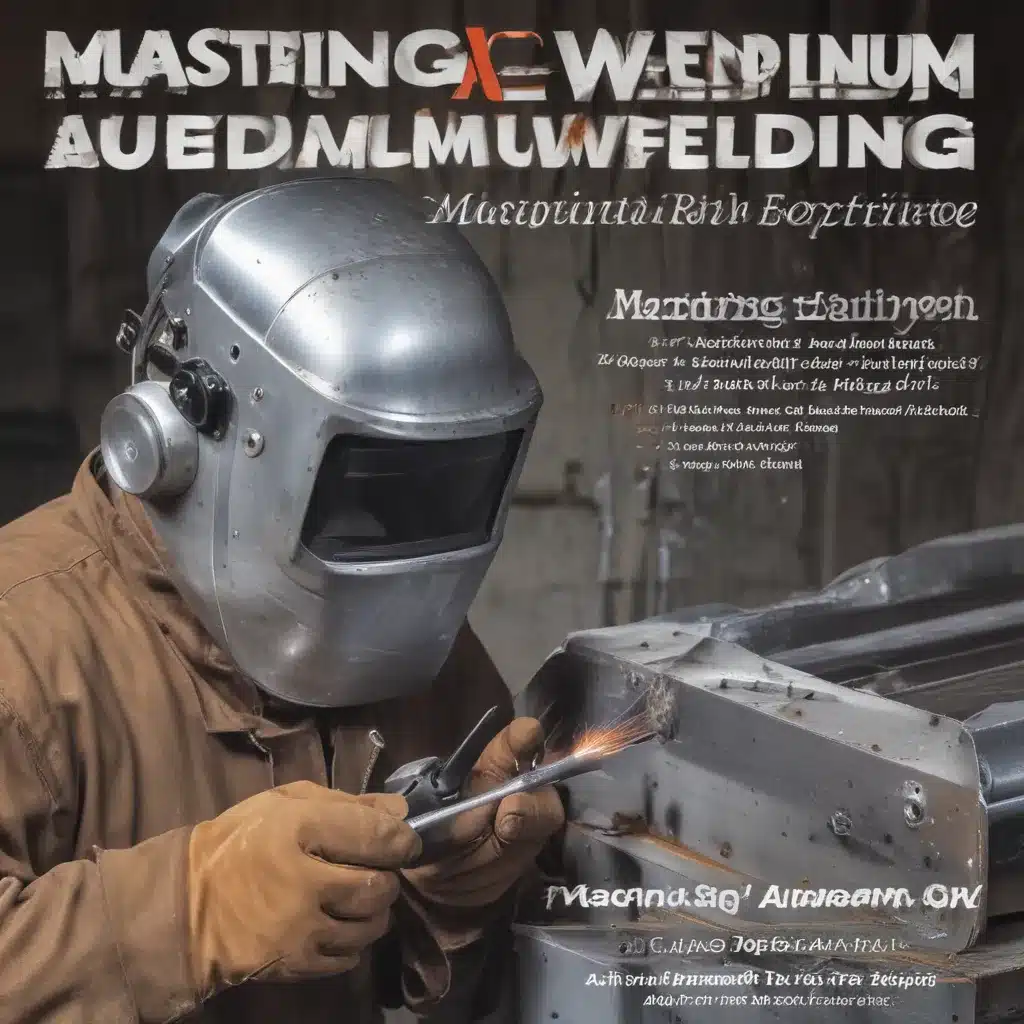
The Magic of Aluminum
Ahh, aluminum – the shiny, silvery metal that has captured the hearts and minds of welders and fabricators alike. As someone who’s been in the welding game for longer than I can remember, I’ve come to appreciate the unique challenges and joys of working with this versatile material.
You see, aluminum is like the chameleon of the metals – it can transform itself into all sorts of shapes and forms, from sleek automotive parts to sturdy industrial equipment. And let me tell you, mastering the art of aluminum welding is no easy feat. It’s like trying to wrangle a feisty alley cat – you’ve got to have the right tools, the right techniques, and the right mindset to get the job done.
But fear not, my friends! In this comprehensive guide, I’m going to take you on a deep dive into the world of aluminum welding, covering everything from the essential equipment you’ll need to the intricate settings and techniques that’ll turn you into a true aluminum welding virtuoso. So, strap in and get ready to unleash your inner metal-shaping wizard!
Aluminum Welding Equipment: The Essentials
First things first, let’s talk about the gear you’ll need to tackle those aluminum projects. Now, I know what you’re thinking – “Welding is welding, right? How different can it be?” Well, let me tell you, when it comes to aluminum, you’ve got to have the right tools for the job.
For starters, you’re going to need a TIG (Tungsten Inert Gas) welder. This bad boy is the crème de la crème of welding machines when it comes to aluminum. Unlike its MIG (Metal Inert Gas) counterpart, the TIG welder gives you precise control over the heat input, allowing you to finesse your way through those delicate aluminum seams without melting the whole darn thing.
But the welder is just the beginning. You’re also going to need a steady supply of pure argon gas to shield your weld pool and prevent oxidation. And let’s not forget the all-important tungsten electrodes – these little buggers come in various sizes and tip shapes, each one tailored for specific aluminum welding tasks.
