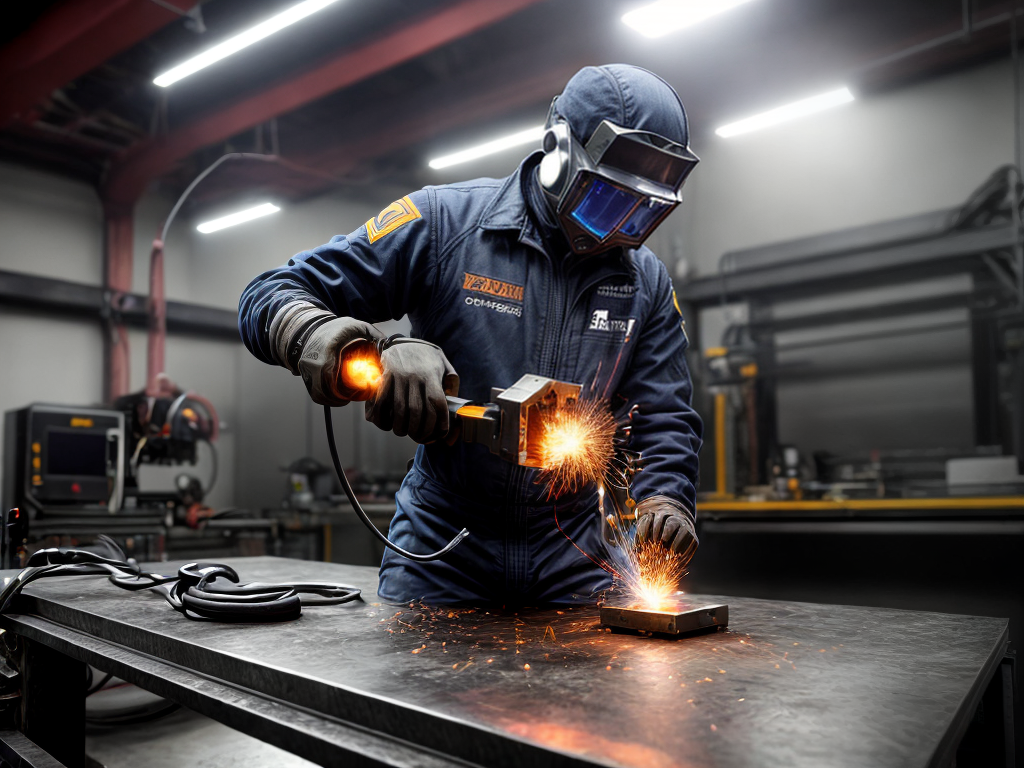
As a passionate advocate for cutting-edge technology and innovation, I am convinced that 3D printing and welding are revolutionizing the future of fabrication. The possibilities that these advancements offer are mind-boggling! Imagine being able to effortlessly create intricate and complex designs with just a few clicks. This merging of 3D printing and welding techniques opens up a whole new world of possibilities for customization, efficiency, and sustainability in fabrication. In this article, we will explore the latest advancements in 3D printing technology and the evolution of welding techniques. We will also delve into the exciting applications of combining these two methods in various industries. Join me on this journey as we uncover the transformative potential of 3D printing and welding in the future of fabrication.
Advancements in 3D Printing Technology
In my opinion, with the advancements in 3D printing technology, the possibilities for fabrication are expanding exponentially. The rapid progress in this field has led to significant breakthroughs in materials development, revolutionizing the way we create and manufacture objects. 3D printing, also known as additive manufacturing, allows for the precise layering of materials to build complex structures with incredible detail and accuracy. This technology has evolved from primarily using plastics to incorporating a wide range of materials, including metals, ceramics, and even biological substances. These advancements have opened up new avenues for innovation in industries such as aerospace, healthcare, and automotive, where customized and lightweight parts can be created with ease. With ongoing research and development, the future of 3D printing holds immense potential for further advancements in materials and fabrication techniques.
The Evolution of Welding Techniques
With the advancements in 3D printing technology, the future of fabrication lies in the evolution of welding techniques. As we continue to push the boundaries of what is possible in fabrication, the need for more efficient and precise welding methods becomes increasingly important. The evolution of welding techniques is driven by the desire to create stronger, lighter, and more complex structures. Future advancements in welding technology will focus on improving the speed, accuracy, and versatility of welding processes. This includes the development of new materials, such as advanced alloys and composites, that can be joined together seamlessly. Additionally, advancements in automation and robotics will play a significant role in the future of welding, allowing for increased productivity and safety. As fabrication continues to evolve, so too will the techniques and technologies used in welding.
Combining 3D Printing and Welding for Enhanced Fabrication
How can 3D printing and welding be combined to enhance fabrication? Integrating 3D printing with welding presents several challenges. One of the main challenges is the integration of two different technologies and ensuring that they work seamlessly together. Another challenge is material compatibility. Different materials used in 3D printing and welding may have different properties, making it difficult to find compatible materials that can be used in both processes. Additionally, joint strength is a crucial factor in fabrication. Welding provides strong and durable joints, but when combined with 3D printing, it is essential to ensure that the joints are robust enough to withstand the required loads and stresses. Researchers and engineers are continuously working on developing innovative techniques to address these challenges and improve material compatibility and joint strength in the integration of 3D printing and welding.
Applications of 3D Printing and Welding in Various Industries
As we explore the applications of 3D printing and welding in various industries, it becomes evident that these technologies offer industry-specific benefits and advancements in fabrication. From aerospace to healthcare, 3D printing and welding have revolutionized the way we manufacture and build. The ability to create complex, customized designs and rapidly prototype parts has opened up new possibilities and efficiencies across a wide range of sectors.
