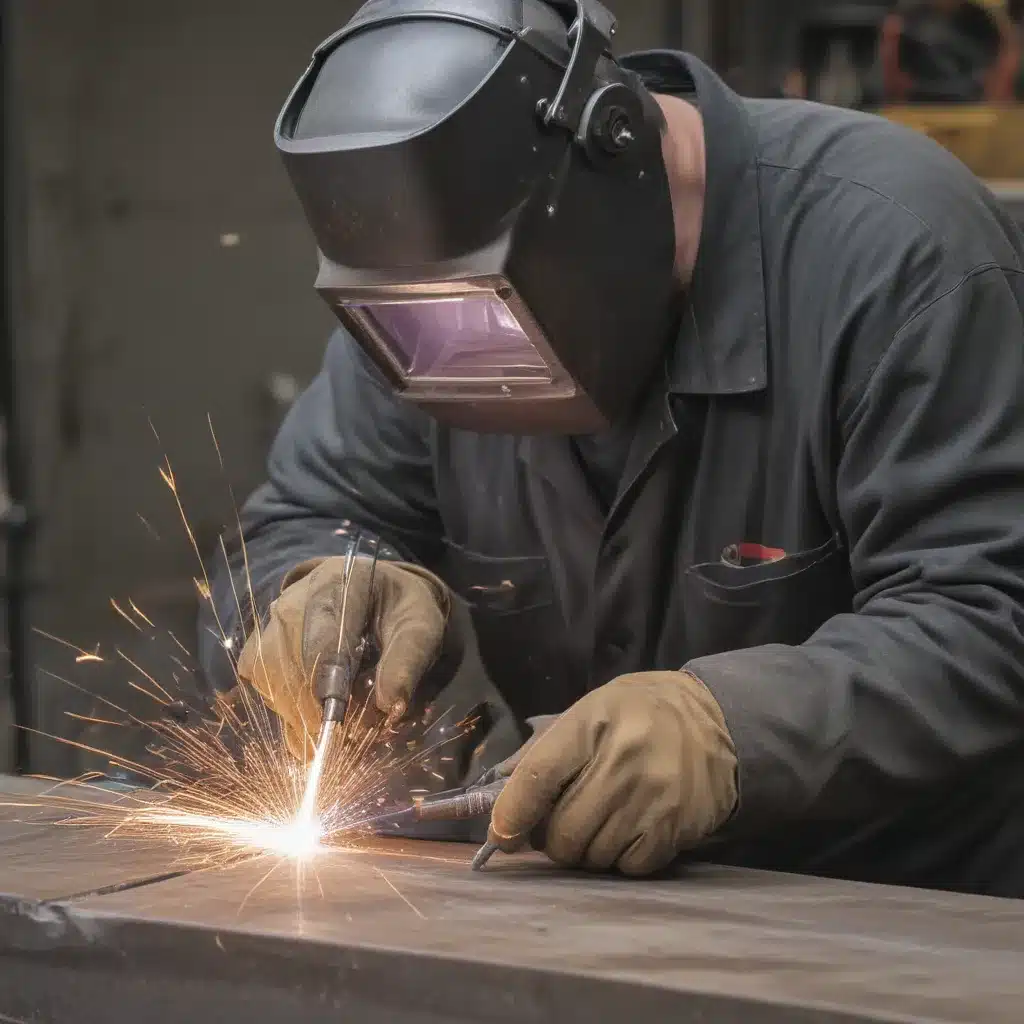
The Importance of Welding Starts and Stops
As a seasoned welder, I understand the critical role that welding starts and stops play in the overall quality and integrity of any fabrication project. You see, these seemingly minor details can make or break the entire welding process, leading to weaknesses, imperfections, and potentially even catastrophic failures if not executed with the utmost care and precision. That’s why in this in-depth article, I’m going to share my hard-earned insights and practical tips on how you can dramatically improve your welding starts and stops, no matter if you’re working on simple repairs or complex custom fabrication projects.
