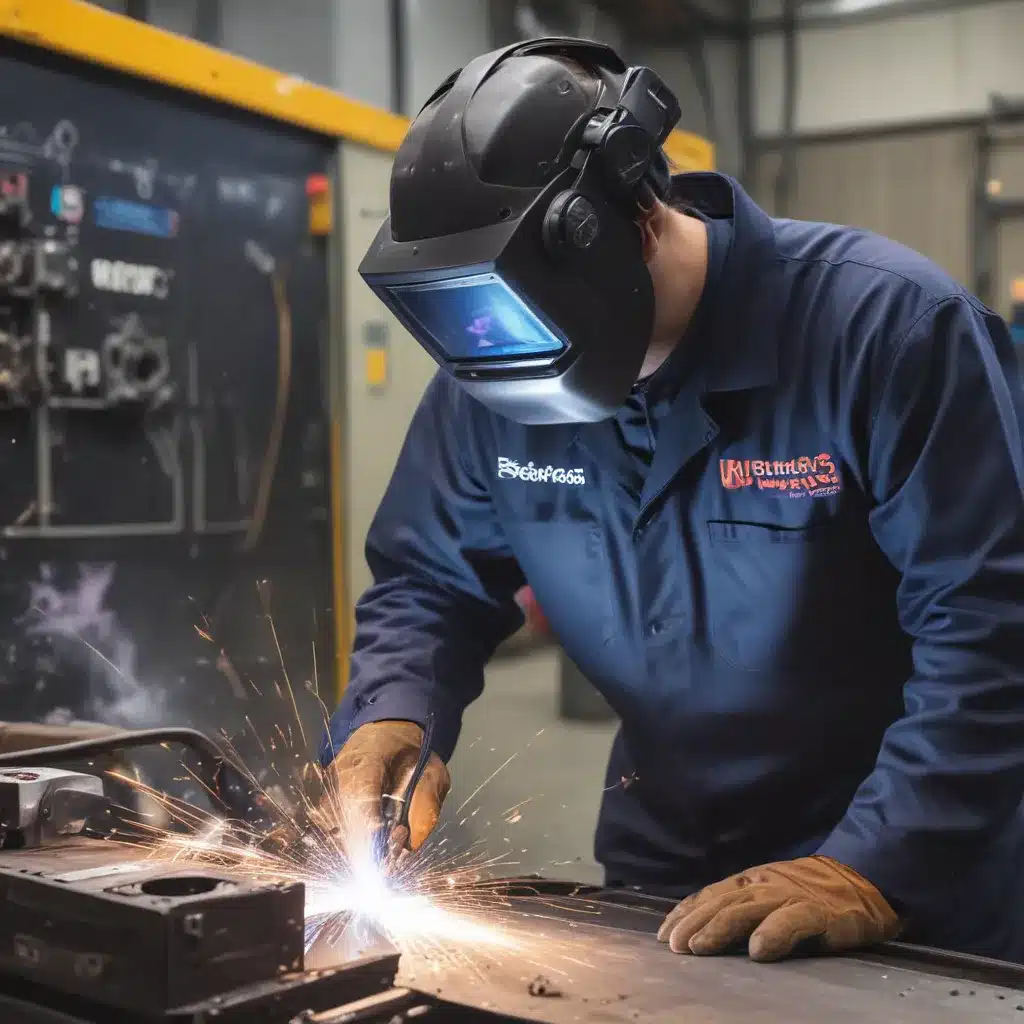
A Welder’s Perspective on the Transformative Power of AR
You know, when I first got into welding, I’ll admit – I didn’t see myself as the type of person who would be on the cutting edge of technology. I mean, my dad was a welder, and his dad before him. It’s a craft that’s been around for centuries, and there’s a certain timelessness to it, you know? The smell of the arc, the sizzle of the metal, the satisfying hiss as the weld cools – that’s the stuff that gets my blood pumping.
But as I’ve progressed in my career, I’ve come to realize that the world of welding is changing in some pretty incredible ways. And at the forefront of that change is augmented reality (AR). Now, I know what you’re thinking – “AR? In my welding shop? Get outta here!” But trust me, this technology is about to revolutionize the way we work.
Enhancing Precision and Accuracy with AR Welding
Let’s start with the basics. One of the biggest challenges in welding is maintaining precise control over the welding process. There are so many variables to keep track of – the angle of the torch, the distance from the workpiece, the speed of travel, the heat input, and on and on. And if any of those factors get out of whack, you can end up with a sloppy, subpar weld that just won’t cut it.
