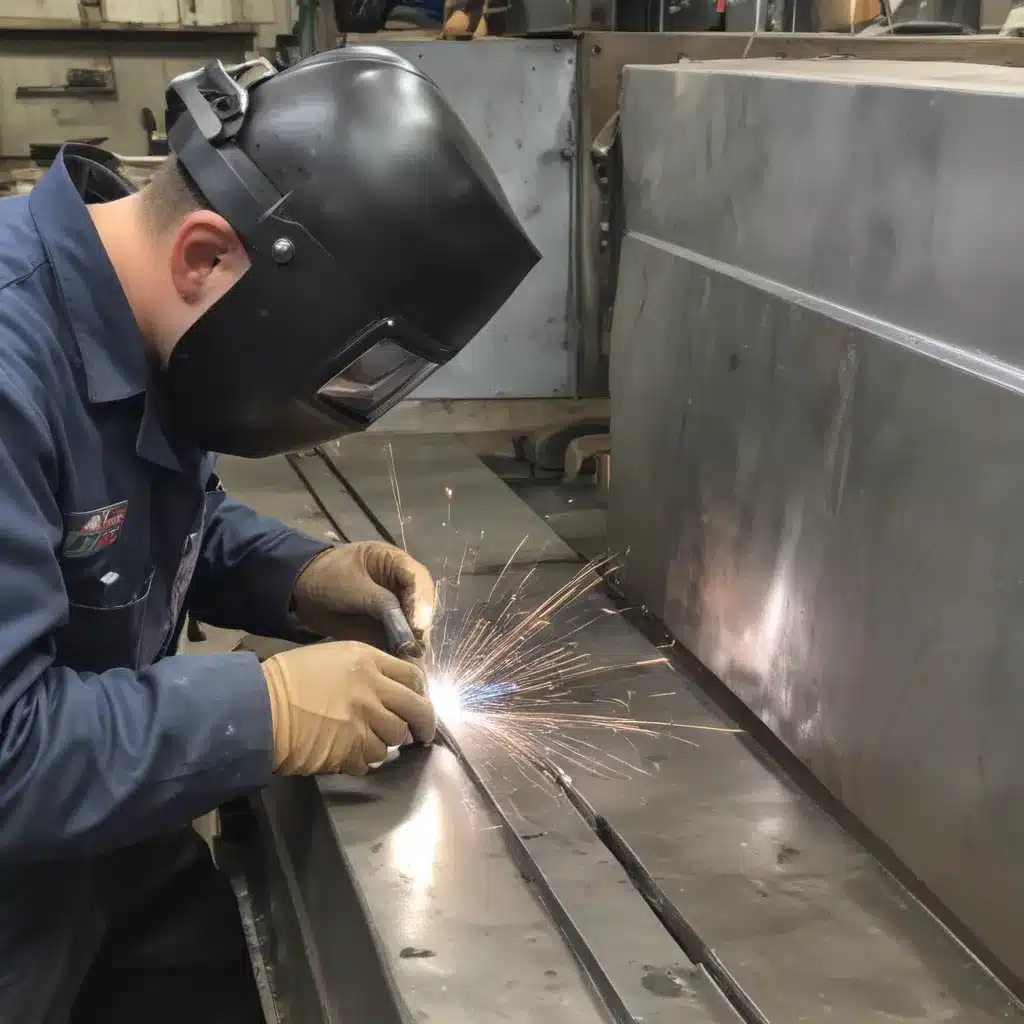
The Art of Perfection: Mastering the Intricacies of Welding
Ah, the wonderful world of welding – where sparks fly, metal mingles, and the very fabric of our industrial landscape is forged, quite literally, with each sizzling seam. As a seasoned welding professional, I’ve seen it all – from the breathtaking beauty of a perfectly executed weld to the heart-stopping horror of a catastrophic failure. And let me tell you, there’s nothing quite like the thrill of achieving that elusive state of welding nirvana: the flawless, gleaming bead that could put a prima ballerina to shame.
But let’s be real, my friends – perfection in welding is no easy feat. It’s a delicate dance, a strategic symphony of variables that must be meticulously orchestrated to achieve that coveted outcome. Fear not, however, for I’m here to guide you through the intricate labyrinth of quality control, arming you with the knowledge and tools you need to conquer the welding world and produce welds that would make even the most discerning engineer swoon.
Mastering the Fundamentals: The Building Blocks of Flawless Welds
Before we dive into the nitty-gritty of quality control, let’s take a moment to revisit the foundational principles of welding. You see, my fellow welding enthusiasts, the path to flawless welds begins with a firm grasp of the basics. It’s like learning to play the piano – you can’t exactly start banging out Beethoven’s Ninth without first mastering those scales and arpeggios.
So, let’s get back to the basics, shall we? The key elements that dictate the quality of a weld are the base metal, the filler metal, the welding process, and the welding parameters. Each of these components must be carefully selected and precisely controlled to ensure the integrity and strength of the final weld.
Now, I know what you’re thinking – “Duh, Clive, tell me something I don’t know!” But bear with me, my friends, for even the most seasoned welders can sometimes overlook the little details that make all the difference. For example, did you know that the chemical composition and microstructure of the base metal can have a significant impact on weldability? Or that the filler metal must be carefully matched to the base metal to ensure proper fusion and minimize the risk of defects?
And let’s not forget about the welding process itself. Whether you’re wielding a trusty stick welder, a sleek MIG gun, or a high-tech TIG torch, the specific technique and settings you choose can make or break the final product. Ah, the delicate dance of amperage, voltage, and travel speed – the very heartbeat of a flawless weld.
