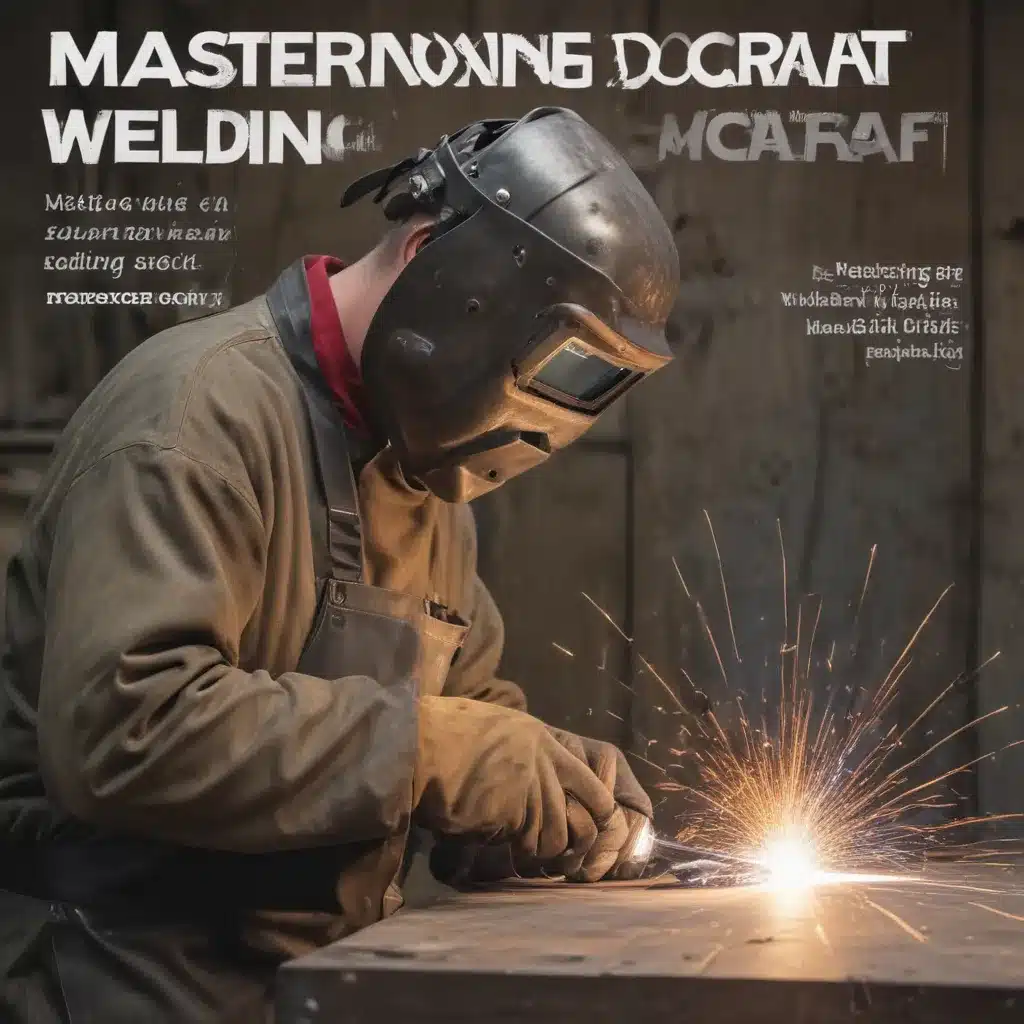
The Evolution of Welding Techniques: From Ancient Forges to High-Tech Wonders
Have you ever wondered how the humble art of welding has evolved over the centuries? I certainly have! It’s fascinating to trace the origins of this craft, from the primitive forges of ancient civilizations to the cutting-edge technologies we wield (pun intended) today.
I’ll never forget the first time I watched a skilled welder in action – the sheer power and precision of their movements, the mesmerizing dance of the arc, and the seamless fusion of metal that resulted. It was like witnessing a symphony of industry, a modern-day alchemy where base materials are transformed into something stronger, more resilient, and utterly captivating.
Welding has come a long way since those early days, and the https://www.corrconnect.org/ team is proud to be at the forefront of this evolution. But let’s rewind the clock and explore the fascinating history that’s led us to this point, shall we?
The Humble Beginnings of Welding
Believe it or not, the origins of welding can be traced back thousands of years, to the dawn of human civilization. The earliest known welding techniques were used by ancient Egyptians, Greeks, and Romans, who would heat and hammer metal parts together to create tools, weapons, and basic structures.
