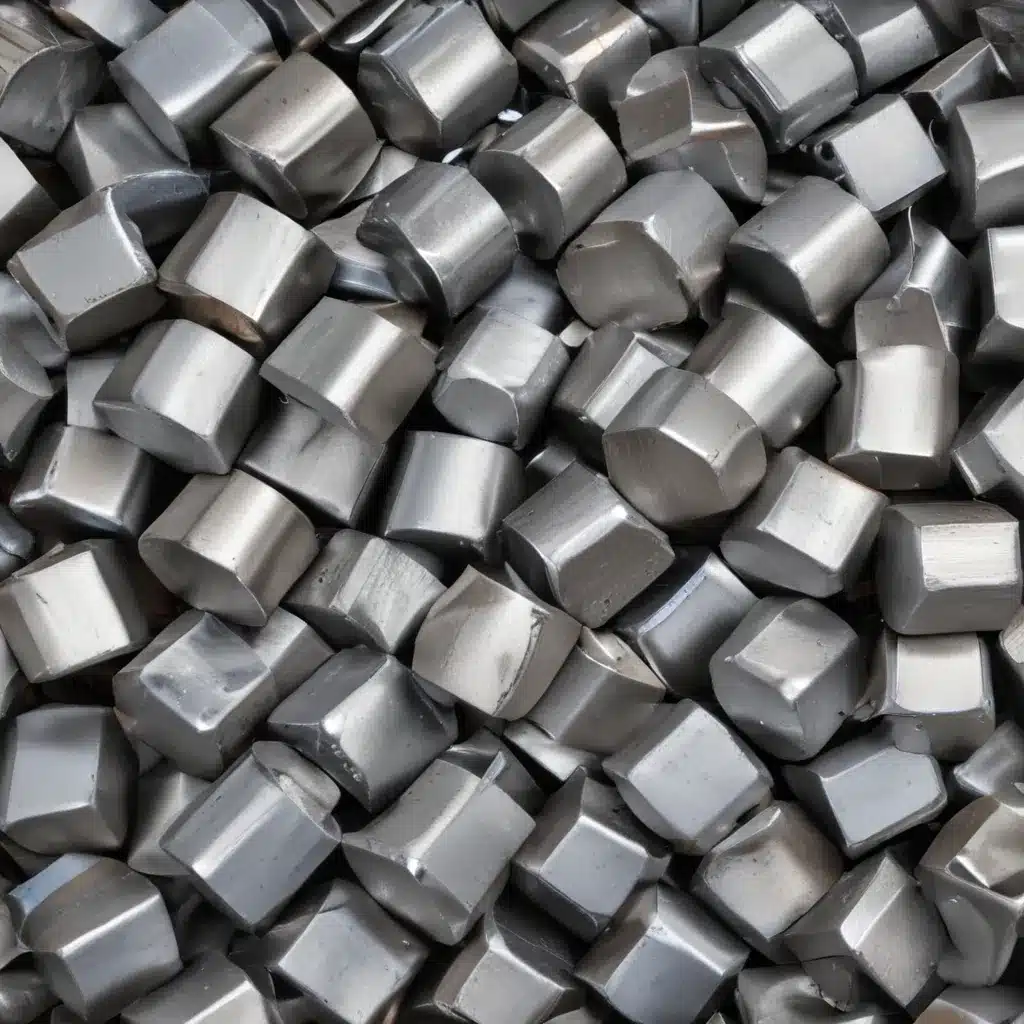
The Metallic Trifecta: Exploring Your Options
Ah, the age-old dilemma for any budding metalworker – which metal should I choose? Steel, aluminum, or stainless steel? It’s a question that’s plagued DIYers and professionals alike, and let me tell you, I’ve been there. But fear not, my fellow metal enthusiasts, for I’m here to guide you through the winding world of metallic selection.
You see, each of these metals has its own unique set of characteristics, strengths, and weaknesses. And depending on your project, one might just be the perfect fit. So, let’s dive in and explore the trinity of metals, shall we?
Steel: The Workhorse of the Metallic Realm
First up, we have good ol’ reliable steel. This sturdy, versatile metal has been the backbone of countless projects, from towering skyscrapers to the humble garden shed. And let me tell you, steel is no slouch when it comes to welding. In fact, it’s one of the most commonly used materials in the welding industry.
One of steel’s biggest draws is its incredible strength-to-weight ratio. This means that you can create sturdy, durable structures without having to lug around a ton of heavy material. And when it comes to welding, steel is a breeze to work with, thanks to its high melting point and excellent heat conductivity.
But steel isn’t just about brute strength. It also has a certain aesthetic appeal, with a range of finishes and coatings that can give your projects a sleek, industrial look. And let’s not forget about the versatility – steel can be easily cut, shaped, and formed to suit your every need.
Aluminum: The Lightweight Champ
Now, if you’re looking for something a little lighter on your feet, aluminum might just be the metal for you. This silvery-white wonder is incredibly lightweight, yet still manages to pack a punch when it comes to strength and durability.
One of the biggest advantages of aluminum is its corrosion-resistant properties. Unlike steel, which can rust and corrode over time, aluminum forms a protective oxide layer that shields it from the elements. This makes it a great choice for outdoor projects or anything exposed to the elements.
But don’t let its lightweight nature fool you – aluminum is still a force to be reckoned with when it comes to welding. It may require a bit more finesse than steel, but with the right techniques and equipment, you can create some truly impressive welds.
And let’s not forget about the aesthetic appeal of aluminum. With its clean, modern look, it can add a touch of sophistication to any project. Plus, it’s easy to anodize or powder-coat, giving you endless possibilities for customization.
