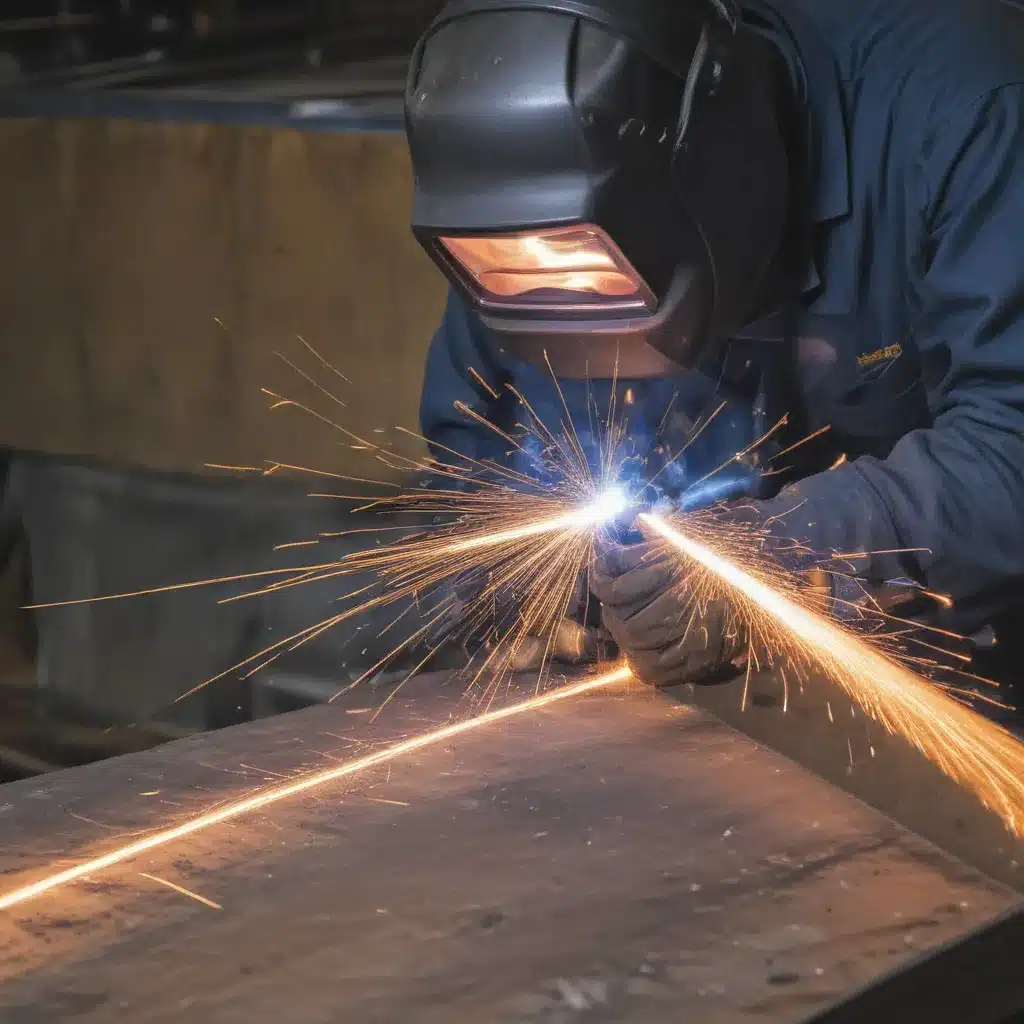
The Scourge of Warp and Distortion
Ah, the perils of welding – where the very heat that binds metal can also be its undoing. As a seasoned welder, I’ve seen my fair share of warped and distorted workpieces, and let me tell you, it’s enough to make even the most grizzled fabricator want to throw in the towel. But fear not, my friends, for I’m here to share the secrets of minimizing these pesky devils, and trust me, it’s a journey worth taking.
You see, the thing about welding is that it’s a bit like a dance – a delicate balance between heat, pressure, and the whims of the metal itself. Get one step wrong, and suddenly, you’ve got a piece that looks like it’s been through a carnival fun house. But fear not, for I’ve got the moves to keep your workpieces as straight as an arrow.
Understanding the Causes of Welding Distortion
Let’s start with the basics, shall we? Welding distortion is the bane of every fabricator’s existence, and it occurs when the heat of the welding process causes the metal to expand and contract in uneven ways. This can lead to all sorts of unsightly and downright problematic results, from warped edges to a general loss of dimensional accuracy.
But what’s really causing this madness, you ask? Well, my friends, it’s a perfect storm of factors, a veritable dance of heat, stress, and the inherent properties of the metal itself. You see, when you apply heat to a piece of metal during the welding process, the heated area expands, while the surrounding, cooler areas remain relatively unchanged. This creates a mismatch in thermal expansion, which in turn leads to the development of internal stresses within the material.
