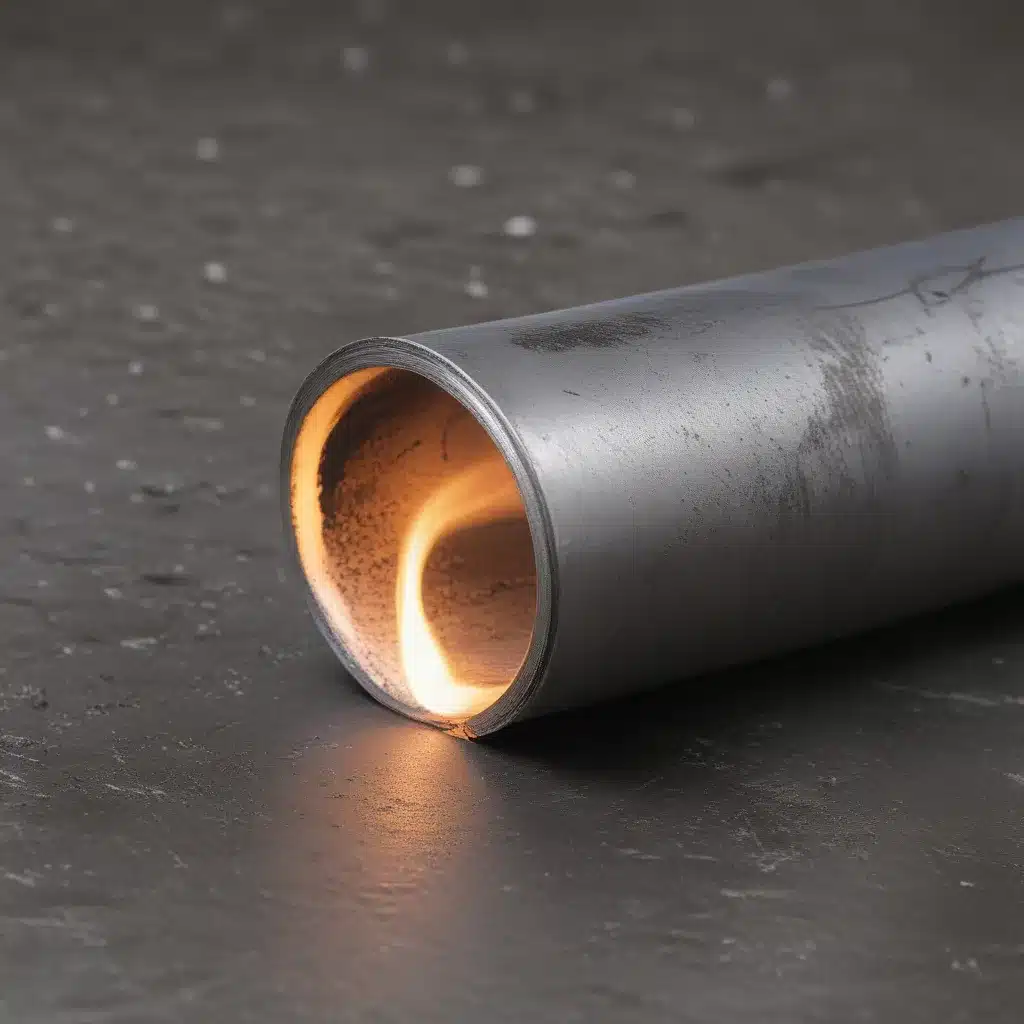
Uncovering the Mysteries of Moly
As a seasoned welding professional, I’ve seen my fair share of challenges when it comes to working with Chrome-Moly (Cr-Mo) steels. These high-strength alloys are incredibly useful, but they can also be a real headache if you don’t know what you’re doing. And let me tell you, the issue of reheat cracking is one of the trickiest problems you’ll encounter.
Now, I know what you’re thinking – “Reheat cracking? What the heck is that?” Well, my friend, let me enlighten you. Reheat cracking is a nasty little phenomenon that can rear its ugly head when you’re welding on Cr-Mo steels, especially in thick sections. It’s caused by a complex interplay of metallurgical factors, and if you don’t take the right precautions, it can turn your beautiful weld into a cracked, unsightly mess.
