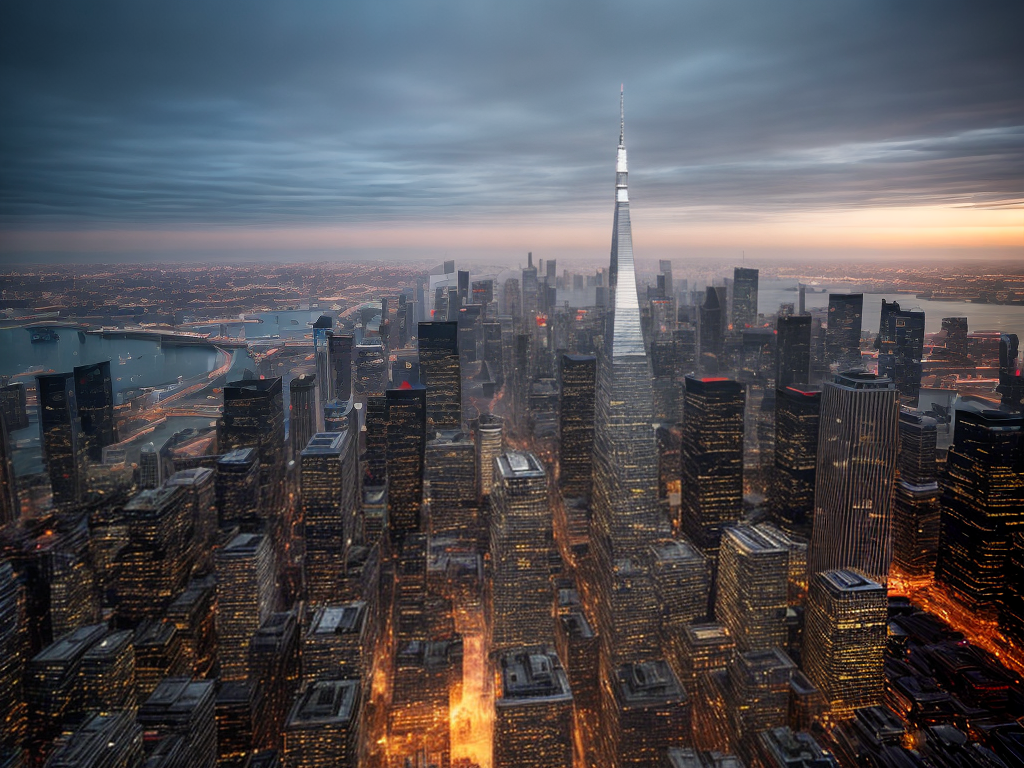
When it comes to welding, the highest skyscrapers are my playground. In “Welding the Tallest Skyscrapers: Techniques and Tales,” I dive into the world of welding in the realm of monumental architecture. This book is a comprehensive guide for those seeking mastery in the art of skyscraper welding. From the various techniques utilized to the remarkable feats accomplished by fearless welders, every aspect is explored. Not without its challenges, the construction of towering skyscrapers demands unwavering attention to safety measures. Through captivating tales and innovative advancements, we delve into the future of welding in skyline engineering. Join me on this journey as we uncover the secrets behind welding the world’s tallest structures.
The Role of Welding in Skyscraper Construction
Throughout my career as a welder, I have witnessed firsthand the indispensable role that welding plays in the construction of towering skyscrapers. The use of specialized welding equipment and the mastery of certain skills are vital for the successful completion of these massive structures. Welding equipment, such as welding machines, torches, and protective gear, is essential for ensuring the safety and efficiency of the welding process. Additionally, skill requirements for welders working on skyscraper construction projects include expertise in various welding techniques, such as arc welding, MIG welding, and TIG welding. Precision, attention to detail, and the ability to interpret blueprints and technical drawings are also crucial skills. Without the proper equipment and skills, the construction of these magnificent skyscrapers would not be possible.
Types of Welding Techniques Used
One of the most commonly used welding techniques in skyscraper construction is arc welding. This technique utilizes a welding equipment called an arc welder, which creates an electric arc between the base metal and the electrode. The intense heat generated by the arc melts both the base metal and the electrode, creating a weld pool that solidifies into a strong joint. Arc welding is preferred in skyscraper construction due to its versatility and ability to weld various types of metals, including steel and aluminum. To perform arc welding in skyscraper construction, welders must possess the necessary welding certifications, ensuring their competence in handling the welding equipment and executing the technique safely and effectively. These certifications validate their knowledge and skills, guaranteeing the high quality and structural integrity of the welded joints in the tallest skyscrapers.