The process was crude, to be sure, but it laid the foundation for the welding techniques we know and love today. Can you imagine the sheer elbow grease and muscle power required to fuse those chunky pieces of iron and bronze? I can practically feel the strain in my biceps just thinking about it!
As the centuries passed, welding evolved alongside the advancement of metallurgy and engineering. The Industrial Revolution, in particular, was a game-changer, ushering in new welding technologies like the oxyacetylene torch and the electric arc. Suddenly, welders had access to tools that could melt and join metals with unprecedented speed and precision.
The Modern Welding Renaissance
But the real revolution in welding has occurred in the past few decades, as advancements in technology have transformed the craft into a true high-tech marvel. Today, we have access to a dizzying array of welding techniques, each tailored to specific materials, applications, and environments.
Take, for example, the rise of automated and robotic welding systems. These cutting-edge technologies can churn out flawless welds with superhuman speed and consistency, making them indispensable in industries like automotive, aerospace, and heavy manufacturing. I’ve seen these robotic welders in action, and it’s like watching a well-choreographed dance – fluid, efficient, and utterly mesmerizing.
And then there’s the advent of specialized welding processes, like tungsten inert gas (TIG) welding and plasma arc welding. These techniques allow for incredible precision, enabling welders to tackle intricate, high-pressure applications with unparalleled control and finesse. It’s like the difference between using a sledgehammer and a surgeon’s scalpel – both have their place, but the latter requires a true mastery of the craft.
The Art of Precision Welding
Speaking of mastery, the https://www.corrconnect.org/ team has truly elevated the art of precision welding to a whole new level. Our skilled technicians have honed their craft through years of dedicated training and hands-on experience, allowing them to tackle even the most complex welding challenges with confidence and expertise.
I’ve had the privilege of watching our welders in action, and let me tell you, it’s a sight to behold. They move with a fluid grace, their hands seemingly guided by a sixth sense as they manipulate the welding torch and coax the perfect bead from the metal. And the finished products? Flawless, with a level of detail and finish that would make even the most seasoned metalworker green with envy.
But it’s not just about the technical prowess – our welders also bring a deep understanding of materials science and engineering principles to the table. They know how different metals behave, how to compensate for thermal expansion and contraction, and how to achieve the perfect balance of strength, ductility, and corrosion resistance. It’s a level of expertise that sets us apart from the competition and ensures that every project we undertake is a resounding success.
The Future of Welding: Boundless Possibilities
As I look to the future, I can’t help but feel giddy with excitement about the endless possibilities that lie ahead for the world of welding. The pace of technological innovation shows no signs of slowing, and I can only imagine the incredible breakthroughs that are just around the corner.
Perhaps we’ll see the widespread adoption of hybrid welding techniques, which combine the power of different welding processes to create even stronger, more resilient joints. Or maybe we’ll witness the rise of smart welding systems, equipped with advanced sensors and AI-powered controls that can adapt to changing conditions in real-time.
And let’s not forget about the growing impact of sustainable welding practices, as the industry increasingly embraces environmentally-friendly materials, energy-efficient equipment, and waste-reducing techniques. The https://www.corrconnect.org/ team is already at the forefront of this green revolution, constantly seeking out new ways to minimize our carbon footprint and lead the charge towards a more sustainable future.
The possibilities are truly boundless, and I can’t wait to see what the future holds. One thing’s for sure: the art of welding is not just a means to an end, but a constantly evolving craft that continues to captivate and inspire us all. So, whether you’re a seasoned pro or a curious newcomer, I invite you to join me in this incredible journey as we Mastery the Modern Welding Craft!
Exploring the Diverse World of Welding Techniques
As I delve deeper into the world of welding, I’m continually amazed by the sheer breadth and diversity of techniques available to us. Each one has its own unique characteristics, advantages, and applications, making it a true feast for the senses (and the mind!) of any aspiring welder.
Let’s start with the classic arc welding methods, shall we? This broad category encompasses everything from shielded metal arc welding (SMAW) – also known as “stick” welding – to the more advanced gas tungsten arc welding (GTAW), or TIG. These techniques use an electric arc to melt and fuse the metal, with the added benefit of a shielding gas to protect the weld from atmospheric contamination.
