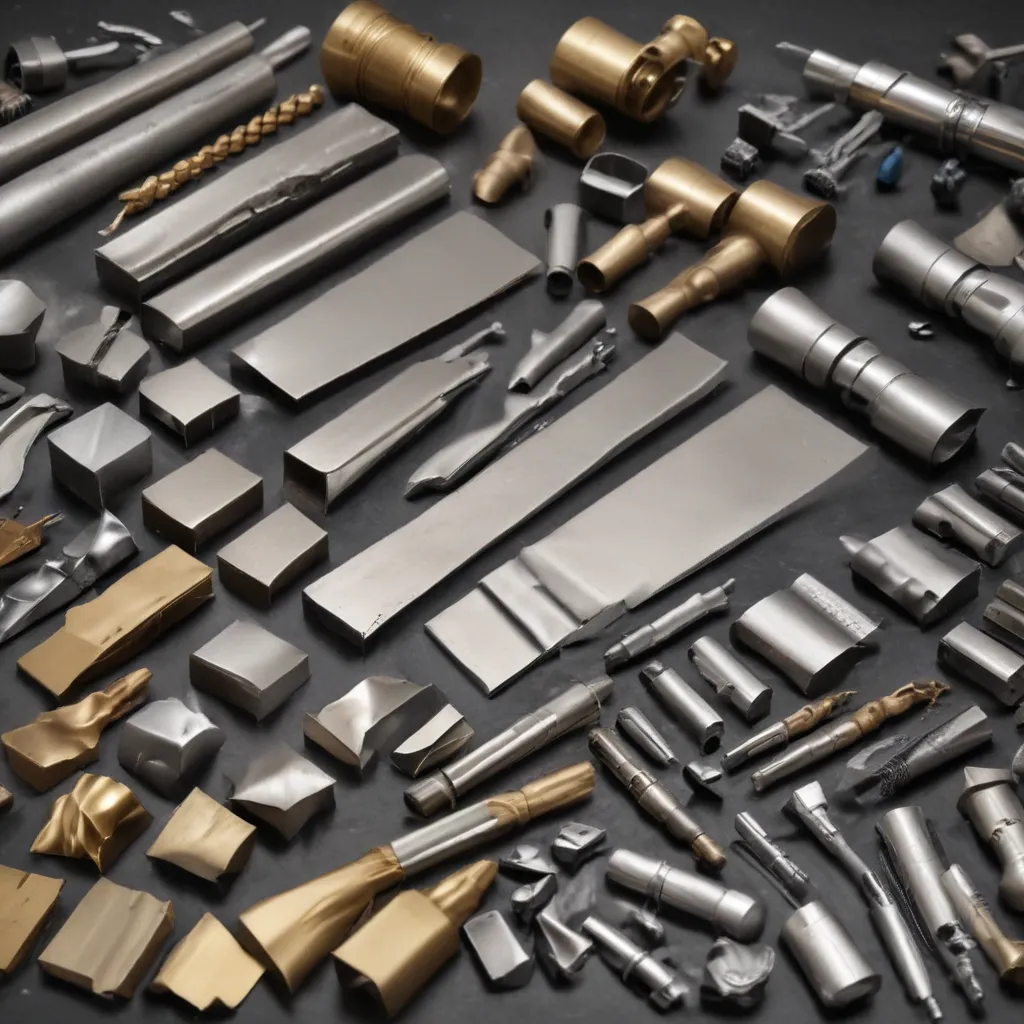
Unlocking the Secrets of Successful Welding: It’s All About the Metals
Ah, the art of welding – a symphony of molten steel, sparks, and sheer craftsmanship. As a seasoned welding professional, I’ve seen it all, from the triumphant arcs that bring structures to life to the heartbreaking failures that can leave even the most experienced welders scratching their heads. But you know what they say, “the devil is in the details,” and when it comes to welding, that couldn’t be more true.
You see, the key to achieving flawless, long-lasting welds isn’t just about having a steady hand and a keen eye. It’s all about understanding the intricate dance between the base metals and the filler metals – the yin and yang, if you will, of the welding world. And let me tell you, it’s a dance that can get pretty complicated, with all the different alloys, melting points, and compatibility issues to consider.
