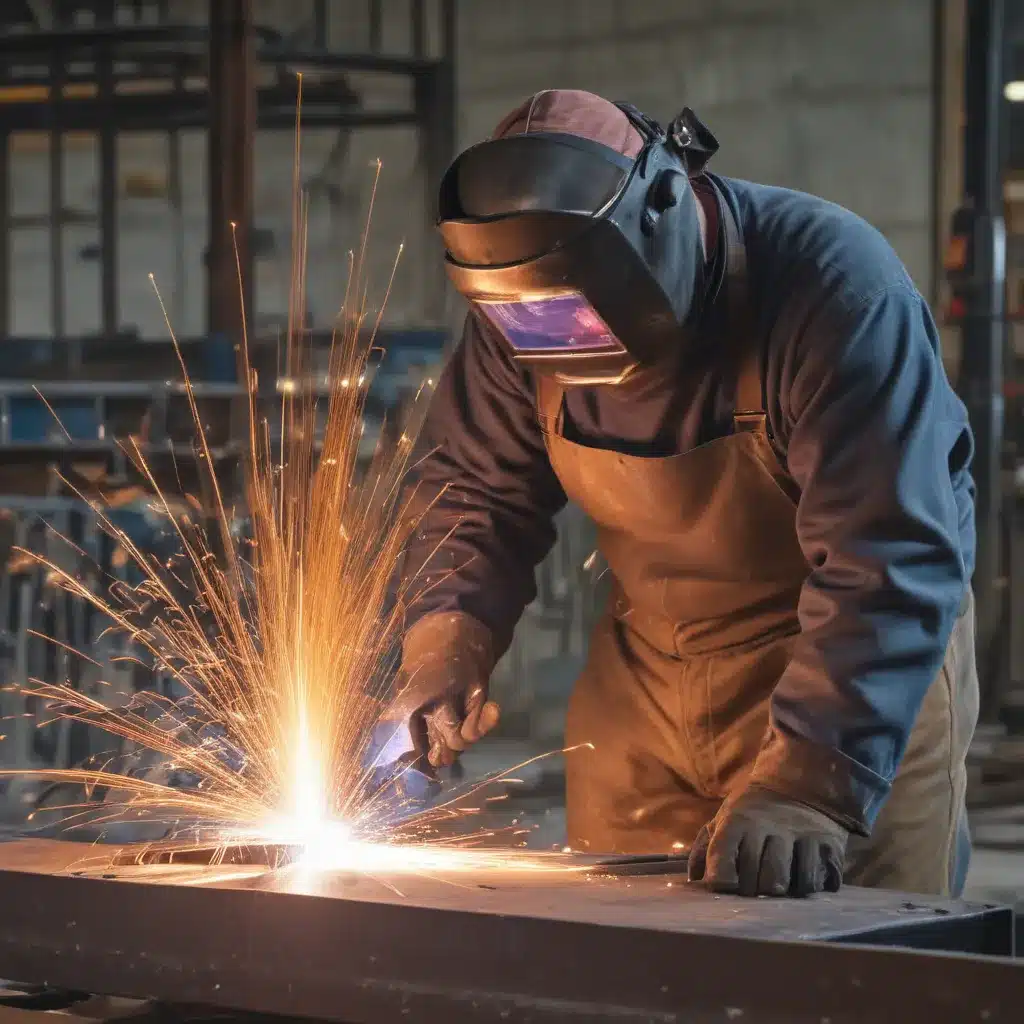
The Foundations of Strength: Mastering Welding for Structural Steel
As a seasoned expert in the world of welding, I’ve seen the industry evolve and transform over the years. One area that has remained a constant focus is the critical role of welding in structural steel construction. The strength, durability, and integrity of our built environment quite literally hinge on the mastery of welding techniques.
So, let’s dive in and explore the realm of welding strategies for structural steel construction. Shall we? 🤓
The Importance of Welding in Structural Steel Construction
Structural steel is the backbone of many modern buildings, bridges, and infrastructure projects. Quite simply, without the precision and expertise of welders, these structures would quite literally collapse under their own weight. The welds that hold the steel members together are the lifeblood of these colossal endeavors.
But it’s not just about brute strength – the quality of the welding also determines the long-term performance and safety of these structures. Improper welding can lead to cracks, fatigue, and even catastrophic failures down the line. That’s why mastering welding strategies for structural steel construction is paramount.
As someone who’s been in the industry for over two decades, I can attest to the sheer complexity and importance of this field. It’s not just about striking an arc and melting some metal – it’s about understanding the unique properties of steel, the intricacies of joint design, and the subtle nuances of welding techniques.
Choosing the Right Welding Process for Structural Steel
When it comes to welding structural steel, there’s no one-size-fits-all solution. The specific welding process you choose will depend on a variety of factors, including the thickness of the steel, the joint configuration, the accessibility of the workspace, and the desired weld properties.
Let’s take a closer look at some of the most common welding processes used in structural steel construction:
Shielded Metal Arc Welding (SMAW)
Also known as “stick welding,” SMAW is a versatile and widely-used process for structural steel. It’s particularly well-suited for welding thicker materials, working in tight spaces, and tackling challenging joint configurations. The flux-coated electrode provides shielding gas and produces a stable, penetrating arc that can handle a wide range of steel grades.
Gas Metal Arc Welding (GMAW)
Also known as “MIG welding,” GMAW is a semi-automatic process that uses a continuous wire electrode and a shielding gas to produce high-quality welds. It’s known for its speed, flexibility, and ability to handle a variety of steel thicknesses. GMAW is often used for welding structural steel members, especially in shop or factory settings.