Oh, and let’s not forget the personal protective equipment (PPE). When you’re dealing with molten metal, you’ve gotta keep yourself safe. That means flame-resistant clothing, sturdy gloves, and a high-quality welding helmet with a large viewing area. Trust me, you don’t want to be caught with your guard down when sparks are flying.
Now, I know what you’re thinking – “Whoa, that’s a lot of gear!” But trust me, once you’ve got all the right equipment in your arsenal, the aluminum welding world is your oyster. So, let’s dive a little deeper into the nitty-gritty of setting up your TIG welder for those aluminum masterpieces.
Dialing in the TIG Welder for Aluminum
Okay, so you’ve got your shiny new TIG welder, your argon gas, and your tungsten electrodes – now what? Well, my friends, it’s time to get that machine dialed in and ready to tackle some aluminum.
First and foremost, you’re going to want to make sure your TIG welder is set to the appropriate current for the thickness of your aluminum workpiece. As a general rule of thumb, you’ll want to use a lower amperage for thinner materials (around 100-150 amps) and a higher amperage for thicker pieces (up to 300 amps). But don’t just take my word for it – be sure to consult the manufacturer’s recommendations and do some test runs to find the sweet spot.
But the current settings are just the tip of the iceberg. You’ve also got to consider the gas flow rate, the electrode type and diameter, and the tungsten grind. Yep, that’s right – the way you sharpen that tungsten tip can make a world of difference in the quality of your welds.
For the gas flow rate, you’ll typically want to set it somewhere between 15-25 cubic feet per hour (CFH) for aluminum welding. Too little flow and you risk air getting into the weld pool, leading to porosity and other nasty defects. Too much, and you’ll end up with a turbulent, unstable arc that’s harder to control.
And when it comes to the tungsten electrode, you’ll generally want to go with a pure (green-tipped) or zirconiated (brown-tipped) variety. The pure tungsten is great for general-purpose welding, while the zirconiated version can handle higher amperage and is a bit more durable. As for the grind, a pointed tip is best for thin materials, while a balled tip works better for thicker workpieces.
Whew, that’s a lot of technical mumbo-jumbo, I know. But trust me, once you get the hang of dialing in your TIG welder for aluminum, it’ll become second nature. And the payoff? Smooth, consistent welds that’ll make your aluminum projects shine like the top of the Chrysler Building.
Mastering Aluminum Welding Techniques
Alright, now that we’ve covered the essential equipment and settings, it’s time to dive into the nitty-gritty of aluminum welding techniques. This is where the real magic happens, my friends.
First and foremost, you’re going to want to make sure your aluminum workpiece is clean, clean, clean. Any traces of oxidation, grease, or other contaminants can wreak havoc on your weld quality. So, be sure to give those surfaces a good scrubbing with a stainless steel brush or some aluminum-safe solvents.
Next up, you’ll want to get comfortable with the two-handed technique. Unlike steel welding, where you can often get away with one-handed work, aluminum requires a bit more finesse. You’ll want to use one hand to control the torch and the other to feed the filler metal into the weld pool. This allows you to precisely control the heat input and ensure even, consistent penetration.
But the real secret sauce to aluminum welding is all in the weld pool management. You see, aluminum has a much lower melting point than steel, and it also tends to be more reflective. This means you’ve got to be extra careful with your heat input and keep a close eye on that molten puddle.
One trick I like to use is the “skip-and-fill” method. Instead of trying to lay down one long, continuous bead, I’ll make a series of short, overlapping passes, allowing the weld pool to solidify briefly between each one. This helps prevent the aluminum from getting too hot and melting through the workpiece.
And let’s not forget about the importance of filler metal selection. When it comes to aluminum, you’ll want to use an alloy that’s compatible with your base material. The most common choices are ER4043 (silicon-based) and ER5356 (magnesium-based), each with their own unique properties and applications.
Oh, and one last tip – don’t be afraid to experiment and find what works best for you. Aluminum welding is as much an art as it is a science, and different techniques and setups may work better for different projects. So, have fun, get creative, and don’t be afraid to mess up a few times along the way. That’s all part of the journey, my friends!
Mastering Aluminum Welding: A Lifelong Pursuit
Whew, well there you have it – the ins and outs of mastering aluminum welding. From the essential equipment to the intricate techniques, we’ve covered a lot of ground. But you know what they say, “Mastering aluminum welding is a lifelong pursuit, not a destination.”
You see, the world of aluminum welding is always evolving, with new technologies, materials, and techniques constantly emerging. And as a true welding enthusiast, I can tell you that the journey is half the fun. There’s always something new to learn, some new challenge to overcome, and some new masterpiece to create.
So, whether you’re a seasoned pro or a curious newcomer, I encourage you to embrace the adventure. Dive in, experiment, and don’t be afraid to make a few mistakes along the way. Because, trust me, those “oops” moments are where the real magic happens. Before you know it, you’ll be churning out aluminum masterpieces like a pro, leaving your friends and colleagues in awe of your welding prowess.
And who knows, maybe one day you’ll even become the neighborhood aluminum welding guru, sharing your hard-earned knowledge with the next generation of metal-shaping superstars. The possibilities are endless, my friends, so what are you waiting for? Grab that TIG welder, fire it up, and let’s get to work!
Oh, and before I forget, if you’re ever in the market for some top-notch welding services, be sure to check out Corr Connect. They’ve got a team of aluminum welding experts who can tackle just about any project you can throw at them. Just sayin’!