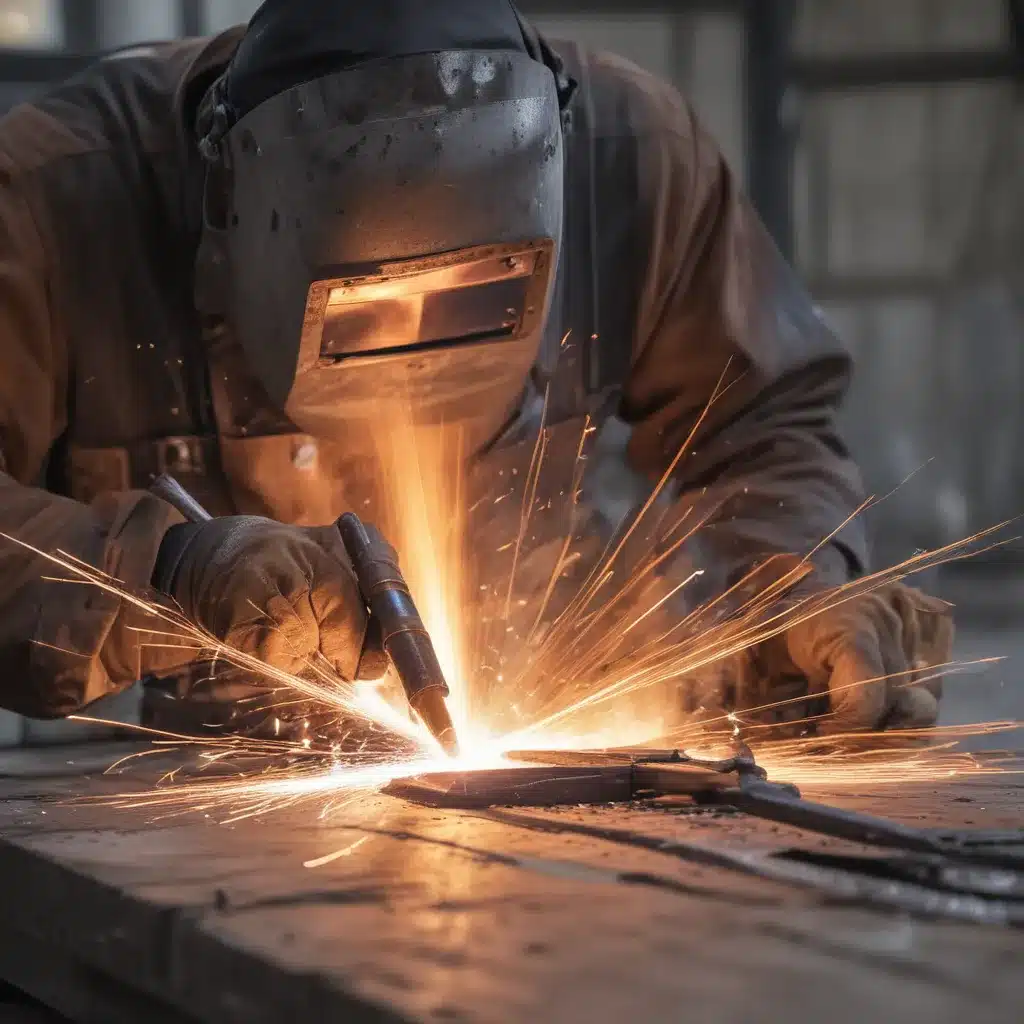
The Importance of Weld Fatigue Strength
The strength and resilience of welds are crucial considerations for any project involving metal fabrication. After all, the integrity of a weld can be the difference between a structure that stands the test of time and one that crumbles under pressure. As a welding services provider, I’ve seen firsthand the impact that weld fatigue can have on the longevity and safety of metalwork. That’s why I’m excited to delve into the topic of improving weld fatigue strength through post-weld heat treatment.
You see, weld fatigue is a complex and often misunderstood phenomenon. It’s the gradual weakening of a weld due to repeated stress, leading to cracks, fractures, and ultimately, failure. And the consequences of poor weld fatigue can be catastrophic – from bridge collapses to equipment malfunctions, the risks are simply too high to ignore.
But fear not, my friends! There is a solution, and it lies in the realm of post-weld heat treatment (PWHT). This process involves the controlled heating and cooling of the weld area, and it can dramatically improve the fatigue life of a joint. By carefully manipulating the microstructure of the metal, PWHT can reduce residual stresses, increase ductility, and enhance the overall strength of the weld.
Understanding Weld Fatigue
To fully appreciate the impact of post-weld heat treatment, we first need to understand the underlying mechanisms of weld fatigue. So, let’s dive in, shall we?
Weld fatigue is a complex phenomenon that arises from the cyclic loading and unloading of a welded joint. Imagine a bridge – the weight of passing vehicles, the sway of the structure, the changing weather conditions – all of these factors contribute to the constant stress and strain on the welds holding the bridge together.
Over time, these repeated stresses can cause microscopic cracks to form in the weld. As the cracks grow larger, they can eventually lead to catastrophic failure. And the problem is, these cracks aren’t always visible to the naked eye, making them even more insidious.
But it’s not just the cyclic loading that contributes to weld fatigue. The welding process itself can introduce residual stresses and microstructural defects that make the weld more susceptible to cracking. Things like improper welding technique, incorrect filler material, or even the order in which the welds are laid down can all impact the fatigue life of a joint.
The Role of Post-Weld Heat Treatment
Now that we understand the challenges posed by weld fatigue, let’s explore how post-weld heat treatment can be the solution we’re looking for.