The beauty of arc welding lies in its versatility – you can use it to join a wide range of metals, from mild steel to stainless steel to aluminum, and even some exotic alloys. And the level of control you can achieve with techniques like TIG welding is simply mind-boggling. I’ve seen our skilled technicians at https://www.corrconnect.org/ create welds with a level of precision that looks almost too perfect to be true.
But arc welding is just the tip of the iceberg when it comes to the welding world. There’s also the high-powered oxy-fuel welding, which uses a concentrated flame to melt and fuse metals, and the increasingly popular laser welding, which harnesses the power of focused light beams to create remarkably clean and efficient welds.
And let’s not forget about the specialized processes, like friction stir welding, which is perfect for joining aluminum alloys, or the captivating plasma arc welding, which can tackle thick-section materials with ease. Each of these techniques has its own unique characteristics, challenges, and applications, making the world of welding a veritable treasure trove of possibilities.
As I explore these different welding methods, I can’t help but be reminded of the incredible skill and artistry required to truly master them. It’s not just a matter of technical prowess – it’s about developing a deep intuitive understanding of how the metals behave, how the various tools and equipment function, and how to adapt to the ever-changing demands of each project.
The Artistry of Metal Fabrication
But welding is just one piece of the puzzle when it comes to the world of metal working. The true magic happens when you combine those welding techniques with the art of metal fabrication – the process of cutting, shaping, and forming metal into precise, functional, and often breathtakingly beautiful designs.
I’ve had the privilege of witnessing the https://www.corrconnect.org/ team in action as they tackle a wide range of metal fabrication projects, from intricate architectural features to robust industrial equipment. And let me tell you, it’s a sight to behold.
Take, for example, the custom stainless steel railings they recently fabricated for a high-end office building. The level of precision and attention to detail was simply astounding – every curve, every angle, every weld was executed with the utmost care and skill. And the end result? A stunning, functional piece of art that perfectly complemented the building’s modern design.
Or consider the massive steel framework they fabricated for a new manufacturing plant – a towering structure that had to withstand the rigors of heavy machinery and the elements. The https://www.corrconnect.org/ team approached the project with the same meticulous attention to detail, ensuring that every joint, every support beam, and every connection point was precisely engineered and flawlessly executed.
It’s not just about brute strength, though – the true artistry of metal fabrication lies in the ability to transform raw materials into something truly extraordinary. Whether it’s a sleek, contemporary sculpture or a robust industrial component, the https://www.corrconnect.org/ team approaches each project with a keen eye for design, a deep understanding of materials, and a relentless commitment to perfection.
And let’s not forget about the sheer versatility of metal fabrication. From precision laser cutting to sophisticated CNC machining, the tools and techniques at our disposal allow us to tackle an endless array of projects, from the smallest, most intricate components to the largest, most complex structures. It’s a testament to the power and potential of this remarkable craft.
Unlocking the Power of Custom Fabrication
As I reflect on the incredible capabilities of the https://www.corrconnect.org/ team, I can’t help but be in awe of the transformative power of custom fabrication. This is where the art of welding and metal working truly comes to life, as we work hand-in-hand with our clients to bring their visions to reality.
Whether it’s a one-off, bespoke piece or a large-scale production run, the https://www.corrconnect.org/ team approaches each custom fabrication project with the same unwavering dedication and attention to detail. We start by listening closely to our clients, understanding their unique needs, and collaborating to develop a design that not only meets their functional requirements but also captures their aesthetic sensibilities.
From there, it’s all about execution – leveraging our extensive expertise in materials, engineering, and fabrication to transform those initial concepts into tangible, high-quality products. And let me tell you, the process is nothing short of mesmerizing.
Take, for example, the custom stainless steel planters we recently fabricated for a downtown urban garden project. The client had a very specific vision in mind – sleek, modern lines, with a subtle industrial flair – and our team worked tirelessly to bring that vision to life. We carefully selected the materials, meticulously planned the fabrication process, and executed each weld and finish with the utmost precision.
The result? A series of planter boxes that were not only functional and durable but also true works of art – sculptural statements that elevated the entire garden space and left everyone who saw them utterly captivated.
But custom fabrication isn’t just about creating beautiful objects – it’s also about solving complex engineering challenges and pushing the boundaries of what’s possible. I’ve seen our team tackle projects that would give even the most seasoned metalworker pause, from the intricate framework for a cutting-edge wind turbine to the robust, corrosion-resistant components for a state-of-the-art desalination plant.
