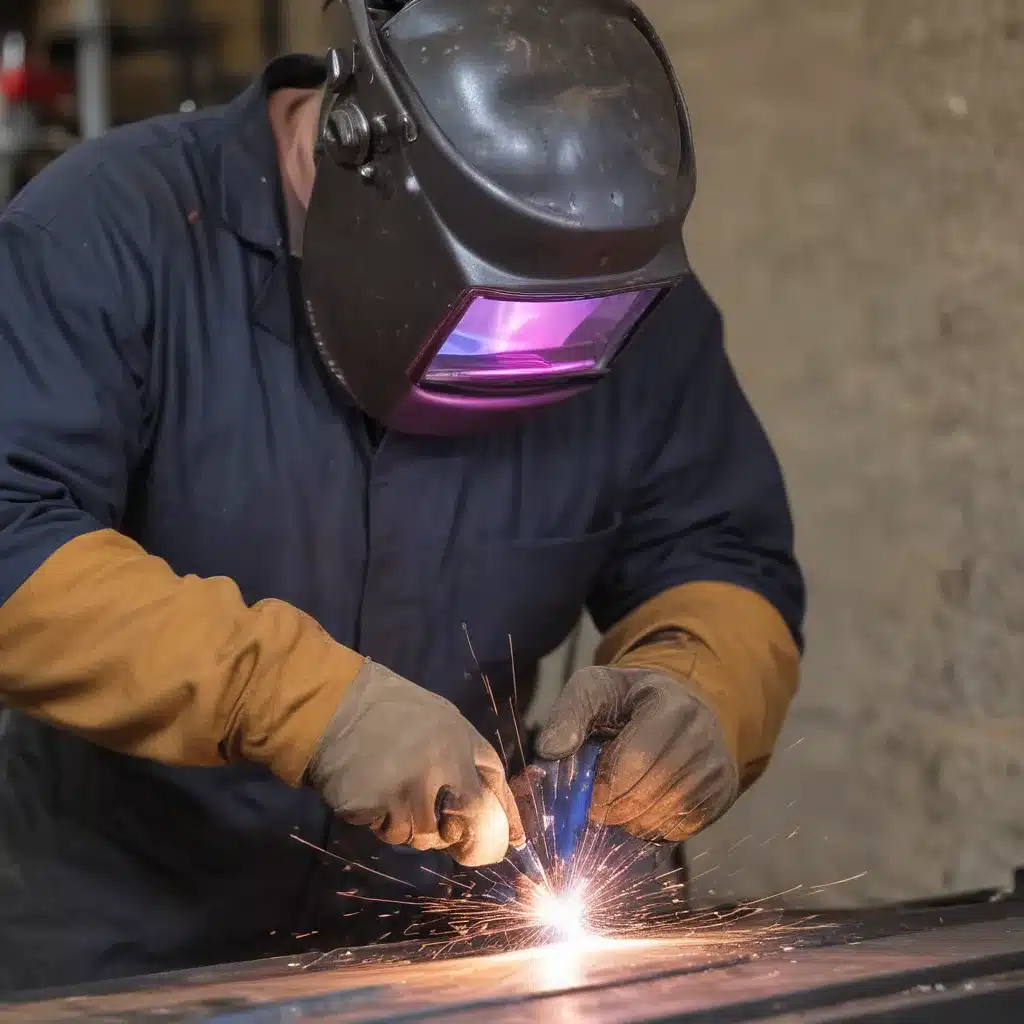
The Arc of Opportunity: Exploring the Wonders of Stick Welding
Ahoy there, fellow metalheads! Today, we’re diving headfirst into the world of stick welding, also known as Shielded Metal Arc Welding (SMAW). Get ready to strap on your welding goggles and join me on a thrilling journey through the sparks and sizzles of this timeless joining technique.
I can still remember the first time I struck an arc – the sheer power and magic of it was enough to make my heart race like a Formula 1 car. The way the molten metal dances and flows, forming a strong, unyielding bond between two pieces of steel, is nothing short of mesmerizing. It’s like watching a symphony of fire and molten metal, and I’m the conductor, orchestrating the whole shebang.
