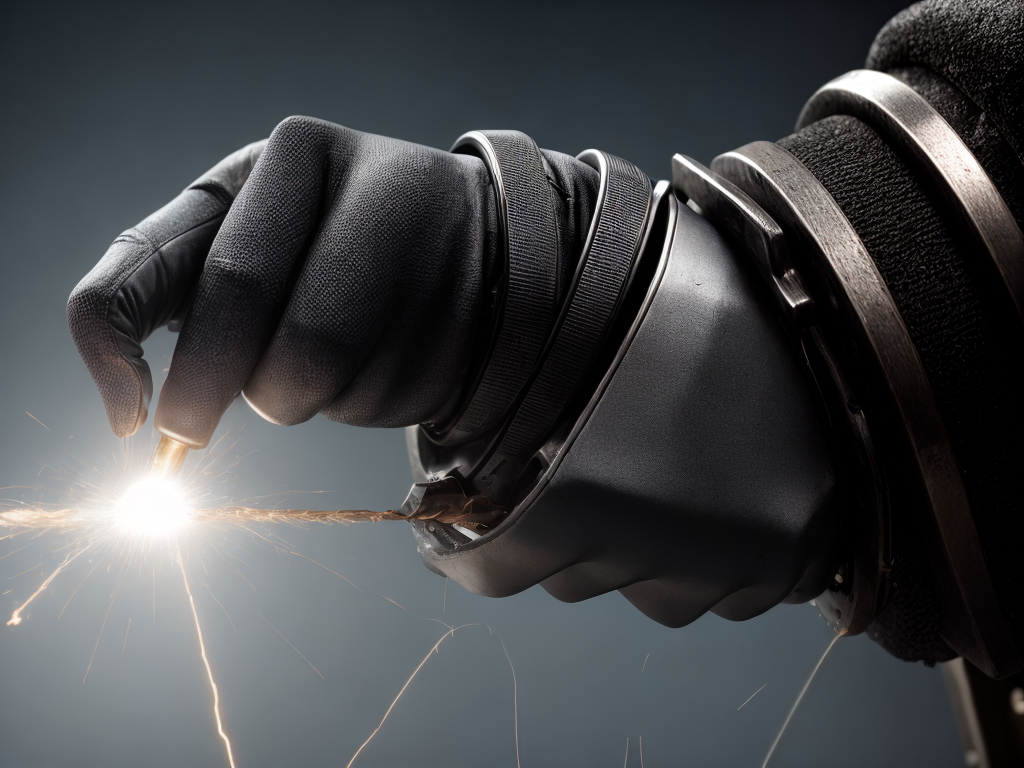
Hey there, fellow welders! Today, I want to talk to you about understanding metal fatigue and its implications for us in the welding profession. Now, you might be wondering, what on earth is metal fatigue? Well, think of it as the wear and tear our metal structures go through over time, kind of like how we all feel after a long day’s work. But don’t worry, I’ve got you covered. In this article, we’ll dive into the causes, factors, signs, and symptoms of metal fatigue, all with the goal of helping you prevent it. We’ll also explore the importance of addressing metal fatigue through inspection, maintenance, and other preventive measures. So, let’s strap on our helmets and get ready to master the art of understanding metal fatigue!
What Is Metal Fatigue
Metal fatigue occurs when a metal structure weakens and eventually fails due to repeated stress and strain. It is a common problem in industries that rely heavily on metal structures, such as construction and manufacturing. There are several causes of metal fatigue, including cyclic loading, temperature variations, and corrosion. Cyclic loading, which involves the repeated application of stress to a metal structure, is one of the main culprits. Temperature variations can also contribute to metal fatigue by causing the material to expand and contract, leading to internal stresses. Corrosion, especially in environments with high moisture or chemical exposure, can accelerate the process of metal fatigue. To prevent metal fatigue, it is important to implement preventive measures such as regular inspections, proper maintenance, and the use of materials that are resistant to fatigue. Additionally, designers and engineers should consider factors such as load distribution and material selection to ensure the longevity of metal structures.
