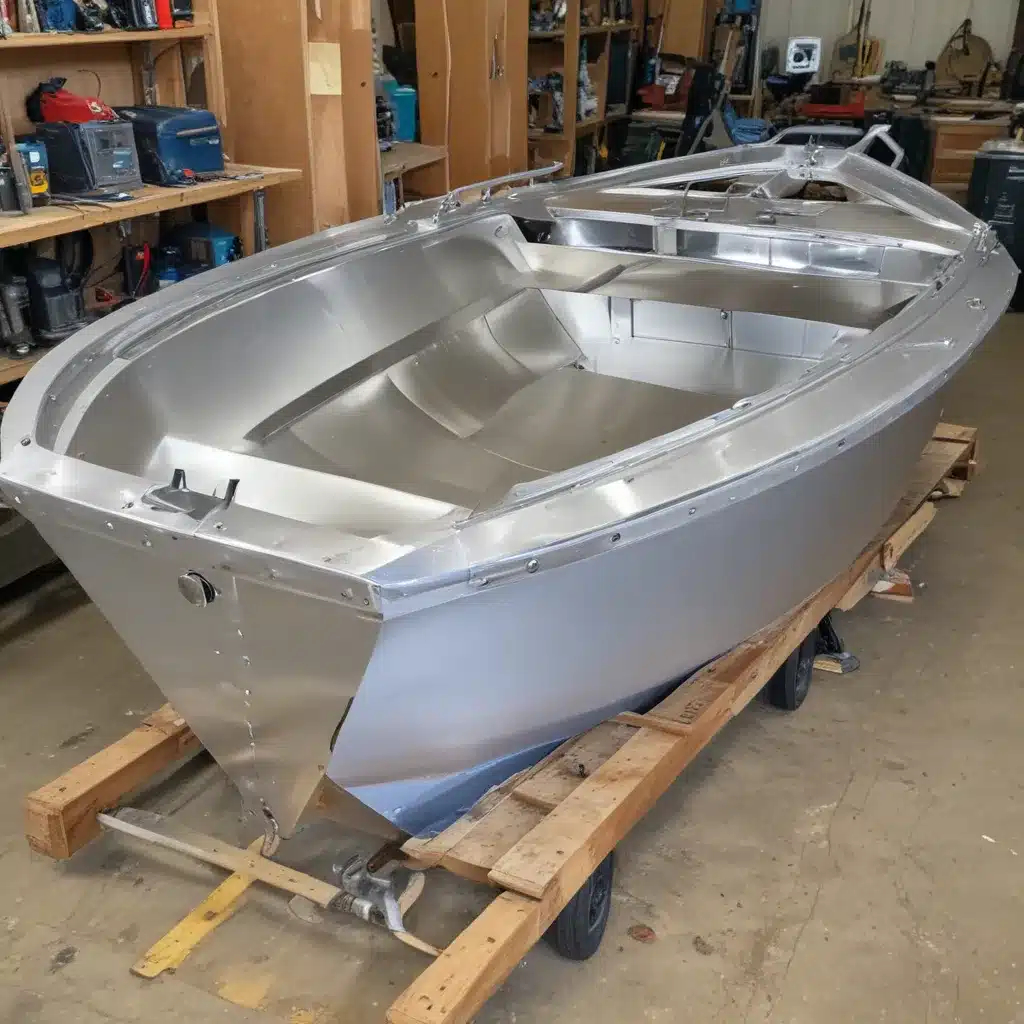
Aluminum Boats: A DIY Dream Come True
Ahoy, fellow DIY enthusiasts! Today, I’m here to dive into the exciting world of welding aluminum boat parts at home. Now, I know what you might be thinking – “Welding aluminum? Isn’t that some sort of wizardry reserved for the pros?” Well, my friends, let me tell you, with the right know-how and a bit of elbow grease, you too can become a master of aluminum welding and transform your trusty aluminum boat into a true nautical masterpiece.
For starters, let me paint you a picture. Imagine yourself on a serene lake, the sun glimmering off the water, and the gentle lapping of waves against the hull of your very own aluminum boat. Sounds pretty darn idyllic, doesn’t it? Well, let me tell you, the journey to get there can be just as rewarding as the destination.
Gearing Up for Aluminum Welding
Now, I know what you’re thinking – “But wait, don’t I need some fancy-schmancy professional equipment to weld aluminum?” Well, my friend, let me let you in on a little secret. While it’s true that welding aluminum does require some specialized gear, it’s not nearly as intimidating as you might think.
First and foremost, you’ll need a good quality aluminum welding machine. Now, I’m not talking about some industrial-sized behemoth that’ll take up your entire garage. Nope, these days, there are plenty of user-friendly, compact welding machines that are perfect for the home DIYer. Think of it like a trusty sidekick, ready to help you tackle all your aluminum welding projects.
Next up, you’ll need some personal protective equipment (PPE) to keep you safe and sound. We’re talking a welding helmet with a shaded lens, heat-resistant gloves, and a sturdy pair of boots. Trust me, you don’t want to be caught without these essential items. It’s like going into battle without your trusty shield and armor – you just can’t do it.
