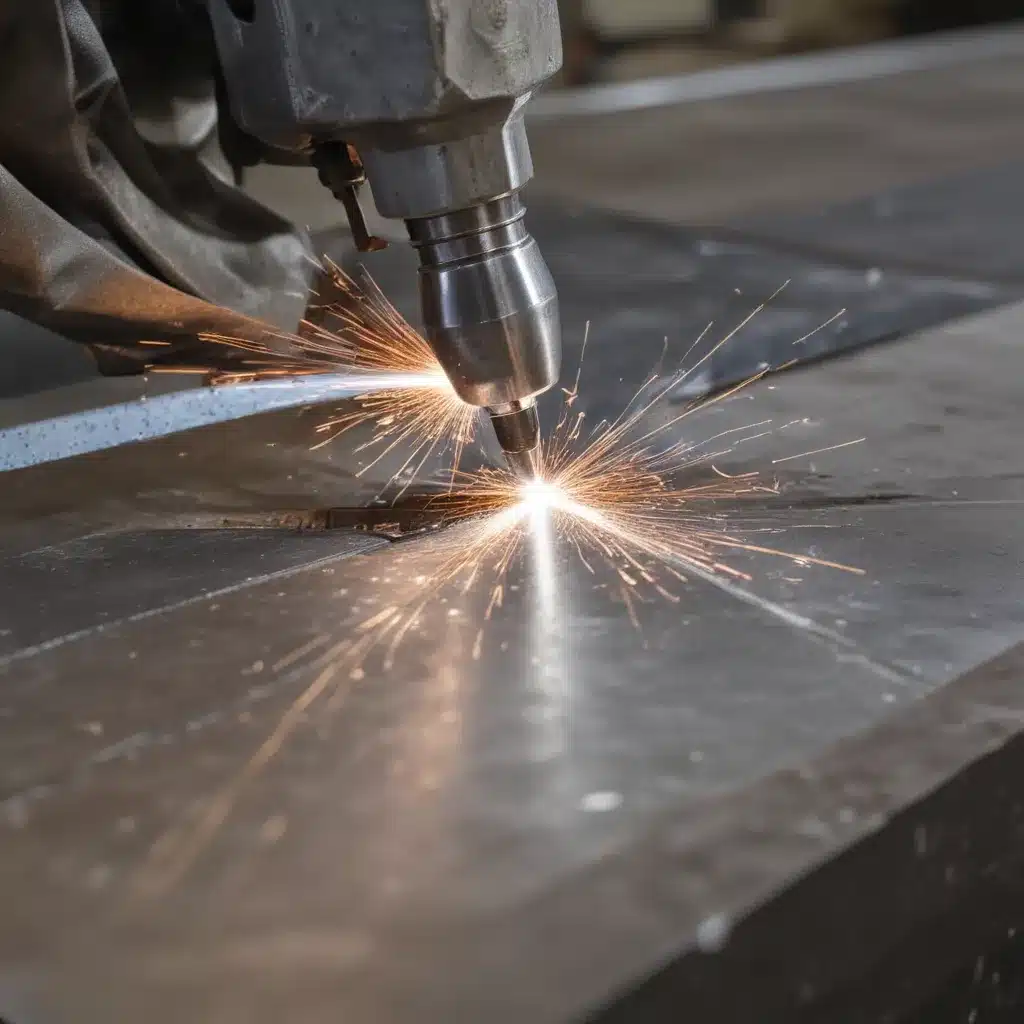
The Quest for Perfection: Navigating the Complexities of Precision Welding
As a lifelong lover of all things mechanical, I’ve always been fascinated by the art and science of precision welding. From the first time I watched a skilled welder coax molten metal into seamless, high-strength joints, I’ve been hooked. The precision, control, and sheer technical mastery required to produce flawless welds in even the most demanding applications – now, that’s the stuff that gets my gears turning.
But let’s be real, precision welding isn’t all fun and games. It’s a field rife with unique challenges that can test even the most seasoned professionals. That’s why I’m thrilled to dive deep into the nitty-gritty of tackling precision welding’s biggest hurdles. So buckle up, because we’re about to go on one heck of a technical journey.
Mastering the Fundamentals: The Building Blocks of Precision Welding
Let’s start with the basics, shall we? When it comes to precision welding, the foundation lies in understanding the core welding processes and techniques. Arc welding, for instance, is a versatile and widely-used method that relies on an electric arc to fuse metal components together. The devil, as they say, is in the details – factors like amperage, voltage, and electrode selection can make or break a precision weld.
But arc welding is just the tip of the iceberg. Metal cutting, using tools like plasma cutters and oxy-fuel torches, is another essential skill for the precision welding aficionado. And let’s not forget about custom fabrication – the ability to design and build complex, one-of-a-kind parts and structures from scratch. This requires a deep understanding of materials, engineering principles, and the latest fabrication technologies.
The key, I’ve found, is to approach each of these fundamental welding disciplines with a relentless dedication to mastery. It’s not enough to simply “know” the basics – you’ve got to live and breathe them, honing your skills through endless practice and experimentation. Only then can you truly harness the power of precision welding and tackle the challenges that lie ahead.
Facing the Challenges: Overcoming the Obstacles to Perfection
Now, let’s get to the heart of the matter – the biggest challenges that precision welding professionals face on a daily basis. Trust me, there’s no shortage of them.
One of the most daunting obstacles is the sheer complexity of the welding process itself. With so many variables at play – from materials and equipment to environmental conditions and operator technique – it can be downright maddening to achieve consistently perfect results. Even the slightest deviation in any one of these factors can lead to costly defects and rework.
