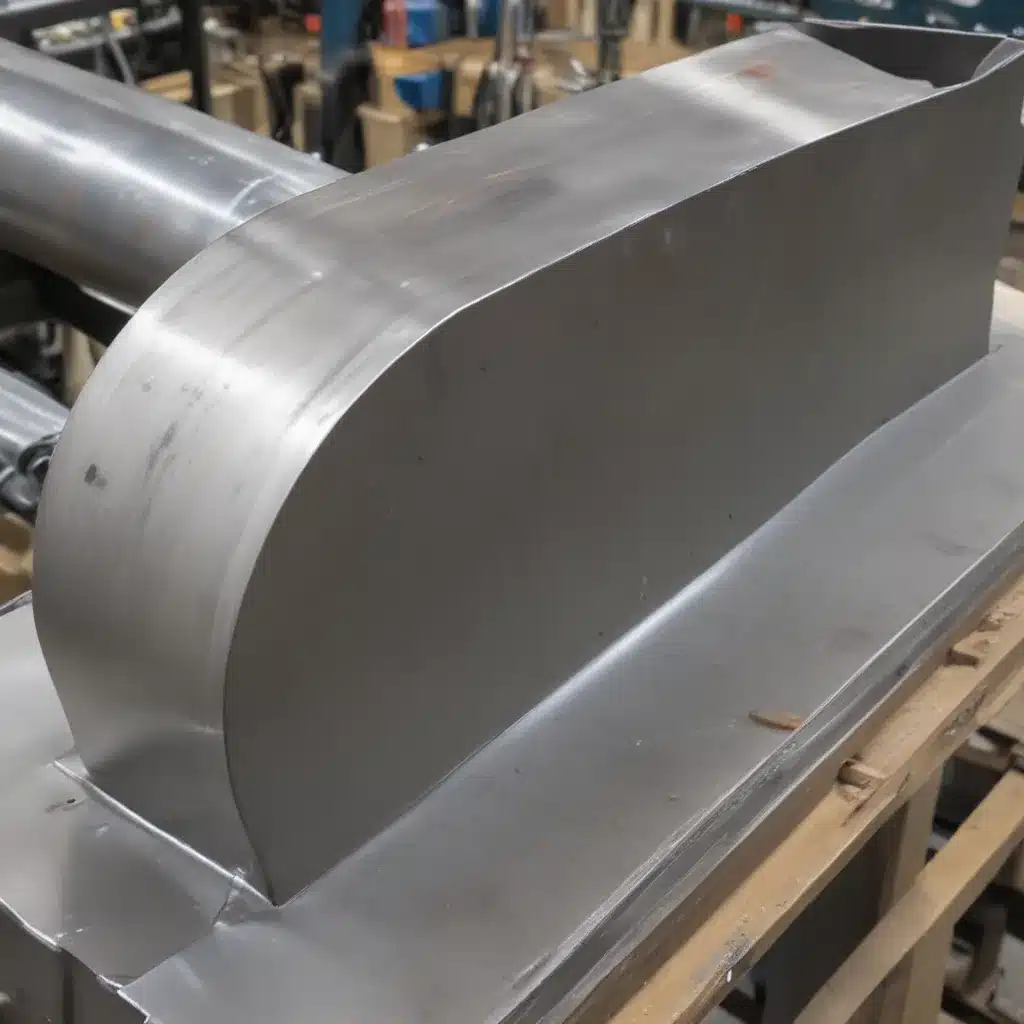
The Telltale Signs of Welding Distortion
As a seasoned welder, I’ve seen my fair share of distortion issues in welded assemblies. It’s a frustrating problem that can arise even for the most experienced professionals. But you know what they say – forewarned is forearmed! That’s why I’m here to share my insights on the telltale signs of welding distortion and how to prevent it from wreaking havoc on your projects.
Let me start by painting you a picture. Imagine you’ve just completed a complex welding job, all proud of your handiwork. But when you step back and admire your creation, your heart sinks. The once-pristine metal components have become warped, twisted, and out of alignment. That, my friends, is the telltale sign of welding distortion.
But what causes this mischievous phenomenon, you ask? Well, the culprit is the intense heat generated during the welding process. As the metal heats up, it expands, and when it cools down, it contracts. This uneven heating and cooling is what leads to those pesky distortions. And trust me, they can be a real headache to deal with, especially when you’ve invested time, effort, and hard-earned cash into a project.
Identifying the Different Types of Welding Distortion
Now, distortion isn’t a one-size-fits-all problem. Oh no, it comes in a variety of shapes and sizes, each with its own unique characteristics. Let’s dive in and explore the different types of welding distortion you might encounter:
Longitudinal Distortion
This is when the weld bead causes the metal to bend or curve along the length of the joint. Imagine a once-straight piece of metal now resembling a gentle arc – that’s longitudinal distortion for you.
Transverse Distortion
This one’s all about the metal moving perpendicular to the weld line. Picture a perfectly flat surface now sporting a series of humps and bumps – that’s transverse distortion in action.
Angular Distortion
Ah, the dreaded angular distortion. This occurs when the weld causes the two pieces of metal to twist or rotate in relation to each other. Imagine a perfect right angle now looking more like a triangle – that’s the telltale sign of angular distortion.
Bowing Distortion
This one’s a real head-scratcher. Bowing distortion happens when the weld causes the metal to curve or bow out of its original flat plane. Imagine a once-flat surface now resembling a gentle wave – that’s bowing distortion for you.
