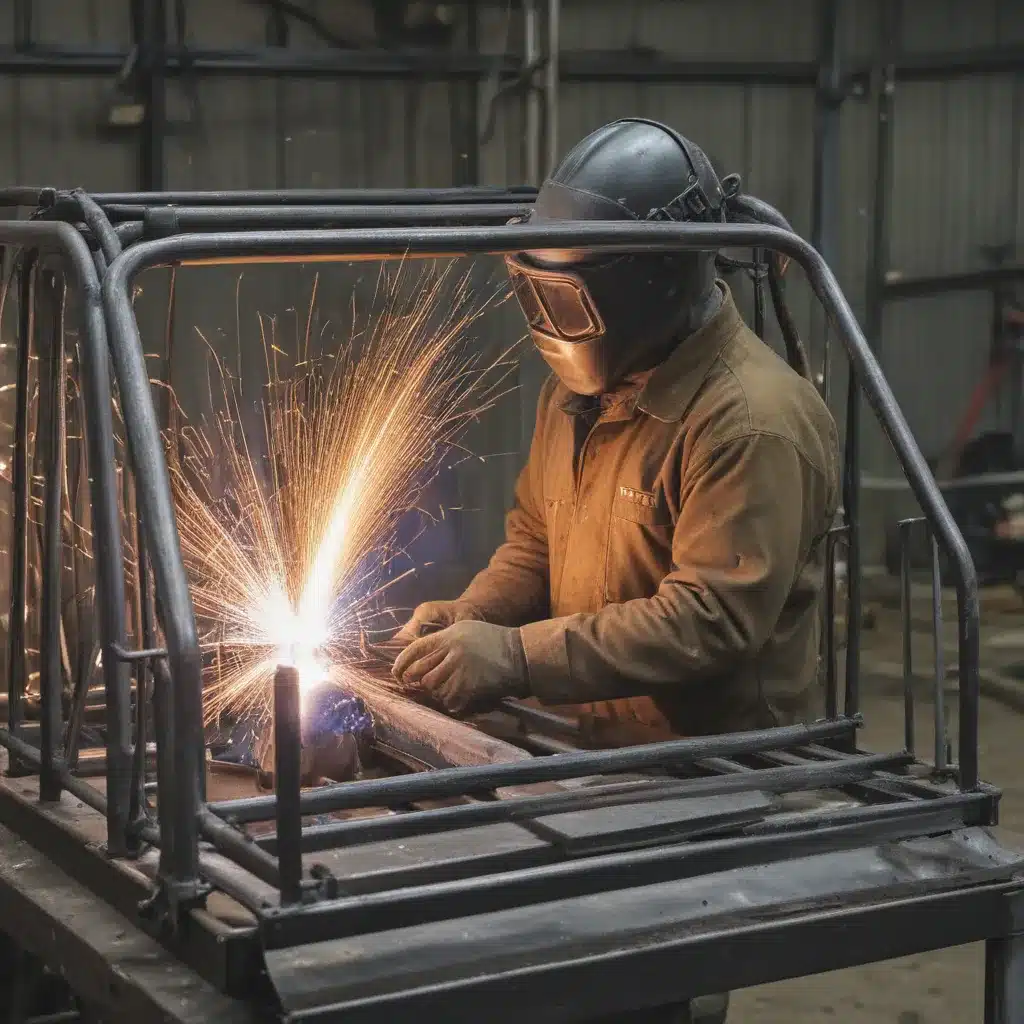
The Importance of Robust Roll Cage and Chassis Design
As an avid motorsports enthusiast and the owner of a custom welding shop, I’ve had the privilege of working on all sorts of high-performance vehicles – from race cars to rally buggies and everything in between. One of the most critical aspects of any off-road or high-speed machine is the roll cage and chassis design. These structural components are quite literally the backbone that keeps the driver safe in the event of a collision or rollover.
Over the years, I’ve learned that there is no one-size-fits-all solution when it comes to fabricating the perfect roll cage and chassis. Each project presents its own unique set of challenges and design considerations. That’s why I always take the time to consult closely with my clients, understand their specific needs and preferences, and then leverage my expertise to bring their vision to life.
In this comprehensive article, I’m excited to share some of the top welding techniques that I’ve honed for fabricating bulletproof roll cages and chassis. Whether you’re building a custom race car, restoring a classic off-road vehicle, or designing a cutting-edge new chassis from scratch, these are the skills and strategies that I rely on to deliver unparalleled results.