Now, I know what you’re thinking – “But what about all the other fancy tools and gadgets?” Well, fear not, my friend. While there are certainly a few other items you might want to have on hand, like a wire brush and some flux for cleaning the aluminum, you can totally get started with the basics. In fact, the beauty of aluminum welding is that it’s a lot more user-friendly than you might think.
Mastering the Technique
Alright, now that we’ve got the gear sorted out, let’s talk about the actual process of welding aluminum boat parts. Now, I know what you’re thinking – “But isn’t aluminum, like, super tricky to weld?” Well, my friend, let me tell you, with a little bit of practice and the right techniques, you’ll be welding aluminum like a seasoned pro in no time.
The key to successful aluminum welding is all about controlling the heat. You see, aluminum has a much lower melting point than good ol’ steel, so you’ve got to be really careful not to overheat the metal and end up with a big, gooey mess. That’s where the right welding technique comes in.
One of the most popular methods for welding aluminum boat parts is the TIG (Tungsten Inert Gas) welding process. Now, I know what you’re thinking – “TIG welding? Isn’t that some kind of advanced voodoo magic?” Well, let me tell you, it’s actually a lot simpler than it sounds. With TIG welding, you use a non-consumable tungsten electrode to create the weld, and you feed in a separate aluminum filler wire to fill in the gaps. It’s like a little dance, but once you get the rhythm down, it’s a breeze.
Now, I know what you’re thinking – “But what about the whole ‘controlling the heat’ thing?” Well, my friend, that’s where the real magic happens. You see, with TIG welding, you’ve got this nifty little foot pedal that lets you control the heat output of the welding arc. It’s like having a dimmer switch for your welding machine – you can crank it up when you need a little extra oomph, or dial it down when you need to take it easy on the aluminum.
Practical Applications: Repairing and Customizing Your Boat
Now that we’ve covered the basics of welding aluminum, let’s talk about all the awesome things you can do with it. I mean, let’s be real, who doesn’t love a good old-fashioned DIY project, am I right?
One of the most practical applications for welding aluminum boat parts is, well, repairing your boat. Let’s say you’ve got a little ding or dent in the hull, or maybe the transom is looking a bit worse for wear. No problem! With your trusty welding machine and a little bit of know-how, you can have that baby looking good as new in no time.
But wait, there’s more! Welding aluminum also opens up a whole world of custom fabrication possibilities. Imagine being able to add a sweet little swim platform to the back of your boat, or maybe even a custom-built storage compartment. The possibilities are endless, my friends.
And let’s not forget about the sheer joy of simply tinkering and experimenting. I mean, who doesn’t love a good old-fashioned garage project, am I right? With welding aluminum, the sky’s the limit. Maybe you want to try your hand at building a custom boat trailer, or maybe you just want to mess around and see what kind of cool little projects you can come up with. Either way, it’s all about the journey, my friends.
Embracing the Challenges
Now, I know what you’re thinking – “But wait, isn’t welding aluminum, like, super tricky and dangerous?” Well, my friend, you’re not wrong. Welding aluminum does come with its fair share of challenges, but that’s all part of the fun, isn’t it?
One of the biggest hurdles you’ll have to overcome is the whole “controlling the heat” thing. You see, aluminum has a much lower melting point than steel, which means you’ve got to be super careful not to overheat the metal and end up with a big, gooey mess. But trust me, with a little bit of practice and the right techniques, you’ll be welding aluminum like a pro in no time.
Another challenge you might face is the whole “cleanliness” aspect. You see, aluminum is a bit of a diva when it comes to welding – it’s super susceptible to oxidation, which can really mess up your welds if you’re not careful. But fear not, my friends, with a good wire brush and a little bit of flux, you can keep that aluminum squeaky clean and ready to weld.
And let’s not forget about the safety aspect. I mean, let’s be real, welding is no joke, and when you’re dealing with aluminum, you’ve got to be extra vigilant. But, hey, that’s what all that fancy-schmancy PPE is for, right? Slap on that welding helmet, pull on those heat-resistant gloves, and you’ll be good to go.
Embracing the Adventure
But you know what, my friends? Despite all the challenges, welding aluminum boat parts at home is an adventure like no other. It’s a chance to tap into your inner MacGyver, to get your hands dirty, and to create something truly one-of-a-kind.
Imagine the sense of pride and accomplishment you’ll feel when you step back and admire your handiwork – that custom swim platform, that sleek new storage compartment, or that perfectly repaired hull. It’s like a little piece of you becomes a part of that boat, and let me tell you, there’s nothing quite like it.
And who knows, maybe you’ll even discover a hidden talent you never knew you had. Maybe you’ll become the neighborhood’s go-to aluminum welding guru, or maybe you’ll just find a new, deeply satisfying hobby that brings you joy every time you step into the garage.
So, my friends, what are you waiting for? Grab that welding machine, put on your safety gear, and let’s get to work! The open waters of adventure await, and with a little bit of elbow grease and a whole lot of determination, you can make your aluminum boat dreams a reality.
Oh, and before I forget, if you’re ever in need of some top-notch welding services, be sure to check out Corr Connect. These guys are the real deal when it comes to all things welding, from custom fabrication to precision welding and beyond. Trust me, you won’t be disappointed.