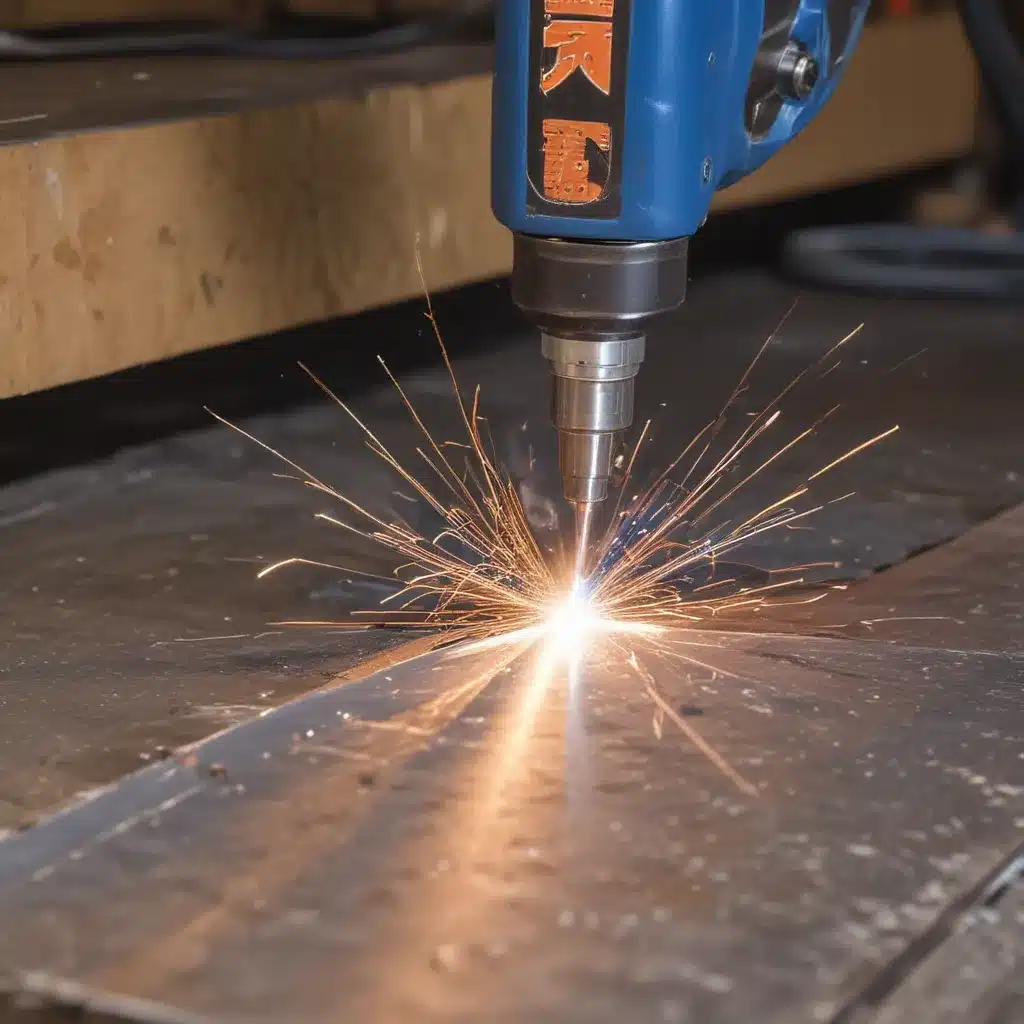
The Essentials of Plasma Cutting
Ahh, the humble plasma cutter – a true workhorse in the world of metalworking! As a seasoned welder, I can tell you that this nifty little tool is an absolute game-changer when it comes to preparing metal edges for that perfect weld. I mean, think about it – with just a few deft swipes, you can slice through thick steel like a hot knife through butter. It’s like having a lightsaber for your workshop, but with way less potential for Jedi-related mishaps.
Now, let’s dive a little deeper into the plasma cutting process, shall we? The basic premise is pretty straightforward – the plasma cutter takes compressed air (or another gas) and uses it to create a high-temperature, high-velocity plasma arc that can melt and vaporize metal. This arc is precisely focused and directed, allowing you to make clean, precise cuts with minimal distortion or heat-affected zones. It’s a far cry from the old-school oxy-acetylene torch, that’s for sure.
