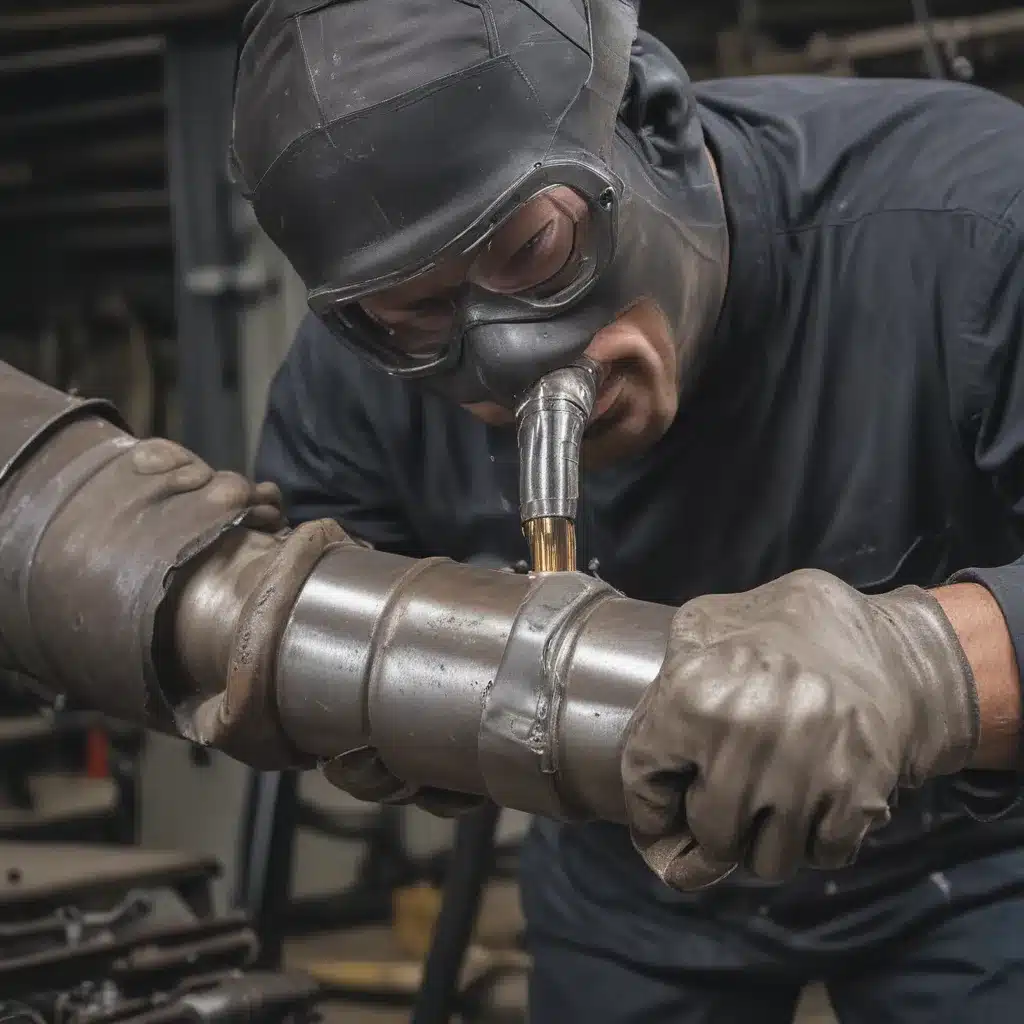
The Art of Exhaust Welding: A Hands-On Approach
As a seasoned welder, I’ve had the privilege of working on all sorts of projects, from intricate architectural pieces to heavy-duty industrial equipment. But one area that’s always held a special place in my heart is automotive exhaust welding. There’s just something about the precision, the attention to detail, and the sheer satisfaction of creating a high-performing, long-lasting exhaust system that truly speaks to me.
You see, exhaust pipes and headers are the unsung heroes of the automotive world. They’re the vital components that channel the hot, noxious gases away from the engine, keeping your ride running smoothly and efficiently. And when it comes to welding these parts, it’s not just about striking a few seams – it’s about mastering a delicate dance of heat, filler metal, and unwavering focus.
