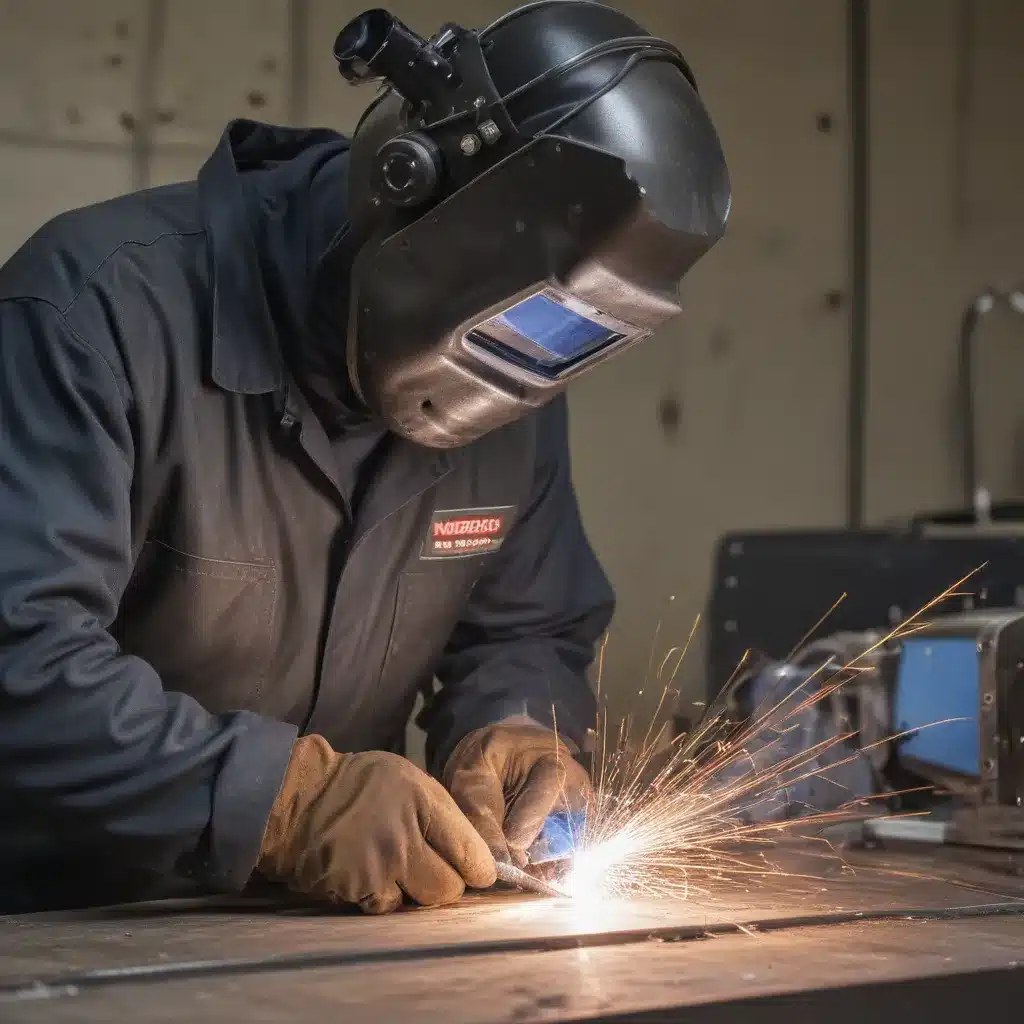
Exploring the Cutting Edge of Welding Techniques
As I sit here in my workshop, surrounded by the hum of welding torches and the dance of sparks, I can’t help but feel a sense of awe and excitement for the incredible advancements happening in the world of welding technology. Gone are the days of basic arc welding and clunky metal cutting – the industry is undergoing a revolution, and I’m thrilled to share with you some of the incredible innovations that are transforming the way we approach metal fabrication.
Let me start by painting a picture of the old-school welding world that I grew up in. Back in the day, if you wanted to join two pieces of metal, you’d better have a strong back and a steady hand. The process was laborious, time-consuming, and often produced uneven, sloppy results. And forget about precision – trying to cut intricate shapes out of metal was like trying to perform open-heart surgery with a blunt hatchet. It was a time-honored craft, to be sure, but it lacked the finesse and efficiency that modern fabricators demand.
But then something incredible happened. The mad scientists in the welding R&D labs started tinkering with new technologies, pushing the boundaries of what was possible. Suddenly, we had access to tools that could weld with laser-like precision, cut through thick steel like a hot knife through butter, and even 3D print entire metal structures from scratch. It was like the world of welding had been catapulted into the future.
Revolutionizing Arc Welding: The Power of Automation
One of the most exciting advancements in welding tech has been the rise of automated welding systems. Gone are the days of hunching over a workpiece, meticulously guiding a welding torch by hand. These days, we’ve got robotic welding arms that can execute complex welding patterns with unparalleled speed and consistency.