But fear not, my friends, for I’m about to let you in on the secrets of mastering these fundamental elements. With a little elbow grease and a lot of practice, you’ll be cranking out welds that would make even the most seasoned fabricator green with envy.
Diving into Quality Control: The Keystone of Flawless Welds
Alright, now that we’ve got the basics covered, let’s get to the meat of the matter: quality control. This, my friends, is the holy grail of welding – the key to unlocking the door to those gloriously flawless welds that will have your clients begging for more.
Quality control, you see, is all about ensuring that every single aspect of the welding process is meticulously monitored and controlled. It’s like conducting a symphony – you’ve got to keep tabs on the tempo, the pitch, the dynamics, and the timing to create a masterpiece. And in the world of welding, the stakes are even higher, for a single misstep can lead to catastrophic consequences.
So, what does quality control entail, you ask? Well, let me break it down for you:
Visual Inspection: The First Line of Defense
The foundation of any quality control program starts with good old-fashioned eyeballs. That’s right, my friends – the humble visual inspection is the first and perhaps most crucial step in ensuring the quality of your welds. By carefully examining the weld bead, the heat-affected zone, and the surrounding base metal, you can quickly identify a host of potential defects, from porosity and undercut to incomplete fusion and cracking.
But don’t let the simplicity of this approach fool you – it takes a trained eye and a keen attention to detail to truly master the art of visual inspection. You’ve got to know what to look for, where to look, and how to interpret the subtle nuances of the weld. And let me tell you, it’s a skill that can take years to hone, but once you’ve got it, it’s like a superpower that can save you from a world of trouble.
Non-Destructive Testing: Seeing Beyond the Surface
Now, as impressive as visual inspection may be, sometimes you need to dig a little deeper to uncover the hidden secrets of a weld. That’s where non-destructive testing (NDT) comes into play – a suite of advanced techniques that allow you to peer beneath the surface without compromising the structural integrity of the final product.
Imagine, if you will, a welding inspector armed with an arsenal of high-tech gadgets, each one capable of revealing the inner workings of a weld with incredible precision. We’re talking everything from ultrasonic testing to penetrant inspection, each one tailored to detect a specific type of defect.
And let me tell you, the results can be downright astounding. I’ve seen welds that looked picture-perfect on the surface only to reveal a veritable treasure trove of hidden flaws when put under the NDT microscope. It’s like peeling back the layers of an onion, only instead of tears, you get a clear and comprehensive understanding of the weld’s true quality.
Destructive Testing: Pushing the Limits
But wait, there’s more! Sometimes, you just can’t get the full picture without getting a little, well, destructive. That’s where destructive testing comes into play – a series of rigorous evaluations that put the weld through its paces, testing its strength, ductility, and resistance to various stresses and strains.
Imagine a weld sample being subjected to crushing forces, bending stresses, or even cryogenic temperatures – all in the name of ensuring that it can withstand the demands of the real-world application. It’s like putting a superhero through their paces, testing the limits of their strength and resilience.
And let me tell you, the results of these destructive tests can be both fascinating and terrifying. You might uncover hidden weaknesses that you never even knew existed, or you might be blown away by the sheer power and durability of a particularly well-executed weld.
Continuous Improvement: The Never-Ending Quest for Perfection
But quality control doesn’t stop there, my friends. No, it’s an ongoing process, a never-ending quest for perfection that requires constant vigilance, diligence, and a willingness to adapt and evolve.
You see, the welding landscape is always shifting, with new technologies, new materials, and new challenges constantly emerging. And as a quality control professional, it’s your job to stay ahead of the curve, to anticipate these changes and develop strategies to address them.
It’s like being a master chef, constantly experimenting with new ingredients, techniques, and flavor profiles to create dishes that are truly transcendent. You’ve got to be willing to try new things, to push the boundaries of what’s possible, and to never settle for anything less than the absolute best.
And let me tell you, the rewards of this relentless pursuit of perfection are truly immeasurable. When you deliver a weld that is so flawless, so perfectly executed, that it leaves your clients in awe – well, there’s simply no feeling quite like it. It’s the kind of satisfaction that can only come from knowing that you’ve truly mastered your craft, that you’ve become a true artisan in the world of welding.
The Payoff: Delivering Flawless Welds Every Time
So, my fellow welding enthusiasts, are you ready to take your quality control game to the next level? Are you prepared to dive headfirst into the fascinating and ever-evolving world of weld perfection?
Well, buckle up, my friends, because the journey ahead is not for the faint of heart. It’s going to require dedication, discipline, and a relentless pursuit of excellence. But trust me, when you finally achieve that elusive state of welding nirvana – when you produce a weld that is so flawless, so breathtakingly beautiful, that it leaves your clients slack-jawed and awestruck – the payoff will be worth every single drop of sweat, every hour of meticulous planning and preparation.
And the best part? Once you’ve mastered the art of quality control, the possibilities are truly endless. You’ll be able to tackle the most complex and challenging welding projects with confidence, knowing that your work will stand the test of time and withstand even the harshest of conditions.
So, what are you waiting for? Let’s get to work, my friends! Let’s dive headfirst into the world of quality control and show the world what we’re made of. Because when it comes to welding, there’s no such thing as “good enough” – it’s all about striving for perfection, one flawless weld at a time.
And if you’re looking for a team of welding experts who can help you achieve that elusive state of weld nirvana, be sure to check out Corr Connect. With their cutting-edge quality control processes and unwavering commitment to excellence, they’re the perfect partners to help you take your welding game to the next level.