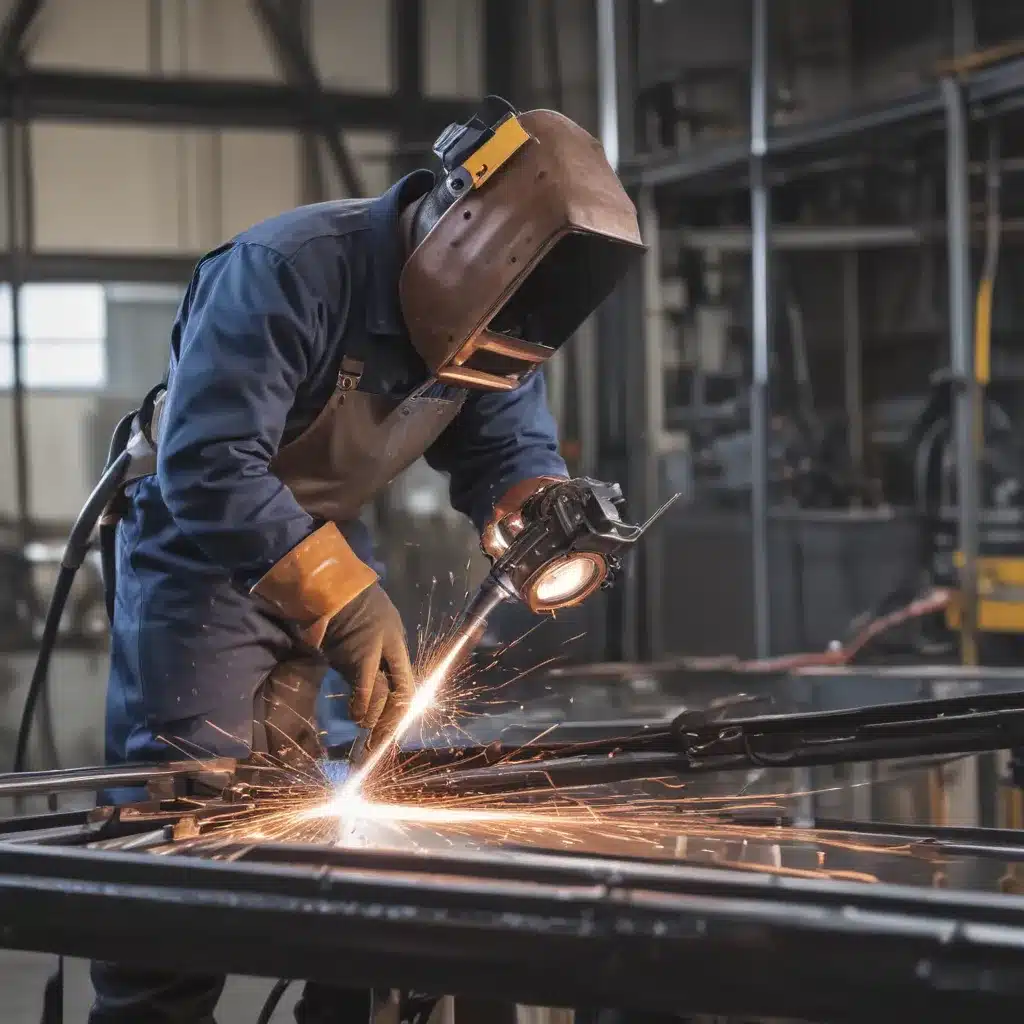
The Rise of Automated Welding: A Glimpse Into the Future
I’ll never forget the first time I stepped onto the floor of a modern, state-of-the-art fabrication facility. The air was thick with the acrid scent of molten metal and the constant hum of high-powered machinery. It was like stepping into the beating heart of industry – a symphony of automation, precision, and raw power.
As I navigated the maze of robotic welding cells and computer-controlled cutting tables, I couldn’t help but be in awe of the sheer efficiency and speed of these automated systems. Gone were the days of arduous, manual welding – these machines could churn out complex metal components with a level of consistency and quality that left their human counterparts in the dust.
Of course, the path to this automated utopia wasn’t without its challenges. I remember talking to the facility manager, a veteran welder with more calluses on his hands than I had hairs on my head. He recounted the early days of automation, when workers feared for their jobs and suppliers struggled to keep up with the breakneck pace of technological change.
“It was a tough transition, I’ll admit,” he told me, wiping the sweat from his brow. “But once we got the hang of it, there was no going back. These machines made us faster, more precise, and frankly, a hell of a lot more profitable. Now, I can’t imagine running this place any other way.”
Unlocking the Power of Automated Welding
As I delved deeper into the world of automated welding, I began to understand just how transformative this technology has been for the industry. Gone are the days of tedious, manual welding – these sophisticated systems have ushered in a new era of efficiency, precision, and cost-savings.
Take, for example, the humble arc welding process. Traditionally, this was a slow, labor-intensive task that required a high degree of skill and dexterity. But with the advent of automated arc welding systems, the entire process has been streamlined and optimized. These machines can lay down clean, consistent welds at breakneck speeds, all while maintaining a level of quality that would be virtually impossible for a human welder to achieve.
And it’s not just arc welding that’s been transformed by automation. Metal cutting and custom fabrication have also benefited from the integration of advanced robotics and computer-controlled machinery. I’ve seen these systems effortlessly slice through thick steel plates, creating intricate, custom-tailored components with a level of precision that leaves even the most skilled manual craftsman in awe.