I remember the first time I saw one of these robotic welders in action – it was like watching a skilled dancer, gracefully moving back and forth, laying down perfect bead after perfect bead. And the best part? These machines can work tirelessly, 24/7, without the need for breaks or rest. It’s a game-changer for high-volume production, where consistency and efficiency are key.
But the benefits of automated welding go far beyond just speed and efficiency. These systems are also incredibly precise, capable of producing welds that are perfectly uniform in size, shape, and penetration. This is a game-changer for industries like aerospace and automotive, where even the slightest flaw in a weld can have catastrophic consequences.
And the technology just keeps getting better. We’re now seeing the integration of advanced sensors and computer vision systems that can actually inspect welds in real-time, automatically adjusting the welding parameters to ensure optimal quality. It’s like having a team of expert welders working around the clock, ensuring that every single weld is perfect.
Precision Cutting: The Rise of Cutting-Edge Technologies
Of course, welding is only half the battle – the other crucial component of metal fabrication is cutting. And in this realm, we’ve also seen some truly remarkable advancements in recent years.
Gone are the days of the old-school oxy-fuel torch, where you’d spend hours carefully guiding a hot, unwieldy flame through thick metal plates. These days, we’ve got high-tech plasma cutters and laser cutting systems that can slice through steel like a hot knife through butter.
I remember the first time I got my hands on a state-of-the-art plasma cutter – it was like wielding a lightsaber. The power and precision of these machines is truly mind-blowing. With the push of a button, I can cut intricate shapes and patterns with surgical accuracy, without the need for any manual guidance. And the speed – oh, the speed! I can cut through inch-thick steel in a matter of seconds, leaving behind a perfectly clean, square edge.
But the real game-changer has been the rise of laser cutting technology. These systems use highly focused beams of light to vaporize the metal, creating cuts that are so clean and precise that they almost look like they were machine-carved. I’ve seen these lasers cut through 1/2-inch thick steel like it was butter, with zero distortion or heat-affected zone. It’s truly a marvel of modern engineering.
And the applications for these cutting technologies are endless. From custom fabrication of complex metal parts to the creation of intricate sculptures and art pieces, the possibilities are limited only by our imagination. I can’t wait to see what the future holds for this incredible field.
Pushing the Boundaries of Metal Fabrication: 3D Printing and Beyond
But the innovations in welding and cutting technology are just the tip of the iceberg. In recent years, we’ve also witnessed the rise of additive manufacturing, or 3D printing, in the world of metal fabrication.
Imagine being able to design a complex metal part on a computer, and then have a machine literally print it out, layer by layer, in high-strength steel or titanium. It’s like something out of a science fiction movie, but it’s very much a reality. And the applications are mind-blowing.
I’ve seen 3D-printed metal parts used in everything from aerospace components to medical implants. The level of complexity and precision that these machines can achieve is truly staggering. Gone are the days of being limited by the constraints of traditional manufacturing processes – with 3D printing, the only limit is your imagination.
But the innovation doesn’t stop there. We’re also seeing the rise of hybrid manufacturing techniques, where traditional welding and cutting processes are combined with additive manufacturing to create truly unique and innovative metal structures.
Imagine a world where you could 3D print the basic framework of a complex metal part, and then use precision welding and cutting to add intricate details and reinforcements. It’s like taking the best of both worlds and combining them into something truly remarkable.
And the applications for this kind of hybrid manufacturing are endless. I’ve seen it used to create everything from custom motorcycle frames to one-of-a-kind architectural sculptures. The possibilities are limited only by our creativity and our willingness to push the boundaries of what’s possible.
The Future of Welding: A Glimpse into the Crystal Ball
As I sit here, surrounded by the cutting-edge tools of my trade, I can’t help but feel a sense of excitement and wonder for the future of welding and metal fabrication. The pace of innovation in this industry is truly astonishing, and I can only imagine what the next few years (or even decades) will bring.
Will we see the rise of fully autonomous welding systems, capable of operating without any human intervention? Will we witness the development of even more precise and efficient cutting technologies, that can slice through metal with the precision of a surgeon’s scalpel? And what about the potential of advanced materials like carbon fiber and titanium – how will they transform the way we approach metal fabrication?
The truth is, I don’t have all the answers. But what I do know is that the future of welding is brighter than ever. With the incredible advancements happening in this industry, I can’t wait to see what the next generation of metal fabricators will be able to create.
So, if you’re a fellow welding enthusiast, or someone who’s simply curious about the cutting edge of this fascinating field, I encourage you to keep your eyes peeled and your mind open. The future is coming, and it’s going to be one heck of a ride.
And if you’re in need of high-quality welding services, be sure to check out Corr Connect. They’re at the forefront of the welding revolution, using the latest technologies and techniques to deliver unparalleled results. Trust me, you won’t be disappointed.