One of the key advantages of plasma cutting is its versatility. You can use it to cut a wide range of metal thicknesses, from thin sheet metal all the way up to hefty structural steel. And the best part? The cuts are clean, square, and ready for welding with minimal additional prep work. No more tedious grinding or filing to get those edges just right – the plasma cutter does the heavy lifting for you.
Choosing the Right Plasma Cutter for the Job
Of course, not all plasma cutters are created equal, and the one you choose can make a big difference in the quality of your work. When it comes to selecting the right plasma cutter for your needs, there are a few essential factors to consider.
First and foremost, you’ll want to think about the thickness of the metal you’ll be cutting. Different plasma cutters have varying power outputs and cutting capacities, so it’s important to match the tool to the job at hand. As a general rule of thumb, the thicker the material, the more powerful the plasma cutter you’ll need.
Another important consideration is the quality of the cut. Some plasma cutters are designed to produce clean, precise cuts with minimal slag and dross, while others may leave a bit more mess behind. If you’re working on high-precision welding projects, you’ll want to invest in a plasma cutter that can deliver a clean, consistent edge every time.
And let’s not forget about portability! If you’re a mobile welder or fabricator, you might want to look for a compact, lightweight plasma cutter that you can easily toss in the back of your truck. After all, there’s nothing worse than lugging around a hulking great big machine to every jobsite.
Mastering the Plasma Cutting Technique
Okay, so you’ve got your shiny new plasma cutter all set up and ready to go. Now what? Well, my friend, it’s time to put those skills to the test and start slicing and dicing those metal edges.
The key to getting the most out of your plasma cutter is all about technique. You see, it’s not just a matter of pulling the trigger and watching the sparks fly. Oh no, there’s a bit more to it than that.
For starters, you’ll want to make sure you’re holding the plasma cutter at the right angle – usually around 90 degrees to the workpiece. This helps ensure a clean, straight cut and prevents any wandering or jagged edges. And don’t forget to maintain a consistent standoff distance – that’s the distance between the tip of the plasma torch and the metal surface. Too close, and you might end up with a ragged, uneven cut. Too far, and you risk losing the arc altogether.
Another important technique to master is the speed of your cut. Go too fast, and you might end up with a rough, unfinished edge. Go too slow, and you risk burning through the metal and creating a messy, distorted cut. It’s all about finding that sweet spot and keeping a steady, consistent pace.
And let’s not forget about controlling the plasma arc itself. You’ll want to keep that sucker nice and focused, avoiding any wandering or drifting as you make your cut. A well-focused arc will give you a clean, precise edge that’s ready for welding in no time.
Preparing Metal Edges for Welding
Alright, now that we’ve got the basics of plasma cutting down, let’s talk about how to use this handy tool to prepare metal edges for welding. Because, let’s be real, a good weld starts with a good edge preparation, am I right?
One of the key advantages of using a plasma cutter for edge prep is that it can create a square, consistent edge with minimal distortion. This is crucial for achieving a strong, high-quality weld joint. With a traditional oxy-fuel torch or angle grinder, you might end up with ragged, uneven edges that can be a real pain to work with. But with a plasma cutter, you can slice through that metal like a hot knife through butter, leaving you with a crisp, clean edge that’s ready to be joined.
Another important benefit of using a plasma cutter for edge prep is that it can help minimize the heat-affected zone (HAZ) around the weld area. The focused, high-energy plasma arc produces a very localized heating effect, which means you don’t end up with a big ol’ heat-warped zone around your weld like you might with other cutting methods. This helps preserve the structural integrity of the metal and makes it easier to achieve a solid, reliable weld.
And let’s not forget about the time and effort savings. With a plasma cutter, you can zip through your edge prep in a fraction of the time it would take with traditional grinding or filing. No more hours spent hunched over a workbench, slowly and painstakingly shaping those edges by hand. Just a few quick passes with the plasma cutter, and you’re good to go!
Optimizing Weld Quality with Plasma-Cut Edges
Now, I know what you’re thinking – “Sure, plasma cutting is great for edge prep, but how does it really impact the quality of the final weld?” Well, my friends, let me tell you, the benefits are pretty darn impressive.
For starters, those clean, square edges that you get from plasma cutting help ensure a tight, consistent fit-up between the workpieces. This is crucial for achieving a strong, penetrating weld with minimal voids or gaps. When you’ve got ragged, uneven edges, it can be a real challenge to get that perfect fit, leading to all sorts of welding headaches down the line.
