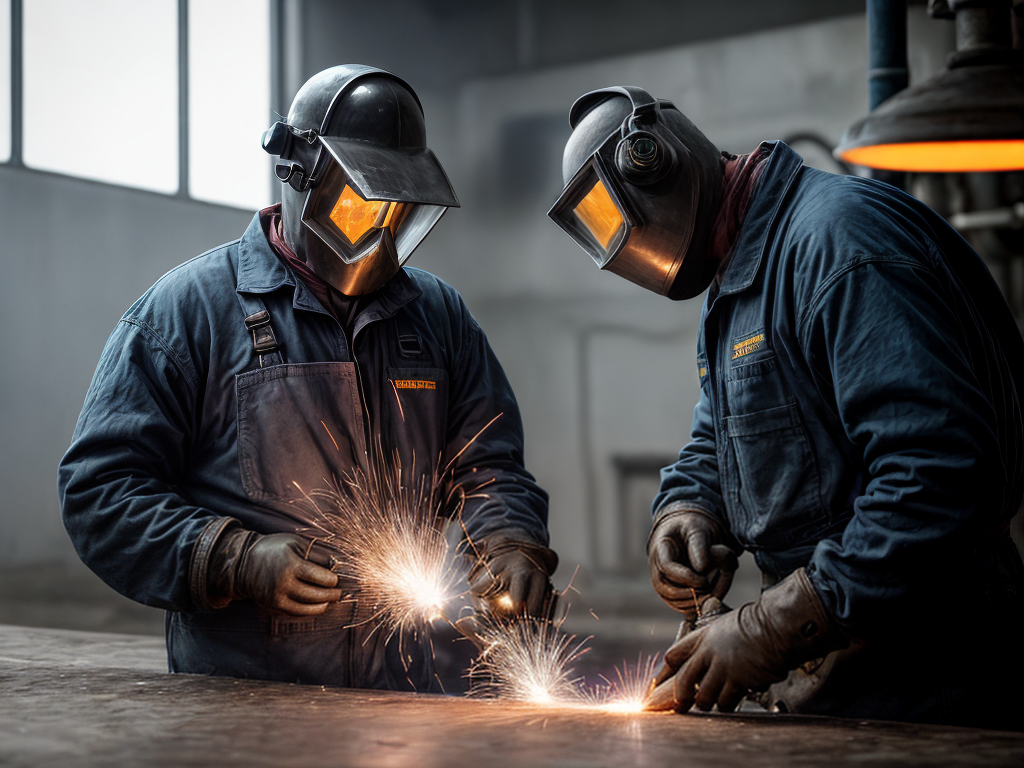
As someone who is passionate about welding and desires mastery in the craft, I understand the importance of achieving a clean weld. That’s why I am excited to share with you the essentials of mastering MIG welding. By combining the power of precision and technique, we can create welds that are not only strong and durable, but also aesthetically pleasing. In this guide, we will delve into the fundamentals of MIG welding, from selecting the right equipment to preparing your workpiece for welding. We will explore setting the correct voltage and wire feed speed, as well as mastering the proper welding technique. Additionally, we will discuss the crucial role of gas coverage in achieving a clean weld. Finally, we will provide essential tips for weld inspection and cleaning. Get ready to take your MIG welding skills to the next level!
Understanding MIG Welding Basics
I’ll explain the basic principles of MIG welding. When it comes to MIG welding techniques, there are a few key principles to keep in mind. First, ensure that your workpiece is clean and free from any contaminants that could compromise the weld. Next, select the appropriate wire size and shielding gas for the specific material you are welding. Maintaining proper wire tension and gun angle is crucial for achieving a clean and consistent weld. Troubleshooting common welding issues is also essential. If you experience problems such as wire feed issues, porosity, or spatter, check for proper grounding, gas flow, and wire speed. Understanding these basics will set you on the path to mastering MIG welding.
Choosing the Right Welding Equipment
When it comes to MIG welding, choosing the right equipment is crucial for achieving clean and precise welds. In this section, I will provide you with some equipment selection tips and recommendations for welding tools that can help you achieve your desired results. By using the right equipment, you can ensure that your welds are strong, durable, and aesthetically pleasing.
Equipment Selection Tips
To ensure optimal welding results, it is crucial to select the right welding equipment. The key to achieving this is by focusing on equipment maintenance and troubleshooting techniques. Proper maintenance of welding equipment is essential for its longevity and performance. Regularly inspecting and cleaning the equipment, as well as replacing worn-out parts, can prevent potential issues during welding. Additionally, familiarizing yourself with troubleshooting techniques can help you identify and resolve any problems that may arise during the welding process. This includes understanding common welding defects, such as porosity or lack of fusion, and knowing how to address them effectively. By prioritizing equipment maintenance and equipping yourself with troubleshooting skills, you can ensure smooth and successful welding operations.
Welding Tool Recommendations
Continuing with the importance of equipment selection, maintaining and troubleshooting the welding tools is crucial for achieving optimal results in MIG welding. Proper maintenance ensures that the tools are in good working condition and reduces the chances of any issues during the welding process. Regularly inspecting and cleaning the torch, wire feeder, and welder can prevent potential problems that may arise due to dirt, debris, or damage. Additionally, troubleshooting common welding tool issues is essential for minimizing downtime and maximizing productivity. Understanding how to identify and resolve issues such as wire feed problems, gas flow disruptions, or faulty connections can save valuable time and resources. By prioritizing welding tool maintenance and being equipped to troubleshoot common issues, welders can ensure consistent and high-quality welds.
