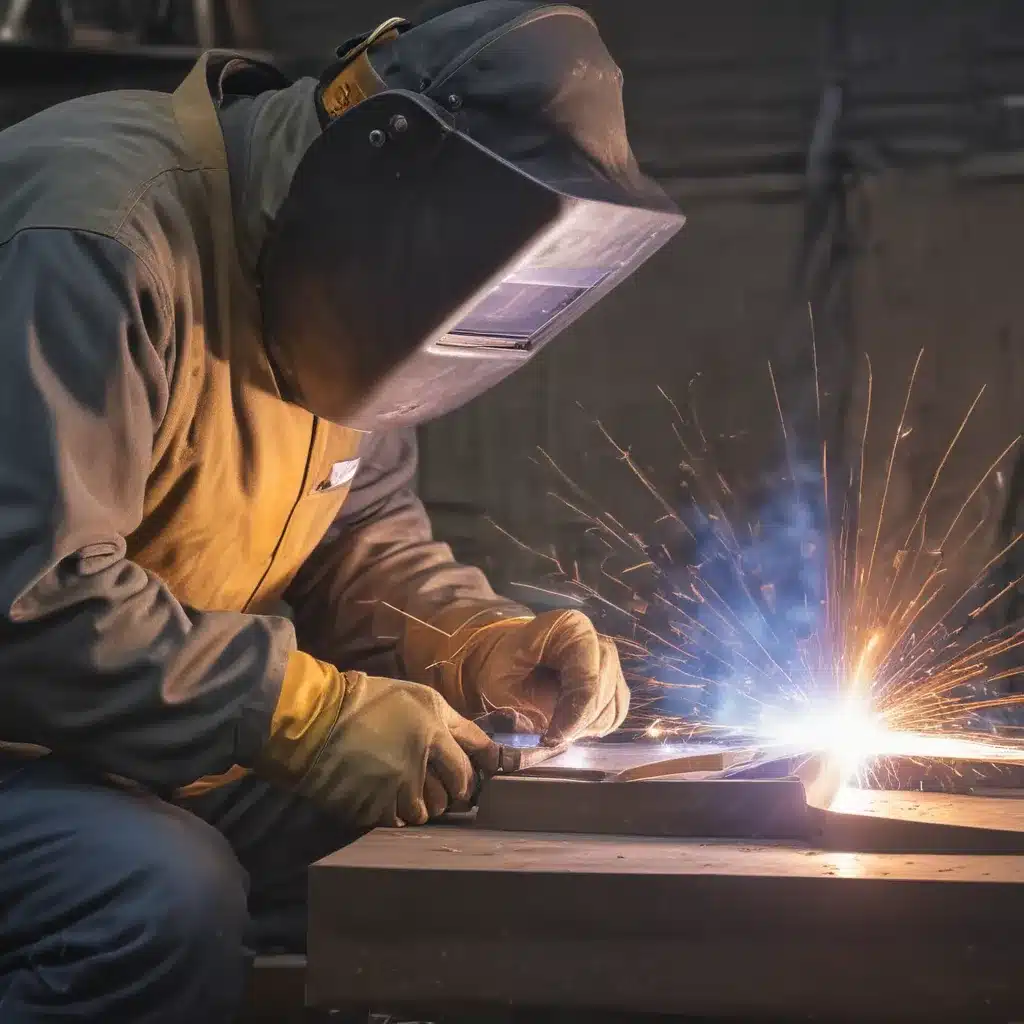
The Challenges of Welding Thin Metals
As I dive into the world of welding thin metals, I can’t help but feel a mix of excitement and trepidation. On one hand, the precision and finesse required to tackle these delicate materials is a true test of a welder’s skills. But on the other hand, the inherent challenges can make even the most seasoned professionals break a sweat.
You see, thin metals are a whole different beast compared to their thicker counterparts. They’re prone to warping, burning through, and generally behaving in ways that can turn a simple job into a hair-pulling exercise in frustration. But fear not, my fellow welding enthusiasts! I’ve been down this road before, and I’m here to share some hard-won tips and tricks that will have you conquering thin metal welds like a pro.
Mastering the Heat Input
When it comes to welding thin metals, the name of the game is heat control. Unlike thicker materials that can handle a bit of thermal abuse, thin metals require a feather-light touch. Apply too much heat, and you’ll end up with a molten mess. But skimp on the juice, and you might as well be trying to weld water.
So, how do we strike that delicate balance? The key is to fine-tune your heat input, using the lowest possible amperage and travel speed that will still create a solid, consistent weld. This might mean experimenting with different electrode sizes, welding techniques, and even gas flow rates to find the sweet spot.
Proper Preparation is Half the Battle
But heat control is only half the battle. Before you even strike that first arc, you need to make sure your workpiece is primed and ready to go. This means meticulously cleaning the surfaces, removing any dirt, grease, or rust that could interfere with the weld.
I’ve found that a good degreasing agent, followed by a light sanding or grinding, can work wonders. And don’t forget to clamp your pieces firmly in place – thin metals have a pesky habit of shifting and warping, and you don’t want to end up with a crooked, uneven weld.
Mastering the Welding Technique
Once the prep work is done, it’s time to put your welding skills to the test. When tackling thin metals, I find that a gentle, almost caressing approach works best. Slow and steady wins the race, as they say.
Start by striking a short arc and maintaining a tight, consistent travel speed. Avoid long welds, as the heat buildup can quickly spiral out of control. Instead, break larger joints into smaller, more manageable sections. And be sure to keep a close eye on your puddle, adjusting your torch angle and travel speed as needed to keep it just the right size.
Minimizing Distortion and Warping
Ah, the bane of every thin metal welder’s existence – distortion and warping. These pesky phenomena can turn your carefully crafted masterpiece into a twisted, unrecognizable mess. But fear not, my friends, for I have some tricks up my sleeve.
One of the keys is to use a technique called “tack welding.” By laying down a series of small, evenly spaced tack welds, you can help anchor your pieces in place and minimize the warping that can occur during the main welding process. Another trick is to weld in a specific pattern, such as a zigzag or staggered sequence, to help balance out the heat input and keep things nice and straight.
The Power of Clamping and Backing Plates
But sometimes, even the most meticulous welding technique isn’t enough to prevent distortion. That’s where the power of clamping and backing plates comes into play.
By using sturdy clamps to hold your workpiece in place, you can effectively “freeze” the metal and prevent it from moving as you weld. And for added insurance, a well-placed backing plate can provide the necessary support to keep your welds perfectly aligned.
Embracing the Art of Thin Metal Welding
As I reflect on my journey of conquering thin metal welding, I can’t help but feel a sense of pride and accomplishment. It’s a delicate dance, to be sure, but one that truly separates the wheat from the chaff when it comes to welding prowess.
But the real beauty lies in the fact that, with a little practice and the right techniques, anyone can master the art of thin metal welding. It’s a constant challenge, sure, but the satisfaction of pulling off a flawless weld on a delicate, paper-thin workpiece is unparalleled.
So, my fellow welders, I encourage you to embrace the beauty and complexity of thin metal welding. Treat it as a puzzle to be solved, a dance to be mastered, and a true test of your skills. And who knows, maybe one day you’ll be the one sharing your hard-won tips and tricks with the next generation of welding enthusiasts.
Now, if you’ll excuse me, I’ve got a custom fabrication project waiting for me, and I can’t wait to put my thin metal welding prowess to the test. Corrconnect.org