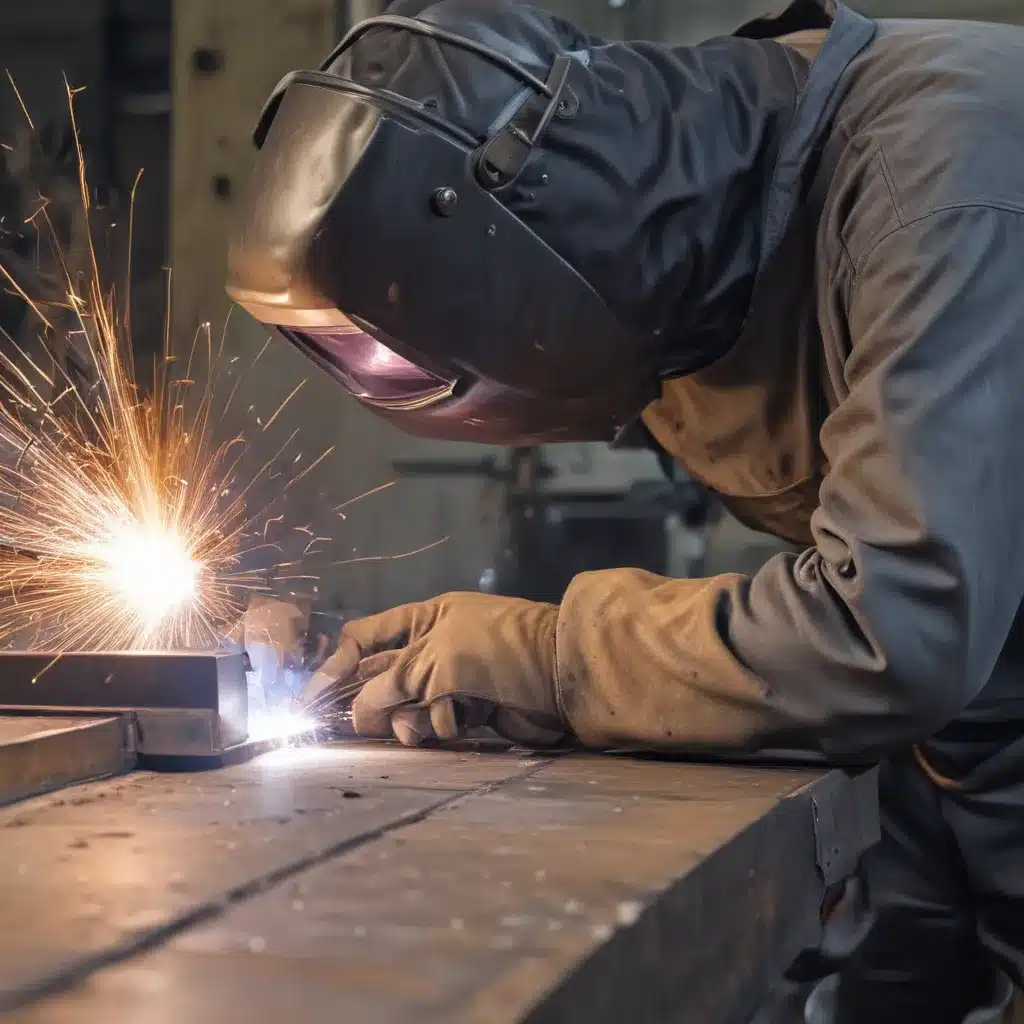
Navigating the Tricky World of Welding Thin Metals
Ah, the joys of welding thin metals – it’s a dance of precision, concentration, and a whole lot of finesse. As a seasoned welder, I’ve had my fair share of experiences (both triumphant and, well, not so much) when it comes to tackling those delicate, razor-thin materials. But fear not, my fellow welding enthusiasts, for I’m here to share some battle-tested tips and tricks that will have you welding thin metals like a pro in no time.
