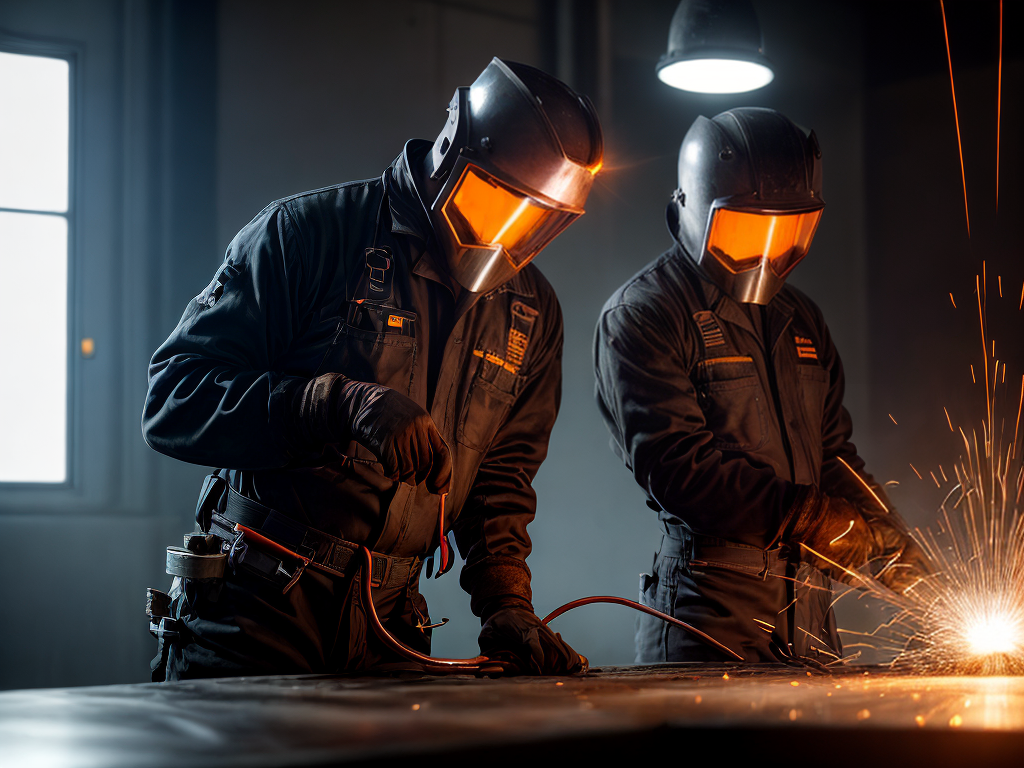
Did you know that choosing the right combination of metals for welding can have a significant impact on the strength and durability of the final product? In fact, studies have shown that up to 80% of welding failures can be attributed to improper material match-up. As someone who seeks mastery in the art of welding, understanding how to pair metals correctly is crucial. In this guide, we will explore the factors to consider when selecting metals for welding, common metal combinations that work well together, and potential issues that may arise. Additionally, we will delve into different welding techniques for various metal pairings and the importance of pre-weld testing. So, let’s dive in and discover the secrets to successful material match-up in welding.
Understanding Metal Compatibility
I have found that understanding the compatibility of metals is crucial when it comes to welding, as it determines how effectively the metals will bond together. There are several factors affecting compatibility that should be considered when selecting metals for welding. One of the main factors is the chemical composition of the metals. Different metals have different chemical properties, and some combinations may lead to weak or brittle welds. Another factor is the physical properties of the metals, such as their melting points and thermal conductivity. Metals with similar melting points and thermal conductivity are more likely to form a strong bond. Additionally, the presence of impurities or surface contaminants can also affect compatibility. To ensure successful welding, it is important to follow metal selection guidelines that take into account these factors and choose metals that are compatible with each other.
Factors to Consider in Metal Selection
When selecting metals for welding, it is important to consider various factors that can influence their compatibility. Understanding the factors that affect metal selection is crucial for achieving successful welds. One of the main factors to consider is the metal’s composition. Different metals have different properties, such as melting points and strength, which can affect their compatibility when welded together. Additionally, the intended application of the welded metal should be taken into account. The metal selection should be based on its ability to withstand the specific conditions of the application, such as temperature, pressure, and corrosion resistance. Other factors to consider include the required mechanical properties of the welded joint, such as tensile strength and ductility. By carefully considering these metal selection factors and having a deep understanding of metal compatibility, welders can ensure high-quality and durable welds.
Common Metal Combinations for Welding
I want to talk about the common metal combinations that are often used in welding. When it comes to welding, it is important to consider compatible metal alloys to ensure a strong and durable weld. Additionally, different metal combinations may require different welding techniques to achieve the desired results.
Compatible Metal Alloys
Pairing metals for welding involves identifying compatible metal alloys, ensuring their successful fusion during the welding process. The selection of compatible metal alloys is crucial to achieve a strong and durable weld joint. Different metal alloys have varying properties, such as melting temperature, thermal expansion coefficient, and mechanical strength. When welding, it is important to match metals with similar properties to ensure a proper bond and avoid issues like cracking or distortion.
In the welding industry, there are standards and guidelines that provide recommendations for compatible metal alloy combinations. These standards consider factors such as metallurgical compatibility, chemical composition, and mechanical properties. By following these industry standards, welders can ensure that the metal alloys they are using are compatible and will result in a high-quality weld.