Preparing Your Workpiece for Welding
Before starting the welding process, it is crucial for me as a MIG welder to thoroughly clean and properly secure my workpiece. Workpiece preparation is a critical step in achieving a clean and strong weld. To ensure a successful weld, I must first clean the surface of the workpiece. This involves removing any dirt, rust, paint, or other contaminants that may hinder the welding process. I can use a wire brush, sandpaper, or a grinder to clean the surface. It is important to remove all traces of contaminants to ensure proper fusion and prevent defects in the weld. Once the surface is clean, I must also properly secure the workpiece to prevent any movement or misalignment during the welding process. This can be done using clamps, vices, or welding jigs. Proper workpiece preparation lays the foundation for a high-quality weld and is essential for mastering MIG welding.
Setting the Correct Voltage and Wire Feed Speed
When it comes to MIG welding, setting the correct voltage and wire feed speed is crucial for achieving clean welds. Finding the right balance between the two is essential to ensure proper penetration and weld quality. By understanding the relationship between voltage and wire feed, welders can optimize their settings and produce high-quality welds with minimal spatter and distortion.
Voltage Vs. Wire Feed
Adjusting the voltage and wire feed speed is crucial for achieving a clean weld when mastering MIG welding. By understanding the relationship between voltage and wire feed, you can optimize your welding process and produce high-quality welds.
When it comes to voltage control, it is important to find the right balance. Too high of a voltage can lead to excessive heat, which can result in a lack of penetration and potential burn-through. On the other hand, too low of a voltage can lead to poor fusion and incomplete welds. It is essential to experiment and find the optimal voltage setting for your specific welding project.
Similarly, wire feeding techniques play a significant role in achieving a clean weld. The wire feed speed determines the amount of wire being deposited into the weld pool. Adjusting the wire feed speed allows you to control the size and shape of the weld bead. Too high of a wire feed speed can result in a large and uneven bead, while too low of a wire feed speed can lead to a narrow and discontinuous bead.
By mastering voltage control and wire feeding techniques, you can ensure consistent and clean welds. Remember to refer to the manufacturer’s guidelines and practice with different settings to find what works best for your welding needs.
Voltage Control | Wire Feeding Techniques |
---|---|
Find the optimal voltage setting for your specific project. | Adjust the wire feed speed to control the size and shape of the weld bead. |
Avoid excessive heat by not setting the voltage too high. | Ensure that the wire feed speed is not too high, resulting in an uneven bead. |
Prevent poor fusion by not setting the voltage too low. | Avoid setting the wire feed speed too low, resulting in a narrow and discontinuous bead. |
Optimal Settings for MIG
To set the correct voltage and wire feed speed for optimal MIG welding, I find it essential to refer to the manufacturer’s guidelines and experiment with different settings. The optimal wire thickness will depend on the material being welded and the desired weld strength. Thinner wires are suitable for thinner materials, while thicker wires are better for thicker materials. When troubleshooting common MIG welding problems, such as poor penetration or excessive spatter, adjusting the voltage and wire feed speed can often help. Increasing the voltage can improve penetration, while decreasing it can reduce spatter. Similarly, increasing the wire feed speed can increase deposition rate, while decreasing it can reduce heat input. By finding the right balance, we can achieve clean and strong welds.
Achieving Clean Welds
I find it crucial to set the correct voltage and wire feed speed in order to achieve clean welds. When it comes to MIG welding, minimizing splatter and preventing porosity are two key factors in producing high-quality welds. Splatter occurs when there is excessive heat or improper wire feed, leading to molten metal being scattered around the weld area. To minimize splatter, I recommend adjusting the voltage and wire feed speed to the appropriate settings for the specific materials being welded. Additionally, porosity, which is the formation of gas pockets within the weld, can be prevented by ensuring the correct voltage and wire feed speed. By setting these parameters correctly, we can achieve clean welds and enhance the overall quality of our work.
Mastering the Proper Technique for Welding
When learning how to master MIG welding, it is crucial to focus on developing the proper technique for achieving clean and precise welds. Proper welding techniques are essential for improving weld quality and ensuring the strength and durability of the finished product. To achieve mastery, one must pay attention to various factors such as the angle, speed, and distance of the weld. Maintaining a consistent angle and speed throughout the welding process helps to ensure even penetration and a uniform bead. Keeping the weld puddle small and moving it along smoothly also contributes to a clean weld. Additionally, proper wire feed and voltage settings are crucial for achieving the desired weld penetration and heat input. By honing these techniques, one can achieve mastery in MIG welding and consistently produce clean and precise welds.
Ensuring Adequate Gas Coverage for a Clean Weld
As I focus on mastering the proper technique for achieving clean and precise welds in MIG welding, it is crucial to ensure adequate gas coverage for a clean weld. Gas flow and the use of shielding gas play a vital role in creating a high-quality weld. Shielding gas serves to protect the molten weld pool from atmospheric contaminants, such as oxygen and nitrogen, which can cause defects and impurities in the weld. Proper gas flow ensures that the shielding gas effectively surrounds the weld area, preventing these contaminants from entering and compromising the integrity of the weld. It is essential to maintain a consistent and appropriate gas flow rate to achieve optimal shielding and produce clean welds. By prioritizing gas coverage, I can ensure the quality and durability of my MIG welds.
Essential Tips for Weld Inspection and Cleaning
To ensure the integrity and quality of my MIG welds, I must implement essential tips for inspecting and cleaning the welds. Weld inspection techniques are crucial in identifying any defects or imperfections in the welds. Visual inspection is the first step, where I carefully examine the weld for cracks, porosity, or lack of fusion. I also use non-destructive testing methods like dye penetrant or ultrasonic testing to detect any hidden flaws. Once the inspection is complete, cleaning the weld is essential to remove any contaminants or residue. Wire brushing or grinding can be used to remove surface impurities, while solvents or degreasers can be used to clean the weld zone. By following these weld inspection techniques and cleaning methods, I can ensure that my MIG welds are of the highest quality.