Industry-Specific Benefits
In my experience, I have witnessed significant cost savings achieved through the implementation of 3D printing and welding in industries across the board. These technologies address industry-specific challenges and offer numerous benefits that make them a cost-effective solution for various applications.
Industry | Industry-Specific Challenges |
---|---|
Automotive | Customization, prototyping, and reducing production lead times |
Aerospace | Lightweight components, complex geometries, and reduced material waste |
Healthcare | Personalized implants, prosthetics, and medical devices |
A cost effectiveness analysis of implementing 3D printing and welding in these industries shows a reduction in material costs, labor costs, and production time. For instance, in the automotive industry, 3D printing allows for the production of customized parts quickly and at a lower cost compared to traditional manufacturing methods. In the aerospace industry, 3D printing enables the creation of lightweight components with intricate geometries, resulting in fuel savings and improved performance. In the healthcare industry, 3D printing enables the production of personalized implants and prosthetics, reducing the need for costly manual customization.
Advancements in Fabrication
I have witnessed significant advancements in fabrication through the applications of 3D printing and welding in various industries. One major advancement is the progress in additive manufacturing, also known as 3D printing. This technology allows for the creation of complex and customized designs with precision and efficiency. It has revolutionized the manufacturing process by reducing costs, minimizing waste, and increasing production speed. Additionally, the impact of automation on fabrication cannot be overlooked. Automation has streamlined the welding process, making it faster and more accurate. It has also improved safety by reducing the need for human intervention in hazardous environments. Overall, these advancements in fabrication have transformed industries such as automotive, aerospace, healthcare, and architecture, paving the way for innovative and sustainable solutions.
Overcoming Challenges in 3D Printing and Welding Integration
As we explore the challenges in integrating 3D printing and welding, there are three key areas that require attention. First, ensuring material compatibility is crucial to prevent issues such as warping or weak joints. Second, enhancing joint strength is necessary to meet the structural requirements of the fabricated parts. Lastly, optimizing the integration process itself can help streamline production and improve overall efficiency. These points will be discussed in detail to shed light on the solutions and advancements in this field.
Material Compatibility Solutions
To tackle the challenges of integrating 3D printing and welding, I devised innovative material compatibility solutions. One of the main material compatibility challenges in this integration is finding materials that can be effectively printed and welded together. To address this, I developed a comprehensive database of compatible materials, taking into account their printing and welding properties. This database allows engineers and designers to easily identify suitable materials for their projects, reducing time and effort in the material selection process. Additionally, I created a material testing protocol to ensure the compatibility of different materials before printing and welding. This protocol involves evaluating factors such as adhesion strength, thermal stability, and structural integrity. These innovative solutions not only enhance the integration of 3D printing and welding but also pave the way for the future of fabrication.
Enhanced Joint Strength
One solution to overcome challenges in integrating 3D printing and welding is by enhancing joint strength. By focusing on increasing durability and joint reinforcement, we can ensure that the final fabrication is both strong and reliable. When it comes to 3D printing and welding integration, joint strength is crucial for the overall performance and longevity of the finished product. By implementing techniques and technologies that enhance joint strength, we can address the limitations and vulnerabilities that arise during the integration process. By reinforcing the joints, we can ensure that the different components of the fabrication are securely connected, minimizing the risk of failure or structural damage. Ultimately, enhancing joint strength in the integration of 3D printing and welding will result in more robust and reliable fabricated objects.
Integration Process Optimization
After identifying the challenges in integrating 3D printing and welding, I will now discuss how to optimize the integration process. Optimizing the workflow is crucial to ensure a cost-effective integration of these two fabrication methods. One way to achieve this is by streamlining the process and minimizing unnecessary steps. This can be done by identifying bottlenecks and finding ways to eliminate or reduce them. Additionally, utilizing advanced software and automation can greatly improve efficiency and accuracy. By automating repetitive tasks and utilizing real-time monitoring, the integration process can be optimized for maximum productivity. Furthermore, implementing standardized procedures and guidelines can help ensure consistency and reduce errors. By carefully analyzing the workflow and making necessary adjustments, a cost-effective integration of 3D printing and welding can be achieved.
The Future of Customization and Personalization in Fabrication
In my opinion, the future of customization and personalization in fabrication lies with the integration of 3D printing and welding. Customization trends are on the rise, driven by consumer demand for unique and personalized products. With 3D printing, manufacturers can easily create customized designs and prototypes, allowing for greater flexibility and creativity in the fabrication process. Welding, on the other hand, offers the strength and durability needed for functional products. By combining these two technologies, we can achieve a new level of customization and personalization in fabrication. Imagine a world where individuals can easily design and create products tailored to their specific needs and preferences. The integration of 3D printing and welding opens up a world of possibilities for custom-made, high-quality products that truly reflect individuality.
Implications of 3D Printing and Welding for Sustainability and Efficiency
The integration of 3D printing and welding in fabrication has significant implications for sustainability and efficiency. When it comes to sustainability, 3D printing and welding offer numerous benefits. Firstly, these technologies enable the use of recycled materials, reducing waste and promoting a more circular economy. Additionally, 3D printing and welding allow for the creation of lightweight structures, which can minimize the environmental impact associated with transportation and energy consumption. Moreover, by reducing the need for traditional manufacturing processes, such as casting or machining, 3D printing and welding can also lower energy consumption and carbon emissions. In terms of efficiency, these technologies offer faster production times, reduced material waste, and improved design flexibility. Overall, the integration of 3D printing and welding in fabrication holds great potential for achieving sustainability goals and enhancing operational efficiency.