To better understand the compatibility of metal alloys for welding, refer to the table below:
Metal Alloy 1 | Metal Alloy 2 |
---|---|
Stainless Steel | Carbon Steel |
Aluminum | Copper |
Titanium | Nickel |
Inconel | Hastelloy |
Brass | Bronze |
Strength and Durability
To ensure the strength and durability of a weld joint, it is essential to consider common metal combinations that are known for their compatibility and ability to withstand various welding conditions. When it comes to metal welding techniques, selecting the right combination of metals is crucial to achieve a strong and long-lasting weld. Different metals have varying physical properties, such as melting points, thermal conductivity, and tensile strength, which can greatly affect the quality of the weld joint. Therefore, a thorough pre-weld evaluation is of utmost importance. This evaluation involves assessing the properties of the metals to be welded, identifying any potential issues or incompatibilities, and determining the best welding method and filler material to use. By carefully considering these factors, one can ensure that the weld joint will possess the necessary strength and durability to withstand the intended application.
Welding Techniques Required
When considering the strength and durability of a weld joint, it is important to understand the welding techniques required for common metal combinations. Welding joint preparation and heat input control are two key factors that play a crucial role in achieving a successful weld. Properly preparing the joint by cleaning, beveling, and aligning the metal pieces ensures optimal fusion and reduces the risk of defects. Additionally, controlling the heat input during the welding process is essential to prevent distortion, cracking, and metal fatigue. By carefully monitoring the heat input, welders can maintain the desired mechanical properties of the joint and ensure its longevity. Table below provides a summary of common metal combinations for welding and the corresponding welding techniques required.
Metal Combination | Welding Technique | Joint Preparation | Heat Input Control |
---|---|---|---|
Steel to Steel | SMAW, MIG, TIG | Clean, Bevel | Preheat, Interpass Temp |
Aluminum to Aluminum | MIG, TIG | Clean, Bevel | Low Heat Input |
Steel to Aluminum | MIG, TIG | Clean, Bevel | Moderate Heat Input |
Stainless Steel to Stainless Steel | SMAW, TIG | Clean, Bevel | Low Heat Input |
Matching Metals for Strength and Durability
I match metals for welding based on their strength and durability. When it comes to metal compatibility, it is crucial to consider the specific metal selection factors that contribute to the overall strength and durability of the welded joint. One key factor to consider is the tensile strength of the metals being joined. Matching metals with similar tensile strengths ensures that the welded joint will be able to handle the desired load without failure. Additionally, the hardness of the metals should also be taken into account. Welding metals with similar hardness levels helps to prevent issues such as cracking or distortion during the welding process. By carefully considering these factors, I can ensure that the metals I choose for welding will result in strong and durable welded joints.
Potential Reactions and Issues in Metal Pairings
Considering the potential reactions and issues that can arise in metal pairings, it is important to anticipate any challenges that may affect the strength and durability of the welded joint. Welding different metals together can lead to several problems, including cracking, porosity, and reduced mechanical properties. These issues can arise due to differences in melting points, thermal expansion coefficients, and chemical reactions between the metals. For instance, when welding stainless steel to carbon steel, the difference in their thermal expansion coefficients can cause stress and cracking. Additionally, if two metals with significantly different melting points are welded together, the lower melting point metal can melt and weaken the joint. Therefore, it is crucial to carefully select compatible metal combinations and apply appropriate welding techniques to minimize the potential reactions and issues in metal welding.
Metal Combination | Potential Reactions | Issues |
---|---|---|
Stainless Steel + Carbon Steel | Stress and cracking | Reduced joint strength |
Aluminum + Copper | Intermetallic compound formation | Reduced mechanical properties |
Titanium + Steel | Brittle intermetallic formation | Increased susceptibility to corrosion |
Welding Techniques for Different Metal Combinations
To address the potential reactions and issues in metal pairings, it is essential to employ appropriate welding techniques for different combinations of metals. Welding challenges can arise when joining different metals due to differences in melting points, thermal expansion rates, and chemical reactions. One important aspect to consider is joint design, which plays a crucial role in ensuring a strong and durable weld. For instance, when welding dissimilar metals, it is crucial to create a joint design that allows for proper fusion and minimizes the formation of brittle intermetallic compounds. Additionally, selecting the right welding technique, such as TIG (Tungsten Inert Gas) or MIG (Metal Inert Gas), depending on the specific metal combination, can help overcome welding challenges and ensure a successful weld.
Importance of Pre-Weld Testing and Evaluation
When evaluating the compatibility of metal pairings, conducting pre-weld testing and evaluation is essential. Before beginning any welding project, it is crucial to perform a pre weld inspection to assess the condition of the materials and ensure they are suitable for welding. This inspection involves examining the surfaces for contaminants, such as oil, rust, or paint, which can negatively impact the weld quality. Additionally, material compatibility testing is necessary to determine if the metals can be successfully welded together without compromising their structural integrity. This testing involves checking the chemical composition and mechanical properties of the metals to ensure they are compatible and will form a strong weld joint. By conducting thorough pre-weld testing and evaluation, welders can prevent potential issues and ensure the success of their welding projects.
Tips for Successful Metal Match-Up in Welding
To ensure a successful metal match-up in welding, I rely on a meticulous analysis of the metals’ properties and compatibility. There are several factors to consider when selecting metals for welding, such as their composition, strength, and thermal conductivity. Compatibility is crucial to avoid potential reactions that could weaken the weld or compromise its integrity. One important factor to consider is the melting temperature of the metals being joined. If one metal has a significantly lower melting temperature than the other, it may result in uneven heating and potential structural issues. Additionally, it is essential to assess the reactivity of the metals to prevent any adverse reactions, such as the formation of brittle intermetallic compounds. By carefully considering these factors, I can ensure a successful metal match-up and create strong, durable welds.