Flux-Cored Arc Welding (FCAW)
FCAW is a versatile process that combines the advantages of both SMAW and GMAW. It uses a tubular, flux-filled wire electrode that provides its own shielding gas, making it well-suited for outdoor or windy environments. FCAW is a popular choice for structural steel construction due to its high deposition rates and ability to handle a range of steel thicknesses.
Submerged Arc Welding (SAW)
SAW is a highly productive, automated welding process that’s often used for fabricating large, thick-walled structural steel components. It utilizes a continuously fed wire electrode that’s submerged in a granular flux, creating a protective “submerged arc” that produces deep, high-quality welds. SAW is particularly useful for welding long seams on heavy-duty structural elements.
The choice of welding process will ultimately depend on the specific requirements of the project, the expertise of the welding team, and the available equipment and resources. As an experienced welder, I’ve had the opportunity to work with all of these processes, and I can attest to the unique strengths and challenges of each one.
Ensuring Weld Quality and Integrity
But it’s not just about choosing the right welding process – it’s also about ensuring the quality and integrity of the welds themselves. After all, the structural integrity of the entire building or infrastructure project rests on the strength and reliability of those welds.
One of the key factors in weld quality is joint preparation. Proper joint design, edge preparation, and fit-up are crucial for achieving consistent, high-strength welds. Factors like weld bead size, penetration, and profile all play a role in determining the overall integrity of the joint.
Another critical aspect is the use of qualified welding procedures and the implementation of rigorous quality control measures. This might include things like:
- Nondestructive testing (NDT) techniques like ultrasonic, radiographic, or dye penetrant inspection to detect defects
- Mechanical testing of weld samples to verify strength and ductility
- Ongoing monitoring and inspection of the welding process by certified welding inspectors
And of course, the skill and experience of the welding team themselves is paramount. Proper training, certification, and adherence to industry best practices are essential for ensuring the highest levels of weld quality and structural integrity.
Overcoming Challenges in Structural Steel Welding
Now, I’d be remiss if I didn’t acknowledge the unique challenges that come with welding structural steel. After all, it’s not exactly a walk in the park, is it? 😅
One of the biggest challenges is dealing with the inherent variability of steel as a material. Steel composition, heat treatment, and residual stresses can all have a significant impact on weldability and the risk of defects like cracking or porosity. Welders have to be constantly vigilant and adapt their techniques accordingly.
Another challenge is the sheer size and scale of many structural steel projects. Welding giant support beams or massive bridge girders requires specialized equipment, staging, and safety protocols that are vastly different from typical workshop welding. Accessibility and workspace constraints can also add layers of complexity to the process.
And let’s not forget about the environmental factors, shall we? Outdoor welding in harsh weather conditions, high winds, or extreme temperatures can really put a welder’s skills to the test. Maintaining weld quality and consistency in these scenarios requires a whole different level of expertise and problem-solving.
But you know what they say – where there’s a will, there’s a way! 💪 Experienced welders have developed all sorts of ingenious strategies and techniques for overcoming these challenges. From the use of preheat and post-weld heat treatment to specialized joint designs and welding sequences, there’s always a solution to be found.
Embracing Innovation and Advancing the Craft
As an industry, we’re constantly pushing the boundaries of what’s possible when it comes to welding for structural steel construction. Innovations in welding automation, robotics, and data-driven quality control are transforming the way we approach these projects.
Take, for example, the rise of orbital welding systems. These computer-controlled welding machines can precisely control the welding parameters and produce highly consistent, high-quality welds on pipe and tube assemblies. The automation and repeatability of these systems have been a game-changer in the fabrication of complex structural steel components.
And then there’s the growing adoption of digital tools and technologies in welding. From virtual reality training simulations to real-time weld monitoring and quality control software, these advancements are helping to improve the efficiency, safety, and reliability of structural steel welding.
But it’s not just about the hardware and software – the welding craft itself is also evolving. Welders are constantly honing their skills, experimenting with new techniques, and sharing best practices with one another. It’s a dynamic, ever-changing field that requires a relentless dedication to continuous improvement.
And you know what? I wouldn’t have it any other way. 😊 The thrill of tackling a new welding challenge, the satisfaction of seeing a strong, beautiful weld, and the pride of knowing that your work is supporting the foundations of our built environment – that’s what keeps me coming back day after day.
Forging Ahead: The Future of Welding in Structural Steel Construction
As I look to the future, I can’t help but feel excited about the endless possibilities that lie ahead for welding in structural steel construction. The industry is on the cusp of a revolution, with groundbreaking technologies and innovative approaches that are poised to transform the way we build.
Imagine a world where robots can autonomously weld complex steel structures with pinpoint precision, without the need for human intervention. Or a future where advanced sensing and monitoring systems can continuously assess the health and integrity of welds in real-time, ensuring the safety and longevity of our infrastructure.
And what about the materials themselves? The development of new, high-strength steel alloys and composite materials could unlock entirely new design possibilities for structural steel construction. Welders will need to stay on the cutting edge of these advancements, constantly adapting their techniques and honing their skills.
But it’s not just about the technical side of things. The workforce of the future will also need to embrace a holistic approach to welding, one that prioritizes safety, sustainability, and collaboration. Imagine welding teams working in harmony with designers, engineers, and project managers to create truly integrated, efficient, and resilient structural steel solutions.
The future is bright, my friends, and I can’t wait to be a part of it. 🌟 As we continue to push the boundaries of what’s possible, I know that the role of welding in structural steel construction will only grow in importance and significance.
So, if you’re reading this and feeling inspired to join us on this exciting journey, I say the door is wide open! Whether you’re a seasoned welder looking to level up your skills or a newcomer to the industry, there’s never been a better time to get involved.
Who knows – maybe one day, you’ll be the one shaping the future of structural steel construction, one weld at a time. 😉
For more information on our welding services, including arc welding, metal cutting, custom fabrication, and precision welding, please visit our website.