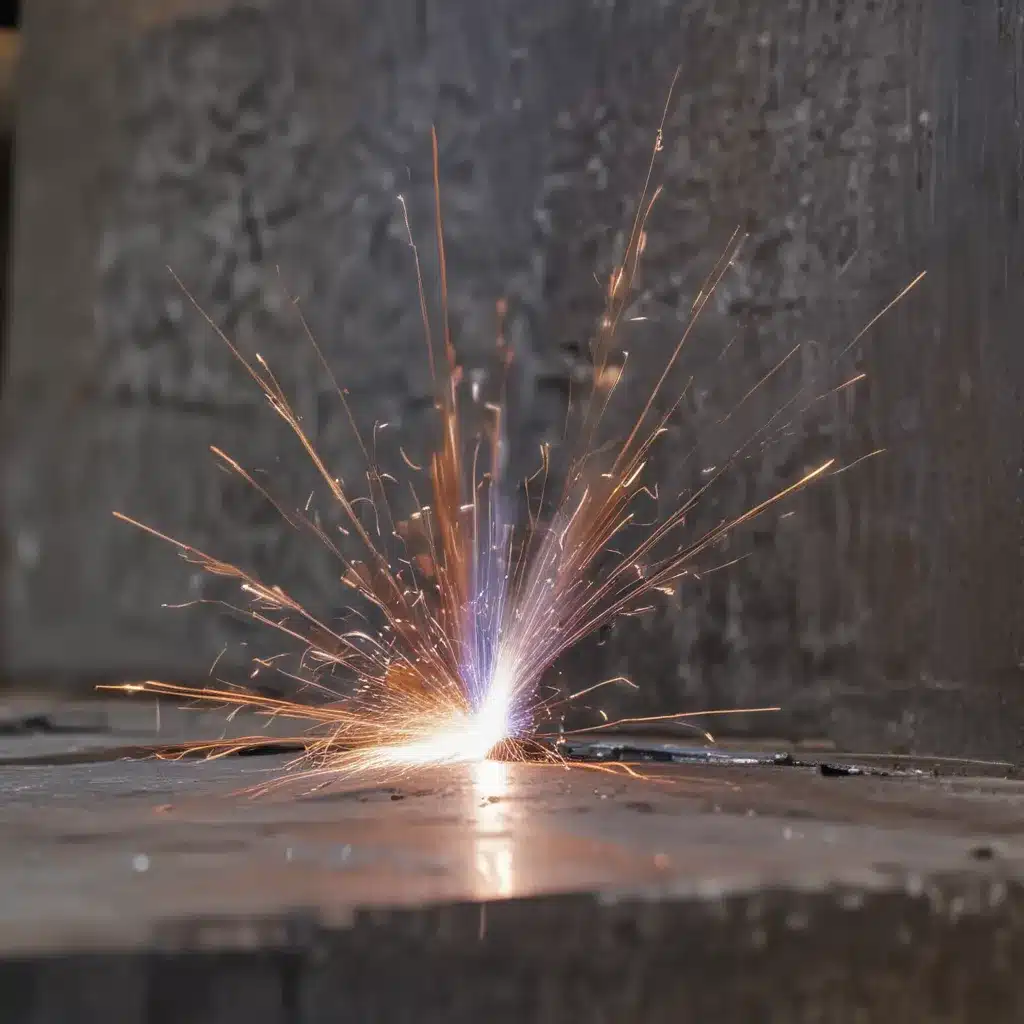
The Challenges of Welding Thick Metals
Ah, the joys of working with thick metals! It’s like trying to wrangle an angry grizzly bear – you need to be strong, smart, and have a whole lot of patience. I’ve seen my fair share of thick metal welding projects over the years, and let me tell you, it’s not for the faint of heart.
You see, when you’re dealing with thick metals, the rules of the welding game change dramatically. The heat input required to melt and fuse those hefty chunks of steel or aluminum is off the charts, and that’s where the real trouble starts. Crank up that arc or oxy-fuel torch too high, and you’re just asking for trouble – distortion, cracking, and a whole host of other nasty surprises that can turn your project into a nightmarish mess.
But fear not, my welding-savvy friends! I’m here to share some hard-earned wisdom and show you how to tame those thick metal beasts and come out on top. With the right techniques and a bit of know-how, you can prevent those pesky distortion and cracking issues and end up with a beautiful, structurally sound weld. So, let’s dive in and explore the world of welding thick metals, shall we?
The Causes of Distortion and Cracking in Thick Metals
Now, let’s talk about the primary culprits behind distortion and cracking in thick metal welding – heat input and thermal expansion. When you’re dealing with thick materials, the sheer amount of heat required to melt and fuse those layers can be downright staggering. And as that heat spreads through the metal, it causes it to expand in all directions.
