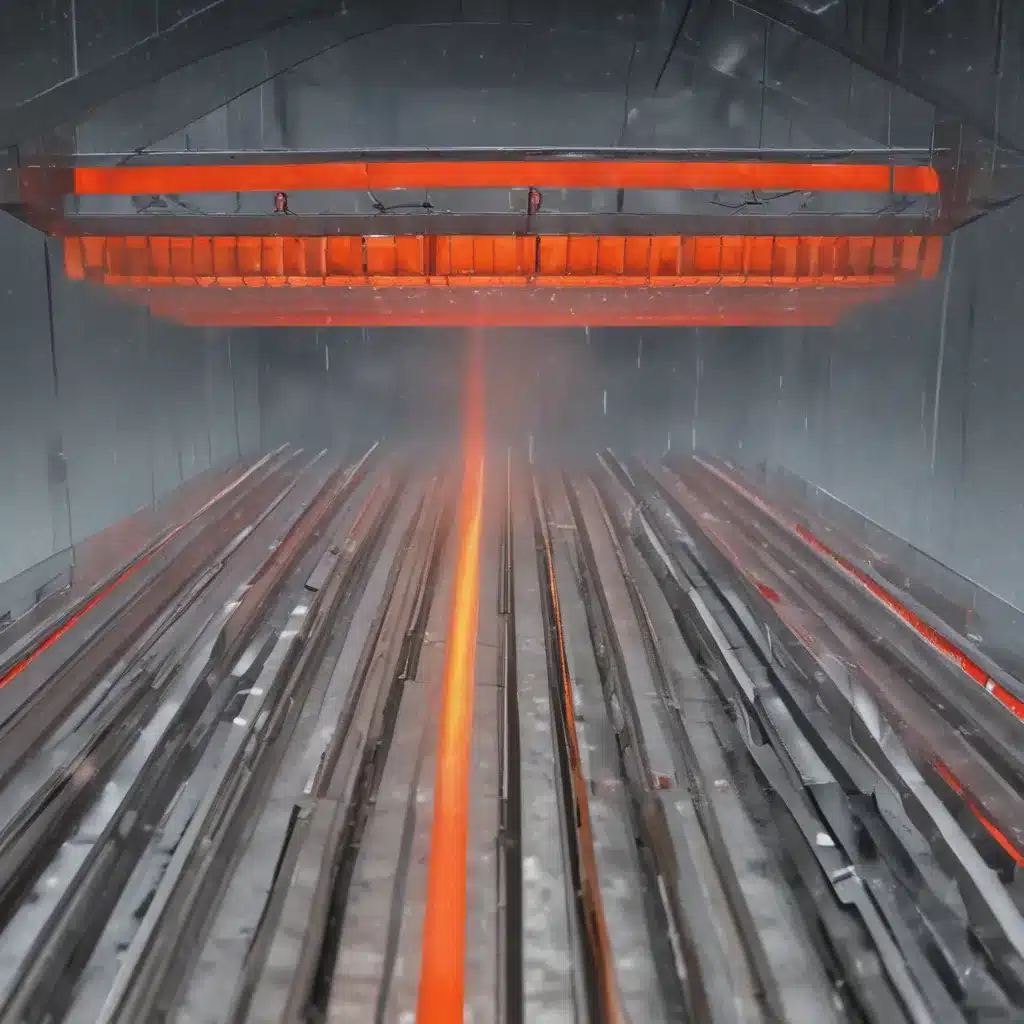
Alright, folks, buckle up because we’re about to dive deep into the world of welding and the crucial role of interpass temperature. Now, I know what you’re thinking – “Interpass temperature? Isn’t that just a fancy term for the temperature between weld passes?” Well, my friends, you’d be absolutely right! But trust me, this topic is way more exciting than it might sound.
Understanding Interpass Temperature
Let’s start with the basics, shall we? The interpass temperature is the temperature of the base metal in between successive weld passes. This temperature is a critical factor in determining the quality and integrity of the final weld. You see, when you’re laying down those beautiful, shiny beads of molten metal, the temperature of the base material can have a significant impact on the microstructure, mechanical properties, and even the overall appearance of the weld.
But why does this temperature matter so much? Well, imagine you’re trying to build a sandcastle, and the sand is just too hot to work with. It’s going to be a real pain, right? The same thing applies to welding. If the base metal is too hot, it can cause the weld to become brittle and prone to cracking. On the other hand, if the base metal is too cold, the weld might not fuse properly, leading to all sorts of issues down the line.
Material Considerations
Now, here’s where things get really interesting. The optimal interpass temperature can vary quite a bit depending on the type of material you’re working with. Let’s take a closer look at some of the common materials used in welding and how their interpass temperature requirements differ.
Steel
Ah, good ol’ steel – the backbone of many of our most impressive structures and machines. When it comes to welding steel, the interpass temperature is typically kept between 150°C and 300°C (300°F and 570°F). This range helps to ensure that the weld microstructure remains stable and free from potential defects, such as cracking or porosity.
