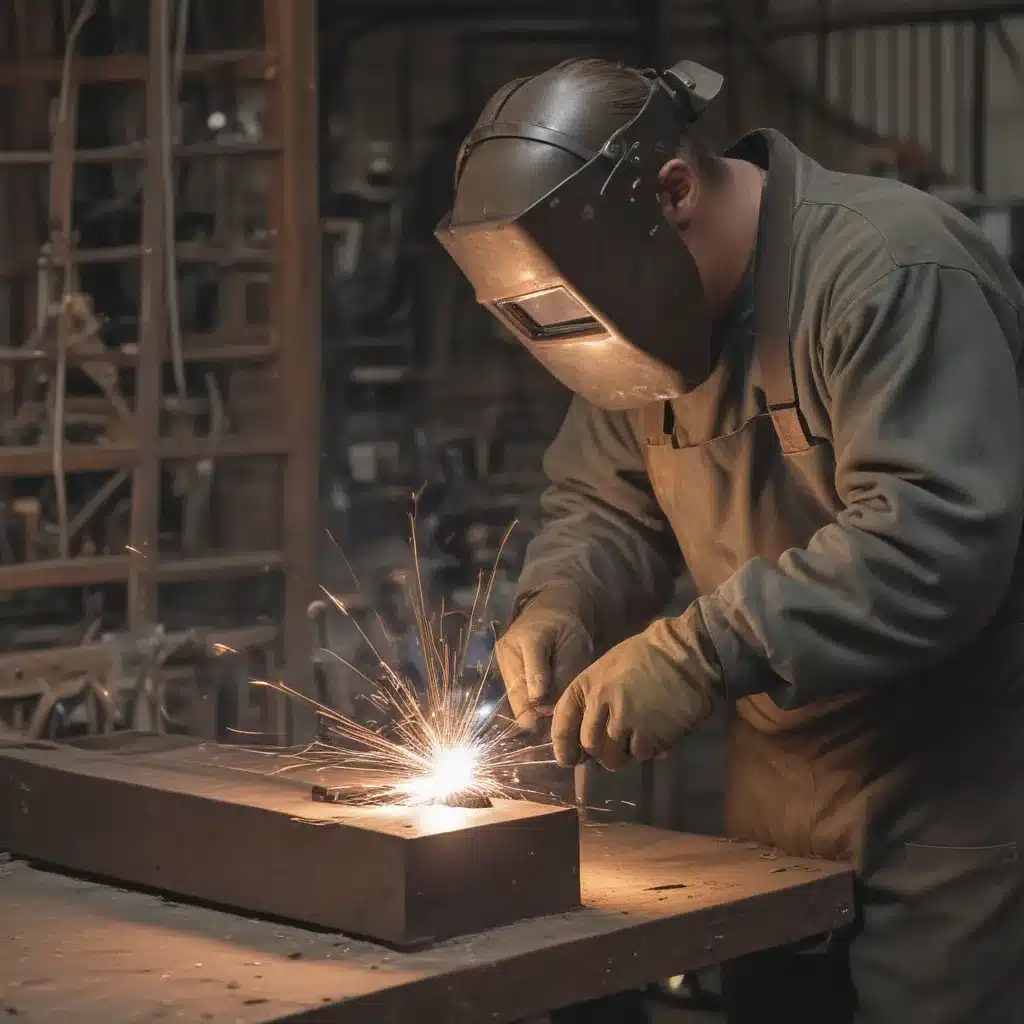
The Ancient Origins of Metalworking
Can you believe that the art of welding and metalworking has been around for thousands of years? It’s true! The origins of this incredible craft can be traced back to the dawn of human civilization.
I mean, think about it – early humans were already shaping and manipulating metal way back in the Bronze Age, using basic forge welding techniques to join pieces of copper and tin together. And as technology progressed over the centuries, so too did the methods of metalworking. The ancient Egyptians, Greeks, and Romans all made major advancements, developing more sophisticated welding processes and tools.
Heck, even the legendary blacksmiths of medieval Europe were masters of their craft, using techniques like forge welding and pattern welding to create those iconic swords, armor, and other metal goods. Can you imagine the skill and dedication it must have taken to become a true blacksmith back then? Talk about a labor of love!
And it’s not just the old-timey metalworkers who deserve our respect. Nope, the modern welding industry has come a long way too. Cutting-edge technologies like arc welding, MIG welding, and TIG welding have completely transformed the game. Nowadays, we can weld all sorts of complex metal components with mind-blowing precision – everything from supersonic aircraft to massive industrial machinery.
The Evolution of Welding Techniques
You know, as I dive deeper into the fascinating history of welding, I can’t help but be amazed by how much the craft has evolved over time. I mean, the basic principles may be the same, but the tools and techniques have undergone some truly remarkable transformations.
Take arc welding, for instance. This method, which uses an electric arc to melt and fuse metal, can be traced all the way back to the late 19th century. Back then, it was a pretty crude and laborious process, requiring bulky, cumbersome equipment and a lot of manual dexterity from the welder.
