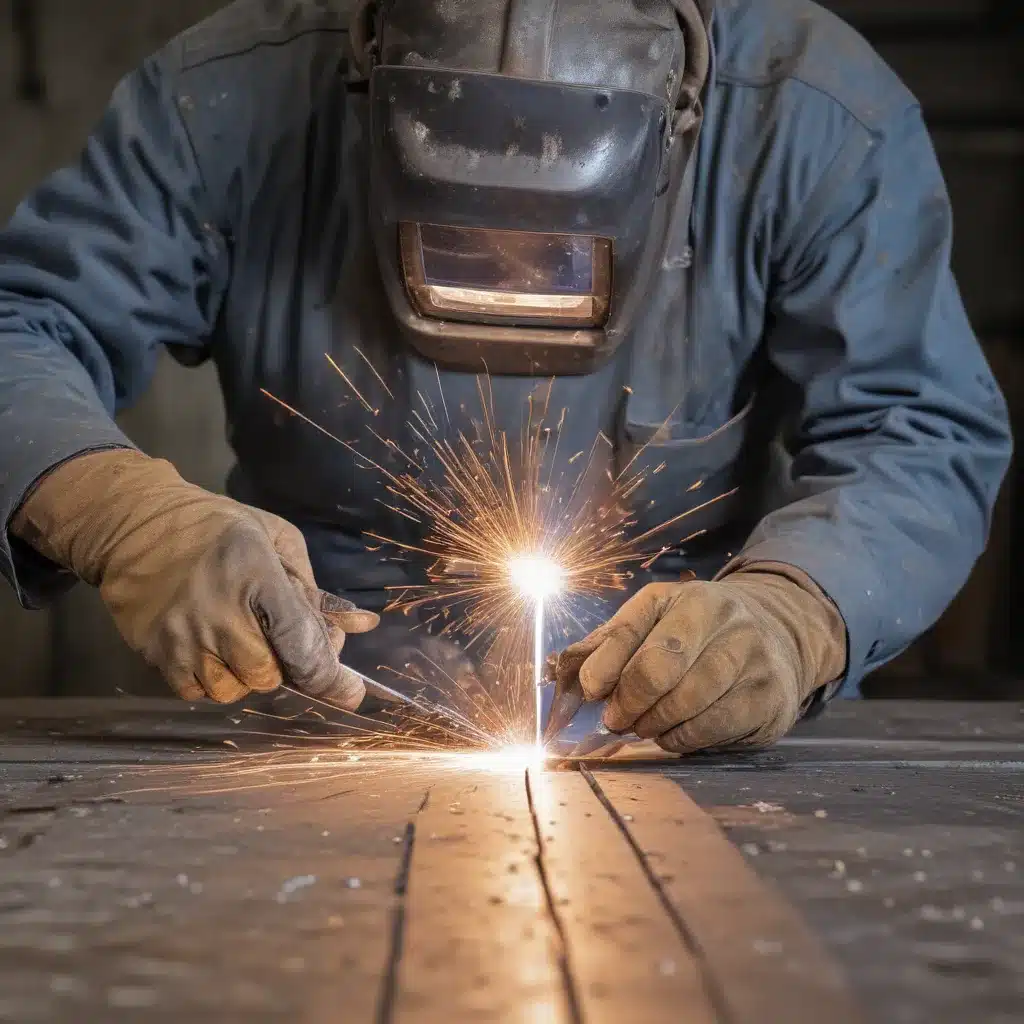
Ahh, the wonderful world of welding – where sparks fly, metal fuses, and the occasional, err… ‘hiccup’ can occur. As a seasoned welding professional, I’ve seen it all – from the perfectly executed bead to the dreaded welding defects that can make even the most hardened welder cringe. But fear not, my friends, for I’m here to guide you through the ins and outs of detecting, preventing, and correcting those pesky welding flaws.
Understanding Welding Defects: A Closer Look
So, what exactly are these welding defects we speak of? Well, my friends, they’re the unwanted blemishes, imperfections, and inconsistencies that can crop up in our precious welds. And trust me, they come in all shapes and sizes – from the unsightly porosity to the dreaded lack of fusion. It’s like a welding version of a beauty pageant, but with a lot less glitz and a whole lot more grime.
