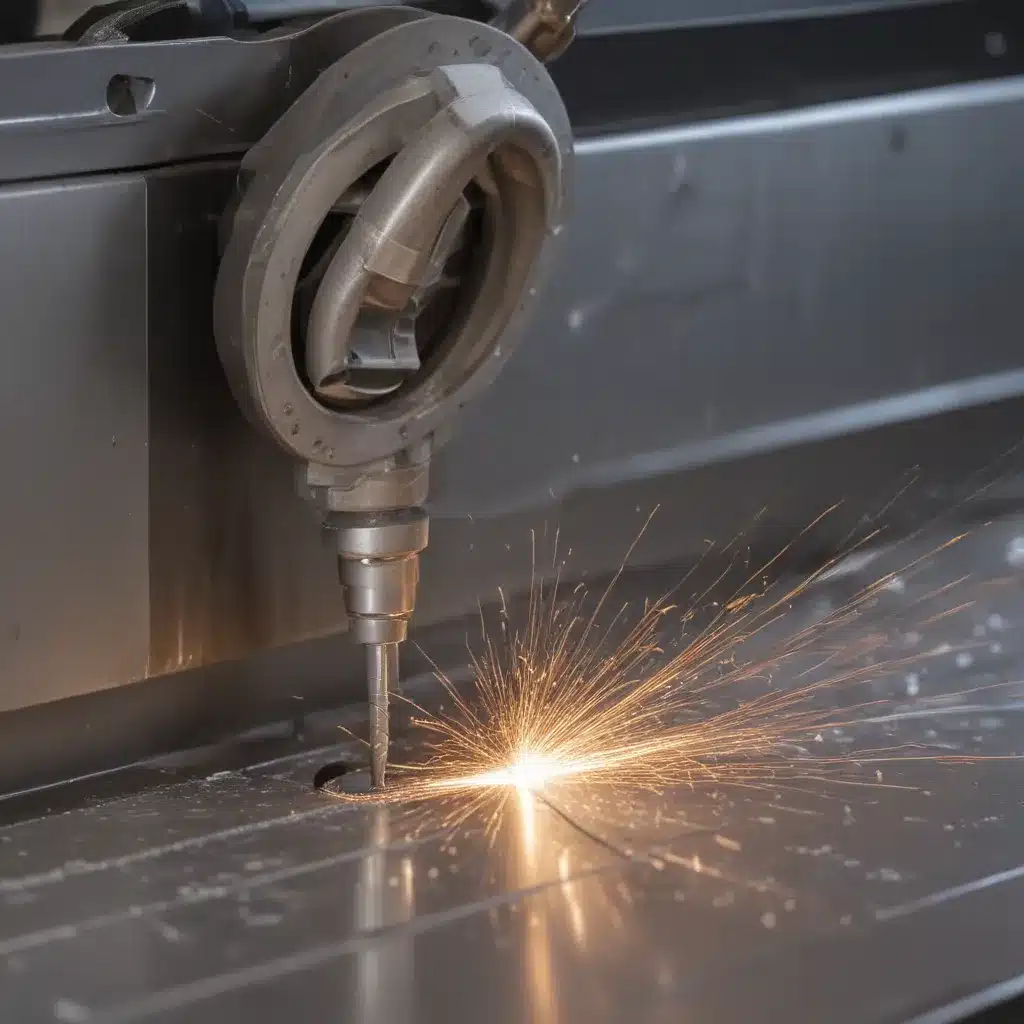
The Need for Speed (and Precision)
As a seasoned welding professional, I’ve seen firsthand how the speed of the welding process can make all the difference in the quality and durability of the final product. In the world of sheet metal fabrication, where precision and consistency are paramount, the optimization of travel speed is a critical aspect that often separates the good from the great.
You see, the travel speed at which you move the welding torch or electrode along the joint can have a profound impact on the heat input, bead profile, and overall integrity of the weld. Move too fast, and you risk incomplete fusion, porosity, and a weak, inconsistent bead. Move too slow, and you can end up with excessive heat input, distortion, and a messy, unattractive weld.
But finding that sweet spot – that perfect harmony of speed and precision – is where the magic happens. It’s where you can unlock the true potential of your welding skills and deliver exceptional results for your clients. And that’s precisely what I’m here to help you achieve.
Mastering the Fundamentals of Travel Speed
So, what exactly goes into optimizing travel speed for quality welds in sheet metal fabrication? Well, my friends, it all starts with a deep understanding of the underlying principles at play.
First and foremost, we need to consider the relationship between travel speed, heat input, and weld penetration. You see, as you increase the travel speed, the heat input per unit length of weld decreases, which can lead to a shallower, more narrow weld bead. Conversely, decreasing the travel speed results in a higher heat input and a deeper, wider weld.