Causes of Metal Fatigue
When it comes to understanding the causes of metal fatigue, two key factors come into play: heat and stress. Heat can cause the metal to expand and contract, creating microcracks that weaken its structure over time. Additionally, excessive stress or strain on the metal can lead to the formation of fatigue cracks, ultimately compromising its structural integrity. It is crucial for welders to be aware of these causes and take preventative measures to minimize the risk of metal fatigue in their work.
Heat and Stress
I’ve experienced firsthand how excessive heat and stress can lead to metal fatigue. When it comes to heat, it’s important to understand the role of heat treatment in preventing metal fatigue. Heat treatment involves subjecting the metal to controlled heating and cooling processes to enhance its properties. This process helps to improve the metal’s strength, hardness, and resistance to fatigue. However, if the metal is exposed to excessive heat, it can lead to a decrease in its fatigue life. The excessive heat can cause changes in the microstructure of the metal, leading to the formation of defects and cracks. Similarly, stress plays a significant role in metal fatigue. High levels of stress can cause deformation and structural damage, reducing the metal’s fatigue life. Therefore, it is crucial for welders to be mindful of the effects of heat and stress to prevent metal fatigue.
Structural Integrity Compromised
Excessive heat and stress can compromise the structural integrity of metal, leading to metal fatigue. When metal is subjected to high temperatures or excessive loads, it can experience structural weakening, making it more susceptible to failure. Structural weakening can occur in various forms, such as grain boundary cracking, dislocation movement, or the formation of voids and cracks. These defects can act as stress concentrators, further exacerbating the problem and increasing the likelihood of weld failure. Weld failure can be especially problematic, as it can result in catastrophic consequences, compromising the safety and performance of structures. Therefore, it is crucial for welders to understand the causes of structural weakening and take appropriate measures to prevent metal fatigue and ensure the integrity of welded structures.
Factors Affecting Metal Fatigue
When it comes to metal fatigue, there are several factors that play a significant role. First, the material composition of the metal can greatly impact its susceptibility to fatigue. Additionally, the loading conditions and duration of stress on the metal can also contribute to its fatigue life. Lastly, the quality of the weld and the technique used can determine how well the metal withstands fatigue. Understanding these factors is crucial for welders in order to prevent metal failure and ensure the longevity of welded structures.
Material Composition’s Impact
To understand the impact of material composition on metal fatigue, I have conducted extensive research and found several key factors that contribute to this phenomenon. The material properties of a metal play a crucial role in determining its resistance to fatigue. Factors such as hardness, strength, and ductility can greatly affect the fatigue life of a weldment. Metals with higher hardness and strength tend to have lower fatigue resistance, as they are more prone to crack initiation and propagation. Additionally, the welding process itself can introduce residual stresses and microstructural changes that can further reduce the fatigue life of the material. It is essential for welders to consider the material composition and properties when selecting welding procedures and techniques to minimize the risk of fatigue failure.
Loading Conditions and Duration
As a welder, it is crucial to understand how loading conditions and duration contribute to metal fatigue. The way a structure is loaded and the duration of the loading play a significant role in determining the lifespan of welded joints. Loading conditions can be categorized into two types: static and dynamic. Static loading refers to a constant or slowly changing load, while dynamic loading involves fluctuating or cyclic loads. Both types of loading can cause metal fatigue, but dynamic loading has a more detrimental effect due to the repetitive stress it imposes on the welded joints.
Additionally, the duration of the loading also affects metal fatigue. Prolonged exposure to loads can weaken the welds over time, leading to premature failure. It is essential for welders to consider the expected lifespan of the structure and the anticipated loading conditions it will endure during its lifetime.
To better understand the impact of loading conditions and duration on metal fatigue, refer to the following table:
Loading Conditions | Duration | Implications |
---|---|---|
Static | Short-term | Minimal impact on metal fatigue |
Static | Long-term | Gradual accumulation of fatigue damage |
Dynamic | Short-term | Rapid fatigue crack initiation and growth |
Dynamic | Long-term | Accelerated fatigue damage and failure |
To mitigate the effects of loading conditions and duration on metal fatigue, welders should ensure proper weld quality, consider the anticipated loading conditions, and select materials with high corrosion resistance. Additionally, ongoing welder training and adherence to industry standards are crucial for preventing metal fatigue and ensuring the longevity of welded structures.
