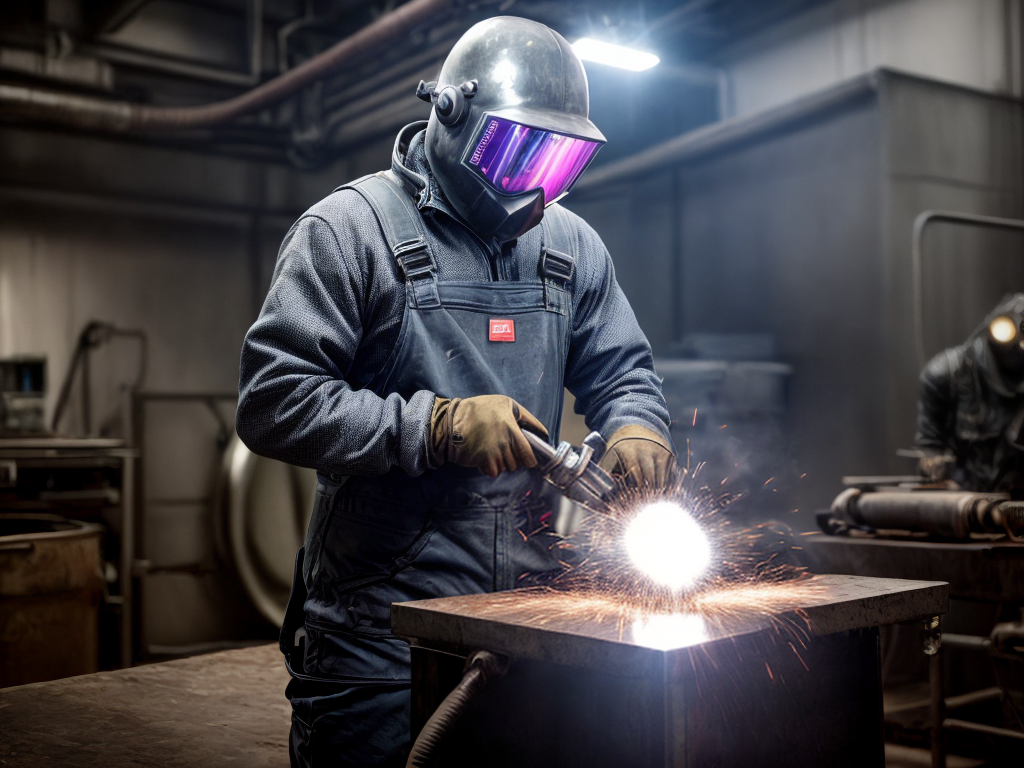
Welcome to “The Ultimate Guide to Welding Aluminum,” where I will be your trusted companion on the journey to mastering the art of aluminum welding. As a passionate expert in the field, I am here to equip you with the knowledge and skills needed to weld aluminum with precision and finesse. Throughout this guide, we will explore the unique properties of aluminum, delve into the process of selecting the right welding equipment, and uncover the secrets to preparing the aluminum surface for a flawless weld. We will also discover the best welding techniques to achieve professional results and prioritize safety in every step of the way. So, let’s dive in and unlock the secrets of welding aluminum like a true master!
Understanding Aluminum Properties
Understanding aluminum properties begins with knowing its unique characteristics and how they impact the welding process. Aluminum is known for its corrosion resistance, making it an ideal choice for various applications. However, it is crucial to understand the factors that contribute to aluminum corrosion, such as exposure to moisture and certain chemicals. When welding aluminum joints, it is essential to ensure proper preparation and cleanliness of the surfaces to be joined. Aluminum’s high thermal conductivity requires careful control of heat input during the welding process to avoid distortion or burn-through. Additionally, its low melting point necessitates the use of specialized techniques and equipment, such as AC welding or pulsed current. By mastering the understanding of aluminum properties, one can achieve successful and durable welds on aluminum joints.
Selecting the Right Welding Equipment
To ensure successful welding of aluminum joints, it is important to carefully select the appropriate welding equipment. There are various welding machine types available for welding aluminum, including TIG (Tungsten Inert Gas) welders and MIG (Metal Inert Gas) welders. TIG welders are commonly used for thinner aluminum sheets, while MIG welders are suitable for thicker materials. When choosing a welding machine, consider factors such as power output, duty cycle, and ease of use. Additionally, proper maintenance of welding equipment is crucial for optimal performance. Regularly clean welding torches, replace consumables such as nozzles and contact tips, and check for any loose connections. Following manufacturer guidelines and performing routine maintenance will extend the lifespan of your welding equipment and ensure consistent and high-quality welds.
Preparing the Aluminum Surface
My preferred method for preparing the aluminum surface is by thoroughly cleaning it with a mild solvent. Surface cleaning is crucial to ensure a strong and durable weld. Before starting the cleaning process, it is essential to remove any dirt, grease, or oil from the surface. I recommend using a mild solvent like isopropyl alcohol or acetone. These solvents effectively dissolve contaminants without damaging the aluminum. Simply apply the solvent to a clean cloth and wipe the surface in a circular motion. Make sure to remove all residue and allow the surface to dry completely before proceeding. Surface treatment is equally important and can be done with a stainless steel brush or sandpaper. This helps remove any oxidation or corrosion, ensuring better adhesion of the weld.
Choosing the Best Welding Technique
After preparing the aluminum surface, it’s time to determine the most suitable welding technique. Choosing the right technique is crucial for achieving high-quality welds and avoiding common welding defects. To help you make an informed decision, let’s compare three commonly used welding processes: MIG (Metal Inert Gas), TIG (Tungsten Inert Gas), and Stick welding.
Welding Process | Advantages | Disadvantages |
---|---|---|
MIG | High welding speed, good for thick materials. | Limited penetration, requires shielding gas. |
TIG | Precise control, suitable for thin materials. | Slow welding speed, requires high skill level. |
Stick | Versatile, can be used in outdoor environments. | High heat input, difficult for thin materials. |
Ensuring Proper Welding Safety
I always prioritize ensuring proper welding safety when working with aluminum. It is crucial to be aware of the common welding mistakes that can occur and take the necessary precautions to prevent accidents. One of the most important aspects of welding safety is proper ventilation. When welding aluminum, harmful fumes and gases can be released, such as aluminum oxide and nitrogen dioxide. These can be hazardous to your health if inhaled, causing respiratory problems or other serious health issues. Therefore, it is essential to work in a well-ventilated area or use ventilation systems to remove the fumes. Additionally, wearing the appropriate personal protective equipment, such as a welding helmet, gloves, and protective clothing, is vital to protect yourself from burns and other injuries. By prioritizing welding safety and ensuring proper ventilation, you can create a safe and efficient working environment when welding aluminum.