And as if that wasn’t enough, the cooling process can also contribute to the problem. As the heated area cools, it contracts, but the surrounding, cooler areas don’t necessarily follow suit at the same rate. This can result in the infamous warping and distortion that we all know and love to hate.
Strategies for Minimizing Welding Distortion
But fear not, my friends, for I have a few tricks up my sleeve to help you tame the beast of welding distortion. Let’s dive in, shall we?
Proper Joint Design
Ah, the humble joint design – the unsung hero of the welding world. You see, the way you configure your joints can have a significant impact on the final outcome. By carefully considering factors like joint type, weld sequence, and the distribution of heat, you can help to minimize the stresses that lead to distortion.
For example, let’s talk about butt joints. These bad boys can be a real nightmare when it comes to welding distortion, as the heat concentrates in a single, narrow area. But by opting for a double-V or double-U joint design, you can distribute the heat more evenly, helping to counteract the uneven expansion and contraction.
And let’s not forget about the weld sequence – the order in which you lay down your welds can make a world of difference. By following a strategic pattern, you can help to balance out the stresses and reduce the likelihood of distortion.
Proper Fixturing and Clamping
Now, let’s talk about the importance of proper fixturing and clamping. You see, these unsung heroes of the welding world can be the difference between a perfectly straight workpiece and a Picasso-esque masterpiece. By securely holding your metal in place during the welding process, you can help to minimize the movement and distortion caused by the heat.
But it’s not just about clamping down – oh no, my friends. You’ve got to be strategic about it. By carefully positioning your fixturing and clamping devices, you can actually help to counteract the distortion forces, guiding the metal into the desired shape as it cools.
And let’s not forget about the materials you use for your fixturing. By choosing the right tools for the job – be it sturdy steel clamps or heat-resistant ceramics – you can ensure that your workpiece stays put, no matter how hot things get.
Controlled Heat Input
Ah, the elusive art of controlled heat input – the secret sauce of the welding world. You see, the amount of heat you apply to your workpiece can have a huge impact on the final outcome. Too much, and you’re looking at a warped, distorted mess. Too little, and you might as well be trying to weld with a box of matches.
But fear not, my friends, for I’ve got the key to the perfect heat balance. By carefully adjusting your welding parameters – things like amperage, voltage, and travel speed – you can ensure that the heat is distributed evenly and efficiently, minimizing the stresses that lead to distortion.
And let’s not forget about the importance of preheating and post-heating. By carefully controlling the temperature of your workpiece before and after the welding process, you can help to reduce the impact of thermal expansion and contraction, keeping those pesky distortions at bay.
Real-World Examples of Minimizing Welding Distortion
Now, I know what you’re thinking – “All this talk is well and good, but how does it actually work in the real world?” Well, my friends, let me regale you with a few tales from the trenches.
Take the case of the mighty steel bridge project, for example. When we started this job, the client was worried sick about the potential for warping and distortion – after all, we were dealing with some seriously hefty beams and girders. But by carefully designing our joints, strategically placing our fixturing, and meticulously controlling our heat input, we were able to produce a finished product that was as straight as an arrow.
Or how about the time we tackled that tricky aluminum alloy fabrication? Now, anyone who’s worked with aluminum knows that it can be a real diva when it comes to welding distortion. But by using a combination of specialized joint designs, precision clamping, and targeted pre- and post-heating, we were able to create a piece that looked like it had been machined to perfection.
And let’s not forget the time we helped a local artist bring their vision to life. They had this incredible sculpture in mind, but they were worried that the complex, organic shapes would be impossible to weld without distortion. But by working closely with them, analyzing the design, and developing a customized welding strategy, we were able to create a masterpiece that defied the laws of physics.
The Welding Distortion Minefield: Navigating the Challenges
Now, I know what you’re thinking – “This all sounds great, but what about the really tricky stuff? The stuff that keeps us welders up at night?” Well, my friends, I’ve got you covered.
Let’s talk about those thin, delicate workpieces, shall we? When you’re dealing with sheet metal or other thin materials, the risk of distortion is amplified tenfold. The heat just seems to wreak havoc, no matter what you do. But fear not, for I have a few tricks up my sleeve.
By carefully selecting the right welding process – perhaps opting for a lower-heat technique like TIG or MIG – and employing strategic clamping and fixturing, we can help to minimize the distortion and keep those thin materials as straight as an arrow.
And what about those complex, three-dimensional shapes? Oh, the headaches they can cause! But fear not, my friends, for with a little creativity and a whole lot of problem-solving, we can tame even the most daunting of distortion demons.
It might involve a combination of specialized joint designs, multi-pass welding techniques, and the strategic use of heat sinks and backing bars. But trust me, when you see the final product – all sleek and straight, without a hint of warp or twist – it’s enough to make even the most seasoned welder shed a tear of joy.
The Welding Distortion Minefield: Navigating the Challenges
Now, I know what you’re thinking – “This all sounds great, but what about the really tricky stuff? The stuff that keeps us welders up at night?” Well, my friends, I’ve got you covered.