Let’s start with the basics, shall we? Welding thin metals is a bit like walking a tightrope – one wrong move, and suddenly you’ve got a warped, distorted mess on your hands. The key is to understand the unique challenges that come with these featherweight workpieces and learn how to overcome them. Trust me, it’s worth the effort, because the end result can be simply stunning.
Mastering the Art of Heat Control
The number one enemy when welding thin metals? Heat. It’s a delicate dance, my friends, and if you don’t lead it just right, your metal will end up looking more like a Salvador Dalí painting than a pristine weld. But fear not, I’ve got some moves that will have you twirling around those thin sheets with grace and precision.
First and foremost, you’ve got to get a handle on your heat input. This means dialing down the amperage, adjusting your travel speed, and maybe even considering a lower-heat welding process altogether. Trust me, I’ve been there – the temptation to crank up the heat and get it done quick is strong, but it’s a surefire way to end up with a wavy, distorted mess.
Speaking of heat input, have you ever heard of the concept of “preheat” and “interpass temperature”? These are essential considerations when welding thin metals, as they can mean the difference between a flawless weld and a nightmare scenario. Preheat your workpiece to just the right temperature, and maintain that optimal interpass temp throughout the process, and you’ll be well on your way to warp-free glory.
And let’s not forget about the importance of heat sinks, folks. These clever little devices can be a lifesaver when you’re trying to keep those thin metals from twisting and turning like a gymnast on a balance beam. Strategically placed heat sinks can help dissipate that pesky heat and keep your workpiece nice and flat.
Proper Clamping and Fixturing
Now, heat control is only half the battle when it comes to welding thin metals. The other crucial element? Proper clamping and fixturing. Trust me, this is where the real magic happens.
Think about it – those thin sheets of metal are practically featherweights, which means they’re incredibly susceptible to warping and distortion. But with the right clamping and fixturing setup, you can keep those suckers locked down tight and ensure a perfectly flat final product.
I’ve experimented with all sorts of clamping devices over the years – from good old-fashioned C-clamps to fancy-schmancy hydraulic workholding systems. And you know what I’ve learned? There’s no one-size-fits-all solution. It really depends on the specific project, the material thickness, and the overall complexity of the weldment.
What I can tell you, though, is that the key is to create a rock-solid foundation for your thin metal workpiece. Secure it from multiple angles, use backup plates or stiffeners to reinforce weak spots, and don’t be afraid to get a little creative with your clamping and fixturing setup. After all, the more stable and supported your metal is, the less likely it is to warp and twist under the heat of the welding process.
Welding Techniques for Thin Metals
Alright, now that we’ve got the heat control and clamping/fixturing figured out, let’s talk about the actual welding techniques you’ll want to employ when working with thin metals. Because trust me, these bad boys require a whole different approach compared to their thicker, more robust counterparts.
First and foremost, you’ll want to consider using a lower-heat welding process, like TIG or even plasma arc welding. These methods allow for a more precise, controlled heat input, which is exactly what you need to avoid warping and distortion. Trust me, cranking up the old MIG welder is a surefire recipe for disaster when it comes to thin metals.
Another key technique to master? Tack welding. I know, it might sound like a step backward, but trust me, those little spot welds can be a lifesaver when you’re trying to keep your thin metal workpiece in place. Strategically placed tack welds can help anchor your pieces and prevent them from shifting or moving during the full weld process.
And let’s not forget about weld sequencing, folks. When welding thin metals, it’s all about minimizing that pesky heat input, which means you’ll want to use a specific weld sequence to help distribute the heat evenly and reduce the risk of warping. Start in the center, work your way outward, and always be mindful of the heat buildup.
Oh, and one more thing – don’t be afraid to experiment with different weld bead shapes and sizes. Narrow, stringer beads can help reduce heat input, while wider, more overlapping beads can provide additional stability and support. It’s all about finding the right balance for your specific project.