But fast-forward to today, and arc welding has become an incredibly sophisticated and versatile technique. With the advent of things like shielded metal arc welding (SMAW) and flux-cored arc welding (FCAW), we can now weld all sorts of metals with astonishing speed and precision. Heck, some modern arc welding machines are practically robotic in their precision and efficiency!
And it’s not just arc welding that’s evolved, either. Metal cutting and fabrication techniques have come a long way too. I mean, remember those old-school oxyacetylene torches? They were the go-to for cutting and shaping metal back in the day. But nowadays, we’ve got state-of-the-art plasma cutters and laser cutters that can slice through even the toughest alloys with surgical precision.
And when it comes to custom fabrication? Fuggedaboutit! The tools and techniques available to modern metalworkers are simply mind-boggling. From computer-controlled CNC machines to high-tech welding robots, we can create custom metal components and structures that would have been the stuff of science fiction just a few decades ago.
The Art of Precision Welding
Now, as impressive as all of these advancements in welding and metalworking technology are, I’ve gotta say – there’s still something to be said for the old-school, hands-on approach. After all, at the end of the day, welding is still an art form that requires a tremendous amount of skill, experience, and artistry.
Take precision welding, for example. This is the realm where the true masters of the craft ply their trade. We’re talking about welders who can fuse together metal components with unbelievable accuracy and consistency – the kind of work that’s essential for things like aerospace parts, high-pressure vessels, and ultra-precise industrial equipment.
I mean, just think about the level of control and dexterity it takes to lay down a perfectly uniform bead of molten metal, time after time. And then factor in the need to adjust for things like material thickness, joint design, and environmental conditions, and you’ve got a seriously demanding job.
But you know what? The best precision welders out there absolutely thrive on that kind of challenge. They take immense pride in their work, and rightfully so. After all, the parts and structures they create are literally the backbones of some of the most critical industries on the planet. From defense and aerospace to energy and infrastructure, precision welding is the unsung hero that keeps the world moving.
Real-World Examples of Welding Mastery
And speaking of real-world applications, let me tell you about a few truly awe-inspiring examples of welding and metalworking in action. Because trust me, when you see what these modern-day metalworkers are capable of, it’ll blow your mind.
Take the case of that massive oil refinery project I worked on a few years back. The client needed a series of absolutely massive storage tanks fabricated and installed – we’re talking structures that were over 100 feet tall and made from super-thick alloy steel. Now, just the logistics of getting that kind of heavy-duty equipment on-site and assembled was a feat in itself.
But the real show-stopper was the welding. The tolerances were insane – we’re talking about needing to maintain a joint gap of just a few millimeters across the entire structure. And the welds themselves had to be flawless, with no porosity, cracking, or other defects whatsoever. Anything less, and the whole thing could have been a catastrophic failure.
And you know what? The welding team we assembled absolutely crushed it. They used state-of-the-art tools and techniques – everything from automated welding systems to advanced inspection methods – to deliver a final product that was nothing short of perfection. I still get goosebumps thinking about it, to be honest.
Or how about that time we got brought in to work on a custom luxury yacht? Now that was a real challenge, let me tell you. The client wanted a one-of-a-kind vessel with all sorts of intricate metal fabrications – everything from sleek exterior panels to ultra-fancy interior furnishings. And not only did it all have to be flawlessly crafted, but it also had to be absolutely watertight.
But would you believe it? Our team of master welders and fabricators pulled it off with flying colors. They used specialized TIG welding techniques to fuse the thin, delicate marine-grade alloys with mind-blowing precision. And the final result? A absolutely stunning yacht that turned heads everywhere it went. Seriously, it was a work of art!
The Future of Welding and Metalworking
You know, as I reflect on all of these incredible examples of welding and metalworking mastery, I can’t help but wonder – what does the future hold for this ancient and ever-evolving craft? I mean, the pace of technological change in this industry has been staggering, and I have a feeling we ain’t seen nothin’ yet.
Just imagine the possibilities, you know? With advancements in robotics, artificial intelligence, and materials science, I bet we’re going to see some truly mind-blowing developments in the years to come. Maybe welding robots that can think and adapt on the fly, or ultra-durable alloys that can withstand the harshest environments. Heck, we might even see the rise of 3D printed metal components, fabricated with pinpoint precision.
And you know what else is exciting? The growing emphasis on sustainability and environmentally-friendly manufacturing. I mean, as the world becomes more conscious of its carbon footprint, the welding and metalworking industries are going to have to step up their game. We’re probably going to see a big push towards more energy-efficient welding processes, as well as the increased use of recycled and renewable materials.
But at the end of the day, no matter what the future holds, one thing is for certain – the art of welding and metalworking will always be in demand. After all, the world runs on metal – from the skyscrapers that dot our skylines to the cars that get us from A to B. And as long as there’s a need to shape, join, and fabricate those essential materials, there will always be a place for the skilled and passionate metalworkers of the world.
So here’s to the welders, the fabricators, the blacksmiths, and the metalworking maestros – past, present, and future. Your work may not always get the spotlight, but it’s the backbone of our modern civilization. And I, for one, am in awe of your skill, your artistry, and your unwavering dedication to your craft. Keep on doing what you do best, my friends – the world needs you!