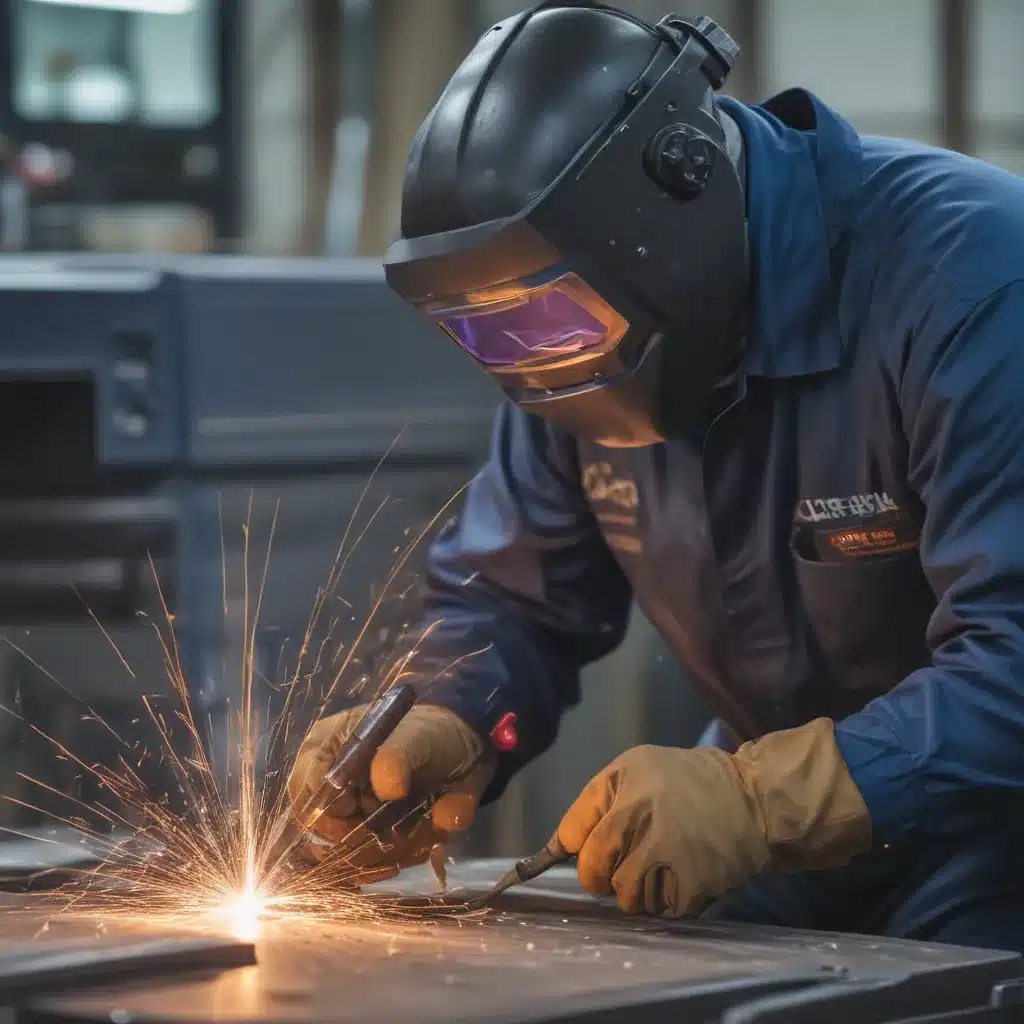
The Scoop on Laser Welding
As a seasoned welding enthusiast, I’ve always been fascinated by the constant evolution of welding technologies. The age-old debate between traditional arc welding and the more modern laser welding has sparked my curiosity for years. So, when I was asked to dive into this topic, I couldn’t wait to share my insights and experiences.
You see, I’ve had the privilege of working with both arc and laser welding techniques over the course of my career. And let me tell you, there’s a lot more to it than meets the eye. It’s not just about the shiny sparks or the mesmerizing laser beams – there’s a whole world of nuance and technicality that goes into choosing the right welding method for the job.
The Arc Welding Advantage
Now, let’s start by acknowledging the tried-and-true power of arc welding. This classic technique has been the backbone of the industry for decades, and for good reason. The ability to weld thick metals with a high degree of control and precision is truly impressive.