But with AR, we can take a lot of the guesswork out of the equation. Imagine being able to see a virtual overlay of the perfect weld profile, right there in front of you as you work. You could adjust the torch position, the travel speed, and other parameters in real-time, and get immediate feedback on how it’s affecting the weld quality. It’s like having a welding coach standing right beside you, giving you tips and adjustments every step of the way.
And the benefits don’t stop there. AR can also help us better visualize the workpiece and the surrounding area, identifying potential obstacles or interference points before they become a problem. I can’t tell you how many times I’ve had to stop and re-position a part because something was in the way, or the access just wasn’t quite right. With AR, I’d be able to see those issues ahead of time and plan accordingly.
Improved Training and Knowledge Sharing with AR
But the real game-changer, in my opinion, is how AR can transform the way we train new welders and share knowledge across the industry. Imagine being able to take a prospective welder through a virtual welding simulation, where they can practice techniques and get immediate feedback without ever striking an arc. They could learn the fundamentals of joint preparation, torch manipulation, and weld profile control in a safe, controlled environment, before ever setting foot in the shop.
And once they’re on the job, AR can continue to be a valuable training tool. Imagine being able to overlay expert-level welding techniques right onto the workpiece, and have a novice welder follow along, learning the subtle nuances of the process. Or being able to remotely guide a less experienced welder through a challenging joint, offering real-time feedback and adjustments. The possibilities for knowledge sharing and skill development are endless.
Streamlining Custom Fabrication with AR
Of course, the benefits of AR in welding aren’t just limited to training and precision. It can also have a huge impact on the custom fabrication side of the business. Think about it – when you’re working on a one-off project, there’s a lot of back-and-forth between the design team, the welders, and the client. Trying to communicate complex geometries and weld requirements through 2D drawings and verbal descriptions can be a real headache.
But with AR, we can create virtual 3D models of the project, and literally walk through the fabrication process step-by-step. The design team can overlay their vision directly onto the physical workpiece, showing the welders exactly what needs to be done. And the client can come in and see the project in real-time, offering feedback and approvals without having to interpret a bunch of technical drawings.
It’s a game-changer for custom work, where every project is unique and the margin for error is slim. With AR, we can eliminate a lot of the guesswork and miscommunication, and focus on delivering the highest-quality results possible.
The Future is Bright for Welding and AR
Now, I know what you’re thinking – “This all sounds great, but is it really ready for the real world?” And I’ll be honest, the technology is still relatively new and there’s a lot of room for improvement. But the progress I’ve seen in just the last few years has been truly remarkable.
The AR welding systems I’ve tried are becoming more user-friendly, more accurate, and more affordable all the time. And as the hardware and software continue to evolve, I can only imagine what the future will hold. Maybe one day we’ll have AR-enabled welding helmets that can give us real-time guidance and feedback, or AR-controlled robotic welding systems that can produce flawless welds with superhuman precision.
The way I see it, AR isn’t just the future of welding – it’s the present. And those of us who are willing to embrace it and push the boundaries of what’s possible are going to be the ones who shape the industry for years to come. So if you ask me, the future of welding is looking pretty bright. And I, for one, can’t wait to be a part of it.
Bringing It All Together: The Endless Possibilities of AR in Welding
As I reflect on the transformative potential of augmented reality in the world of welding, I’m honestly blown away by the endless possibilities. From enhancing precision and accuracy, to improving training and knowledge sharing, to streamlining custom fabrication – this technology has the power to revolutionize our industry in ways I couldn’t have imagined just a few short years ago.
And the best part is, we’re just scratching the surface. As the hardware and software continue to evolve, I can only imagine what the future will hold. Maybe we’ll see AR-enabled welding helmets that can provide real-time guidance and feedback. Or perhaps we’ll witness the rise of AR-controlled robotic welding systems that can produce flawless welds with superhuman precision.
The way I see it, the time to embrace AR in welding is now. Those of us who are willing to push the boundaries of what’s possible and explore the full potential of this technology will be the ones who shape the industry for years to come. It’s an exciting time to be a welder, that’s for sure.
So if you’re a fellow welder, I encourage you to keep an open mind and dive headfirst into the world of augmented reality. Trust me, it’s going to change the way you think about our craft. And if you’re not a welder, but you’re interested in the future of manufacturing and industrial technology, I’d urge you to keep a close eye on the developments in AR welding. Because this is just the beginning, my friends. The future is bright, and it’s coming at us fast.