And then there’s the issue of precision – the unrelenting demand for flawless, high-tolerance welds that can withstand the most extreme stresses and environments. We’re talking aerospace components, nuclear power plant systems, and cutting-edge medical devices, just to name a few. The margin for error is razor-thin, and any imperfections could have catastrophic consequences.
But perhaps the biggest challenge of all is the need for continuous improvement. In a world that’s constantly evolving, with new materials, technologies, and industry standards emerging all the time, precision welding professionals must be perpetual students. Staying ahead of the curve requires an insatiable thirst for knowledge, a willingness to adapt, and a relentless drive to push the boundaries of what’s possible.
The Path Forward: Strategies for Tackling Precision Welding’s Toughest Challenges
So, how do we overcome these daunting obstacles and rise to the top of the precision welding game? Well, my friends, it’s all about developing a multi-faceted approach that addresses the challenges head-on.
First and foremost, it’s essential to invest in the latest welding technologies and equipment. From advanced digital control systems to high-precision cutting tools, having the right tools for the job can make all the difference in achieving flawless results. But it’s not just about the hardware – it’s also crucial to stay on top of the latest software, simulation tools, and data analytics platforms that can help optimize the welding process and identify areas for improvement.
Equally important is the cultivation of a highly skilled and knowledgeable welding team. This means attracting and retaining the best and brightest welding professionals, providing them with ongoing training and development opportunities, and fostering a culture of continuous learning and innovation. After all, no matter how advanced the technology, it’s the human element that truly sets precision welding apart.
But the real secret to success, in my experience, lies in the relentless pursuit of quality and process improvement. This means implementing rigorous quality control measures, conducting in-depth failure analysis, and continuously refining welding procedures and techniques. It’s a never-ending journey, to be sure, but one that’s essential for staying ahead of the competition and delivering the level of precision that today’s industries demand.
Case Study: Tackling Precision Challenges in Aerospace Manufacturing
And speaking of delivering precision, let me share a real-world example that perfectly encapsulates the challenges we’ve been discussing. Not long ago, our team was tasked with providing precision welding services for a cutting-edge aerospace manufacturer. The project involved the fabrication of critical structural components for a new generation of fighter jets – parts that would be subjected to immense stresses and environmental extremes during flight.
The stakes couldn’t have been higher. A single defect in these welds could have catastrophic consequences, putting both lives and multi-million-dollar aircraft at risk. And with the constantly evolving design and engineering requirements, we knew we’d need to bring our A-game to the table.
So, we dove in headfirst, leveraging our state-of-the-art welding equipment and the expertise of our most seasoned professionals. We conducted rigorous testing and quality control measures at every stage of the process, leaving no stone unturned in our quest for perfection. And you know what? It paid off. The final components passed every inspection with flying colors, earning the trust and admiration of our aerospace partners.
But the real victory, in my mind, was the sense of pride and accomplishment that came from overcoming such daunting challenges. It’s moments like these that remind me why I love this field so much – the thrill of pushing the boundaries of what’s possible, the satisfaction of delivering uncompromising quality, and the knowledge that our work is making a real difference in the world.
Embracing the Future: Innovations and Emerging Trends in Precision Welding
Of course, the journey of precision welding doesn’t end there. As we speak, the industry is undergoing a remarkable transformation, with a slew of exciting innovations and emerging trends poised to reshape the way we approach this crucial discipline.
Take, for instance, the rise of robotic and automated welding systems. These cutting-edge technologies are revolutionizing the way we approach precision welding, allowing for unprecedented levels of consistency, speed, and repeatability. And with the integration of advanced sensing and control systems, these robotic welders are becoming increasingly intelligent, able to adapt to changing conditions and make real-time adjustments to ensure flawless results.
But the innovation doesn’t stop there. We’re also witnessing the rapid advancement of materials science, with the development of new alloys and composite materials that push the boundaries of what’s possible in precision welding. Couple that with the proliferation of additive manufacturing (or 3D printing) technologies, and you’ve got a recipe for truly revolutionary breakthroughs in custom fabrication and design.
And let’s not forget about the growing importance of data analytics and digital integration in precision welding. By leveraging the power of IoT sensors, predictive maintenance algorithms, and cloud-based monitoring platforms, we can gain unprecedented insights into the welding process, identify areas for optimization, and ultimately deliver unparalleled levels of quality and efficiency.
The future of precision welding, my friends, is nothing short of awe-inspiring. And I, for one, can’t wait to see what the next chapter holds. After all, as the old saying goes, “the only constant is change” – and in this dynamic and ever-evolving field, that’s a mantra we must embrace with open arms.
Embracing the Precision Welding Challenge: A Call to Action
So, there you have it – a deep dive into the world of precision welding and the myriad challenges that come with it. From mastering the fundamental skills to staying ahead of the curve in a rapidly changing industry, it’s a journey that’s equal parts exhilarating and daunting.
But you know what? I wouldn’t have it any other way. Because for those of us who live and breathe precision welding, it’s not just a job – it’s a passion, a calling, a relentless pursuit of perfection. And the more we can push the boundaries of what’s possible, the more we can contribute to the advancement of technology, the betterment of society, and the realization of our wildest dreams.
So, if you’re up for the challenge, I invite you to join me on this exciting journey. Whether you’re a seasoned welding professional or a newcomer to the field, there’s always room for more talented and dedicated individuals to make their mark. Together, we can tackle the biggest obstacles, embrace the future of this industry, and redefine what it means to weld with uncompromising precision.
Who’s with me?
If you’re interested in learning more about our precision welding services, I encourage you to check out https://www.corrconnect.org/. Our team of experts is always ready to help you tackle your toughest welding challenges, no matter how complex or demanding they may be. Let’s get to work!