But fear not, my welding warriors! I’m here to share my hard-earned knowledge and guide you through the minefield of Cr-Mo welding. We’re going to dive deep into the science behind reheat cracking, explore the factors that contribute to it, and most importantly, learn how to prevent it from happening in the first place.
The Science of Reheat Cracking
Let’s start by understanding the underlying metallurgical processes at play. When you’re welding Cr-Mo steels, you’re introducing a significant amount of heat into the material. This heat can cause some serious microstructural changes, and it’s these changes that can lead to the dreaded reheat cracking.
The problem lies in the formation of a brittle, hard phase called martensite. You see, Cr-Mo steels are alloyed with chromium and molybdenum to improve their strength and wear resistance. However, these alloying elements also make the steel more susceptible to transformation into martensite during the welding process.
And here’s the kicker – martensite is incredibly hard and brittle. When it forms in the weld or heat-affected zone, it can become a weak point in the metal, prone to cracking under stress. This is where reheat cracking comes into play – the repeated heating and cooling cycles during welding can cause the martensite to crack, leading to a compromised weld.
But wait, there’s more! The composition of the Cr-Mo steel also plays a crucial role. The higher the carbon content, the more prone the steel is to forming martensite and, consequently, reheat cracking. And let’s not forget the influence of other alloying elements, like nickel and vanadium, which can also contribute to the problem.
Factors Affecting Reheat Cracking
Now that we’ve got the science down, let’s dive into the factors that can influence the likelihood of reheat cracking in Cr-Mo steel welds. Understanding these factors is key to developing effective strategies for prevention.
Welding Heat Input
One of the primary contributors to reheat cracking is the amount of heat input during the welding process. Higher heat input can lead to the formation of more martensite, increasing the risk of cracking. This means that welding parameters like amperage, voltage, and travel speed need to be carefully controlled to optimize the heat input.
Pre-Heat and Inter-Pass Temperature
Another crucial factor is the pre-heat and inter-pass temperature – the temperature of the workpiece before and during welding. Maintaining the proper pre-heat and inter-pass temperature can help mitigate the formation of martensite and reduce the risk of reheat cracking. Too low, and you might not be able to prevent the transformation; too high, and you could end up with other issues like excessive grain growth.
Weld Bead Sequence and Geometry
The way you lay down your weld beads can also play a role in reheat cracking. Optimizing the weld bead sequence and geometry can help distribute the stresses more evenly, reducing the likelihood of crack formation. This might involve techniques like staggering weld passes or using a specific bead placement pattern.
Post-Weld Heat Treatment
Last but not least, post-weld heat treatment can be a game-changer when it comes to preventing reheat cracking. By carefully controlling the tempering or stress-relieving process, you can effectively soften the martensite and relieve the residual stresses in the weld. This can make a huge difference in the overall integrity and durability of the joint.
Putting it all Together
Now that we’ve covered the key factors involved in reheat cracking, let’s talk about how you can put this knowledge into practice. As a welding professional, you need to be proactive and adopt a comprehensive approach to preventing this pesky issue.
Start by thoroughly understanding the composition and metallurgical properties of the Cr-Mo steel you’re working with. This will help you anticipate the potential for martensite formation and tailor your welding procedures accordingly.
Next, pay close attention to your welding parameters and techniques. Experiment with different heat inputs, pre-heat and inter-pass temperatures, and weld bead sequences to find the optimal combination that minimizes the risk of reheat cracking.
And don’t forget the power of post-weld heat treatment! Implement a carefully designed tempering or stress-relieving regimen to ensure that your Cr-Mo welds are as strong and crack-resistant as possible.
But wait, there’s more! If you really want to take your Cr-Mo welding game to the next level, consider seeking out the expertise of specialized welding service providers like Corrconnect. These seasoned professionals have the knowledge and equipment to tackle even the trickiest Cr-Mo welding challenges, ensuring that your projects are completed to the highest standards of quality and durability.
So there you have it, my fellow welding enthusiasts – the secrets to preventing reheat cracking in Cr-Mo steel welds. It’s a complex issue, to be sure, but with the right knowledge and the proper techniques, you can conquer this challenge and create truly exceptional welds that will stand the test of time.
Now, if you’ll excuse me, I think it’s time to fire up the ol’ welding machine and put these principles into practice. Cracks knuckles Let’s do this!