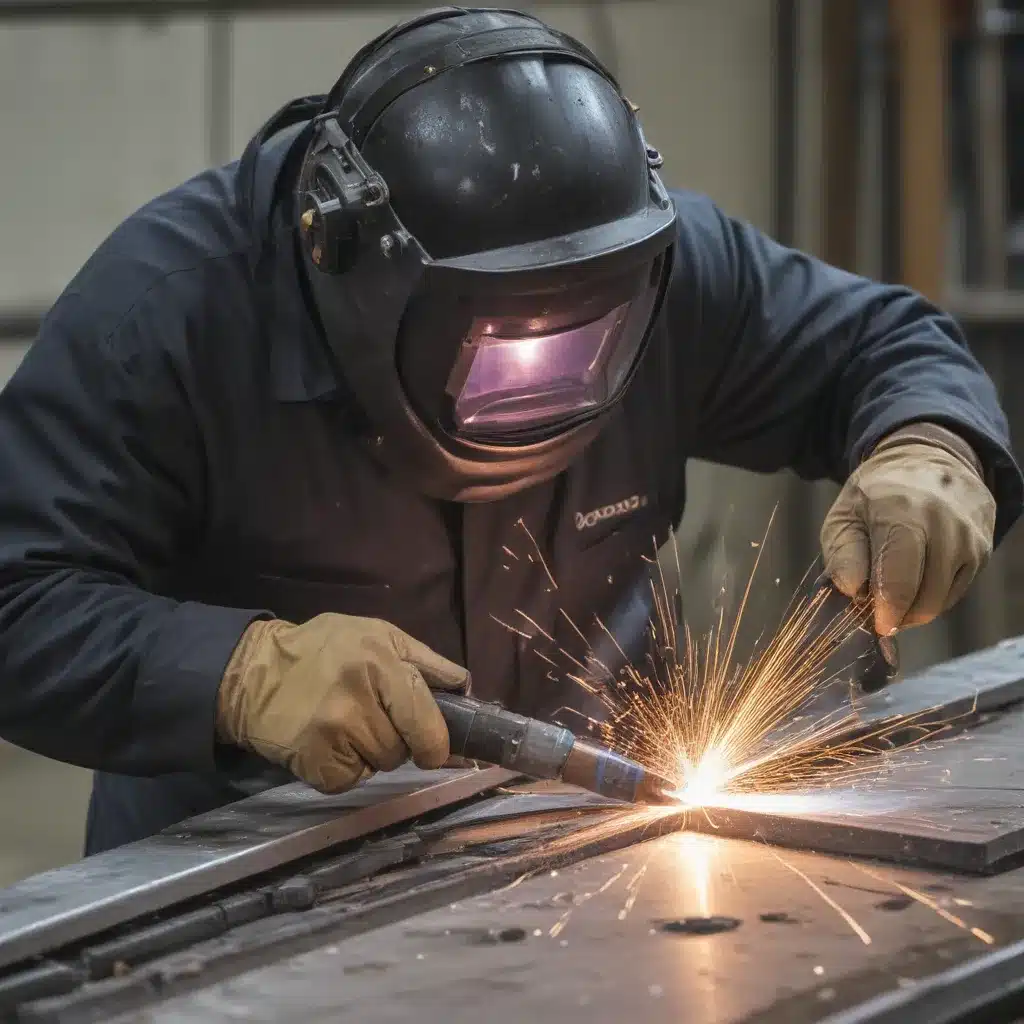
What is Orbital Welding, Exactly?
Alright, let’s dive right into the juicy stuff – orbital welding. Now, I know what you’re thinking… “Orbital welding? Isn’t that some sort of advanced, sci-fi sounding welding technique that only the big-bucks companies can afford?” Well, my friends, you’d be partially right. Orbital welding is a pretty specialized process, but it’s not as out-of-reach as you might assume. In fact, it could be the perfect solution for your next welding project, depending on your needs.