Challenges Faced by Welders in Skyscraper Projects
As a welder working on skyscraper projects, I face numerous challenges that require utmost caution and preparedness. One of the main concerns is ensuring safety precautions are followed to protect myself and my fellow workers from accidents and injuries. Additionally, extreme weather conditions such as strong winds and extreme temperatures pose significant challenges that must be overcome to ensure the quality and integrity of the welds.
Safety Precautions for Welders
I prioritize safety by implementing rigorous precautions and navigating the unique challenges faced by welders in skyscraper projects. When it comes to preventing accidents, proper use of protective equipment is crucial. Welders must wear personal protective equipment (PPE) such as welding helmets, safety glasses, fire-resistant clothing, and gloves to shield themselves from sparks, heat, and UV radiation. Additionally, ventilation systems and respiratory protection are essential to minimize exposure to harmful fumes and gases. Working at heights presents its own set of challenges, so fall protection systems like harnesses and safety nets are employed to minimize the risk of falls. Adhering to strict safety protocols and staying updated on the latest safety practices ensures that welders are able to carry out their work safely and efficiently.
Preventing Accidents | Protective Equipment | Challenges |
---|---|---|
Proper use of PPE | Welding helmets | Working at heights |
Ventilation systems | Safety glasses | Exposure to fumes and gases |
Fall protection systems | Fire-resistant clothing | Risk of falls |
Gloves | ||
Respiratory protection |
Extreme Weather Conditions
To tackle the challenges posed by extreme weather conditions in skyscraper projects, it is crucial for welders to adapt their techniques and equipment accordingly. When it comes to extreme weather, such as high winds, intense heat, or freezing temperatures, welders must take extra precautions to ensure the safety and quality of their work. Firstly, selecting the right welding equipment is essential. For example, using welding machines with built-in weather protection can prevent damage from rain or snow. Additionally, welders need to obtain the necessary welding certifications that demonstrate their competence in handling adverse weather conditions. These certifications not only ensure the welder’s proficiency but also provide reassurance to project managers and clients that the job will be carried out safely and effectively, even in extreme weather.
Safety Measures in Skyscraper Welding
Skyscraper welding requires meticulous adherence to safety measures. When working at such heights, it is imperative to prioritize the safety of both the welders and the structure itself. This begins with the proper use of welding equipment. Ensuring that all equipment is well-maintained and in good working condition is crucial to prevent accidents. Additionally, welders must possess the necessary welding certifications. These certifications validate their skills and knowledge, guaranteeing that they are capable of executing the job safely and effectively. By being certified, welders are trained to understand potential hazards and take appropriate precautions. Safety measures, such as wearing protective gear and harnesses, are also strictly enforced. In the realm of skyscraper welding, safety is non-negotiable, and every precaution must be taken to protect lives and maintain the integrity of these magnificent structures.
Tales of Remarkable Welding Feats in Skyscrapers
One of the most memorable moments in my career as a skyscraper welder was when I successfully joined two massive steel beams at an astonishing height. It was a testament to the remarkable welding achievements in the history of skyscrapers. In the early 20th century, during the construction of the Empire State Building, welders faced incredible challenges. They had to work without safety harnesses, relying solely on their skills and courage. One iconic anecdote tells the story of a welder who fearlessly welded beams while balancing on a narrow girder, hundreds of feet above the ground. These historical welding anecdotes serve as a reminder of the extraordinary feats accomplished by the brave men and women who shaped the skylines of our cities.
Welding Innovations for Skyscraper Construction
During my time as a skyscraper welder, I have witnessed firsthand the remarkable welding innovations that have revolutionized the construction of these towering structures. The use of innovative materials has been a game-changer in the industry. Advanced alloys such as high-strength steel and titanium have replaced traditional materials, allowing for stronger and lighter structures. These materials not only enhance the structural integrity of skyscrapers but also contribute to their aesthetic appeal. Additionally, automation advancements have significantly improved the efficiency and precision of welding processes. Robots equipped with advanced sensors and algorithms can now perform complex welding tasks with minimal human intervention. This not only speeds up construction but also ensures consistent and high-quality welds. These welding innovations have undoubtedly propelled skyscraper construction into a new era of safety, durability, and efficiency.
The Future of Welding in Skyline Engineering
As a skyscraper welder, I anticipate even more exciting advancements in the future of welding for skyline engineering. One area that holds great promise is robotic welding. With the development of advanced robotics technology, we can expect to see more automation in the welding process. Robots can be programmed to perform precise and repetitive welds, increasing efficiency and reducing the risk of human error. This not only saves time and money but also improves the overall quality of the welds. Additionally, sustainability in welding is becoming increasingly important. The industry is moving towards more environmentally friendly welding processes, such as using renewable energy sources and implementing recycling programs for welding materials. These advancements will not only benefit the environment but also contribute to the long-term sustainability of skyline engineering.