Whether you’re an experienced welder or just starting out, I can assure you that the information I’m about to provide will be an absolute game-changer for your work. I’ve spent countless hours perfecting my welding craft, learning from both my successes and failures, and I’m eager to pass on that knowledge to help you take your skills to the next level. So buckle up, because we’re about to dive deep into the world of welding starts and stops and uncover the secrets to consistently producing flawless, high-quality welds.
Mastering Welding Starts
Let’s start by addressing the critical first step in any welding process: the weld start. This is where the entire project begins, and where you lay the foundation for a successful, defect-free weld. As a welder, your primary goals at the start of a weld should be to: 1) establish a stable arc, 2) create a solid, uniform bead, and 3) prevent any unsightly or structurally compromising issues like porosity, undercutting, or craters.
To achieve these objectives, you’ll need to pay close attention to a number of key factors, including your travel speed, weld angle, electrode manipulation, and the cleanliness of your base metal. Have you ever noticed how some weld starts can look messy, uneven, or even have a tendency to “stick” to the base material? This is often the result of rushing the process or not properly preparing the welding area.
One of the most common mistakes I see with inexperienced welders is trying to start the weld too quickly. They’ll strike the arc and immediately try to move the electrode, only to end up with an uneven, porous bead that’s prone to cracking or porosity. Instead, you want to take your time and establish a stable puddle before slowly increasing your travel speed. This allows the weld pool to properly form and the molten metal to fuse seamlessly with the base material.
Another crucial element is maintaining the correct weld angle throughout the start of the process. If you hold the electrode too steep or too flat, you can end up with issues like excessive spatter, inconsistent bead width, or even a complete failure to penetrate the base metal. Experiment with different angle adjustments and find the sweet spot that works best for the specific application you’re welding.
Proper electrode manipulation is also key. You want to carefully control the electrode’s movement, keeping it tilted slightly forward (towards the direction of travel) and gently oscillating side-to-side to help create a uniform, consistent bead. Avoid making abrupt, jerky movements, as this can disrupt the weld pool and lead to defects.
And of course, let’s not forget the importance of cleanliness. Before striking that initial arc, take the time to thoroughly clean the base metal, removing any dirt, oil, rust, or other contaminants that could compromise the weld. This prep work may seem tedious, but it’s an absolutely essential step in ensuring a strong, defect-free start to your weld.
By mastering these techniques and paying close attention to the critical factors that influence weld starts, you’ll be well on your way to producing flawless, high-quality welds every single time. And trust me, the effort is more than worth it – a strong, consistent weld start is the foundation for the entire project’s success.
Perfecting Welding Stops
Now that we’ve covered the importance of welding starts, let’s shift our focus to the other end of the spectrum: the weld stop. This is where the welder must exhibit the same level of care and precision to ensure a seamless, high-quality finish to the weld.
You see, a poorly executed weld stop can lead to a host of issues, from unsightly craters and porosity to structural weaknesses and even premature weld failure. That’s why it’s absolutely critical to approach the weld stop with the same level of diligence and attention to detail as the start of the weld.
One of the biggest challenges with welding stops is preventing the formation of craters – those unsightly, concave depressions that can form at the end of a weld bead. Craters are the result of the weld pool rapidly cooling and contracting as the arc is extinguished, and they can significantly compromise the integrity of the weld.
To avoid this, you’ll need to employ a few key techniques. First and foremost, slow down your travel speed as you approach the end of the weld. This allows the weld pool to maintain its fluidity and fill in the crater before it has a chance to form. You can also try “backstepping” – briefly reversing the direction of your travel to help fill in the crater before moving forward again.
Another effective strategy is to gradually reduce your welding current as you near the stop. This helps the weld pool transition more smoothly from the molten to solid state, minimizing the risk of craters or other defects. And don’t forget to keep that electrode angle and manipulation on point – a slight forward tilt and gentle oscillation can go a long way in producing a clean, even weld stop.