Post-Weld Techniques to Prevent Warping
Alright, so you’ve mastered the art of welding thin metals without warping during the actual process. But the battle’s not over yet, my friends. You’ve still got to tackle the post-weld phase to ensure your hard work doesn’t go to waste.
One of the most important post-weld techniques to consider? Controlled cooling. That’s right, even after the welding is done, you’ve got to be mindful of how quickly (or slowly) your workpiece cools down. Sudden temperature changes can lead to warping and distortion, so it’s crucial to take a gentle, gradual approach to cooling.
Maybe you’ve heard of the old “bury it in the sand” trick? Well, let me tell you, that’s not just an urban legend – it’s a legit technique that can work wonders for preventing warping in thin metals. By slowly cooling your workpiece, you can help relieve those pesky internal stresses and keep everything nice and flat.
And let’s not forget about post-weld straightening, folks. Sometimes, even with all your best efforts, a little bit of warping is just unavoidable. But fear not, because there are plenty of tools and techniques at your disposal to help straighten things out. From good old-fashioned hammers and dollies to more high-tech hydraulic presses, the options are endless.
The key is to be patient, take your time, and really understand the unique properties of the metal you’re working with. Different materials will require different approaches, so don’t be afraid to experiment and find what works best for your specific project.
Real-World Examples and Case Studies
Now, I know I’ve been throwing a lot of technical information your way, but let’s take a moment to look at some real-world examples and case studies of successful thin metal welding projects. Because at the end of the day, the proof is in the pudding, am I right?
One project that really sticks out in my mind was a custom fabrication job we did for a local artist. They had this vision of creating a massive, free-standing sculpture made entirely out of paper-thin stainless steel sheets. Talk about a challenge! But with our careful attention to heat control, precise clamping and fixturing, and specialized welding techniques, we were able to bring their artistic vision to life without a single warp or distortion in sight.
Another case study that comes to mind is a precision welding project we took on for a high-end automotive manufacturer. They needed us to fabricate a series of ultra-thin, intricate body panels for their latest concept car, and the stakes were high. But by closely following the techniques we’ve discussed today – from preheat and interpass temperature control to strategic tack welding and weld sequencing – we were able to deliver a flawless final product that had the client raving.
And let’s not forget about the time we worked with a local aerospace engineer on a cutting-edge satellite component. Talk about thin metals – these were practically translucent! But with our expertise in heat management, clamping, and specialized welding processes, we were able to produce a series of perfectly flat, warp-free parts that met even the most stringent aerospace standards.
The moral of the story? When you’ve got the right tools, techniques, and know-how, welding thin metals doesn’t have to be a nightmare. In fact, it can be a downright rewarding and satisfying experience. And trust me, the sense of accomplishment you’ll feel when you pull off a flawless thin metal weld is truly unparalleled.
Conclusion: Embrace the Challenge, Master the Technique
So there you have it, my fellow welding enthusiasts – a comprehensive guide to navigating the tricky world of thin metal welding without succumbing to the dreaded warping curse. It may seem daunting at first, but I promise, with a little practice and the right techniques, you’ll be welding those delicate sheets like a seasoned pro in no time.
Remember, the key is to stay calm, be meticulous in your approach, and never underestimate the power of proper heat control, clamping, and specialized welding techniques. And who knows, you might even surprise yourself and discover a newfound love for the art of thin metal welding.
So, what are you waiting for? Grab your gear, fire up that welder, and get ready to create some truly stunning, warp-free masterpieces. The world of thin metal welding is your oyster, my friends. Go forth and conquer!
Oh, and before I forget – if you’re ever in the market for top-notch welding services, be sure to check out Corrconnect. Their team of skilled welders and fabricators have the know-how and expertise to tackle even the most challenging thin metal projects, no matter how delicate or intricate. Just a friendly little plug for my fellow welding enthusiasts out there!