Let’s take a deeper dive, shall we? One of the most common culprits is porosity – those pesky little gas bubbles that get trapped in the weld, making it look like the surface of the moon. These buggers can be caused by all sorts of things, from contaminated filler metal to improper shielding gas coverage. And don’t even get me started on lack of fusion – when the weld bead just can’t seem to, well, fuse with the base metal. It’s like trying to get two peas to stick together with a toothpick.
But wait, there’s more! How about undercut, where the weld bead dips below the surface of the base metal, leaving behind a lovely little groove? Or slag inclusions, where bits of that pesky slag (the rocky byproduct of welding) get trapped in the weld? It’s a veritable smorgasbord of welding imperfections, my friends.
Detecting Welding Defects: Keeping a Keen Eye
Now, you might be wondering, “How in the world do I even spot these welding defects?” Well, my friends, it’s all about keeping a keen eye and a discerning mind. Visual inspection is often the first line of defense, where you scrutinize the weld with a critical gaze, looking for any telltale signs of trouble.
But sometimes, the naked eye just won’t cut it. That’s where the trusty nondestructive testing (NDT) methods come into play. From dye penetrant to magnetic particle inspection, these techniques can help you uncover the hidden flaws that might be lurking beneath the surface.
And let’s not forget about the good ol’ destructive testing methods, where we literally tear the weld apart to see what’s going on inside. It’s a bit like performing welding surgery, but with a lot more sparks and a lot less anesthesia.
Preventing Welding Defects: An Ounce of Preparation
Ah, the old saying “an ounce of prevention is worth a pound of cure” definitely applies to the world of welding. Because, let’s face it, once those pesky defects rear their ugly heads, it can be a real pain to fix them. That’s why it’s crucial to take the proper precautions and set the stage for welding success from the very beginning.
One of the most important factors is proper joint preparation. Making sure the surfaces are clean, the fit-up is just right, and the edge preparation is on point can go a long way in preventing those dreaded defects. And let’s not forget about the importance of selecting the right welding process and parameters – it’s like a chef choosing the perfect recipe for their culinary masterpiece.
But the fun doesn’t stop there, oh no! Proper shielding gas selection and monitoring can also be the difference between a smooth, defect-free weld and, well, a hot mess. And let’s not forget about the importance of welder training and certification – because, let’s face it, even the best equipment in the world won’t do much good if the person wielding the torch doesn’t know what they’re doing.
Correcting Welding Defects: Bringing It Back to Life
Alright, so we’ve covered the art of detecting and preventing welding defects, but what happens when that pesky imperfection just won’t go away? Well, my friends, that’s where the true skill of the welder comes into play.
First and foremost, it’s crucial to properly identify the type of defect you’re dealing with. Is it porosity? Lack of fusion? Undercut? Once you’ve got that figured out, you can start to formulate a plan of attack.
For some defects, like porosity, it might be as simple as adjusting the welding parameters or increasing the shielding gas coverage. But for more stubborn issues, like lack of fusion, you might need to take a more drastic approach, such as grinding out the defect and re-welding the area.
And let’s not forget about the importance of post-weld inspection – because, let’s face it, you don’t want to go through all that hard work only to have the same darn defect crop up again. It’s like a never-ending game of whack-a-mole, but with a lot more sparks and a lot less fun.
Embracing the Challenge: A Welder’s Perspective
Now, I know what you’re thinking – “Geez, this welding defect thing sounds like a real headache!” And you know what? You’re not wrong. But as a seasoned welding professional, I’ve come to see these challenges as, well, opportunities.
Because let’s face it, the thrill of the chase is what keeps us welders going. It’s the satisfaction of taking on a tough problem, analyzing the root cause, and implementing a solution that truly gets our welding juices flowing. And when we’re able to deliver a flawless, defect-free weld? Well, that’s the kind of victory that makes all the hard work worth it.
So, my fellow welding enthusiasts, I encourage you to embrace these welding defects as a chance to hone your skills, sharpen your problem-solving abilities, and take your craft to new heights. Who knows, you might even discover a newfound appreciation for the art of welding – and maybe even a few war stories to share over a cold brew.
And remember, if you ever need a little extra help or guidance, the good folks over at Corr Connect are always here to lend a hand. After all, we’re all in this welding journey together, and there’s no better feeling than a little camaraderie and collaboration.
So, let’s raise a metaphorical torch to the art of welding, and all the unique challenges that come with it. Because, let’s face it, where’s the fun in a flawless weld, anyway? Bring on the defects, I say – we’ve got some work to do!