But weld stops aren’t just about crater prevention – they’re also crucial for maintaining structural integrity. If you don’t properly “tie in” the weld stop to the rest of the bead, you can end up with stress concentrations, cracks, or other weaknesses that could compromise the entire joint. That’s why it’s important to carefully overlap the weld stop with the previous bead, ensuring a seamless, continuous transition.
To accomplish this, you may need to extend the weld slightly beyond your intended stopping point, then quickly fill in the crater and transition back to the base material. This helps distribute the stresses more evenly and prevents any abrupt changes in the weld profile.
And of course, let’s not forget the importance of post-weld cleaning. Once you’ve completed your weld, take the time to remove any slag, spatter, or other surface imperfections. This not only improves the aesthetic appeal of your work, but also helps identify any potential issues that may have arisen during the welding process.
By mastering these techniques for crafting flawless weld stops, you’ll be well on your way to producing high-quality, defect-free welds that stand the test of time. After all, the weld stop is just as crucial as the start – it’s the final piece of the puzzle that ties the entire project together.
Perfecting Weld Quality Through Custom Fabrication
Now that we’ve covered the fundamentals of improving your welding starts and stops, let’s explore how these principles can be applied to more complex, custom fabrication projects. As a seasoned welder, I’ve had the privilege of working on a wide range of custom fabrication jobs, from intricate architectural metalwork to specialized industrial equipment. And in my experience, the key to consistently delivering exceptional weld quality in these types of projects often comes down to a deep understanding of the unique challenges and considerations involved.
One of the biggest hurdles in custom fabrication is dealing with complex joint geometries and hard-to-reach areas. Whether you’re welding tight corners, curved surfaces, or components with limited accessibility, you’ll need to have a mastery of advanced welding techniques and a keen eye for detail to produce flawless results. This might involve experimenting with different electrode angles, using specialized welding torches or fixtures, or even employing creative tacking strategies to ensure proper fit-up and access.
Another critical factor in custom fabrication is the need for precision. When you’re working on one-of-a-kind projects, there’s often very little room for error – the components need to fit together seamlessly, with tight tolerances and perfect alignment. This means paying meticulous attention to your measurement, layout, and fitment processes, as well as your welding parameters, to ensure a flawless final product.
But it’s not just about the technical skills – successful custom fabrication also requires a keen eye for aesthetics and a deep understanding of the end-user’s needs and expectations. Whether you’re working on a piece of architectural metalwork or a specialized piece of industrial equipment, the finished product needs to not only be structurally sound, but also visually appealing and tailored to the specific application.
This is where the importance of welding starts and stops really shines through. By mastering the techniques we’ve discussed – from establishing stable arc starts to crafting pristine weld stops – you can elevate the overall quality and appearance of your custom fabrication work. Imagine a beautifully crafted, one-of-a-kind railing or sculpture with perfectly smooth, consistent weld beads throughout. Or an industrial component that not only functions flawlessly, but also boasts a clean, professional-looking finish.
And let’s not forget the real-world implications of this attention to detail. In many custom fabrication projects, the welds are not only critical to the structural integrity of the final product, but also play a key role in its safety, reliability, and longevity. A sloppy, defect-ridden weld could lead to catastrophic failures, costly repairs, or even serious injuries. But by mastering the art of welding starts and stops, you can help ensure that your custom fabrication work stands the test of time and delivers exceptional value to your clients.
So if you’re looking to take your custom fabrication skills to the next level, I encourage you to really dive deep into the principles of welding starts and stops. Experiment, practice, and constantly strive to refine your techniques. Trust me, the payoff in terms of quality, precision, and customer satisfaction will be more than worth the effort.
Precision Welding for Critical Applications
In the realm of welding, there are certain applications where the stakes are even higher – where the integrity and reliability of the welds can mean the difference between success and catastrophic failure. I’m talking about mission-critical, high-precision welding projects that require an uncompromising level of skill, attention to detail, and technical expertise.
