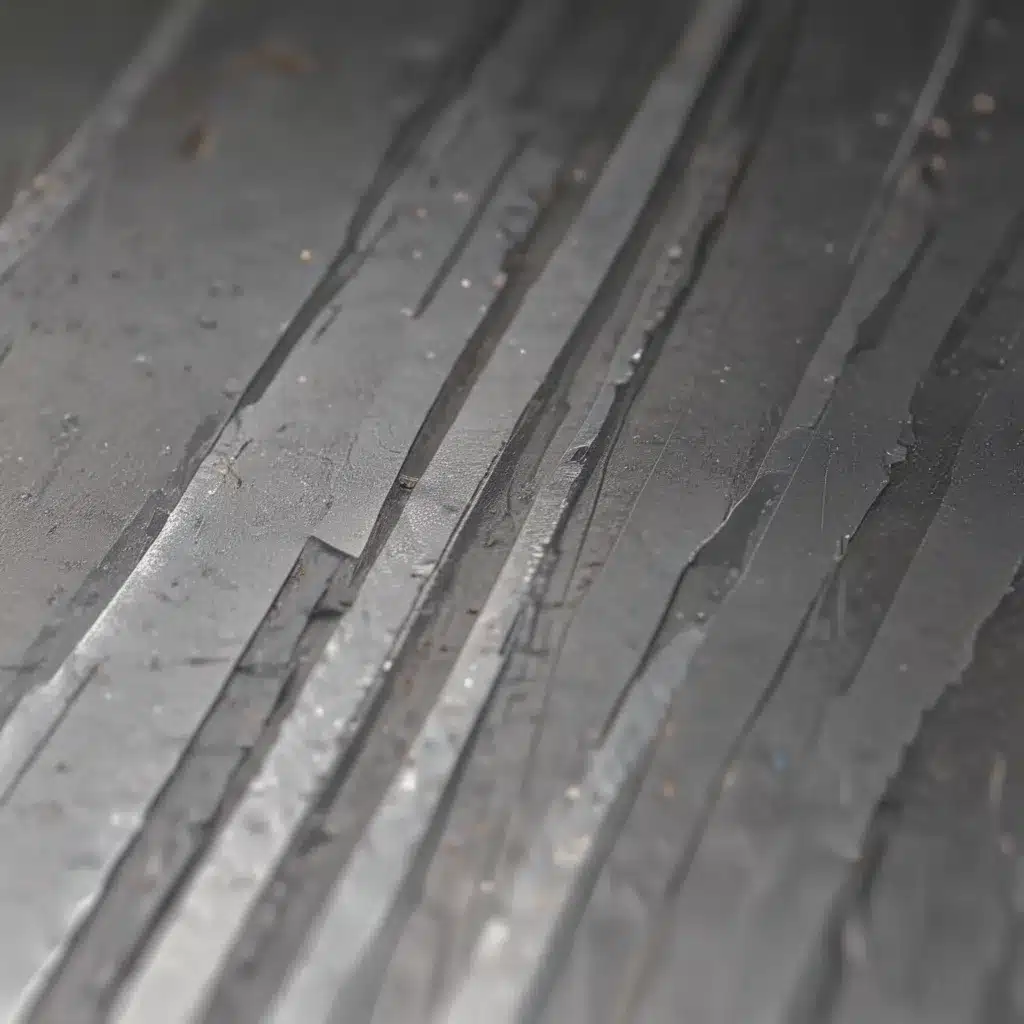
The Delicate Dance of Thin Metal Welding
Ah, the world of welding – where sparks fly, metal fuses, and the very fabric of our physical realm is transformed. But when it comes to working with thin metals, the process becomes a delicate dance, a waltz between control and chaos. As a seasoned welding enthusiast, I’ve had my fair share of experiences with this tricky endeavor, and I’m here to share my insights, tips, and a few entertaining anecdotes along the way.
You see, thin metals are like the prima ballerinas of the welding world – incredibly graceful, but oh-so-fragile. Weld them with too heavy a hand, and they’ll buckle and bend like a frail tree branch in a thunderstorm. But tame them just right, and you’ll be rewarded with the most delicate, intricate work that’ll have your clients singing your praises.
Mastering the Art of Thin Metal Welding
The Challenges of Thin Metals
Now, where do we begin, you ask? Well, let’s start by addressing the elephant in the room – or should I say, the thin metal in the room. These delicate materials pose a unique set of challenges that we welders must overcome. For starters, their very thinness makes them susceptible to warping, distortion, and even complete meltdown during the welding process.
Imagine trying to perform open-heart surgery with a sledgehammer – that’s what welding thin metals can feel like sometimes. The heat input, the speed, the angle of the weld – all of these factors must be meticulously controlled to prevent the metal from becoming a twisted, melted mess. And if that’s not enough, the risk of burnthrough is ever-present, where the intense heat just blows right through the material, leaving an unsightly hole in its wake.
Precision: The Key to Success
But fear not, my fellow welding aficionados! With the right techniques and a keen eye for detail, we can tame even the most unruly thin metals. The key, as I’ve discovered, is all about precision. We’re talking about measuring, marking, and aligning every component with the utmost care, ensuring that the fit-up is as tight and uniform as a newlywed couple.
I remember one project where I was tasked with welding some delicate stainless steel panels for a high-end kitchen display. The client was adamant about maintaining a seamless, flawless finish, and let me tell you, I sweated bullets the entire time. But by taking my time, adjusting my welding parameters to the nth degree, and constantly double-checking my work, I managed to pull off a stunning result that left the client absolutely ecstatic.