But the real beauty of these automated systems lies in their ability to adapt and evolve. Thanks to sophisticated control systems and advanced programming, these machines can be easily reconfigured to handle a wide range of welding and fabrication tasks – from simple repairs to complex, one-off projects. This unparalleled flexibility has made them an indispensable asset for businesses of all sizes, from small custom fabrication shops to large-scale manufacturing facilities.
The Cutting Edge of Welding Automation
As I continued my exploration of the automated welding landscape, I couldn’t help but be amazed by the sheer breadth of technological innovations taking place. It’s a veritable arms race, with manufacturers constantly pushing the boundaries of what’s possible in terms of speed, precision, and versatility.
One area that’s particularly exciting is the rise of robotic welding systems. These advanced machines are equipped with sophisticated sensors and control algorithms that allow them to perform complex welding tasks with a level of precision that would make even the steadiest-handed human welder green with envy. I’ve seen them seamlessly navigate tight spaces, maintain perfect bead placement, and adjust on the fly to accommodate slight variations in the workpiece – all without breaking a sweat.
And it’s not just the welding process itself that’s been transformed by automation. The supporting technologies, like automated material handling and computer-aided design (CAD) software, have also undergone a revolution. Imagine a world where a design engineer can simply upload a 3D model, and the entire fabrication process – from cutting to welding to finishing – is handled by a coordinated network of automated systems. It’s a level of efficiency and productivity that would have been unimaginable just a few short decades ago.
But perhaps the most exciting development in the world of automated welding is the increasing integration of artificial intelligence (AI) and machine learning. These cutting-edge technologies are enabling welding systems to “learn” from their own experience, constantly fine-tuning their processes and adapting to changing conditions. I’ve seen welding robots that can detect subtle flaws in their own work and make real-time adjustments to prevent defects – a level of quality control that would be virtually impossible for a human welder to achieve.
The Future of Precision Welding Services
As I reflect on the incredible advancements I’ve witnessed in the world of automated welding, I can’t help but feel a sense of excitement and anticipation for the future. The possibilities are truly limitless, and I can’t wait to see what the next generation of welding automation will bring.
Perhaps the most intriguing aspect of this technological revolution is the way it’s transforming the very nature of welding services. Gone are the days of relying on a team of highly skilled, but ultimately fallible, human welders. Instead, businesses are turning to precision welding services that leverage the power of automation to deliver unparalleled consistency, quality, and cost-effectiveness.
I’ve had the privilege of speaking with several industry leaders who have embraced this new paradigm, and the stories they’ve shared are nothing short of inspiring. Take, for example, the case of a small custom fabrication shop that was struggling to keep up with demand. By investing in a state-of-the-art automated welding system, they were able to drastically increase their production capacity while simultaneously improving the quality of their work. The owner told me that the return on investment was almost immediate, and the boost in efficiency has allowed them to take on larger, more complex projects that were previously out of reach.
Or consider the experience of a large-scale manufacturing facility that was plagued by inconsistent welds and high rates of defects. By partnering with a precision welding service that specializes in automated systems, they were able to streamline their entire fabrication process, reducing scrap rates and improving overall product quality. The cost savings were significant, but the real benefit, according to the plant manager, was the peace of mind that came with knowing that every weld would be executed with unparalleled precision and consistency.
Embracing the Future of Welding
As I wrap up my exploration of the world of automated welding, I can’t help but feel a sense of awe and wonder. This technology has truly revolutionized the way we approach fabrication and manufacturing, ushering in a new era of efficiency, precision, and cost-effectiveness.
But it’s not just about the numbers and the metrics – it’s about the profound impact that these automated systems are having on the very nature of welding and fabrication. By taking the tedium and variability out of these critical processes, we’re freeing up our skilled workers to focus on higher-level tasks and problem-solving. It’s a shift that’s not only improving the bottom line, but also enhancing job satisfaction and fostering a culture of innovation and continuous improvement.
And as I look to the future, I can’t help but feel a deep sense of excitement and anticipation. With the rapid advancements in robotics, AI, and computer control systems, I can only imagine what the next generation of automated welding will bring. Perhaps we’ll see welding robots that can self-diagnose and repair their own components, or systems that can interpret complex 3D designs and automatically generate the optimal welding sequence. The possibilities are truly endless, and I can’t wait to see how this technology continues to evolve and transform the industry.
So if you’re a business owner or a fabrication professional, I urge you to embrace the power of automated welding. Explore the cutting-edge solutions available, and discover how these transformative technologies can unlock new levels of efficiency, quality, and profitability for your operation. The future of welding is here, and it’s time to dive in and be a part of it.
And if you’re looking for a trusted partner to help you navigate this exciting new frontier, I highly recommend checking out Corr Connect. Their team of welding experts specializes in the design, installation, and maintenance of state-of-the-art automated welding systems, and they’re always at the forefront of the latest industry innovations. Whether you’re looking to upgrade your existing operation or build a cutting-edge fabrication facility from the ground up, Corr Connect has the knowledge, the experience, and the passion to help you succeed.
So what are you waiting for? The future of welding is here, and it’s time to get on board. Let’s dive in, explore the wonders of automation, and unlock a whole new world of possibilities for your business. The future is bright, my friends, and it’s time to embrace it with open arms.