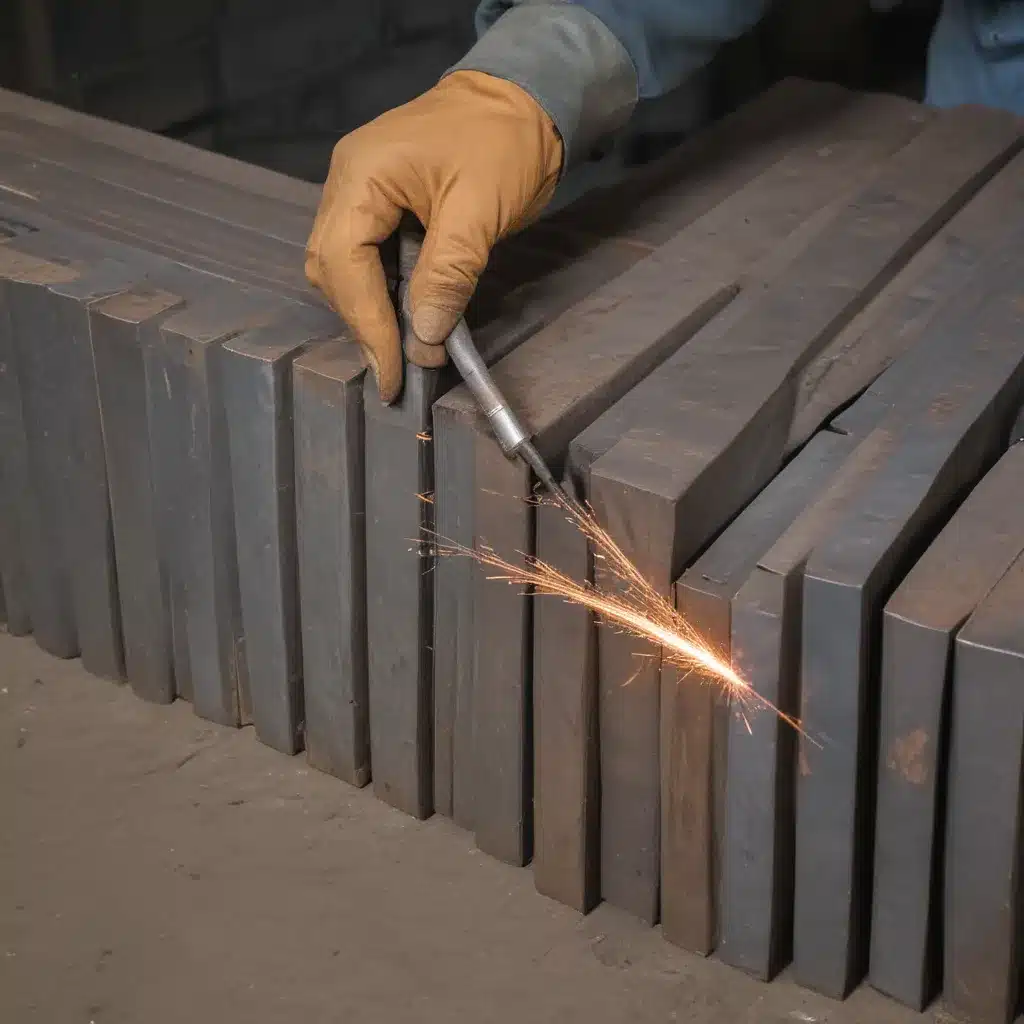
The Importance of Choosing the Right Welding Rod
As a seasoned welder with years of experience under my belt, I can tell you that the selection of the right welding rod is crucial to the success of any welding project. It’s like choosing the perfect tool for the job – get it right, and you’ll be well on your way to creating a masterpiece. Get it wrong, and you might as well be trying to hammer in a nail with a wrench (trust me, I’ve been there, and it ain’t pretty).
You see, the welding rod is the backbone of the welding process. It’s the conduit through which the molten metal flows, the bridge that connects two pieces of metal together. And just like a good bridge, it needs to be sturdy, reliable, and built to withstand the test of time. But with so many different types of welding rods out there, how do you know which one is right for your project?
Understanding the Basics of Welding Rods
Let’s start with the basics, shall we? A welding rod is essentially a consumable electrode used in the welding process. It’s made up of a core wire, which is surrounded by a flux coating. The core wire is what actually melts and fuses the two pieces of metal together, while the flux coating serves a variety of purposes, from shielding the weld from atmospheric contaminants to stabilizing the arc and adding strength to the finished weld.
Now, the type of welding rod you choose will depend on a variety of factors, such as the thickness and composition of the metals you’re working with, the welding process you’re using (e.g., SMAW, GMAW, GTAW), and the desired appearance and properties of the finished weld.
Selecting the Right Welding Rod for the Job
Mild Steel Welding
If you’re working with mild steel, you’ll want to choose a low-hydrogen welding rod, such as an E6010 or E7018. These rods are designed to produce a strong, ductile weld with minimal cracking or porosity. The E6010 is a great all-around choice for general-purpose welding, while the E7018 is better suited for high-strength applications.