In this in-depth article, I’ll share with you the proper techniques for welding automotive exhaust pipes and headers. From the importance of pre-welding preparation to the nuances of different welding processes, we’ll dive deep into the world of exhaust welding and uncover the secrets to achieving professional-grade results. So buckle up, grab your welding gear, and let’s get started on this exciting journey!
The Fundamentals of Exhaust Welding
Before we can dive into the specifics of welding exhaust pipes and headers, it’s crucial to understand the fundamental principles that govern this specialized craft. After all, exhaust components are subjected to intense heat, vibration, and corrosive environments, so the welds must be strong, durable, and able to withstand these demanding conditions.
One of the primary considerations in exhaust welding is the type of metal being joined. Exhaust systems are typically fabricated from stainless steel, aluminized steel, or even titanium, each with its own unique properties and welding requirements. Stainless steel, for instance, is known for its corrosion resistance, but it can be prone to warping and cracking if not welded with the proper techniques. Aluminized steel, on the other hand, requires specialized filler metals and shielding gases to prevent oxidation and achieve a high-quality weld.
Another crucial factor is the thickness of the exhaust components. Thinner metal, such as that found in mufflers and catalytic converters, requires a gentler touch and a more controlled heat input to avoid burn-through or distortion. Thicker materials, like those used in headers and downpipes, can handle a higher heat input but may require multiple passes to ensure complete penetration and a strong, uniform weld.
Understanding these fundamental principles is the foundation for mastering the art of exhaust welding. By keeping these key considerations in mind, you’ll be well on your way to producing exceptional results that will stand the test of time.
Preparing for Exhaust Welding Success
Before you can even think about striking that first arc, proper preparation is the name of the game when it comes to welding automotive exhaust components. This meticulous pre-welding process is the difference between a professional-grade finish and a subpar, potentially dangerous result.
One of the most important steps is ensuring the surfaces to be welded are thoroughly cleaned and free of any contaminants. Exhaust pipes and headers can accumulate a variety of unwanted materials, from dirt and grease to rust and scale. These impurities can severely compromise the integrity of the weld, leading to porosity, cracking, or even complete failure. That’s why it’s crucial to meticulously clean the surfaces using a combination of solvents, abrasives, and, if necessary, a wire brush.
Another critical aspect of preparation is properly aligning the exhaust components. Proper fitment is essential for achieving a seamless, uniform weld. This may involve the use of specialized jigs, clamps, or even tack welds to hold the parts in place. Paying close attention to the fit-up and ensuring a tight, consistent gap between the surfaces will go a long way in producing a high-quality, professional-looking result.
Lastly, it’s important to consider the welding position and access to the work area. Exhaust components can be notoriously difficult to reach, with tight spaces and awkward angles that can challenge even the most experienced welder. Carefully planning the welding sequence and having the right tools and equipment on hand, such as a flexible welding torch or a magnetic welding ground, can make all the difference in your ability to execute the perfect weld.
By diligently addressing these preparatory steps, you’ll set the stage for success and ensure that your exhaust welding projects are not only structurally sound but also visually appealing.
Mastering the Welding Process for Exhaust Components
Now that we’ve covered the fundamental principles and the importance of proper preparation, it’s time to dive into the nitty-gritty of the welding process itself. When it comes to welding automotive exhaust pipes and headers, there are a few key techniques and considerations that will help you achieve professional-grade results.
One of the most commonly used welding processes for exhaust work is gas metal arc welding (GMAW), also known as MIG welding. This versatile method allows for a high deposition rate and excellent control over the weld bead, making it ideal for joining thinner exhaust components. When MIG welding exhaust pipes and headers, it’s crucial to use the right filler metal – typically a stainless steel or nickel-based alloy that can withstand the high temperatures and corrosive environment.
Another popular option is tungsten inert gas (TIG) welding, also known as GTAW. This process is often preferred for its precision and clean, aesthetic welds, especially on thicker exhaust components like headers and downpipes. TIG welding requires a bit more skill and dexterity, as the welder must manually feed the filler metal while maintaining a steady arc. But the results are typically worth the extra effort, with a smooth, uniform weld that blends seamlessly with the base material.