Aluminum
Aluminum, the lightweight wonder-metal, requires a bit more finesse when it comes to interpass temperature. Unlike steel, aluminum is highly conductive, which means that it can dissipate heat much more quickly. To prevent the weld from becoming too brittle, the interpass temperature for aluminum is usually kept around 100°C (210°F) or below.
Stainless Steel
Stainless steel, with its corrosion-resistant properties, is another material that demands careful attention to interpass temperature. The ideal range for stainless steel is typically between 100°C and 200°C (210°F and 390°F). This helps to maintain the alloy’s desirable microstructure and prevent the formation of harmful sigma phase, which can compromise the material’s strength and ductility.
Titanium
Titanium, the strong and lightweight marvel of the metal world, has its own unique interpass temperature requirements. Due to its high reactivity, titanium welds must be shielded from the surrounding atmosphere to prevent contamination. The interpass temperature for titanium is typically kept below 230°C (450°F) to avoid the formation of undesirable titanium nitrides and oxides.
Wow, that’s a lot of information to take in, isn’t it? But trust me, understanding the interpass temperature for different materials is crucial if you want to produce high-quality welds that can stand the test of time.
Real-World Examples
Now, let’s put all of this theory into practice with some real-world examples. Take, for instance, the case of a marine fabrication company that specializes in building and repairing luxury yachts. These vessels are subjected to all kinds of extreme conditions, from salty sea air to crashing waves. To ensure that their welds can withstand these harsh environments, the fabricators need to pay close attention to interpass temperature.
In one particular project, they were tasked with repairing a damaged stainless steel railing on a high-end yacht. By carefully controlling the interpass temperature between 100°C and 200°C, they were able to produce a weld that not only looked flawless but also retained the corrosion-resistant properties of the stainless steel. The result? A rail that could stand up to the rigors of life on the open sea.
But it’s not just the marine industry that benefits from proper interpass temperature control. In the automotive manufacturing sector, for example, precision welding is crucial for assembling high-performance vehicles. Imagine the suspension components on a race car – these parts need to be able to withstand immense stresses and forces without failing. By carefully managing the interpass temperature during the welding process, the manufacturers can ensure that the welds are strong, ductile, and able to perform at the highest level.
The Importance of Monitoring and Control
Alright, so we’ve covered the basics of interpass temperature and how it varies across different materials. But how do you actually ensure that you’re maintaining the optimal temperature throughout the welding process? Well, my friends, that’s where monitoring and control come into play.
One of the key tools in the welding technician’s arsenal is the thermocouple. This nifty little device allows you to constantly monitor the temperature of the base metal, ensuring that it stays within the desired range. But it’s not just about checking the temperature – it’s also about actively managing it. This might involve using preheat or post-weld heat treatment, or even adjusting the welding parameters, such as the travel speed or the amperage.
And let’s not forget about the importance of proper documentation and record-keeping. By meticulously logging the interpass temperature for each weld, you can identify any potential issues or trends that might be affecting the quality of your work. This information can then be used to fine-tune your welding processes and ensure that every single weld is a work of art.
The Welding Maestro’s Perspective
Now, I know what you might be thinking – “This all sounds great, but how does it actually play out in the real world?” Well, let me introduce you to my good friend, Julio, the welding maestro. Julio has been in the game for over 20 years, and he’s seen it all when it comes to the importance of interpass temperature.
“You know, back in the day, we used to just kind of wing it when it came to interpass temperature,” Julio tells me, with a chuckle. “We’d, like, eyeball it and hope for the best. But let me tell you, those days are long gone. Nowadays, if you want to be a true welding pro, you’ve gotta be on top of that interpass temperature like a hawk.”
Julio goes on to explain that, in his experience, paying close attention to interpass temperature has been the key to consistently producing high-quality welds, no matter the material. “It’s all about understanding the unique properties of each metal, you know? Steel, aluminum, stainless – they all have their own little quirks when it comes to temperature. And if you don’t respect that, you’re just asking for trouble.”
As we wrap up our conversation, Julio leaves me with one final piece of wisdom: “Remember, my friend, welding is an art, and the interpass temperature is like the brush stroke that makes or breaks the masterpiece. So, keep your eye on that temperature, and you’ll be well on your way to becoming a welding legend.”
Conclusion: Mastering Interpass Temperature for Welding Excellence
There you have it, folks – the lowdown on the importance of interpass temperature for different materials. From steel to titanium, each metal has its own unique requirements when it comes to maintaining the perfect temperature between weld passes.
But as we’ve seen, the benefits of mastering interpass temperature are well worth the effort. By carefully monitoring and controlling this critical factor, you can ensure that your welds are strong, ductile, and corrosion-resistant – no matter the application.
So, whether you’re a seasoned welding pro or just starting out, remember the wise words of Julio: “Respect the temperature, and the welds will come.” Keep that in mind, and you’ll be well on your way to creating weld masterpieces that will stand the test of time.
And if you’re looking to put these interpass temperature principles into practice, be sure to check out the welding services offered by Corr Connect. From arc welding to metal cutting and custom fabrication, they’ve got the skills and expertise to deliver precision welding that’s built to last.
So, what are you waiting for? Let’s get out there and start welding!