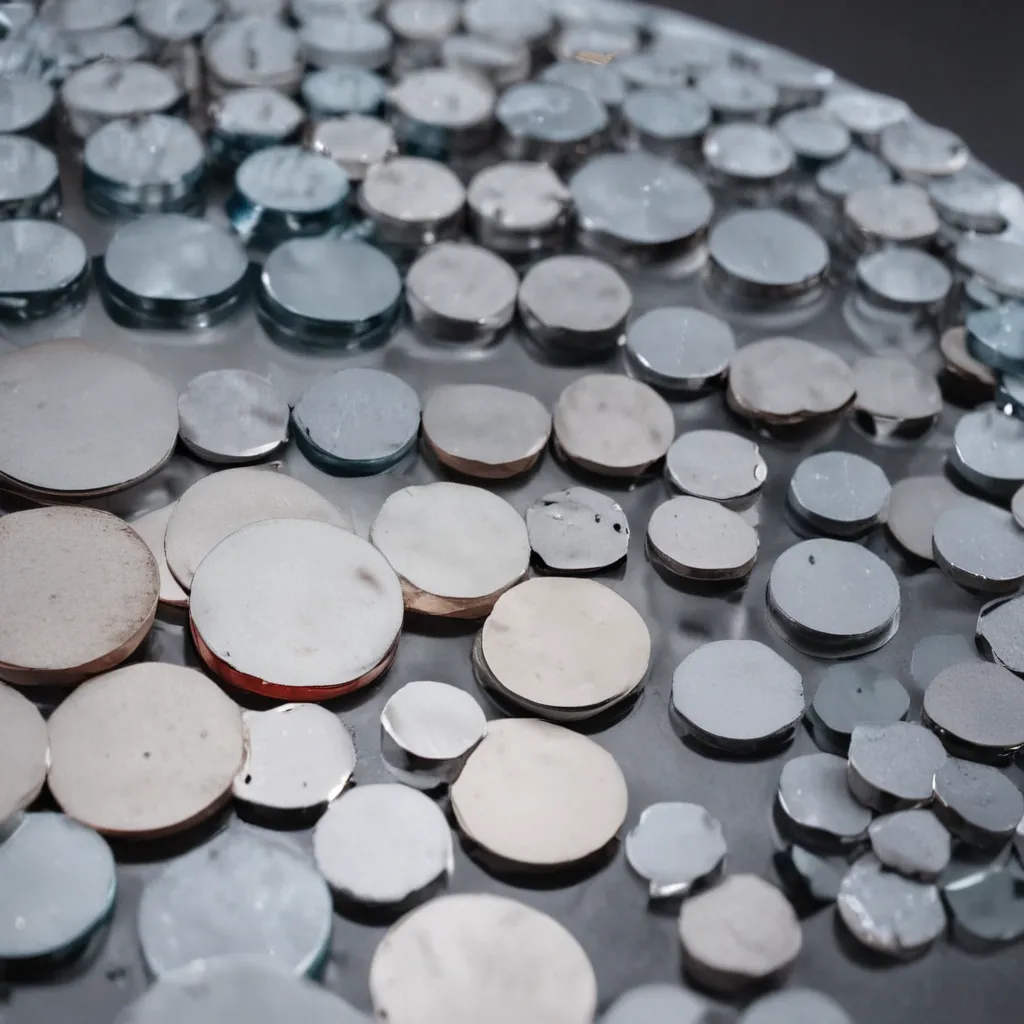
Unraveling the Mysteries of Electrode Coatings
As a welder, I’ve always been fascinated by the ins and outs of electrode coatings. These little buggers can make all the difference in the quality and performance of your welds, but navigating the sheer variety of options out there can be enough to make your head spin. Lucky for you, I’ve got a wealth of knowledge on the subject, and I’m more than happy to share it.
You see, I’ve been in this game for a while now, and I’ve seen it all – from the glorious triumphs of a perfectly executed weld to the disastrous failures that can result from using the wrong electrode coating. And let me tell you, it’s a wild ride. But don’t worry, I’m here to be your guide, your trusted advisor, your wingman in the high-stakes world of welding.