Post-weld heat treatment is a process that involves carefully heating and cooling the weld area, often in a controlled environment like a furnace or oven. The goal is to manipulate the microstructure of the metal, reducing residual stresses and increasing the overall strength and ductility of the weld.
During PWHT, the weld area is heated to a specific temperature, typically between 600°C and 700°C, and then held at that temperature for a predetermined amount of time. This allows the metal to undergo a phase transformation, changing its internal structure and reducing the presence of defects and residual stresses.
After the holding period, the weld is slowly cooled, often at a rate of just a few degrees per minute. This controlled cooling process helps to further relieve internal stresses and ensure that the desired microstructural changes are achieved.
But the benefits of PWHT don’t stop there. By altering the weld’s microstructure, the process can also improve other important properties, such as corrosion resistance and impact toughness. This can be particularly valuable in applications where the welded structure is exposed to harsh environments or high-impact loads.
The Advantages of PWHT for Weld Fatigue
Now that we’ve covered the basics of post-weld heat treatment, let’s dive into the specific advantages it offers for improving weld fatigue strength.
One of the primary benefits of PWHT is its ability to reduce residual stresses in the weld area. As we discussed earlier, residual stresses can be a major contributor to weld fatigue, as they create areas of localized stress that are more prone to cracking. By heating and cooling the weld in a controlled manner, PWHT can help to relieve these internal stresses, making the weld more resistant to fatigue failure.
But the benefits of PWHT don’t stop there. The process can also improve the weld’s microstructure, increasing its overall ductility and toughness. This is particularly important in applications where the welded structure is subject to high levels of cyclic stress, as a more ductile weld is less likely to develop cracks and fail under repeated loading.
Moreover, PWHT can help to homogenize the weld’s microstructure, reducing the presence of defects and inclusions that can act as stress concentrators and weaken the weld. By creating a more uniform and consistent microstructure, PWHT can improve the overall fatigue life of the weld.
And let’s not forget the impact that PWHT can have on corrosion resistance. By altering the weld’s microstructure, the process can make the weld less susceptible to corrosion, which can be a major contributor to fatigue failure in certain environments.
Real-World Examples of PWHT Improving Weld Fatigue
Still not convinced of the power of post-weld heat treatment? Let me share a few real-world examples that showcase the dramatic impact PWHT can have on weld fatigue strength.
Take the case of a major bridge construction project in a coastal region. The welds holding the bridge’s steel girders together were subjected to constant exposure to saltwater, high winds, and heavy traffic loads – a perfect storm for weld fatigue. But by incorporating a rigorous PWHT regimen into the fabrication process, the project team was able to significantly enhance the fatigue life of the welds, ensuring the bridge’s long-term structural integrity.
Or consider the experience of a leading manufacturer of heavy machinery. Their products were subjected to intense vibrations and shock loads, putting tremendous stress on the welds. Conventional welding techniques simply weren’t cutting it, with the machines experiencing premature weld failures that threatened the company’s reputation and bottom line. That is, until they started implementing PWHT – the result? A dramatic increase in weld fatigue life, allowing their machines to stand up to the toughest conditions.
And let’s not forget the aerospace industry, where the stakes are even higher. When building critical components for aircraft and spacecraft, every weld needs to be bulletproof. That’s why leading aerospace manufacturers have long relied on PWHT to ensure that their welds can withstand the rigors of high-speed flight, extreme temperatures, and intense vibrations. The results speak for themselves – a significant reduction in weld-related failures and a boost in the overall reliability of their products.
Optimizing PWHT for Improved Weld Fatigue
Of course, simply performing post-weld heat treatment isn’t a magic bullet. To truly reap the benefits of PWHT for weld fatigue, it’s essential to optimize the process and ensure that it’s tailored to the specific application and materials involved.
That’s where the expertise of a trusted welding services provider like Corrconnect comes into play. Our team of seasoned welding professionals has a deep understanding of the science behind PWHT and the factors that can influence its effectiveness.
For example, we know that the specific temperature and duration of the heat treatment can have a significant impact on the weld’s microstructure and fatigue life. Too little heat, and the residual stresses may not be adequately relieved. Too much heat, and you risk compromising the weld’s overall strength and ductility.
That’s why we take a holistic approach to PWHT, carefully considering factors like the base metal composition, joint design, and expected service conditions. By combining our technical expertise with advanced simulation and testing capabilities, we can develop a customized PWHT regimen that optimizes weld fatigue strength for each unique application.
And it’s not just about the PWHT process itself. We also understand the importance of proper pre-weld preparation and welding technique in laying the foundation for a durable, fatigue-resistant joint. By integrating PWHT into a comprehensive welding strategy, we can help our clients achieve the highest levels of weld quality and performance.
Conclusion: Embracing the Power of PWHT
As a welding services provider, I’ve seen firsthand the transformative power of post-weld heat treatment in improving weld fatigue strength. From bridges and heavy machinery to aerospace components, PWHT has proven to be an invaluable tool in the fight against weld fatigue.
By understanding the underlying mechanisms of weld fatigue and the ways in which PWHT can mitigate these challenges, we can unlock new levels of reliability, safety, and performance in metalwork. Whether you’re working on a critical infrastructure project, developing cutting-edge industrial equipment, or pushing the boundaries of aerospace engineering, PWHT can be the key to ensuring that your welds stand the test of time.
So, if you’re looking to take your welding services to the next level, I encourage you to explore the benefits of post-weld heat treatment. Embrace the power of this transformative process, and unlock a new era of weld fatigue resilience. Your projects, your clients, and your bottom line will all thank you.