So, what is orbital welding, you ask? In short, it’s a type of automated welding where a welding head rotates (orbits) around a stationary workpiece to create a continuous, uniform weld. This is in contrast to standard manual welding, where the welder has to manually move the welding torch around the workpiece.
The key advantage of orbital welding is that it allows for extremely precise, consistent, and repeatable welds – the kind that are essential for high-pressure, critical applications like piping, tubing, and other specialized components. The automated nature of the process means there’s no risk of human error or inconsistency creeping in, which can be a real problem with manual welding.
And the best part? Orbital welding isn’t just for the big boys. Thanks to advancements in technology, there are now orbital welding solutions available that are surprisingly affordable and accessible, even for small-to-medium sized fabrication shops. So don’t count it out just yet!
When Should You Use Orbital Welding?
Alright, now that we’ve got the basics of orbital welding down, let’s talk about when you might want to actually use this specialized technique. After all, it’s not like you should be breaking out the orbital welder for every single welding job, right? There are definitely some specific applications and scenarios where orbital welding really shines.
One of the prime use cases for orbital welding is anything involving tight tolerances, critical welds, or high-pressure systems. Think things like nuclear, aerospace, or semiconductor manufacturing – areas where you simply can’t afford to have sloppy, inconsistent welds. The automated precision of orbital welding ensures that every single weld is exactly the same, which is crucial for maintaining the integrity and safety of these sensitive systems.
Another big area where orbital welding excels is pipe and tubing fabrication. Whether it’s stainless steel, titanium, or exotic alloys, orbital welding can handle all sorts of materials and joint configurations with ease. The ability to create perfectly consistent, leak-tight welds all the way around the pipe is a game-changer for applications like food & beverage processing, pharmaceutical manufacturing, and high-purity chemical systems.
But it’s not just high-stakes industrial applications where orbital welding shines. Even in more standard fabrication work, orbital welding can offer some real benefits. For example, the speed and efficiency of the automated process can make it a great choice for high-volume production work. And the superior weld quality means less post-weld cleanup or rework is needed, saving time and money.
So in summary, if you’re working on any project that demands exceptionally precise, repeatable welds – whether it’s mission-critical industrial equipment or high-volume fabrication – orbital welding is definitely worth considering. It may seem like an advanced, specialized technique, but the technology has come a long way, and it could be more accessible than you think.
The Benefits of Orbital Welding
Okay, so we’ve covered what orbital welding is and when it might be a good fit. But what are the actual benefits that make this welding process so special? Let me break it down for you:
Consistent, Repeatable Welds: As I mentioned before, the key advantage of orbital welding is the ability to create welds that are identical, every single time. There’s no risk of human error or inconsistency creeping in, which is critical for high-pressure, high-stakes applications.
Superior Weld Quality: Orbital welding produces exceptionally clean, uniform, and high-quality welds. The automated process ensures perfect bead appearance, penetration, and fusion, with minimal spatter or distortion. This translates to stronger, more durable joints that require less post-weld cleanup.
Improved Productivity: The speed and efficiency of orbital welding can be a real game-changer, especially for high-volume production work. The automated process is much faster than manual welding, allowing you to crank out more parts in less time. And since the welds are perfect every time, you’ll spend a lot less time on rework or post-weld finishing.
Enhanced Safety: With orbital welding, there’s no need for a welder to stand right next to the workpiece, potentially exposing themselves to fumes, sparks, and other welding hazards. The remote operation of the welding head keeps the operator at a safe distance, reducing the risk of injury or exposure.
Versatility: Orbital welding isn’t just for exotic, high-end applications. Modern orbital welding solutions can handle a wide range of materials, joint configurations, and part sizes – from tiny capillary tubing all the way up to large-diameter pipes. So it’s a flexible tool that can be utilized across many different fabrication projects.
Reduced Distortion: The controlled, consistent heat input of orbital welding minimizes thermal distortion of the workpiece. This is a huge advantage, especially for thin-walled or sensitive components that are prone to warping and deformation during the welding process.