So, buckle up, because we’re about to dive deep into the pros and cons of different electrode coatings. We’ll explore the various types, their unique properties, and how they can impact your welding projects. By the time we’re done, you’ll be an electrode coating expert, ready to take on any welding challenge that comes your way.
The Basic Rundown: Understanding Electrode Coatings
Alright, let’s start with the basics. Electrode coatings are the thin layer of material that covers the metal core of a welding electrode. These coatings serve a variety of important functions, from stabilizing the arc to shielding the weld pool from atmospheric contamination.
The composition of the coating can vary widely, and each type brings its own set of advantages and disadvantages to the table. For instance, some coatings are designed to produce a smooth, uniform bead, while others are better suited for deep penetration or high-speed welding.
To give you a sense of the diversity out there, let’s take a quick look at some of the most common electrode coating types:
- Cellulosic: These coatings are known for their deep penetration and ability to weld through rust and mill scale. They’re great for structural welding, but can be a bit trickier to control.
- Iron Powder: Electrodes with iron powder coatings produce a smooth, consistent bead and are often used for general-purpose welding applications.
- Rutile: Rutile coatings are known for their excellent bead appearance and ease of use, making them a popular choice for beginners and experienced welders alike.
- Basic: Basic coatings are designed to produce welds with high strength and toughness, making them a go-to for critical applications like pressure vessels and pipelines.
Whew, that’s just the tip of the iceberg, my friend. But I think you get the idea – there’s a whole world of electrode coatings out there, each with its own unique characteristics and use cases.
Diving Deeper: Exploring the Pros and Cons of Electrode Coatings
Now that you’ve got a basic understanding of the different types of electrode coatings, let’s take a closer look at the pros and cons of each one. We’ll start with the positives and then dive into the potential drawbacks, so you can make an informed decision about which coating is best for your welding needs.
Cellulosic Coatings: Powerful Penetration with a Side of Complexity
Pros:
– Cellulosic electrodes are known for their incredible penetration depth, making them a great choice for welding thick materials or joining dissimilar metals.
– The coating helps to stabilize the arc, resulting in a smooth, consistent bead that can be particularly useful for out-of-position welding.
– Cellulosic coatings are also adept at cutting through rust, mill scale, and other surface contaminants, which can be a real time-saver on certain projects.
Cons:
– While the deep penetration is a major advantage, it can also be a double-edged sword. Cellulosic coatings tend to produce a more fluid, less viscous weld pool, which can make them more challenging to control, especially for beginners.
– The arc from cellulosic electrodes can be a bit more erratic and unstable compared to other coating types, which can make it harder to maintain a consistent weld.
– These electrodes also have a tendency to produce more spatter and fumes, which can be a pain to clean up and may require additional personal protective equipment (PPE) for the welder.
Iron Powder Coatings: Smooth Sailing for General-Purpose Welding
Pros:
– Iron powder coatings are known for their ability to produce a smooth, uniform bead with minimal spatter and fumes.
– They’re also relatively easy to use, making them a great choice for beginners or welders tackling general-purpose projects.
– The coating composition helps to stabilize the arc, which can lead to improved weld quality and reduced rework.
Cons:
– While iron powder coatings are versatile, they may not be the best choice for specialty applications or situations that require deep penetration or high-speed welding.
– The bead profile tends to be relatively flat, which can be a drawback for certain types of welding joints or aesthetic preferences.
– The coating can also be more sensitive to moisture than some other options, so proper storage and handling is essential to ensure optimal performance.
Rutile Coatings: The All-Rounder’s Choice
Pros:
– Rutile coatings are known for their excellent bead appearance, producing a smooth, even finish that can be particularly appealing for visible welds.
– They’re also relatively easy to use, with a stable arc and a forgiving weld pool that can be a boon for less experienced welders.
– Rutile electrodes are versatile and can be used for a wide range of welding applications, from thin sheet metal to thicker structural work.
Cons:
– While the bead appearance is a major plus, rutile coatings may not provide the same level of deep penetration as some other electrode types.
– The coating can also be more prone to porosity and slag inclusions, which can compromise weld quality if not properly addressed.
– Rutile electrodes may not be the best choice for certain high-strength or mission-critical applications where maximum weld integrity is essential.
Basic Coatings: Strength and Toughness for the Win
Pros:
– Basic coatings are designed to produce welds with exceptional strength and toughness, making them a popular choice for high-stress applications like pressure vessels, pipelines, and structural steel.