Understanding the Basics: Stick Welding 101
But enough about my love affair with stick welding – let’s get down to the nitty-gritty, shall we? First and foremost, what exactly is stick welding, and how does it work? Well, my friends, prepare to have your minds blown!
Stick welding, or SMAW, is a versatile and widely used welding process that utilizes a consumable electrode, which is coated in a flux material. This electrode, when struck against the workpiece, creates an electric arc that heats the metal, causing it to melt and fuse together. The flux coating on the electrode then melts, forming a protective slag that shields the weld from the elements and helps to create a strong, high-quality joint.
One of the things that makes stick welding so appealing is its simplicity. The equipment required is relatively basic – all you need is a power source, a welding electrode holder, and the electrodes themselves. This makes it an accessible and cost-effective option for many welding applications, from small-scale repairs to large-scale fabrication projects.
The Multifaceted World of Stick Welding
But wait, there’s more! Stick welding is not a one-trick pony – oh no, my friends, it’s a veritable Swiss Army knife of welding techniques. You see, the type of electrode used can have a significant impact on the welding process and the resulting weld. Different electrodes are designed for specific applications, such as mild steel, stainless steel, or even cast iron.
And let’s not forget about the different welding positions! Stick welding can be performed in all positions – flat, horizontal, vertical, and overhead – making it a versatile choice for a wide range of projects. Whether you’re working on a simple steel fabrication or tackling a complex structural weldment, stick welding has got your back.
Mastering the Technique: Tips and Tricks for Stick Welding Success
But of course, with great power comes great responsibility (or something like that). Stick welding, while relatively straightforward, does require a certain level of skill and technique to really shine. Proper electrode selection, arc length, and travel speed are just a few of the factors that can make or break a stick weld.
Fear not, though, because I’m here to share some of my hard-earned wisdom with you. One of the keys to success in stick welding is maintaining a steady, consistent arc. This takes practice, but once you’ve got the rhythm down, it’s like riding a bike – you’ll be zipping along and laying down those beautiful, uniform beads in no time.
Another crucial aspect of stick welding is proper joint preparation. Making sure your workpieces are clean, free of rust and contaminants, and properly fitted together is essential for achieving a strong, high-quality weld. Trust me, skimping on this step is a surefire way to end up with a hot mess on your hands.
The Endless Possibilities of Stick Welding
But the real magic of stick welding lies in its versatility and the endless possibilities it opens up. Whether you’re repairing a broken farm implement, fabricating a custom piece of furniture, or even constructing a massive steel structure, stick welding is there to lend a helping hand.
Take, for example, the case of [Company Name], a local fabrication shop that specializes in custom metal work. They recently took on a project to create a series of intricate stainless steel sculptures for a local art gallery. The tight tolerances and complex shapes required precise stick welding techniques to bring the client’s vision to life.
“Stick welding was the perfect choice for this project,” says [Name], the owner of [Company Name]. “The ability to weld in all positions and the control we had over the weld pool allowed us to achieve the level of detail and craftsmanship the client was looking for.”
And the best part? The [Company Name] team was able to complete the project on time and within budget, thanks to their mastery of stick welding. It’s just another example of how this humble welding process can be transformed into a powerful tool in the right hands.
Embracing the Future: Stick Welding and Beyond
So, my fellow metalheads, are you ready to take the plunge and dive into the world of stick welding? Whether you’re a seasoned pro or a complete newbie, I can assure you that the journey is well worth the effort.
And who knows, maybe one day you’ll be the one orchestrating your own symphony of fire and molten metal, just like me. The possibilities are endless, my friends, so what are you waiting for? Grab your helmet, fire up that arc, and let’s get to welding!
Oh, and before I forget, if you’re in the market for top-notch welding services, be sure to check out https://www.corrconnect.org/. These guys are the real deal – they’ve got the skills, the experience, and the passion to tackle any welding project, big or small. Trust me, you won’t be disappointed.
Happy welding, my friends! May the sparks be with you.