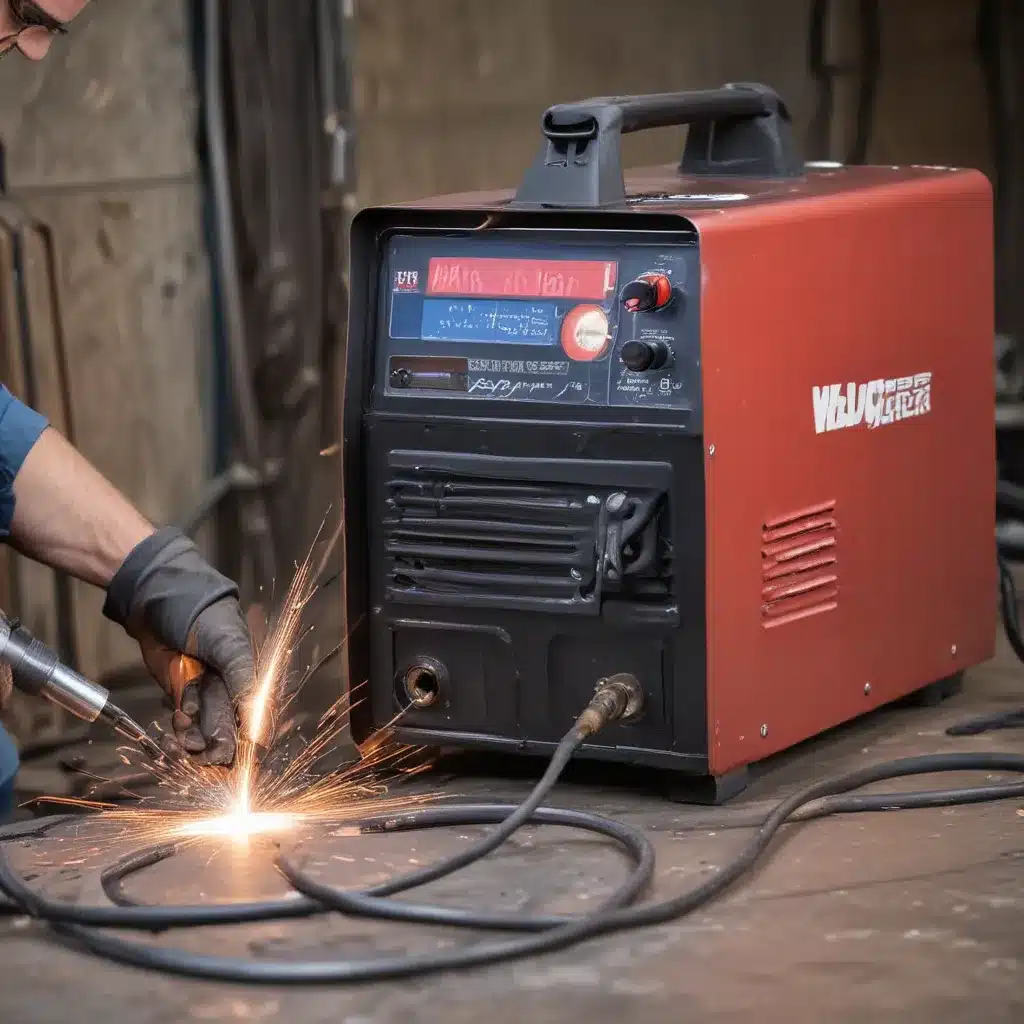
The Curious Case of the Sputtering Welder
Ah, the MIG welder – that trusty workhorse of the metalworking world. It’s the kind of tool that can turn a humble DIYer into a sparky, spatter-wielding superhero, crafting everything from wrought-iron fences to custom hot rod frames. But, as any experienced welder knows, these machines aren’t without their quirks and quirks.
You see, I’ve been there, my friends. I remember the first time my MIG welder started acting up – the sputtering, the uneven bead, the dreaded “burnthrough” that left my workpiece looking like Swiss cheese. It was enough to make even the most seasoned welding pro want to toss their gear out the window and take up needlepoint instead.
But fear not! With a little troubleshooting know-how and the right approach, you can often get your MIG welder back in tip-top shape without too much fuss. So let’s dive in and explore some of the most common MIG welder issues, along with some quick fixes and tips on when it’s time to call in the cavalry (aka, a professional welder).