But fear not, my friends! In this comprehensive guide, I’m going to take you on a journey through the world of base metals and filler metals, exploring the nuances, the challenges, and the strategies that will help you become a welding maestro. So, grab a welding mask, fire up the torch, and let’s dive in!
Demystifying Base Metals: The Foundation of Welding
Let’s start with the basics – the base metals. These are the foundation upon which your entire welding project is built, and they come in a wide variety of shapes, sizes, and compositions. From the sturdy steels to the lightweight aluminums, each base metal has its own unique properties, strengths, and weaknesses.
Take, for example, the humble carbon steel. It’s one of the most common base metals used in welding, and for good reason – it’s strong, durable, and relatively affordable. But did you know that the carbon content can greatly affect its weldability? A higher carbon content can make the steel harder and more brittle, making it more prone to cracking during the welding process. On the other hand, a lower carbon content can result in a softer, more ductile steel that’s easier to work with, but may not have the same level of strength.
Then there’s stainless steel, the darling of the culinary world and the bane of many a welder’s existence. With its high chromium content, stainless steel is resistant to corrosion and oxidation, but it also has a much higher melting point than carbon steel. This can make it a real challenge to weld, as the heat input required to melt the base metal can also cause distortion and warping if you’re not careful.
And let’s not forget about the lightweight, yet often temperamental, aluminum. Aluminum is a popular choice for many welding applications, thanks to its low density and high strength-to-weight ratio. But it also has a lower melting point and a tendency to form an oxide layer on its surface, which can make it tricky to weld without the right techniques and filler metals.
The key to success with these base metals is to understand their unique properties and how they’ll interact with the filler metals you choose. It’s a delicate balancing act, but one that’s essential if you want to create strong, durable welds that can stand the test of time.
The Magic of Filler Metals: Bridging the Gap
Now that we’ve covered the foundation, let’s talk about the glue that holds it all together – the filler metals. These are the materials that you’ll be using to fill the gap between the base metals and create the actual weld.
Just like the base metals, filler metals come in a wide variety of compositions, each with their own strengths and weaknesses. Take, for example, the ever-popular mild steel filler wire. It’s a great all-purpose option, offering good strength and ductility, and it’s relatively affordable to boot. But if you’re welding on a high-strength, low-alloy steel, you might want to consider a more specialized filler metal that can better match the properties of the base material.
Or what about the tricky world of aluminum filler metals? With their low melting points and tendency to form oxides, you need to be extra careful when selecting the right filler to ensure a strong, defect-free weld. And don’t even get me started on the challenges of welding dissimilar metals, like stainless steel to carbon steel – that’s a whole other level of complexity!
But fear not, my friends, for there is a method to this madness. By carefully considering factors like the base metal composition, the welding process, and the desired weld properties, you can select the perfect filler metal to create a seamless, high-quality joint. It’s all about finding that perfect match, like a master chef pairing the right wine with their culinary masterpiece.
The Art of Compatibility: Matching Base Metals and Filler Metals
Now, let’s dive a little deeper into the art of matching base metals and filler metals. It’s a delicate dance, to be sure, but one that’s essential if you want to create welds that can withstand the rigors of the real world.
One of the key factors to consider is the strength and ductility of the base and filler metals. You want to choose a filler metal that can match or exceed the strength of the base metal, so that the weld doesn’t become a weak point in the overall structure. But at the same time, you don’t want the filler metal to be so brittle that it’s prone to cracking or breaking under stress.
Another important factor is the melting point and thermal properties of the metals involved. If the filler metal has a significantly lower melting point than the base metal, it can lead to issues like incomplete fusion or excessive distortion. Conversely, if the filler metal has a much higher melting point, it can be difficult to achieve a proper weld without causing damage to the surrounding material.
And let’s not forget about corrosion resistance – a critical consideration for many welding applications. You want to choose a filler metal that can provide the same level of corrosion protection as the base metal, so that the weld doesn’t become a weak link in the chain.
It’s a delicate balancing act, to be sure, but with the right knowledge and experience, you can master the art of matching base metals and filler metals. And let me tell you, the satisfaction of creating a flawless, long-lasting weld is truly unparalleled.