Stainless Steel Welding
When it comes to stainless steel, you’ll need to use a specialized stainless steel welding rod, such as an ER308L or ER316L. These rods are designed to match the chemical composition of the stainless steel you’re working with, ensuring a strong, corrosion-resistant weld. The ER308L is a good choice for general-purpose stainless steel welding, while the ER316L is better suited for more demanding applications, like marine environments.
Aluminum Welding
Welding aluminum is a whole different ball game, and you’ll need to use an aluminum-specific welding rod, such as an ER4043 or ER5356. These rods are designed to melt at a lower temperature than the aluminum you’re working with, allowing for a smoother, more uniform weld. The ER4043 is great for general-purpose aluminum welding, while the ER5356 is better suited for high-strength applications.
Specialty Welding Rods
But what about those more specialized welding projects, you ask? Well, fear not, my friends, because there’s a welding rod for that too. Whether you’re working with exotic metals like titanium or trying to tackle a tricky welding application, there’s a specialized welding rod out there that’s up for the challenge.
For example, if you’re working with cast iron, you might want to use a nickel-based welding rod, like an ENi-CI. This rod is designed to produce a strong, ductile weld that’s resistant to cracking and porosity. And if you’re working with high-strength alloys, you might want to look into a flux-cored arc welding (FCAW) rod, which can produce a stronger, more penetrating weld than traditional stick welding.
Mastering the Art of Welding Rod Selection
Okay, so now you know the basics of welding rods and the different types available. But how do you actually choose the right one for your project? Well, my friends, it’s all about doing your homework and understanding the specific requirements of your welding application.
Start by consulting the manufacturer’s recommendations for the metals you’re working with. They’ll typically provide guidance on the best welding rods to use, as well as any special considerations or techniques you might need to keep in mind.
Next, think about the desired appearance and properties of the finished weld. Are you going for a strong, ductile weld? A highly corrosion-resistant one? Or maybe you’re looking for a weld that’s easy to grind and finish? Knowing what you want the end result to look like will help you narrow down your welding rod options.
And don’t forget to factor in the welding process you’ll be using. Different welding processes, like SMAW, GMAW, and GTAW, have their own unique requirements when it comes to welding rods. Make sure you choose a rod that’s specifically designed for the welding process you’ll be using.
The Importance of Proper Welding Rod Storage and Handling
But the story doesn’t end there, my friends. Once you’ve selected the perfect welding rod, you’ve got to make sure you’re taking care of it properly. After all, a high-quality welding rod is only as good as the way it’s stored and handled.
Proper welding rod storage is crucial to ensuring the integrity of the flux coating and core wire. You’ll want to keep your rods in a dry, low-humidity environment, away from any potential sources of contamination. And be sure to use them within the recommended shelf life – after all, even the best welding rod can’t work its magic if it’s been sitting around for too long.
And when it comes to handling your welding rods, the golden rule is to keep them clean and dry. Avoid touching the end of the rod with your bare hands, and make sure to wipe away any moisture or debris before striking the arc. Trust me, a little bit of care and attention can go a long way in ensuring the success of your welding project.
Real-World Welding Rod Success Stories
Now, you might be thinking, “Okay, I get it, choosing the right welding rod is important. But how do I know I’m making the right choice?” Well, let me share a couple of real-world success stories to help put things in perspective.
Take the case of our client, Joe, who was tasked with welding some high-strength alloy components for a heavy-duty industrial machine. After consulting with our team, he decided to go with a specialized flux-cored welding rod that was designed to produce a strong, penetrating weld with minimal distortion. The results were nothing short of spectacular – the finished welds were rock-solid, with a clean, uniform appearance that exceeded all of the client’s expectations.
Or how about the time we helped our friend, Sarah, tackle a tricky stainless steel welding project for a high-end commercial kitchen? She was struggling to find the right welding rod to produce the corrosion-resistant, visually-appealing welds she needed. After a bit of guidance from our team, she settled on an ER316L stainless steel rod and absolutely nailed it. The finished product looked like it had been crafted by a master artist, and the client was over the moon with the results.
These are just a couple of examples, but the message is clear: when you take the time to choose the right welding rod for the job, the results can be truly extraordinary. And that’s the kind of magic I live for, my friends.
Conclusion: Embrace the Power of the Welding Rod
So there you have it, the inside scoop on picking the perfect welding rod. Whether you’re a seasoned pro or a DIY enthusiast, mastering the art of welding rod selection is the key to unlocking your full welding potential.
Remember, the right welding rod can mean the difference between a weld that’s strong, durable, and visually stunning, and one that’s… well, let’s just say, less than desirable. So don’t be afraid to experiment, ask questions, and always keep learning. The world of welding is a vast and ever-evolving landscape, and the more you explore, the more rewards you’ll reap.
And who knows, maybe one day you’ll be the one sharing your own welding rod success stories, inspiring the next generation of welders to reach for the stars. Because when it comes to the art of welding, the possibilities are truly endless.
Now, what are you waiting for? Grab that welding rod, fire up that torch, and let’s get to work! The world is waiting for your masterpieces.