So in a nutshell, orbital welding provides unparalleled weld quality, consistency, and productivity – all while enhancing safety and reducing post-weld rework. It’s a specialized technique, sure, but one that can offer a ton of value, even for smaller fab shops and general fabrication work. Definitely something to keep in mind for your next project!
Real-World Applications of Orbital Welding
Now that we’ve covered the basics of orbital welding and the key benefits it offers, let’s take a look at some real-world examples of where this technology is being put to use. After all, seeing the technology in action can really help bring home why it’s such a game-changer in certain industries and applications.
One area where orbital welding is an absolute must-have is the nuclear power industry. These facilities rely on intricate, high-pressure piping systems to safely contain and transport all sorts of radioactive materials and coolants. Given the mission-critical nature of these systems, there’s simply no room for error or inconsistency in the welding. Orbital welding ensures that every single weld, no matter where it’s located, meets the strictest quality standards.
Another prime example is the semiconductor manufacturing sector. These ultra-clean, high-tech facilities require an incredible level of precision, and that extends all the way down to the piping and tubing that transports the specialized gases and liquids used in the manufacturing process. Orbital welding provides the flawless, leak-tight welds that are essential for maintaining the integrity of these critical systems.
And it’s not just heavy industry where orbital welding shines. Take the food and beverage processing world, for instance. Stainless steel pipe and tubing are ubiquitous in this industry, used to transfer all sorts of liquids, slurries, and other products. Orbital welding ensures that these joints are not only strong and durable, but also completely smooth and crevice-free – critical for maintaining proper sanitation and preventing product contamination.
But it’s not just about industrial applications. Orbital welding has even found a home in the world of high-end custom fabrication and restoration work. I’ve seen it used to create stunning, one-of-a-kind stainless steel kitchen islands, outdoor fire pits, and even vintage car restoration projects. The ability to deliver flawless, consistent welds, even on complex, curved components, is a real game-changer for these types of specialty fabrication jobs.
So as you can see, orbital welding is about a lot more than just high-tech nuclear reactors and semiconductor fabs. It’s a versatile technology that’s making its mark across a wide range of industries and applications – wherever precision, consistency, and top-notch weld quality are absolutely essential. And as the technology continues to evolve and become more accessible, I have a feeling we’re going to be seeing a lot more orbital welding out there in the real world.
Choosing the Right Orbital Welding Equipment
Alright, so you’re convinced that orbital welding is the way to go for your next project. But now comes the tricky part – actually selecting the right orbital welding equipment for your needs. After all, not all orbital welding systems are created equal, and the wrong choice could end up costing you big time in terms of productivity, weld quality, and overall return on investment.
One of the first things to consider is the size and configuration of the parts or components you’ll be welding. Orbital welding systems come in a wide range of sizes and designs – from compact, handheld units for small-diameter tubing all the way up to massive, floor-mounted systems for large-diameter pipes. Make sure to carefully measure your workpieces and select a system that can accommodate them comfortably.
Another key factor is the type of materials you’ll be welding. Different orbital welding systems are optimized for different base metals, from standard stainless steel to exotic alloys like titanium or Inconel. The welding power source, shielding gas, and other parameters need to be matched to the specific metallurgy of your project. Choosing the wrong setup can lead to poor weld quality, increased rework, and a whole host of other headaches.
And let’s not forget about automation and control capabilities. The most advanced orbital welding systems these days come loaded with all sorts of smart features – real-time weld monitoring, automated program selection, data logging, and more. These types of capabilities can make a huge difference in terms of streamlining your workflow, ensuring quality, and maximizing productivity. But they also come at a premium, so you’ll need to weigh the benefits against your budget.
Of course, the most important factor of all is finding a supplier and service provider that you can truly trust. Orbital welding is a specialized field, and having access to expert guidance, training, and post-sale support can make all the difference in the world. Look for a vendor that not only sells the equipment, but also has the knowledge and resources to help you get the most out of it.