Regardless of the welding process you choose, the key to success is maintaining the proper welding parameters. This includes carefully controlling the heat input, travel speed, and shielding gas flow to prevent distortion, cracking, or other defects. It’s also crucial to pay close attention to the weld pool and make adjustments as needed to ensure a consistent, high-quality weld.
One often-overlooked aspect of exhaust welding is the importance of post-weld treatment. Depending on the material and the application, the weld may require stress relieving, passivation, or other specialized techniques to enhance its durability and corrosion resistance. Neglecting this critical step can lead to premature failure and costly repairs down the road.
By mastering the nuances of the welding process and incorporating these essential post-weld treatments, you’ll be well on your way to producing exhaust welds that are not only strong and reliable but also visually appealing and long-lasting.
Troubleshooting Common Exhaust Welding Issues
As with any specialized welding task, there’s always the potential for things to go awry. Exhaust welding is no exception, and it’s important to be prepared to tackle any challenges that may arise. By understanding the common issues and knowing how to address them, you can ensure that your exhaust welding projects are a resounding success.
One of the most frequent problems encountered in exhaust welding is cracking. This can be caused by a variety of factors, including thermal stress, material incompatibility, or improper joint preparation. To combat cracking, it’s essential to carefully control the heat input, use the appropriate filler metal, and ensure that the base material is properly prepared and free of contaminants.
Another common issue is porosity, which can occur when gases become trapped in the weld pool. This not only compromises the structural integrity of the weld but can also lead to leaks and premature failure. Addressing porosity often involves adjusting the shielding gas flow, optimizing the welding parameters, and thoroughly cleaning the surfaces before welding.
Warping and distortion are also common challenges in exhaust welding, particularly when dealing with thinner materials. To mitigate these issues, it’s crucial to use the right welding techniques, such as employing a lower heat input, using a narrower weld bead, and potentially incorporating strategies like back-stepping or weaving.
Finally, one of the most frustrating problems in exhaust welding can be the dreaded “burn-through,” where the intense heat of the welding process melts completely through the base material. This can be especially problematic in areas with limited access or thin-walled components. To prevent burn-through, it’s essential to closely monitor the heat input, use a slower travel speed, and potentially employ specialized welding techniques like pulse welding or cold metal transfer.
By familiarizing yourself with these common exhaust welding issues and mastering the techniques to address them, you’ll be well on your way to producing flawless, professional-grade welds every time.
Exploring Advanced Exhaust Welding Techniques
As you become more experienced in the art of exhaust welding, you may find yourself seeking out new and innovative techniques to take your skills to the next level. From specialized welding processes to advanced heat treatment methods, there’s always something new to explore in this ever-evolving field.
One cutting-edge technique that has gained traction in the exhaust welding world is laser welding. This highly precise and controlled process uses a focused laser beam to melt the base material and filler metal, resulting in a narrow, deep weld with minimal distortion and a smooth, uniform appearance. Laser welding is particularly well-suited for delicate exhaust components, such as catalytic converters and mufflers, where traditional welding methods may be too bulky or intrusive.
Another advanced technique that can be leveraged in exhaust welding is plasma arc welding (PAW). This process uses a constricted arc to produce a high-energy, concentrated plasma beam that can penetrate deeply into the base material. PAW is often favored for its ability to weld thicker exhaust components, such as headers and downpipes, with a single pass and minimal heat input, reducing the risk of distortion and cracking.
But it’s not just the welding process itself that can be advanced – the materials used in exhaust fabrication are also evolving. One notable example is the increasing use of exotic alloys, like titanium and Inconel, in high-performance exhaust systems. These materials offer exceptional heat and corrosion resistance, but they also require specialized welding techniques and filler metals to achieve reliable, long-lasting results.
Finally, one area of exhaust welding that has seen significant advancement in recent years is the use of post-weld heat treatment. Techniques like stress relieving and solution annealing can help improve the mechanical properties of the weld, enhancing its resistance to cracking and fatigue. By carefully controlling the heat input and cooling rates, welders can optimize the microstructure of the weld and ensure that it can withstand the demanding conditions of the exhaust system.
As you continue to hone your exhaust welding skills, don’t be afraid to explore these advanced techniques and materials. By staying up-to-date with the latest industry developments and constantly challenging yourself, you’ll be able to take your craft to new heights and deliver exceptional results for your clients.