Phew, that’s quite the distortion dictionary, isn’t it? But fear not, my fellow welding enthusiasts, for I have some tried and true strategies to help you prevent these pesky issues from ruining your hard work.
Strategies for Preventing Welding Distortion
Proper Joint Design
When it comes to welding, the devil really is in the details. And one of the most crucial details? The joint design. You see, the way the metal components are positioned and fit together can have a significant impact on the distortion that occurs during the welding process.
Think of it like building a house – the foundation is crucial to ensuring the structure remains sturdy and straight. Well, the same principle applies to welding. By carefully designing the joint, you can create a solid “foundation” that helps minimize the risk of distortion.
Careful Weld Sequencing
Ah, the art of weld sequencing – it’s like a delicate dance, where each step must be choreographed with precision. You see, the order in which you lay down those weld beads can make all the difference in the world when it comes to preventing distortion.
Imagine you’re building a house, and you start by welding the roof in place before the walls are up. Chaos, right? Well, the same principle applies to welded assemblies. By strategically planning the weld sequence, you can ensure that the metal components are gradually and evenly heated and cooled, reducing the risk of those pesky distortions.
Proper Heat Input Management
Now, I know what you’re thinking – “But won’t more heat mean more distortion?” Well, my friends, it’s all about finding that sweet spot. You see, the key is to strike a balance between the amount of heat input and the resulting distortion.
Think of it like baking a cake – too much heat and you end up with a charred, inedible mess. But just the right amount of heat? Pure perfection. The same principle applies to welding. By carefully controlling the heat input, you can minimize the risk of distortion while still achieving a strong, high-quality weld.
Optimizing Clamping and Fixturing
Ah, the unsung heroes of the welding world – the humble clamps and fixtures. These little workhorses might not be the flashiest part of the job, but they play a crucial role in preventing distortion.
You see, by strategically positioning and securing the metal components during the welding process, you can effectively “hold them in place” and prevent those pesky distortions from occurring. It’s like having a team of invisible assistants keeping your work perfectly aligned.
Post-Weld Heat Treatment
Sometimes, even with all the careful planning and execution, distortion can still rear its ugly head. But fear not, my fellow welding enthusiasts, for there’s a secret weapon in our arsenal: post-weld heat treatment.
By subjecting the welded assembly to a carefully controlled heating and cooling process, we can actually “undo” the distortion and restore the metal to its original shape and alignment. It’s like a magical reset button for your welding projects.
Real-World Examples of Preventing Welding Distortion
Now, I know all this talk of distortion and prevention strategies might sound a bit dry and technical. But let me tell you, in the real world, it’s anything but boring. In fact, I’ve had the privilege of working on some truly fascinating projects where we had to put these strategies to the test.
Take, for example, the time we were tasked with fabricating a massive steel frame for a new high-rise building. Now, you can imagine the sheer scale and complexity of this project – hundreds of individual steel beams, all meticulously welded together to create a sturdy, load-bearing structure.
But here’s the kicker – the design called for razor-sharp precision, with each beam perfectly aligned and the entire frame completely level. Any distortion, even the slightest bit, would have thrown the whole thing off.
So, what did we do? Well, we pulled out all the stops. We carefully engineered the joint designs, planned the weld sequencing like a military operation, and managed the heat input with the precision of a surgeon. And you know what? It worked like a charm. The final frame was a masterpiece of engineering, with not a single trace of distortion to be found.
Or how about the time we were tasked with fabricating a set of custom-made steel exhaust manifolds for a high-performance sports car? Now, these babies were no joke – thin, intricate pieces of metal that had to withstand intense heat and pressure, all while maintaining their sleek, aerodynamic profile.
Again, we pulled out all the stops. We carefully optimized the clamping and fixturing, ensuring that each component was held in place with laser-like precision. And when it came time to lay down those weld beads, we used a combination of pulsed arc welding and strategic cooling techniques to keep the distortion at bay.
The result? A set of exhaust manifolds that not only looked like works of art but also performed like a dream. The client was over the moon, and we were as proud as punch to have pulled off such a challenging feat.
Conclusion: Mastering Welding Distortion for Flawless Assemblies
Well, there you have it, my fellow welding enthusiasts – the ins and outs of preventing distortion in welded assemblies. It’s a complex and multifaceted challenge, but with the right strategies and a healthy dose of know-how, it’s definitely a challenge that can be conquered.
Remember, the key is to think of welding as a delicate dance, where every step must be carefully choreographed and executed. From joint design to weld sequencing, heat input management to clamping and fixturing, it’s all about finding that perfect balance to keep those pesky distortions at bay.
And let’s not forget the power of post-weld heat treatment – that secret weapon in our arsenal that can undo even the most stubborn of distortion issues. It’s like a magical reset button for your welding projects, ensuring that every assembly is as straight and true as the day it was fabricated.
So, the next time you’re tackling a welding project, keep these strategies in mind. And who knows, you might just end up creating a masterpiece that would make even the most seasoned welder green with envy. Happy welding, my friends!
And remember, if you’re ever in need of top-notch welding services, be sure to check out https://www.corrconnect.org/. Their team of skilled professionals are experts at preventing distortion and delivering flawless, precision-engineered welded assemblies. Give them a try – your projects will thank you!