At the end of the day, selecting the right orbital welding setup for your needs is a bit like a high-stakes game of Goldilocks – you need to find the one that’s “just right” in terms of size, capability, and support. But trust me, it’s well worth the effort. Dialing in the perfect orbital welding solution can pay huge dividends in terms of weld quality, productivity, and overall project success. It’s an investment that’s sure to pay off down the road.
Mastering the Art of Orbital Welding
Alright, by now you should have a pretty solid understanding of what orbital welding is all about and why it’s such a game-changer in certain industries and applications. But as with any specialized welding technique, there’s a bit of an art and science to actually executing it flawlessly. And that’s what I want to dive into next.
See, orbital welding may be automated, but that doesn’t mean it’s completely foolproof. There are still plenty of variables and techniques that need to be dialed in to achieve truly high-quality, consistent welds. And mastering those nuances is key to unlocking the full potential of this technology.
One of the big ones is joint preparation. With orbital welding, you need to make sure your workpieces are meticulously cleaned, aligned, and fitted together with laser-like precision. Even the slightest gap or misalignment can wreak havoc on the weld bead and cause all sorts of issues down the line. It’s attention to detail like this that really separates the orbital welding pros from the amateurs.
Another critical factor is selecting the right welding parameters – things like amperage, voltage, travel speed, shielding gas, and so on. These variables need to be fine-tuned for the specific material, joint configuration, and part size you’re working with. Get it wrong, and you could end up with porosity, cracking, or any number of other weld defects. Experienced orbital welders know that it’s all about finding that sweet spot.
And let’s not forget about the human element. Even though orbital welding is automated, there’s still a skilled operator behind the controls. Proper training, practice, and troubleshooting know-how are essential for being able to diagnose issues, make adjustments on the fly, and ensure that every single weld comes out picture-perfect.
I’ve seen firsthand how orbital welding can transform a fabrication operation – taking it from sloppy, inconsistent welds to a level of precision and repeatability that just blows people away. But getting to that point takes real mastery of the craft. It’s about understanding the science, sweating the details, and constantly honing your skills.
Now, I know what you might be thinking – “Geez, this all sounds way too complicated for the average fab shop to pull off.” And to a certain extent, you’d be right. Orbital welding does require a higher level of specialized knowledge and expertise compared to standard manual welding. But the good news is, there are plenty of qualified orbital welding service providers out there who can handle all the heavy lifting for you.
So whether you’re looking to bring orbital welding in-house or just need a trusted partner to handle those critical, high-precision welds, the key is finding the right team of orbital welding experts. With their guidance and support, you can unlock all the incredible benefits of this technology without having to become a master welder yourself. Sounds like a win-win to me!
Conclusion: Unlock the Power of Orbital Welding
Well, there you have it – a deep dive into the world of orbital welding. We’ve covered what it is, when you should use it, the incredible benefits it offers, how to choose the right equipment, and even the art of mastering this specialized welding technique.
The bottom line is this: orbital welding is a game-changer. It’s a welding process that delivers unparalleled precision, consistency, and quality – the kind that’s essential for mission-critical, high-stakes applications in industries like nuclear power, semiconductors, and beyond.
But here’s the best part: orbital welding isn’t just for the big dogs anymore. Thanks to advancements in technology and increased accessibility, this specialized welding solution is now within reach for all sorts of fabrication shops – from small custom fab houses to large-scale production facilities.
So if you’re working on any projects that demand flawless, repeatable welds – whether it’s high-pressure piping, exotic aerospace components, or even intricate custom fabrication – I highly encourage you to take a long, hard look at orbital welding. It might just be the missing piece that takes your welding game to the next level.
Of course, I know navigating the world of orbital welding can be a bit daunting, especially if you’re coming from a more traditional welding background. But that’s where the experts come in. Companies like Corr Connect have the specialized knowledge, state-of-the-art equipment, and top-notch support to help you unlock the full potential of orbital welding for your business.
So what are you waiting for? It’s time to embrace the power of orbital welding and take your fabrication operation to new heights of precision, productivity, and quality. Trust me, your customers (and your bottom line) will thank you.