Mastering the Art of Structural Welding
The foundation of any strong roll cage or chassis is the welding itself. This is where the true magic happens, as I meticulously fuse together the high-strength steel tubing, plates, and other components that will form the rig’s skeletal structure.
Now, I know what you might be thinking – “Welding is welding, right? How hard can it be?” But trust me, there’s a lot more to it than just striking an arc and laying down some beads. The type of welding process, filler metal, and welding parameters can have a huge impact on the overall strength, integrity, and aesthetic of the final product.
Take, for example, the decision between MIG (Metal Inert Gas) and TIG (Tungsten Inert Gas) welding. MIG is generally faster and more beginner-friendly, making it a popular choice for a lot of DIY projects. But when it comes to critical structural welds, I always prefer to use the TIG process. The narrower, more controlled arc and the ability to meticulously control the weld puddle allow me to achieve superior penetration, fusion, and overall weld quality. This is absolutely essential for ensuring the long-term durability and safety of a roll cage or chassis.
Of course, the specific welding techniques I employ can also vary depending on the base material. Mild steel, chromoly, and aluminum all have their own unique welding characteristics and requirements. I have to carefully adjust my approach to match the metallurgy and ensure I’m creating the strongest possible bonds.
Beyond just the technical aspects, there’s also an artistic element to my welding. I take great pride in laying down clean, uniform beads that not only provide incredible strength but also look absolutely gorgeous. After all, the roll cage and chassis are going to be a major visual focal point of the finished vehicle. I want the welding to be a work of art in its own right.
Precision Tube Bending and Fitment
Once the welding fundamentals are dialed in, the next critical step is precision tube bending and fitment. The roll cage and chassis tubing has to be bent and cut with laser-like accuracy to ensure a perfect, gap-free fit between all the components.
This is where my years of experience and meticulously honed skills really come into play. I’ve become a master at reading engineering drawings, visualizing the 3D space, and then using specialized tube benders, notchers, and other tools to shape the tubing just right. It’s a true dance of geometry, physics, and sheer craftsmanship.
One of the biggest challenges is dealing with the compound bends and complex intersections that are so common in roll cage and chassis design. I might need to bend a piece of tubing in multiple planes, then carefully notch it to fit seamlessly with another component. This requires an almost intuitive understanding of how the metal will behave and deform under all that bending and shaping.
And it’s not just about the bending itself – the fitment is just as critical. I have to ensure that every single joint, intersection, and connection point is perfectly aligned and mating up with laser-like precision. Even the slightest gap or misalignment could compromise the overall strength and integrity of the structure.
To achieve this level of perfection, I rely on a combination of technical skills, specialized tools, and good old-fashioned craftsmanship. I’ll often start by fabricating custom jigs and fixtures to hold the components in place while I weld. And I’m constantly taking measurements, making adjustments, and doing test-fits to ensure everything lines up just right.
It’s a painstaking process, for sure, but the end result is a roll cage or chassis that is not only incredibly strong and safe but also a true work of art. The seamless, gap-free joints and precision-bent tubing are a testament to the time and care I put into every single project.
Attention to Detail and Quality Assurance
Of course, precision welding and tube bending are just the beginning. When it comes to fabricating roll cages and chassis, the devil is truly in the details. I have to be meticulous about every single aspect of the build, from start to finish.
One area that I pay particularly close attention to is the overall fit and finish of the components. Sure, the structural integrity is the most important factor, but I also want the final product to look absolutely stunning. That means ensuring perfect alignment, eliminating any unsightly gaps or mismatches, and meticulously grinding and polishing every weld to a mirror-like sheen.
I also put a huge emphasis on quality assurance throughout the entire fabrication process. At every step, I’m carefully inspecting the work, taking measurements, and conducting thorough non-destructive testing (NDT) to catch any potential issues before they become a problem. This might include techniques like dye penetrant inspection, magnetic particle inspection, or ultrasonic testing – whatever it takes to give me complete confidence in the integrity of the structure.
And when it comes to the final installation, I’m just as meticulous. I work closely with my clients to ensure a perfect fit within the vehicle, carefully aligning the roll cage and chassis components with the body and suspension. I also take the time to add any necessary gussets, bracing, or other reinforcements to further enhance the overall strength and rigidity of the setup.
Ultimately, my goal is to deliver a roll cage or chassis that not only meets or exceeds all the relevant safety standards but also exceeds my clients’ wildest expectations in terms of quality, fit, and finish. I want them to look at the final product and feel a true sense of pride and confidence, knowing that they’re rolling in a machine that is as safe as it is stunning.