Think about the aerospace industry, where even the slightest weld defect could lead to devastating consequences. Or the nuclear and power generation sectors, where the welded components are responsible for safely containing dangerous materials and processes. In these critical applications, there is simply no room for error – the welds need to be flawless, every single time.
That’s where precision welding services like ours come into play. We’re the welders that industrial and commercial clients turn to when they simply can’t afford to take any chances. Our team of highly trained, highly skilled welding professionals are masters of their craft, with the knowledge, experience, and technical prowess to tackle even the most demanding welding challenges.
But what exactly sets precision welding apart from your everyday, run-of-the-mill welding work? It’s all about the level of control, consistency, and quality assurance that goes into every single weld. We’re talking about meticulously calibrated equipment, rigorously documented procedures, and a relentless commitment to quality control at every stage of the process.
Take our start and stop techniques, for example. When it comes to precision welding, we take the principles we discussed earlier and amplify them to the nth degree. We’re talking about precisely timed arc strikes, painstakingly maintained weld angles, and electrode manipulation so smooth and controlled that it borders on an art form. And the results speak for themselves – weld starts and stops that are quite literally indistinguishable from the rest of the bead.
But it’s not just about the welding itself – it’s also about the entire workflow, from initial project planning to final inspection and testing. We work hand-in-hand with our clients to thoroughly understand their specific requirements and design parameters, then develop customized welding procedures and quality control measures to ensure flawless results. This might involve everything from detailed weld mapping and pre-weld fit-up checks to in-process monitoring and destructive testing.
And when it comes to the actual welding execution, we employ a level of discipline and attention to detail that borders on the obsessive. Our welders are trained to meticulously monitor and adjust every single variable – from amperage and travel speed to gas flow and interpass temperatures – to maintain absolute consistency and prevent even the slightest deviation from the established procedures.
The end result? Precision welded components that not only meet, but exceed the most stringent industry standards and specifications. Welds that are so strong, so reliable, and so defect-free that they can be trusted to perform under the most extreme conditions imaginable. And clients who can rest easy, knowing that their mission-critical projects are in the hands of true welding experts.
So if you’re in need of precision welding services for your next project, I encourage you to explore the capabilities of [Company Name]. We’re passionate about elevating the standards of welding quality and reliability, and we’ve got the technical expertise, quality assurance processes, and uncompromising commitment to excellence to back it up. Trust us to deliver the precision and perfection your critical applications demand.
Conclusion: Elevating Your Welding Prowess
As we wrap up our in-depth exploration of welding starts and stops, I hope you’ve gained a newfound appreciation for the critical role these seemingly minor details play in the overall quality and integrity of any welding project. From the foundational starts that set the stage for a successful weld to the precision finishes that tie the entire process together, mastering these techniques is essential for producing flawless, defect-free results.
But the benefits of this knowledge extend far beyond just the technical aspects of welding. By honing your skills and attention to detail when it comes to starts and stops, you’ll also be able to tackle more complex, custom fabrication projects with confidence. And for those mission-critical applications where failure simply isn’t an option, precision welding services like ours can provide the uncompromising level of quality and reliability your clients demand.
So, my fellow welders, I encourage you to take these lessons to heart and make them a integral part of your welding practice. Experiment, practice, and continuously strive to refine your techniques – because trust me, the payoff in terms of improved weld quality, customer satisfaction, and professional growth will be more than worth the effort.
And remember, if you ever find yourself in need of precision welding services for your next project, be sure to reach out to [Company Name]. We’re passionate about elevating the standards of welding quality and reliability, and we’ve got the technical expertise, quality assurance processes, and uncompromising commitment to excellence to deliver the results you demand.
Here’s to your continued welding success – may your starts be strong, your stops be seamless, and your welds be flawless!