But it’s not just about the fit-up – the plasma-cut edges also help minimize the amount of weld metal required to fill the joint. Because the edges are so clean and square, you don’t have to worry about excessive gap-filling or uneven penetration. This not only saves you time and materials, but it also results in a stronger, more uniform weld that’s less prone to defects.
And let’s not forget about the visual appeal. I don’t know about you, but I always take a certain pride in a clean, well-executed weld. And when you’ve got those crisp, plasma-cut edges as your starting point, it’s just that much easier to achieve a professional-looking, visually stunning final product. It’s like the difference between a gourmet meal and a hastily thrown-together sandwich – the attention to detail really shines through.
Real-World Applications of Plasma Cutting for Welding
Now, I know we’ve been talking a lot about the theoretical benefits of using a plasma cutter for edge prep, but let’s get a little more practical, shall we? Let’s take a look at how this technology is being used in the real world to transform the welding game.
One area where plasma cutting is really shining is in the fabrication of heavy equipment and machinery. Think about all those massive steel components that need to be precisely fitted and welded together – a plasma cutter is the perfect tool for the job. With its ability to cleanly slice through thick steel with minimal distortion, fabricators can achieve a level of fit and finish that simply wouldn’t be possible with traditional cutting methods.
But it’s not just heavy industry where plasma cutting is making waves. In the world of custom metal art and architectural fabrication, this technology is a total game-changer. Imagine the intricate, intricate designs that can be achieved with a plasma cutter’s precision and control. From delicate, laser-like cuts to bold, sweeping shapes, the creative possibilities are truly endless.
And let’s not forget about the automotive industry, where plasma cutting is revolutionizing the way custom cars and hot rods are built. Whether it’s crafting custom brackets and mounts or fabricating complex chassis components, the speed and accuracy of plasma cutting are helping fabricators push the boundaries of what’s possible in the world of high-performance vehicles.
Integrating Plasma Cutting into Your Welding Workflow
So, now that we’ve explored the myriad benefits of using a plasma cutter for edge prep, you might be wondering how to actually integrate this technology into your welding workflow. Well, fear not, my friends, because I’ve got you covered.
The first step is to, well, actually invest in a plasma cutter. And not just any old plasma cutter, mind you – you’ll want to do your research and find a model that’s well-suited to the type of work you’re doing. As we discussed earlier, factors like cutting capacity, cut quality, and portability should all be taken into consideration.
Once you’ve got your shiny new plasma cutter all set up and ready to go, the next step is to start incorporating it into your everyday welding routine. This might mean setting aside a dedicated area in your workshop or jobsite for plasma cutting, or perhaps even integrating the plasma cutter directly into your welding station for maximum efficiency.
And let’s not forget about the importance of proper training and technique development. Mastering the art of plasma cutting takes time and practice, but trust me, it’s well worth the effort. Spend some time dialing in your standoff distance, cut speed, and arc focus, and you’ll be slicing through metal like a true pro in no time.
But the real key to success is embracing the plasma cutter as a integral part of your welding process. Don’t think of it as a standalone tool – think of it as a vital component in your overall welding workflow. By seamlessly integrating plasma cutting into your routine, you’ll be able to take your weld quality and efficiency to new heights.
Conclusion: Unlocking the Power of Plasma Cutting for Welding
Well, there you have it, folks – the lowdown on using a plasma cutter to prepare metal edges for welding. From the basics of how plasma cutting works to the real-world applications of this technology, I’ve covered it all.
And let me tell you, if you’re a welder who’s not already harnessing the power of plasma cutting, you’re truly missing out. This tool is a game-changer when it comes to achieving clean, consistent edges that are primed and ready for high-quality welding. Plus, with the time and effort savings it provides, you’ll be able to streamline your workflow and focus on what really matters – creating stunning, top-notch welds.
So, what are you waiting for? Go forth, my friends, and let the plasma cutter be your trusty sidekick on the path to welding greatness. With a little practice and the right equipment, you’ll be slicing through metal like a hot knife through butter in no time. Who knows, you might even discover a few unexpected uses for this versatile tool along the way.
Alright, I think that about wraps it up. If you’re feeling inspired and want to learn more about our welding services, be sure to check out the Corr Connect website. Happy welding, and may the plasma be with you!