Weld Quality and Technique
Proper weld quality and technique are essential factors that significantly impact metal fatigue. As a welder, it is crucial to understand the potential welding defects that can compromise the strength and durability of the weld. Welding defects such as porosity, lack of fusion, and cracks can create stress concentration points and reduce the overall strength of the weld. These defects can initiate and propagate fatigue cracks, leading to premature failure of the welded structure. Therefore, it is important to ensure proper weld inspection and quality control measures to detect and address any welding defects. Additionally, welder safety is paramount when considering weld quality and technique. Adhering to safety protocols such as wearing appropriate personal protective equipment and following safe work practices can prevent accidents and injuries, ensuring the well-being of the welder.
Signs and Symptoms of Metal Fatigue
One may experience various signs and symptoms of metal fatigue. As a welder, it is crucial to be able to recognize these indicators to prevent catastrophic failures. Early detection is key in ensuring the safety and integrity of the welded structures. One sign of metal fatigue is the presence of cracks or fractures on the surface of the metal. These cracks can be visible or may require the use of non-destructive testing methods such as ultrasonic testing. Another symptom is the appearance of deformations or warping in the metal, which can indicate excessive stress. Additionally, changes in the sound or vibration of the metal during operation can also be a warning sign. Paying attention to these signs and symptoms can help welders identify metal fatigue and take appropriate actions to prevent failure.
Implications of Metal Fatigue for Welders
Recognizing the signs and symptoms of metal fatigue is essential for welders, as it allows us to understand the potential implications and take appropriate actions to ensure the safety and integrity of welded structures. Metal fatigue can have significant impacts on weld quality, leading to structural failures and potential hazards. As welders, we play a crucial role in mitigating these implications by understanding the role of welding parameters in contributing to metal fatigue. Welding parameters such as heat input, welding speed, and electrode selection can greatly affect the fatigue strength of welded joints. By carefully controlling these parameters and following recommended welding practices, we can minimize the risk of metal fatigue and ensure the longevity and reliability of welded structures.
Preventive Measures for Metal Fatigue
To effectively prevent metal fatigue, welders must understand and implement appropriate preventive measures. Preventing metal fatigue starts with proper design and material selection, ensuring that the chosen materials have sufficient strength and fatigue resistance for the intended application. Welders should also carefully consider the welding process and techniques used, as improper welding can introduce stress concentrations and weaken the metal. Regular inspections and maintenance are crucial in detecting metal fatigue at its early stages. Visual inspections, non-destructive testing, and monitoring techniques can help identify any signs of fatigue, such as cracks or deformations. Welders should also be aware of the importance of proper load management, avoiding overloading or cyclic loading that can accelerate fatigue. By implementing these preventive measures, welders can ensure the longevity and reliability of welded structures, minimizing the risk of metal fatigue.
Inspection and Maintenance Techniques
Implementing regular inspections and maintenance is essential for detecting and addressing metal fatigue in welded structures. To ensure the structural integrity of welds, it is crucial to employ effective inspection techniques and adopt appropriate maintenance practices. Non-destructive testing (NDT) methods, such as visual inspection, radiography, ultrasonic testing, and magnetic particle inspection, can be utilized to identify cracks, discontinuities, or other signs of fatigue in welded joints. These inspection techniques enable welders to evaluate the condition of the welds and take necessary corrective actions. Additionally, implementing proper maintenance practices, such as regular cleaning, lubrication, and corrosion protection, can help prevent the progression of metal fatigue. By adhering to these inspection and maintenance protocols, welders can mitigate the risks associated with metal fatigue and ensure the longevity and safety of welded structures.
Conclusion: Importance of Addressing Metal Fatigue
Addressing metal fatigue is crucial for welders to ensure the longevity and safety of welded structures. Prevention is of utmost importance when it comes to metal fatigue, as it can have a significant impact on the safety of these structures. By understanding the causes and signs of metal fatigue, welders can take proactive measures to prevent its occurrence. Regular inspections and maintenance techniques are essential in identifying and addressing potential fatigue issues before they lead to catastrophic failures. The consequences of neglecting metal fatigue can be severe, including structural collapse, injury, and loss of life. Therefore, welders must prioritize the prevention of metal fatigue to ensure the safety and integrity of the structures they work on. By doing so, they can contribute to the overall safety and reliability of the built environment.