Real-World Exhaust Welding Case Studies
While understanding the theory and principles behind proper exhaust welding techniques is essential, there’s nothing quite like learning from real-world examples and case studies. Let’s dive into a few real-life scenarios that illustrate the challenges and triumphs of this specialized craft.
Case Study 1: Restoring a Classic Muscle Car Exhaust
One of my most memorable projects was working on the exhaust system of a 1969 Dodge Charger. The owner, a dedicated car enthusiast, had painstakingly restored the entire vehicle, but the original exhaust was beyond repair. It was my task to recreate the iconic look and sound of the Charger’s exhaust, while ensuring that it could withstand the rigors of high-performance driving.
The key challenge here was the need to balance aesthetics and function. The exhaust had to not only look the part, with its distinctive headers and dual rear exit, but it also had to be capable of handling the increased airflow and temperatures generated by the car’s powerful V8 engine. This meant carefully selecting the right materials, such as high-grade stainless steel, and employing specialized welding techniques to achieve a seamless, durable finish.
Through meticulous planning, attention to detail, and a deep understanding of exhaust system design, we were able to create an exhaust that not only met the owner’s high standards but also delivered the perfect balance of power, sound, and visual appeal. It was a true testament to the art of exhaust welding and the satisfaction that comes from restoring a beloved classic to its former glory.
Case Study 2: Fabricating a Custom Exhaust for a Racing Application
Another project that stands out in my mind is the custom exhaust system I created for a local race team. These high-performance vehicles demand the utmost precision and attention to detail, as even the slightest imperfection can have a significant impact on engine efficiency and power output.
The primary challenge in this case was the sheer complexity of the exhaust design, with multiple bends, transitions, and intricate components that all had to be expertly fabricated and joined. Achieving the perfect fitment and alignment was crucial, as any misalignment could lead to turbulence, backpressure, and a loss of power.
To tackle this project, I had to draw upon my extensive knowledge of exhaust system dynamics, as well as my mastery of advanced welding techniques. This included leveraging specialized tools and jigs to ensure precise component placement, as well as employing advanced welding methods like pulsed-arc GTAW to minimize distortion and achieve a flawless finish.
The end result was a custom exhaust system that not only looked stunning but also delivered a measurable performance boost to the race team’s vehicle. It was a true testament to the power of skilled exhaust welding and the difference it can make in the world of high-performance motorsports.
These real-world case studies illustrate the diverse challenges and incredible satisfaction that can come from mastering the art of exhaust welding. Whether it’s restoring a classic or fabricating a custom high-performance system, the principles and techniques we’ve explored throughout this article can make all the difference in achieving exceptional results.
Conclusion: Elevating Your Exhaust Welding Prowess
As we reach the end of this in-depth exploration of proper techniques for welding automotive exhaust pipes and headers, I hope you’ve gained a newfound appreciation for the art and science of this specialized craft. From the fundamental principles to the advanced techniques, we’ve covered a wealth of knowledge that can help you elevate your exhaust welding prowess to new heights.
Remember, the key to success in exhaust welding lies in a combination of technical expertise, attention to detail, and a true passion for the work. By meticulously preparing the surfaces, mastering the nuances of the welding process, and troubleshooting any issues that arise, you’ll be well on your way to producing exceptional, long-lasting results that will leave your clients (and their vehicles) thoroughly impressed.
And as you continue to hone your skills, don’t be afraid to explore the cutting-edge of exhaust welding technology. From advanced welding processes to innovative materials, there’s always something new to discover and incorporate into your repertoire. By embracing these advancements and challenging yourself to push the boundaries of what’s possible, you’ll not only solidify your reputation as a master of exhaust welding but also contribute to the ongoing evolution of this crucial automotive discipline.
So, my fellow welding enthusiasts, let’s raise a virtual glass to the art of exhaust welding. It’s a specialized craft that requires patience, precision, and a deep understanding of the underlying principles. But with the knowledge and techniques we’ve explored today, I have no doubt that you’re well on your way to becoming the exhaust welding maestro your clients have been searching for.
Now, if you’ll excuse me, I’ve got some pipes to weld. Time to put these skills into practice and create something truly remarkable. Cheers, and happy welding!