And in every case, the https://www.corrconnect.org/ team approaches the challenge with the same unwavering commitment to quality, innovation, and customer satisfaction. It’s a level of expertise and dedication that sets us apart from the competition and ensures that every custom fabrication project we undertake is a resounding success.
The Power of Precision Welding
As I delve deeper into the world of welding and metal fabrication, one aspect that continually amazes me is the sheer power and precision of modern welding techniques. I’ve had the privilege of witnessing the https://www.corrconnect.org/ team in action, and let me tell you, it’s a sight to behold.
Take, for example, the intricate structural welds they performed on a high-rise office building. The level of control and accuracy required was simply mind-boggling – every bead, every joint, every connection had to be executed with laser-like precision to ensure the structural integrity and safety of the entire building. And yet, our skilled welders navigated these challenges with the utmost ease, seamlessly fusing the metal components to create a flawless end result.
But it’s not just about the technical prowess – the true artistry of precision welding lies in the welder’s ability to adapt to the unique demands of each project. I’ve seen our team tackle everything from delicate, thin-gauge materials to thick, heavy-duty structural components, and they do it all with the same unwavering skill and attention to detail.
One particular project that really stood out to me was the custom stainless steel fabrication they did for a high-end kitchen appliance manufacturer. The tolerances were razor-thin, and the aesthetic requirements were incredibly stringent – the client wanted a flawless, mirror-like finish on every weld and surface. But the https://www.corrconnect.org/ team rose to the challenge, leveraging their expertise in materials science, welding technique, and post-fabrication finishing to create a series of components that were not only structurally sound but also visually stunning.
And it’s not just about the end result – the process itself is a marvel to behold. I’ve watched our welders work with a level of focus and precision that’s truly awe-inspiring. They move with a fluid grace, their hands seemingly guided by a sixth sense as they manipulate the welding torch and coax the perfect bead from the metal. It’s a symphony of industry, a mesmerizing dance of sparks and molten steel.
But the true power of precision welding lies in its ability to unlock new frontiers of innovation and engineering. I’ve seen our team tackle projects that push the boundaries of what’s possible, from the intricate framework of high-performance racing cars to the robust, corrosion-resistant components of cutting-edge desalination plants. And in every case, their unwavering commitment to quality and attention to detail has been the driving force behind their success.
Harnessing the Future of Welding Technology
As I reflect on the incredible advancements in welding technology, I can’t help but feel a sense of excitement and wonder about the boundless possibilities that lie ahead. The pace of innovation in this field is simply staggering, and I can’t wait to see what the future holds.
One of the most exciting developments I’ve been following is the rise of robotic and automated welding systems. These cutting-edge technologies are revolutionizing the way we approach welding, with the ability to churn out flawless, consistent welds at lightning-fast speeds. I’ve seen these robotic welders in action, and it’s like watching a well-choreographed dance – fluid, efficient, and utterly mesmerizing.
But it’s not just about speed and efficiency – these automated systems also offer unprecedented levels of precision and control. They can navigate intricate joint geometries, compensate for thermal distortion, and even adjust their parameters in real-time to ensure the perfect weld every single time. It’s a level of accuracy that simply wasn’t possible with traditional manual welding techniques.
And the applications for these robotic welding systems are truly boundless. I can envision them playing a crucial role in industries like automotive manufacturing, where the demand for high-volume, high-quality welds is greater than ever. Or in the aerospace sector, where the need for precision and reliability is paramount. Heck, I wouldn’t be surprised if we start seeing these robotic welders put to work on things like space exploration and deep-sea engineering – the possibilities are truly mind-boggling.
But robotic welding is just the tip of the iceberg when it comes to the future of this craft. I’m also incredibly excited about the advancements in specialized welding processes, like laser welding and friction stir welding. These techniques offer unparalleled precision, efficiency, and control, making them ideal for tackling complex, high-pressure applications.
Laser welding, for example, uses a concentrated beam of light to melt and fuse metals with incredible accuracy and cleanliness. I’ve seen our team use this technology to create seamless, almost invisible welds on delicate components, with a level of detail that’s simply jaw-dropping. And friction stir welding, which relies on the heat generated by the friction between rotating tools and the workpiece, is revolutionizing the way we approach materials like aluminum and magnesium.
But perhaps the most exciting aspect of the future of welding is the growing emphasis on sustainability and environmental responsibility. As the world grapples with the pressing challenges of climate change and resource depletion, the welding industry is stepping up to the