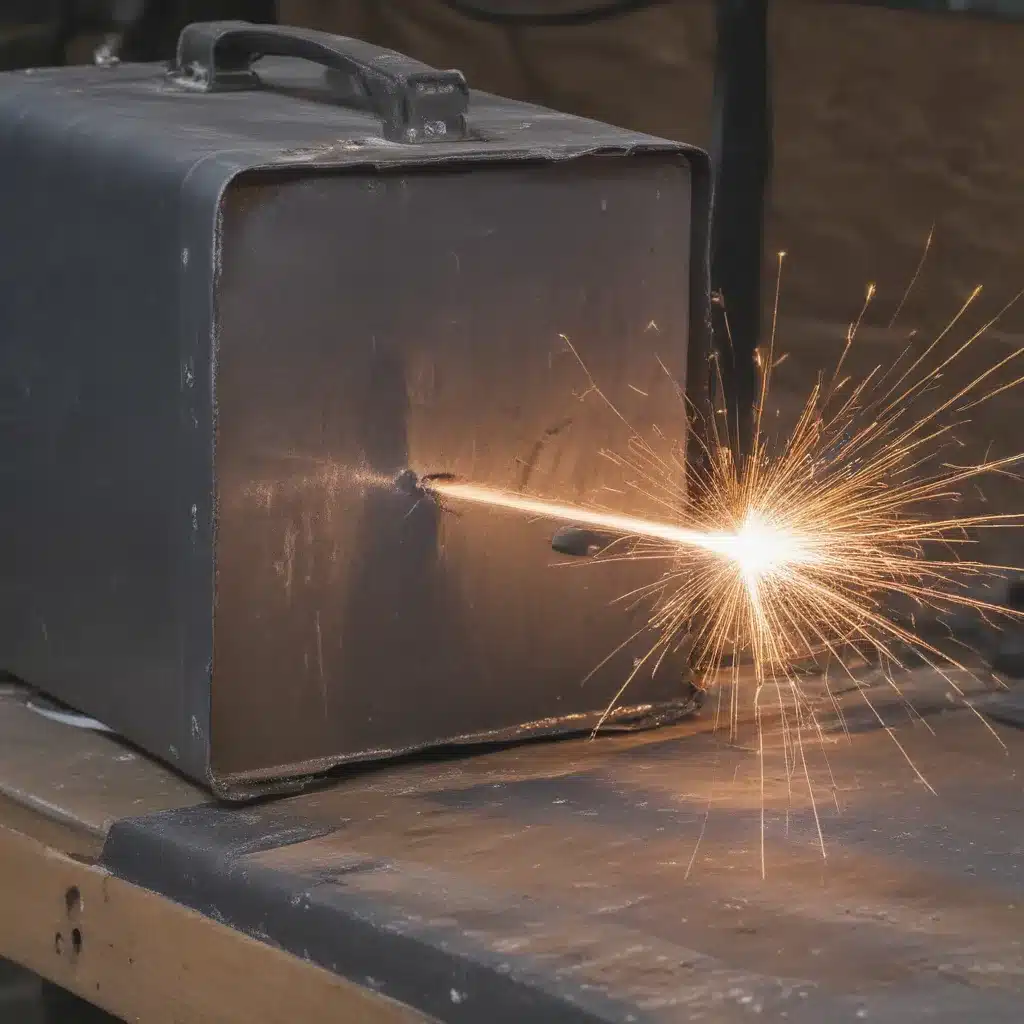
The Flux Core Advantage
As a seasoned welding aficionado, I’ve always been captivated by the sheer power and precision of flux core arc welding (FCAW). There’s just something about the way the molten metal flows and solidifies, creating a robust, durable bond that’s truly mesmerizing. And let me tell you, when it comes to welding, I’m a bit of a mad scientist – always experimenting, pushing the boundaries, and discovering new techniques to get the best possible results.
You see, I believe that FCAW is the unsung hero of the welding world. Sure, it may not have the same glamour and allure as its shiny cousin, TIG welding. But let me tell you, this method packs a serious punch when it comes to real-world applications. Whether you’re working on a heavy-duty construction project, repairing intricate machinery, or fabricating custom metal parts, FCAW is the way to go.