– The coating composition helps to minimize the formation of hydrogen-induced cracking, which can be a major concern in certain welding situations.
– Basic electrodes are also less sensitive to moisture and other environmental factors, allowing for more consistent performance across a range of conditions.
Cons:
– The downside to the increased strength and toughness of basic coatings is that they can be a bit more difficult to use, particularly for beginners.
– The weld bead profile tends to be less smooth and even compared to some other coating types, which may be a drawback for certain aesthetic or functional requirements.
– Basic electrodes can also be more prone to slag inclusions and other defects if the welding parameters are not carefully controlled.
Real-World Applications: Electrode Coatings in Action
Now that we’ve covered the pros and cons of the various electrode coating types, let’s take a look at how they play out in the real world. I’ve got a few case studies that I think will really help to illustrate the impact that these coatings can have on welding projects.
Case Study 1: Structural Steel Fabrication
For a recent project, we were tasked with fabricating a large, complex steel structure for a commercial building. The design called for a significant amount of welding, and the client was particularly concerned about the integrity and appearance of the finished welds.
After evaluating the project requirements, we decided to go with a basic-coated electrode. The increased strength and toughness of the weld would be crucial to the structural integrity of the building, and the basic coating’s resistance to hydrogen cracking would help to ensure a high-quality, defect-free result.
The welding process went smoothly, and the final product exceeded the client’s expectations. The welds were strong, durable, and had a clean, professional appearance that complemented the overall aesthetic of the structure. The client was thrilled with the outcome, and we were able to deliver the project on time and within budget.
Case Study 2: Shipyard Repairs
In another instance, we were called in to assist with some critical repair work on a commercial ship. The vessel had sustained significant damage to its hull, and the welding needed to be performed with the utmost precision and care.
Given the harsh marine environment and the need for exceptional weld quality, we opted to use a cellulosic-coated electrode for this job. The deep penetration and ability to cut through surface contaminants like rust and scale were essential for ensuring a strong, lasting repair.
The welding process was a bit more challenging than our typical work, as the cellulosic coating required a bit more finesse to control the weld pool. However, our experienced welding team was up to the task, and we were able to complete the repairs to the client’s satisfaction.
The final welds were not only structurally sound, but they also had a clean, uniform appearance that met the stringent standards of the shipyard. The client was relieved to have the repairs completed quickly and efficiently, and they were grateful for our expertise in selecting the right electrode coating for the job.
Case Study 3: Automotive Manufacturing
In the fast-paced world of automotive manufacturing, precision and efficiency are key. That’s why, when one of our clients in the automotive industry needed to ramp up their welding production, they turned to us for a solution.
After analyzing the specific requirements of the project, we recommended the use of iron powder-coated electrodes. These coatings are known for their ability to produce smooth, uniform beads with minimal spatter and fumes – perfect for the high-volume, high-speed welding needs of the automotive industry.
The implementation was a resounding success. The iron powder coatings allowed our welding team to maintain a consistent, efficient pace throughout the production run, with little downtime for cleanup or rework. The final welds were of exceptional quality, and the client was thrilled with the improved throughput and cost savings.
Wrapping it Up: Choosing the Right Electrode Coating for Your Needs
Well, there you have it, folks – a deep dive into the pros and cons of different electrode coatings. I hope that by now, you have a better understanding of the various options available and how they can impact the quality and performance of your welding projects.
Remember, when it comes to selecting the right electrode coating, there’s no one-size-fits-all solution. It all comes down to carefully evaluating the specific requirements of your project, the materials you’ll be working with, and the desired outcome. Do you need maximum penetration? Smooth bead appearance? High strength and toughness? The choice of electrode coating can make all the difference.
And if you’re still feeling a bit overwhelmed or unsure about which way to go, don’t worry – that’s what we’re here for. At [Company Name], we’ve got a team of welding experts who are more than happy to help you navigate the complexities of electrode coatings and find the perfect solution for your needs.
So, what are you waiting for? Let’s get welding! Head on over to https://www.corrconnect.org/ to learn more about our top-notch welding services, and let’s work together to tackle your next big project. Trust me, with the right electrode coating in your corner, the possibilities are endless.