Advanced Welding Techniques for Specialized Applications
While the core welding, bending, and fabrication techniques I’ve outlined so far are critical for any roll cage or chassis build, there are also a number of more advanced skills and specialized applications that I’ve had to master over the years.
For example, when working with high-strength alloys like chromoly steel, I have to be extremely careful to avoid heat-related distortion and cracking. This might involve techniques like using a backing bar, pre-heating the material, or carefully controlling the welding parameters to minimize the heat input. It’s a delicate balance, but one that is essential for maintaining the integrity of the structure.
I’ve also had to develop expertise in welding techniques like orbital welding, which is often used for creating consistent, high-quality welds on tubing. This can be incredibly valuable for things like roll cage hoops, where I need to ensure a perfect, seamless bead all the way around the circumference.
And when it comes to custom chassis fabrication, I sometimes need to leverage more advanced metalworking skills, like CNC plasma cutting, to create intricate, precisely-engineered components. This allows me to push the boundaries of what’s possible in terms of strength, weight savings, and overall design.
One of the most rewarding aspects of my work, though, is the ability to collaborate with my clients on truly innovative, boundary-pushing projects. I’ve had the privilege of working with some of the top off-road and motorsports engineers in the industry, and together we’ve brought to life some truly remarkable custom chassis and roll cage designs.
Whether it’s incorporating advanced composite materials, developing specialized suspension mounting points, or devising unique solutions for weight distribution and aerodynamics, I’m always eager to push the limits of what’s possible. It’s a constant learning process, but one that fuels my passion for this craft and keeps me on the leading edge of the industry.
The Importance of Hands-On Experience and Continuous Learning
As you can probably tell, fabricating high-performance roll cages and chassis is not something that can be mastered overnight. It’s a craft that requires years of hands-on experience, ongoing education, and a relentless commitment to honing one’s skills.
Throughout my career, I’ve dedicated countless hours to perfecting my welding technique, studying the latest advancements in metalworking, and experimenting with new fabrication methods. I’ve attended specialized training courses, read countless technical manuals, and collaborated with some of the brightest minds in the industry.
But beyond just the formal education, I’ve also learned that there’s no substitute for real-world, in-the-trenches experience. Every single project I take on, no matter how big or small, is an opportunity to learn something new, refine my approach, and push the boundaries of what’s possible.
Whether it’s working through a complex engineering challenge, troubleshooting an unexpected issue, or discovering a more efficient way to approach a particular fabrication task, each job has contributed to the deep well of knowledge and expertise that I bring to the table.
And I’m always eager to share that knowledge with others. I love mentoring young welders and fabricators, passing on the lessons I’ve learned and helping them develop the skills they need to succeed in this industry. It’s incredibly rewarding to see someone start from scratch, master the fundamentals, and then go on to create incredible, game-changing custom chassis and roll cages of their own.
Ultimately, that’s what drives me – the pursuit of perfection, the thrill of problem-solving, and the deep satisfaction of seeing a client’s vision come to life. It’s a never-ending journey, to be sure, but one that I’m honored to be a part of. And I can’t wait to see what the future holds as I continue to push the boundaries of what’s possible in the world of high-performance chassis and roll cage fabrication.
Conclusion: Crafting Unparalleled Roll Cages and Chassis
As you can see, fabricating truly exceptional roll cages and chassis is a complex and multifaceted endeavor. It requires a unique blend of technical expertise, hands-on craftsmanship, and an unwavering commitment to quality and safety.
But for me, it’s not just a job – it’s a true passion. I love the challenge of solving complex engineering problems, the thrill of bringing a client’s vision to life, and the pride of delivering a finished product that is as safe as it is stunning.
Whether you’re building a custom race car, restoring a classic off-road vehicle, or designing a cutting-edge new chassis from scratch, I’m confident that the welding techniques and fabrication strategies I’ve outlined in this article can help you achieve unparalleled results. From mastering the art of structural welding to perfecting precision tube bending and fitment, I’ve honed the skills and strategies needed to create roll cages and chassis that are truly second to none.
And if you’re ever in the market for these kinds of high-performance fabrication services, I’d be more than happy to chat. You can find me and my team at https://www.corrconnect.org/, where we’re always eager to collaborate on exciting new projects and push the boundaries of what’s possible in the world of custom chassis and roll cage design.
So what are you waiting for? Let’s get to work and create something truly remarkable together!