Stainless Steel: The Shiny, Sleek Sidekick
Last but certainly not least, we have stainless steel – the shiny, corrosion-resistant sibling of good ol’ carbon steel. This material is a favorite among professional welders and fabricators, and for good reason.
One of the biggest advantages of stainless steel is its resistance to corrosion and rust. Thanks to the addition of chromium, stainless steel can withstand exposure to moisture, chemicals, and other environmental factors without succumbing to the dreaded rust demon. This makes it a great choice for outdoor projects, food-related equipment, and anything that needs to maintain a pristine appearance.
But stainless steel isn’t just about durability – it also has a certain je ne sais quoi when it comes to aesthetics. With its mirror-like finish and sleek, modern look, stainless steel can add a touch of elegance to any project. And when it comes to welding, the process is relatively straightforward, with a lower heat input required compared to carbon steel.
However, it’s worth noting that stainless steel can be a bit more challenging to work with than its carbon-based cousin. The higher nickel content can make it more prone to warping and distortion, so it’s important to have a steady hand and a keen eye when welding stainless steel.
Making the Metal-lurgical Decision
So, there you have it – the metallic trifecta in all its glory. Steel, aluminum, and stainless steel – each with its own unique set of characteristics and applications. The question is, which one will you choose for your next project?
Well, my friends, that’s where the real fun begins. You see, the choice of metal isn’t just about strength and durability – it’s also about personal preference, project requirements, and good old-fashioned trial and error.
Are you looking for something sturdy and reliable? Steel might be your new best friend. Need a lightweight material that can stand up to the elements? Aluminum could be the way to go. Or maybe you’re after that sleek, sophisticated look of stainless steel?
The truth is, there’s no one-size-fits-all answer. It all comes down to what you’re trying to achieve and the specific needs of your project. But fear not, because that’s where the experts at Corrconnect come in. We’ve got the knowledge, the experience, and the passion to help you navigate the metallic maze and find the perfect material for your needs.
So, what are you waiting for? Grab your welding gear, fire up that forge, and let’s get to work! The metallic world is your oyster, my friends, and the only limit is your imagination.
Comparing the Metals: A Side-by-Side Breakdown
Now, to help you make that all-important metal selection, let me break down the key characteristics of each one in a handy little table. Take a gander, and let the metallic magic begin!
Characteristic | Steel | Aluminum | Stainless Steel |
---|---|---|---|
Strength | High | Moderate | High |
Lightweight | No | Yes | No |
Corrosion Resistance | Moderate | High | Excellent |
Weldability | Excellent | Good | Good |
Aesthetic Appeal | Industrial | Modern | Sleek |
Cost | Moderate | Low | High |
There you have it, folks – the metallic trifecta in all its glory. Now, it’s time to put on your thinking caps and decide which one is the perfect fit for your next project. And remember, if you need any help along the way, the team at Corrconnect is always here to lend a hand (and a welding torch).
Tailoring Your Welding Approach
Of course, once you’ve settled on your metal of choice, the real fun begins – the welding process itself. And let me tell you, each of these metals requires a slightly different approach to ensure a flawless finish.
For steel, it’s all about finding the right balance of heat input and filler material. You want to make sure you’re not overheating the metal, which can lead to warping and distortion. And don’t forget about the importance of proper joint preparation and cleaning – these little details can make all the difference in the world.
When it comes to aluminum, the key is to keep things cool. This lightweight metal has a lower melting point than steel, so you need to be extra vigilant about controlling the heat input. And don’t be afraid to experiment with different welding techniques, like TIG or MIG, to find the one that works best for your project.
And then there’s stainless steel – the diva of the metallic world. This material can be a bit more finicky when it comes to welding, but with the right techniques and a steady hand, you can create some truly breathtaking results. Remember to keep an eye on those pesky warping and distortion issues, and don’t be afraid to use a little shielding gas to keep things looking fresh.
Embracing the Unexpected: Real-World Welding Adventures
But you know, welding isn’t just about the technical nitty-gritty – it’s also about the unexpected twists and turns that come with the territory. And let me tell you, I’ve had my fair share of welding adventures over the years.
Take that one time I was working on a custom fabrication project for a client, and I accidentally dropped my welding rod right into the molten pool of metal. Talk about a heart-stopping moment! But you know what they say – when life gives you lemons, you just gotta roll with it. So, I grabbed a pair of tongs, fished that sucker out, and got right back to work.
Or that time I was tasked with welding a precision component for a high-tech piece of machinery. Talk about pressure, am I right? But I put on my game face, double-checked my technique, and ended up with a weld that was so smooth and uniform, it could have been mistaken for a work of art.
And let’s not forget the sheer joy of discovering a new welding process or material that just clicks with your style. It’s like finding your soul mate, but instead of a person, it’s a hunk of metal and a perfect bead. Ah, the simple pleasures in life!
The Welding Wheel of Fortune: Embracing the Unknown
You see, the world of welding is full of surprises, both good and, well, not-so-good. But that’s all part of the fun, isn’t it? It’s like a never-ending game of Wheel of Fortune, where you never know what’s going to come up next.
And that’s why I love this craft so much – it’s a constant learning experience, filled with challenges to overcome and new techniques to master. Whether you’re a seasoned pro or a welding newbie, there’s always something new to discover.
So, embrace the unexpected, my friends. Revel in the thrill of the unknown, and don’t be afraid to take a few risks along the way. Because who knows, that little mishap might just lead you to your next great welding adventure.
And remember, you don’t have to go it alone. The team at Corrconnect is always here to lend a helping hand, whether you need advice on material selection, welding techniques, or just a friendly ear to listen to your latest welding war story.
So, what are you waiting for? Grab your welding gear, fire up that forge, and let’s get to work! The metallic world is your oyster, and the only limit is your imagination.