I remember one project where we had to join some heavy-duty steel beams for a massive construction site. The client was adamant about achieving the perfect weld, with zero room for error. Enter: good ol’ arc welding. We were able to carefully manipulate the arc, adjusting the current and voltage to create a seamless, high-strength bond that could withstand the immense stresses of the application.
The Laser Welding Edge
But then, along came laser welding – the new kid on the block, challenging the status quo. And let me tell you, this technology is not to be underestimated. The ability to precisely focus a high-energy laser beam onto a tiny spot on the workpiece is truly remarkable.
I recall a recent project where we were tasked with welding some delicate, thin-gauge stainless steel components for a high-end medical device. Traditional arc welding simply wouldn’t do – the heat input would’ve been too high, risking warping and distortion. But with laser welding, we were able to create tight, localized welds with pinpoint accuracy, all while minimizing the heat-affected zone. The result? A flawless final product that met the client’s stringent quality standards.
Comparing the Pros and Cons
So, when does laser welding shine over its arc-based counterpart? Let’s break it down:
Feature | Arc Welding | Laser Welding |
---|---|---|
Heat Input | Higher | Lower |
Weld Depth | Greater | Shallower |
Weld Width | Wider | Narrower |
Weld Appearance | Typically rougher | Smoother, more consistent |
Flexibility | Highly adaptable | More specialized |
Accessibility | Can access tight spaces | Requires more clearance |
Investment Cost | Lower | Higher |
Operator Skill Level | Moderate | Higher |
As you can see, each technique has its own unique strengths and weaknesses. The key is to carefully evaluate the specific requirements of your project and choose the welding method that best suits your needs.
Real-World Applications
Now, let’s dive into some real-world examples to really drive the point home.
Take the automotive industry, for instance. Laser welding has become increasingly prevalent in the manufacture of modern, lightweight vehicles. The ability to create precise, high-strength welds in thin-gauge steel and aluminum components is simply unmatched by traditional arc welding. This helps automakers optimize weight, improve fuel efficiency, and enhance overall vehicle performance.
On the flip side, when it comes to heavy industrial fabrication, arc welding still reigns supreme. I once worked on a project for a mining equipment manufacturer, where we needed to join some seriously thick, high-strength steel plates. The penetration and control afforded by arc welding allowed us to create sturdy, reliable welds that could withstand the extreme stresses and environments of the mining industry.
The Human Touch
But you know, as much as I love geeking out about the technical aspects of welding, there’s something to be said for the human element. I’ve always believed that the true artistry of welding lies in the skill and experience of the operator – whether they’re wielding a torch or a laser.
I’ll never forget the time I worked with this old-school welder, a real master of his craft. The way he could manipulate the arc, coaxing out the perfect bead with seemingly effortless precision, was nothing short of mesmerizing. It was like watching a virtuoso musician play their instrument.
And let me tell you, when it comes to laser welding, the human touch is just as important. Sure, the technology is incredibly precise and automated, but it still takes a seasoned professional to truly harness its power. I’ve seen novice operators struggle to achieve consistent, high-quality welds, while the veterans make it look like child’s play.
The Evolving Landscape
As the world of welding continues to evolve, I can’t help but wonder what the future holds. Will laser welding eventually usurp the dominance of arc welding, or will the two techniques continue to coexist and complement each other?
One thing’s for certain – the pace of innovation shows no signs of slowing down. Just last week, I read about a new hybrid welding process that combines the best of both worlds, leveraging the precision of lasers with the flexibility of arc welding. It’s mind-boggling to think about the possibilities.
And who knows, maybe one day we’ll have welding robots that can outperform even the most seasoned human operators. The thought of it both excites and terrifies me. But you know what they say – the only constant in this industry is change.
Conclusion: Choose Wisely
So, there you have it – my deep dive into the world of laser welding and its relationship with traditional arc welding. I hope I’ve been able to shed some light on the nuances of these two welding techniques and help you understand when one might be better suited than the other.
At the end of the day, there’s no one-size-fits-all solution. It all comes down to carefully evaluating the specific requirements of your project and choosing the welding method that best fits the bill. And of course, having a skilled, experienced operator at the helm is crucial, no matter which technology you choose.
So, whether you’re in the market for laser welding, arc welding, or any other welding service, I encourage you to do your due diligence, ask the right questions, and partner with a trusted provider that can help you make the best decision for your needs. And who knows, maybe I’ll even get the chance to work with you someday – I’d love to see your welding projects in action!