Common MIG Welder Problems and How to Solve Them
Sputtering and Inconsistent Bead
One of the most frustrating issues you might encounter with your MIG welder is a sputtering, inconsistent weld bead. This can be caused by a variety of factors, from improper wire feed speed to a dirty or worn contact tip.
To tackle this problem, start by checking your wire feed speed. If it’s set too low, the wire won’t be pulled through the gun fast enough, leading to sputtering and inconsistent arc. Crank up the feed speed and see if that does the trick.
Next, take a close look at your contact tip. Over time, these little buggers can get clogged with spatter or even wear down, which can disrupt the smooth flow of wire. Try replacing the contact tip and see if that helps improve the stability of your weld.
If the sputtering persists, it could be an issue with your gas flow. Make sure your gas regulator is set to the proper pressure and that your gas lines aren’t kinked or leaking. A disruption in the gas shielding can cause all sorts of weld quality issues.
Excessive Spatter and Porosity
Ah, spatter – the bane of every welder’s existence. Too much of this pesky, molten metal debris can not only make a mess of your workpiece, but it can also lead to porosity and other weld defects.
One common culprit for excessive spatter is improper wire stick-out. If your wire is sticking out too far from the contact tip, it can cause the arc to become unstable and erratic, leading to spatter galore. Try reducing the wire stick-out and see if that helps.
Another potential cause of spatter is too much or too little voltage. If your voltage is set too high, it can cause the metal to superheat and splatter. On the other hand, if the voltage is too low, the arc won’t have enough heat to properly melt the base metal, leading to a messy, spatter-filled weld.
And let’s not forget about gas flow – a disruption in the shielding gas can expose the weld pool to oxygen, causing porosity and other weld imperfections. Make sure your gas regulator is set to the manufacturer’s recommended pressure and that your gas lines are in tip-top shape.
Burnthrough and Warping
Nothing ruins a perfectly good weld job quite like burnthrough – that dreaded moment when the molten metal eats straight through your workpiece, leaving a gaping hole in its wake. And, of course, where there’s burnthrough, there’s often warping and distortion to follow.
So, what’s the culprit behind this welder’s nightmare? More often than not, it comes down to too much heat input. If your voltage is set too high or your travel speed is too slow, the weld pool can quickly get out of control, leading to that catastrophic burnthrough.
To prevent this, try dialing back the voltage and increasing your travel speed. You might also want to experiment with different welding techniques, like weaving the weld bead or using a stringer pass, to help distribute the heat more evenly.
And let’s not forget about proper prep work. Make sure your base metal is clean and free of any contaminants, and consider using a welding blanket or backing bar to help support the weld and prevent warping.
When to Call in the Pros
Now, I know what you’re thinking – “But wait, I thought you were going to give me all the secrets to fixing my MIG welder woes!” And you’re right, I have shared a bunch of quick fixes and troubleshooting tips. But sometimes, even the savviest DIYer needs to call in the cavalry.
You see, while many MIG welder issues can be resolved with a bit of elbow grease and some basic maintenance, there are certain problems that are best left to the professionals. If you’re dealing with persistent, hard-to-diagnose issues, or if you’re working on a critical structural weld, it’s probably a good idea to bring in a certified welding technician.
These folks have the training, the experience, and the specialized tools to get to the root of the problem and get your welder back in tip-top shape. They can also provide valuable guidance on things like proper welding techniques, safety protocols, and regulatory compliance – all of which are crucial considerations, especially if you’re working on a high-stakes project.
So, don’t be afraid to reach out for help when you need it. After all, the last thing you want is to end up with a shoddy, unsafe weld that could put you or your project in jeopardy. Trust me, it’s better to swallow your pride and call in the pros than to try and tough it out on your own.
The Wrap-up: Keeping Your MIG Welder in Tip-Top Shape
Well, there you have it, folks – a comprehensive guide to troubleshooting your MIG welder and knowing when to call in the big guns. Remember, these machines are powerful tools, but they do require a bit of TLC to keep them running at their best.
Stay on top of regular maintenance, be mindful of common issues, and don’t hesitate to seek professional help when you need it. With the right approach, you can keep your MIG welder humming along, churning out flawless welds project after project.
And who knows, maybe one day you’ll be the one sharing your welding wisdom with the next generation of DIY metalworkers. Until then, keep those sparks flying and your workpieces looking sharp!
If you’re in need of professional welding services, be sure to check out Corr Connect – a leading provider of top-notch welding, metal cutting, and custom fabrication solutions. Their team of certified technicians is ready to tackle any welding challenge, big or small.