Let’s talk about those thin, delicate workpieces, shall we? When you’re dealing with sheet metal or other thin materials, the risk of distortion is amplified tenfold. The heat just seems to wreak havoc, no matter what you do. But fear not, for I have a few tricks up my sleeve.
By carefully selecting the right welding process – perhaps opting for a lower-heat technique like TIG or MIG – and employing strategic clamping and fixturing, we can help to minimize the distortion and keep those thin materials as straight as an arrow.
And what about those complex, three-dimensional shapes? Oh, the headaches they can cause! But fear not, my friends, for with a little creativity and a whole lot of problem-solving, we can tame even the most daunting of distortion demons.
It might involve a combination of specialized joint designs, multi-pass welding techniques, and the strategic use of heat sinks and backing bars. But trust me, when you see the final product – all sleek and straight, without a hint of warp or twist – it’s enough to make even the most seasoned welder shed a tear of joy.
The Art of Precision Welding: Mastering the Techniques
Now, I know what you’re thinking – “Okay, we’ve got the distortion under control, but what about that whole ‘precision’ thing? How do we make sure our welds are as straight and true as a laser pointer?”
Well, my friends, let me tell you – it’s all about mastering the art of precision welding. And let me tell you, it’s a skill that takes years to hone, but the payoff is oh-so-worth it.
It all starts with the fundamentals – things like proper joint preparation, meticulous joint fit-up, and the careful control of welding parameters. But it goes beyond that, my friends. It’s about developing a keen eye for detail, a steady hand, and an innate understanding of the metal itself.
Take, for example, the art of weld bead placement. By carefully controlling the width and height of each individual weld bead, we can create a smooth, visually appealing finish that’s as straight as the day is long. And don’t even get me started on the importance of consistent travel speed and arc length – these little details can make all the difference between a masterpiece and a hot mess.
And let’s not forget about the power of post-weld processing. By employing techniques like careful grinding, polishing, and even heat treatment, we can take our precision welding to the next level, ensuring that our final product is as smooth and flawless as a mirror.
The Future of Welding Distortion Control: Innovation and Automation
Now, I know what you’re thinking – “This all sounds great, but what about the future? Surely there must be some new-fangled technologies or techniques that can take welding distortion control to the next level, right?”
Well, my friends, you’re absolutely right. The world of welding is constantly evolving, and the fight against distortion is no exception.
Take, for example, the rise of advanced simulation and modeling software. By using cutting-edge computer programs, we can now predict and analyze the behavior of metal during the welding process, allowing us to develop tailored strategies for minimizing distortion before we even pick up a torch.
And let’s not forget about the incredible advancements in automation and robotics. With the help of precision-engineered welding systems and computer-controlled clamping devices, we can now achieve levels of consistency and repeatability that would have been unimaginable just a few decades ago.
But the real game-changer, in my opinion, is the emergence of adaptive welding technologies. By incorporating sensors and real-time feedback systems, these cutting-edge systems can actually adjust the welding parameters on the fly, dynamically compensating for changes in the metal and environmental conditions to keep distortion at bay.
The future of welding distortion control is bright, my friends, and I can’t wait to see what the next generation of fabricators and engineers will come up with. But one thing’s for sure – with the right tools and techniques, we can conquer even the most stubborn of welding distortion demons, one straight, precision-crafted workpiece at a time.
Conclusion: Embracing the Challenge of Welding Distortion
And there you have it, my friends – the secrets to minimizing welding distortion and warping, straight from the heart of a seasoned fabricator. It’s a battle that’s been raging for as long as welding has been a thing, but with the right knowledge, the right tools, and the right mindset, we can emerge victorious.
Sure, it’s not always easy. There are curveballs and challenges around every corner, from those tricky thin materials to the maddening complexities of three-dimensional shapes. But that’s what makes this job so darn rewarding, isn’t it? The thrill of conquering the impossible, of turning chaos into order, of creating something truly remarkable from nothing but heat and a little bit of elbow grease.
So, the next time you find yourself staring down the barrel of a warped, twisted workpiece, don’t despair, my friends. Remember the lessons we’ve learned here today – the importance of joint design, the power of precise fixturing, the magic of controlled heat input. And above all, remember that you’ve got the skills, the knowledge, and the sheer force of will to overcome even the most stubborn of welding distortion demons.
Because at the end of the day, that’s what being a welder is all about, isn’t it? Facing down the challenges, embracing the chaos, and emerging victorious. And trust me, when you see that final product, all sleek and straight and true, there’s no better feeling in the world.
So, let’s raise a welding torch to the art of minimizing distortion, my friends. Let’s celebrate the triumphs, learn from the failures, and never stop pushing the boundaries of what’s possible. Because in the end, that’s what makes this profession so darn special – the endless pursuit of perfection, one straight weld at a time.