One of the biggest advantages of FCAW is its versatility. Unlike stick welding, which can be a bit finicky and requires a lot of skill to master, FCAW is relatively straightforward and user-friendly. You don’t need to worry about fiddling with a bunch of different electrodes or constantly adjusting your technique. Just fire up that welder, and the flux-cored wire does all the heavy lifting for you.
And let’s not forget about the sheer power of FCAW. This method can tackle some seriously thick, heavy-duty materials with ease, making it a go-to choice for everything from structural steel to stainless steel fabrication. Plus, the self-shielding nature of the flux core means you can use it in all sorts of tricky environments, like windy jobsites or tight spaces, without worrying about contamination or poor weld quality.
Mastering the Flux Core Arc Welding Technique
Now, I know what you’re thinking – “Alright, this all sounds great, but how do I actually master the art of FCAW?” Well, my friends, I’m about to let you in on some of my top tips and techniques for achieving consistently high-quality welds.
First and foremost, it’s all about understanding the fundamentals. You need to have a solid grasp of things like amperage, voltage, wire feed speed, and travel speed. These variables work together in a delicate dance to create the perfect weld, and it’s up to you to learn how to orchestrate them like a pro.
One of the key things to remember is that FCAW is a bit more forgiving than other welding methods when it comes to these settings. You’ve got a bit more wiggle room to play around and find the sweet spot. But that doesn’t mean you can just throw caution to the wind and hope for the best. Nope, you’ve got to approach it with a keen eye and a steady hand.
Another crucial element is proper joint preparation. Trust me, you can have the most skilled welding technique in the world, but if your workpiece isn’t prepped correctly, you’re just setting yourself up for failure. Take the time to properly clean, bevel, and align your parts before you even think about striking that arc. It may seem tedious, but it’s the difference between a solid, long-lasting weld and a hot mess that’s destined for the scrap heap.
And let’s not forget about the all-important shielding gas. Now, I know what you’re thinking – “But wait, I thought FCAW was self-shielding!” And you’d be right. But let me tell you, adding a little bit of shielding gas to the mix can take your welds to the next level. It helps to stabilize the arc, reduce porosity, and create a cleaner, more aesthetically pleasing finish.
Troubleshooting Common FCAW Issues
Of course, as with any welding process, there are bound to be a few hiccups along the way. But fear not, my fellow welding enthusiasts! I’ve got your back when it comes to troubleshooting those pesky FCAW problems.
One of the most common issues you might encounter is excessive spatter. Now, a little bit of spatter is normal and to be expected, but if it’s getting out of hand, it could be a sign that something’s not quite right. Maybe your voltage is too high, or your wire feed speed is out of whack. Or perhaps your contact tip is worn and needs to be replaced. Whatever the culprit, it’s all about making those fine-tuned adjustments to get that spatter under control.
Another common headache is porosity. This can be a real pain in the you-know-what, as it can seriously compromise the integrity of your welds. But fear not, there are a few tricks up my sleeve to help you tackle this problem. First and foremost, make sure your shielding gas is on point. A proper gas flow rate and composition can work wonders in eliminating those pesky pores. And don’t forget about cleanliness – any contaminants on the surface of your workpiece can lead to porosity, so be sure to give it a thorough cleaning before you start welding.
And let’s not forget about those dreaded undercut issues. You know, when the weld bead starts to dig in and create a little trench along the edge of your joint? Yikes! This can be a real headache, but there’s a simple solution: adjust your travel speed. If you’re going too fast, you’ll end up with that nasty undercut. Slow it down a notch, and voila – nice, clean, consistent welds.
The Power of Flux Core Arc Welding in Action
Now, I know what you’re thinking – “All this talk is great, but show me the real-world applications of FCAW!” Well, my friends, I’ve got some juicy stories to share that’ll really showcase the true power and versatility of this welding method.
Take, for instance, the time I was working on a massive steel bridge renovation project. The client came to us with a laundry list of challenges – thick, heavy-duty materials, tight spaces, and a tight timeline to boot. But you know what they say, “When the going gets tough, the tough get welding!” And that’s exactly what we did.