But here’s the rub: as the metal cools, it contracts, and that’s where the trouble starts. The uneven cooling and contraction can lead to warping, bending, and even cracking – all of which can completely ruin your carefully crafted masterpiece. And let me tell you, trying to fix a badly distorted or cracked weld is like trying to put toothpaste back in the tube. It’s a real headache, and it can often mean starting the whole project over from scratch.
So, what’s the solution, you ask? Well, my friends, it all comes down to careful planning, precise temperature control, and a few nifty welding techniques that can help you stay one step ahead of those pesky distortion and cracking gremlins.
Strategies for Preventing Distortion and Cracking in Thick Metal Welding
Alright, now we’re getting to the good stuff – the tips and tricks that can help you conquer those thick metal welding challenges and come out on top. Let’s start with the basics, shall we?
First and foremost, you need to make sure you’re using the right welding process for the job. For thick metals, you’ll generally want to stick to processes like SMAW (stick welding), GMAW (MIG), or FCAW (flux-cored), as they can deliver the high heat input required without causing too much distortion. And when it comes to filler metals, you’ll want to choose ones with a similar composition to the base metal to minimize thermal expansion issues.
Next, it’s all about temperature control. You need to be meticulous in your pre-heating and post-weld heat treatment, making sure the metal stays within a specific temperature range throughout the welding process. This helps to even out the heating and cooling, reducing the risk of distortion and cracking. And don’t forget about the importance of interpass temperature control – keeping an eye on that can make a big difference in the final result.
But wait, there’s more! Proper joint preparation is also crucial when welding thick metals. You’ll want to ensure that the edges are properly beveled and the fit-up is tight and accurate. This helps to minimize the amount of weld metal required, which in turn reduces the overall heat input and the potential for distortion.
And let’s not forget about the importance of welding sequence and technique. By strategically planning out your welding passes and using techniques like skip welding or back-stepping, you can help to distribute the heat more evenly and minimize the risk of warping or cracking. And of course, maintaining a steady, consistent welding speed is key – too fast, and you risk underfilling the joint; too slow, and you’re just asking for trouble.
Real-World Examples and Case Studies
Now, let’s take a look at some real-world examples of how these strategies have been put into practice to prevent distortion and cracking in thick metal welding projects.
One particularly interesting case study comes from a heavy equipment manufacturer who was struggling with warping and cracking in their thick steel fabrications. After carefully analyzing the issue, they discovered that their pre-heating and post-weld heat treatment processes were simply not up to snuff. By implementing more precise temperature control measures and optimizing their welding sequence, they were able to dramatically reduce the incidence of distortion and cracking, ultimately improving the quality and structural integrity of their products.
Another fascinating example comes from a custom metal fabrication shop that specializes in large-scale architectural installations. When they took on a project to create a massive, curved stainless steel facade, they knew they were in for a challenge. But by employing advanced welding techniques like pulse-arc GMAW and strategic joint design, they were able to weld the thick metal panels with pinpoint precision, minimizing distortion and ensuring a flawless final product.
And let’s not forget about the importance of ongoing training and skill development. I’ve seen countless welders improve their thick metal welding game simply by investing in continued education and honing their techniques. Whether it’s mastering the art of FCAW or perfecting their preheat and interpass temperature control, the more they learn and practice, the better they become at navigating the unique challenges of working with thick metals.
Embracing the Challenges of Thick Metal Welding
So, there you have it, my fellow welding enthusiasts – a deep dive into the world of preventing distortion and cracking in thick metal welding. It’s a challenging field, to be sure, but with the right strategies, techniques, and a whole lot of determination, you can absolutely conquer those thick metal beasts and come out on top.
And you know what? I wouldn’t have it any other way. There’s something truly satisfying about taking on a welding project that pushes the boundaries of what’s possible. The thrill of finding creative solutions to seemingly insurmountable problems, the pride of creating a flawless, structurally sound weld in thick, unyielding metal – it’s all part of the welding journey, and I wouldn’t trade it for anything.
So, if you’re a welder who’s ready to take on the thick metal challenge, I say go for it! Embrace the complexity, the problem-solving, and the pure, unfiltered satisfaction of creating something truly remarkable. And remember, you’re not alone – the welding community is here to support you every step of the way.
Oh, and one more thing – if you’re ever in the market for top-notch welding services, be sure to check out https://www.corrconnect.org/. These guys know a thing or two about taming thick metal beasts, and they’d be more than happy to lend a hand with your next big project. Happy welding, my friends!