Real-World Examples: Putting It All Together
Now, let’s take a look at some real-world examples of how the principles of base metal and filler metal compatibility can be applied in the welding world.
One project that comes to mind is the restoration of a vintage classic car. The client wanted to replace a damaged fender with a perfect replica, but the challenge was that the original fender was made from a different type of steel than the rest of the car’s body. So, we had to carefully select a filler metal that could not only match the strength and ductility of the base metal, but also provide the same level of corrosion resistance to ensure a seamless and durable repair.
Another example is a commercial kitchen renovation, where we were tasked with welding a new stainless steel countertop to the existing stainless steel structure. In this case, we had to be extra careful in choosing the right filler metal, as stainless steel can be notoriously difficult to weld without introducing defects like cracks or porosity. By selecting a filler metal with a similar composition and thermal properties, we were able to create a weld that was not only strong and visually appealing, but also resistant to the harsh conditions of a commercial kitchen environment.
And let’s not forget about the world of custom fabrication, where the ability to match base metals and filler metals is crucial. Take, for example, a client who needed a high-strength, corrosion-resistant structure for their offshore oil platform. We had to carefully evaluate the base metal composition, the welding process, and the expected service conditions to select the perfect filler metal that could deliver the necessary performance characteristics.
These are just a few examples, but they illustrate the importance of understanding the intricacies of base metal and filler metal compatibility. It’s not just about selecting the right materials – it’s about mastering the art of welding, and using your knowledge and expertise to create flawless, durable welds that can stand the test of time.
The Future of Welding: Emerging Trends and Technologies
As we look to the future of the welding industry, it’s clear that the art of matching base metals and filler metals is only going to become more important. With the development of new alloys, advanced welding processes, and increasingly demanding applications, the need for a deep understanding of metal compatibility will only continue to grow.
One exciting trend that’s starting to emerge is the use of hybrid welding techniques, which combine traditional arc welding with other processes like laser welding or plasma welding. These hybrid approaches can offer improved weld quality, increased productivity, and the ability to tackle even the most challenging material combinations. But of course, with these new technologies comes the need to carefully consider the compatibility of the base metals and filler metals involved.
Another area of innovation is the use of additive manufacturing (also known as 3D printing) in welding and fabrication. By building up layers of filler metal to create custom shapes and features, this technology is opening up new possibilities for designers and engineers. But again, the selection of the right filler metal is crucial to ensuring the integrity and performance of the final product.
And let’s not forget about the growing emphasis on sustainability and environmental responsibility in the welding industry. As we strive to reduce our carbon footprint and minimize waste, the need for more efficient and eco-friendly welding solutions will become increasingly important. This may involve the development of new filler metal formulations that are less resource-intensive or more readily recyclable.
Regardless of the specific trends and technologies that emerge, one thing is clear: the art of matching base metals and filler metals will remain a critical skill for welding professionals. By staying on the cutting edge of this field, you can not only create exceptional welds, but also position yourself as a true leader in the industry.
Conclusion: Mastering the Metals, Mastering the Craft
As I reflect on my journey in the welding industry, I’m constantly amazed by the intricate dance between base metals and filler metals. It’s a delicate balance, to be sure, but one that is absolutely essential to creating strong, durable, and long-lasting welds.
Whether you’re working on a restoration project, a commercial renovation, or a custom fabrication piece, the ability to select the right base metal and filler metal combination is key to your success. It’s not just about technical knowledge – it’s about developing an intuitive understanding of how these materials will interact, and using that knowledge to create truly remarkable results.
So, if you’re a welding professional looking to take your craft to the next level, I encourage you to dive deep into the world of base metals and filler metals. Explore the unique properties of each material, experiment with different combinations, and never stop learning. Because when you master the art of matching these essential elements, you’ll unlock a whole new realm of possibilities in the welding world.
And who knows, maybe one day you’ll be the one sharing your own real-world welding stories, inspiring the next generation of welding maestros. After all, the art of welding is a never-ending journey, and the more we share our knowledge and experiences, the stronger our community will become.
So, what are you waiting for? Grab your welding gear, fire up the torch, and let’s dive in! The world of base metals and filler metals is waiting for you.