With our trusty FCAW equipment, we were able to tackle those thick bridge supports and deck panels with ease. The self-shielding nature of the flux-cored wire meant we could work in all sorts of tricky, wind-swept conditions without compromising the integrity of the welds. And the sheer power of the process allowed us to crank out those robust, high-quality joints at a blistering pace, keeping the project on schedule and the client one happy camper.
But it’s not just heavy-duty construction projects where FCAW shines. Oh no, my friends – this welding method is a true jack-of-all-trades. Take, for example, the time I was working with a local machine shop on a series of custom fabricated parts for a fancy new piece of industrial equipment.
These parts were intricate, delicate, and required an insane level of precision. Typical MIG welding just wasn’t going to cut it – we needed something with a little more finesse. Enter FCAW. With its ability to deliver a stable, controlled arc and its forgiving nature when it comes to settings, we were able to lay down those perfect, uniform welds without a hitch. The client was blown away by the quality and attention to detail, and needless to say, we’ve been their go-to welding experts ever since.
So you see, the power of flux core arc welding knows no bounds. Whether you’re tackling a massive structural project or crafting delicate custom parts, this versatile welding method is the swiss army knife of the industry. And as for me, well, I’ll keep singing its praises from the rooftops, because I truly believe it’s the unsung hero of the welding world.
Keeping Up with the Latest FCAW Advancements
Now, as any true welding aficionado knows, the world of flux core arc welding is constantly evolving. And let me tell you, I’m always on the lookout for the latest and greatest advancements in this field.
Take, for instance, the recent developments in flux-cored wire technology. I mean, the stuff we’re working with these days is lightyears ahead of what was available even just a few years ago. The manufacturers have really stepped up their game, formulating fluxes that deliver cleaner, more consistent welds with reduced spatter and improved bead appearance.
And don’t even get me started on the advancements in power sources and wire feeders. These days, you’ve got these super smart, digitally-controlled units that can practically run themselves. Just punch in your settings, and boom – perfectly dialed-in, rock-solid welds, every single time. It’s like having a welding genius in your back pocket, ready to lend a hand whenever you need it.
But it’s not just the hardware that’s evolving – the software side of things is getting pretty darn impressive too. I’m talking about these fancy new welding automation systems that can help you plan out your projects, optimize your parameters, and even monitor the quality of your welds in real-time. It’s like having a personal welding coach there to hold your hand and make sure you’re doing everything by the book.
And you know what really gets me excited? The way all of these advancements are making FCAW more accessible and user-friendly than ever before. I mean, gone are the days when you had to be a welding wizard to produce top-notch results. Nowadays, even the most novice of welders can pick up a FCAW setup and start churning out professional-grade work with just a little bit of practice and the right tools.
So if you ask me, the future of flux core arc welding is looking brighter than ever. With all these incredible innovations on the horizon, I can’t wait to see what the next generation of welders will be able to accomplish. One thing’s for sure – if you’re not already on the FCAW bandwagon, now’s the time to hop on board and see what all the fuss is about. Trust me, your welds will thank you.
Wrap-Up: Embrace the Power of Flux Core Arc Welding
Well, there you have it, folks – my comprehensive guide to the art and science of flux core arc welding. From the fundamental techniques to the latest industry advancements, I’ve laid it all out for you in the hopes of inspiring you to embrace the power of this incredible welding method.
Now, I know that some of you out there might still be a little skeptical. Maybe you’re more of a TIG purist, or perhaps you’ve had a few bad experiences with FCAW in the past. But let me tell you, if you give it another chance and really take the time to master the process, you’ll be blown away by the results.
Whether you’re tackling a massive structural project or crafting delicate custom parts, FCAW has the versatility and power to get the job done right, every single time. And with all the incredible technological advancements happening in this space, it’s only going to get easier and more user-friendly as time goes on.
So what are you waiting for, my friends? Grab that welder, fire up that flux-cored wire, and let’s start wielding some magic. Who knows, you might just discover a newfound love for this unsung hero of the welding world. And if you need any help along the way, you know where to find me – I’ll be right here, welding away and ready to lend a hand (or a welding tip or two).