Now, you might be thinking, “Well, if more heat input means deeper penetration, then I should just go super slow, right?” Not so fast, my welding aficionado. While it’s true that slower speeds can result in deeper penetration, there’s a delicate balance to strike. Excessively slow speeds can lead to excessive heat input, which can cause distortion, burn-through, and other undesirable effects.
To complicate matters further, the optimal travel speed can also vary depending on the thickness of the material, the type of welding process, and the specific joint configuration. Thicker materials, for example, may require a slower travel speed to ensure adequate penetration, while thinner materials may demand a faster pace to avoid burn-through.
Putting Theory into Practice
So, now that we’ve covered the underlying principles, let’s dive into some practical strategies for optimizing travel speed in sheet metal fabrication.
One of the first things I like to do is conduct a series of weld tests, using a range of travel speeds and carefully monitoring the results. This allows me to establish a baseline and identify the sweet spot for a given set of materials and welding parameters. I might start with a slower speed, say 6 inches per minute, and gradually increase the pace, checking the bead profile, penetration, and overall appearance after each pass.
Another important consideration is the type of welding process you’re using. For example, in gas metal arc welding (GMAW), also known as MIG welding, the travel speed can have a significant impact on the weld bead shape and appearance. A faster travel speed can result in a narrower, more uniform bead, while a slower speed may lead to a wider, more convex profile.
On the other hand, in shielded metal arc welding (SMAW), or stick welding, the travel speed is often a bit more forgiving. The flux-coated electrode can help to stabilize the weld pool and compensate for slight variations in speed. That said, finding the optimal travel speed is still crucial for achieving consistent, high-quality welds.
And let’s not forget about the importance of joint preparation and fit-up. The cleanliness and fit of the workpieces can have a direct impact on the travel speed you’re able to maintain. Poorly fitted or contaminated joints may require a slower pace to ensure proper fusion and prevent defects.
Leveraging Technology and Data
In today’s digital age, we’re fortunate to have access to a wealth of technological tools and resources that can help us optimize travel speed for quality welds. From advanced welding machines with built-in travel speed monitoring to sophisticated data-logging systems, the possibilities are endless.
For example, many modern welding power sources come equipped with features that allow you to precisely control and monitor the travel speed. Some even have the ability to automatically adjust the parameters based on the joint configuration and material thickness, taking the guesswork out of the equation.
But the real game-changer, in my opinion, is the use of data-logging and analytics. By capturing detailed information on every weld, from travel speed and heat input to bead profile and penetration, we can identify patterns, troubleshoot issues, and fine-tune our processes for optimal results.
Imagine being able to correlate specific travel speed ranges with the highest-quality welds, or pinpointing the sweet spot for a particular material and joint design. This kind of data-driven approach not only helps us improve our welding skills but also allows us to provide our clients with a level of consistency and reliability that sets us apart from the competition.
The Human Touch: Mastering the Art of Welding
Of course, as advanced as the technology may be, there’s still no substitute for the human touch when it comes to welding. After all, it’s the skill, experience, and intuition of the welder that truly sets the stage for success.
I’ve seen it time and time again – welders with decades of experience who can seemingly dial in the perfect travel speed without even thinking about it. They’ve developed an innate feel for the process, a sixth sense that tells them exactly when to adjust their pace and how to maintain that all-important rhythm.
And it’s not just about the speed; it’s about the way they move, the subtle adjustments they make, the way they read the weld pool and respond to the ever-changing conditions. It’s a true art form, and it’s what separates the masters from the novices.
So, while we may leverage technology to our advantage, we must never lose sight of the human element. The ability to troubleshoot, problem-solve, and adapt on the fly – that’s what really sets the great welders apart. And it’s a skill that can only be honed through dedicated practice, endless experimentation, and a deep, abiding passion for the craft.
Conclusion: Elevating Your Welding Game
At the end of the day, optimizing travel speed for quality welds in sheet metal fabrication is all about striking the perfect balance between science and art. It’s about understanding the underlying principles, leveraging the power of technology, and honing your skills to the point where you can almost intuitively dial in the perfect pace.
But the journey doesn’t end there. As with any craft, there’s always room for growth, always new techniques to explore, and always new challenges to overcome. And that’s what makes this field so endlessly fascinating and rewarding.
So, whether you’re a seasoned pro or just starting out, I encourage you to embrace the challenge, to experiment, and to push the boundaries of what’s possible. Because when you nail that perfect weld, with a bead that’s as strong as it is beautiful, there’s simply nothing else like it.
And who knows, maybe one day, you’ll be the one teaching the next generation of welders the secrets of the trade – the ones that separate the good from the great, and the great from the truly extraordinary.
In the meantime, keep learning, keep practicing, and keep pushing the limits of what’s possible. Because when it comes to welding, the only limit is your own imagination.
And if you’re ever in need of a reliable, precision-focused welding partner, be sure to check out Corr Connect. We’re a team of passionate, skilled welders who live and breathe this craft, and we’d be more than happy to put our expertise to work for you.