The Importance of Heat Control
Of course, precision is only half the battle. The other crucial component in the art of thin metal welding is heat control. These fragile materials require a light touch, a gentle caress of the welding torch, if you will. Gone are the days of cranking up the amperage and blazing through the work – that’s a surefire recipe for warping and distortion.
Instead, I’ve found that a lower heat input, coupled with a slower travel speed, is the key to success. This allows the metal to gradually heat up and fuse, rather than being overwhelmed by a torrent of thermal energy. And don’t forget about the importance of proper shielding gas – the right mix can make all the difference in maintaining a stable, controlled weld pool.
Techniques for Taming Thin Metals
Clamping and Fixturing
Now, let’s dive a little deeper into the practical techniques that I’ve found to be absolute game-changers when it comes to welding thin metals. First and foremost, clamping and fixturing are your best friends. These tools help to hold your delicate workpieces in place, preventing them from shifting, warping, or moving during the welding process.
I remember one time when I was fabricating some intricate stainless steel trim pieces for a high-end automobile. The parts were thinner than a sheet of paper, and I knew that the slightest movement could ruin the entire project. So, I spent hours meticulously setting up my jigs and fixtures, ensuring that every component was locked in place with laser-like precision. The result? A flawless finish that left the client completely blown away.
Tack Welding and Weld Sequencing
Another crucial technique in the thin metal welding arsenal is the art of tack welding. These little spot welds serve as anchors, holding your workpieces in place and preventing distortion as you build up the full weld. But it’s not just about slapping on a few random tacks and calling it a day – oh no, my friends. The key is to strategically plan your tack weld placement, creating a rhythm and sequence that minimizes heat buildup and distributes the stresses evenly.
I’ll never forget the time I was tasked with welding some delicate titanium aircraft components. The tolerances were tight, the materials were thin, and the pressure was on. But by carefully planning my tack weld sequence, alternating between sides and strategically placing my welds, I was able to create a final product that was as strong as it was visually stunning. The client was blown away, and I walked away with a newfound respect for the power of tack welding.
Interpass Temperature Control
And let’s not forget about the importance of interpass temperature control – a fancy term for managing the heat buildup during the welding process. You see, thin metals have a nasty habit of accumulating heat, which can lead to warping, distortion, and even cracking if left unchecked.
That’s why I always make it a point to monitor the temperature of my workpieces, using precise tools like infrared thermometers to ensure that I’m not pushing the limits. Sometimes, that means taking strategic breaks to allow the metal to cool down, or even incorporating specialized cooling techniques like water-soluble markers or temporary heat sinks. It’s all about finding that delicate balance, like a tightrope walker navigating the thin line between success and disaster.
Real-World Examples and Case Studies
Welding Thin Stainless Steel Panels
Let me share a real-world example that really drives home the importance of these techniques. A few years back, I was contracted to weld some ultra-thin stainless steel panels for a high-end kitchen design. The client was looking for a seamless, flawless finish, and they weren’t messing around.
I knew that I had my work cut out for me, but I was determined to deliver. First, I spent hours carefully measuring, marking, and aligning the panels, ensuring that the fit-up was as tight as a drum. Then, I meticulously clamped and fixtured the components, leaving no room for movement.
Next, I developed a strategic tack weld sequence, carefully placing my spots to minimize heat buildup and distortion. As I built up the full weld, I was constantly monitoring the temperature, adjusting my travel speed and heat input to keep everything under control.
The result? A stunning, mirror-like finish that had the client raving. They couldn’t believe their eyes, and to this day, I take immense pride in knowing that my welding prowess transformed their vision into reality.
Fabricating Thin Titanium Aircraft Parts
But it’s not just stainless steel that requires this level of care and attention – oh no, my friends. I’ve also had the privilege of working with thin titanium aircraft components, and let me tell you, that’s a whole other level of complexity.
I remember one particularly challenging project where I was tasked with fabricating some intricate titanium brackets for a high-performance jet. The tolerances were insane, the materials were paper-thin, and the pressure was on to deliver a flawless result.
I knew that I’d have to pull out all the stops, so I spent countless hours perfecting my technique. Clamping, tack welding, interpass temperature control – you name it, I did it. And when the final product rolled off the workbench, I have to admit, I was pretty darn proud.
The client was ecstatic, of course, and they ended up commissioning me for several more projects down the line. It’s moments like these that really make me appreciate the art of welding, and the incredible feats we can accomplish when we combine precision, skill, and a whole lot of passion.
Conclusion: Embrace the Challenge, Master the Craft
So, there you have it, my fellow welding enthusiasts – the ins and outs of navigating the delicate world of thin metal welding. It’s a challenge, to be sure, but one that’s oh-so-rewarding when you get it right.
Remember, the key is all about precision, heat control, and a deep understanding of the techniques that can tame even the most unruly of thin metals. Embrace the challenge, hone your skills, and you’ll be well on your way to creating masterpieces that’ll have your clients singing your praises.
And who knows, maybe one day, you’ll even find yourself welding for high-end clients, just like I did. After all, the world of welding is full of endless possibilities, and the only limit is your own imagination.
So, what are you waiting for? Grab your gear, fire up that welder, and let’s get to work! The thin metal world is waiting, and it’s time to show it who’s boss.