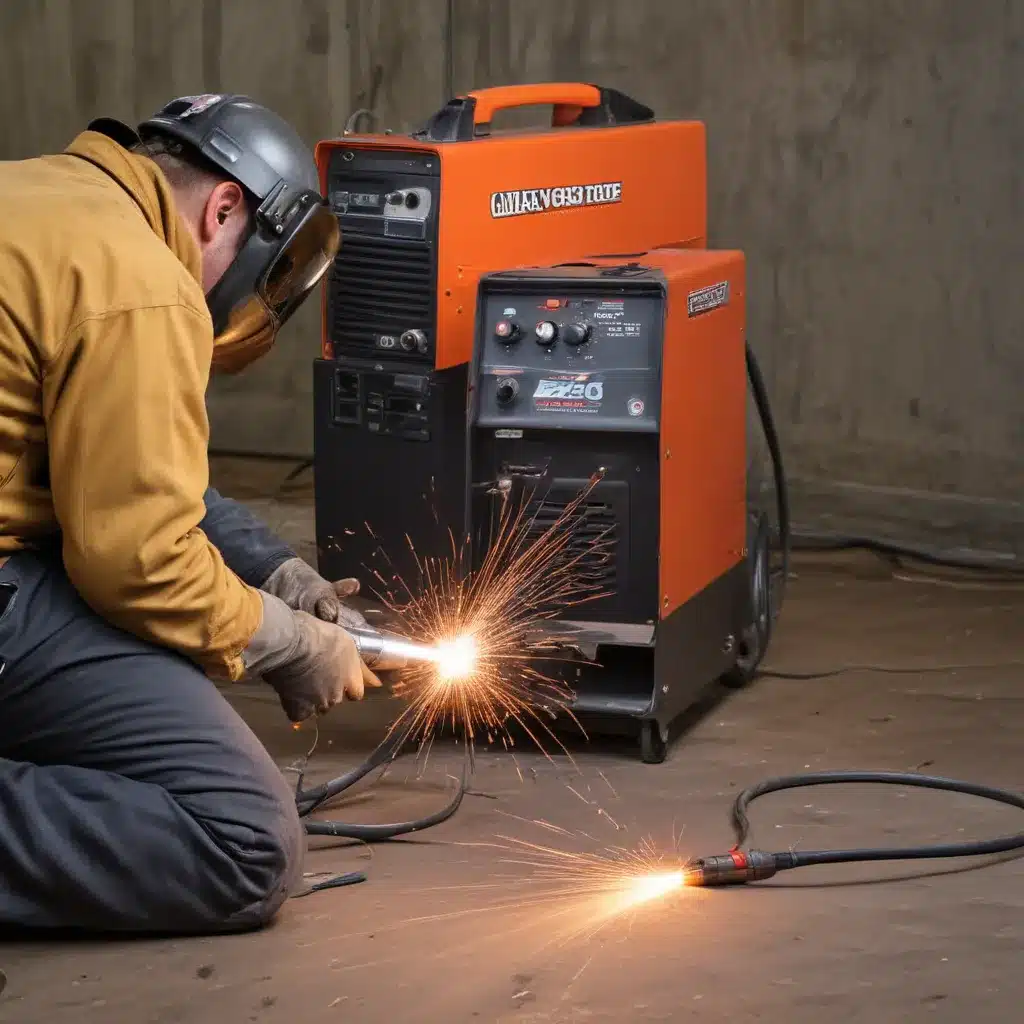
Introduction: Mastering the Art of Flux Core Welding
Ah, the mighty flux core welder! This trusty sidekick has been the backbone of heavy-duty welding operations for decades, and for good reason. With its ability to tackle thick, rugged materials with ease, the flux core welder is the go-to choice for industrial applications, construction projects, and beyond. But fear not, my fellow welding enthusiasts – mastering this powerful tool is well within your reach.
In this comprehensive guide, I’ll take you on a journey through the world of flux core welding, exploring its inner workings, the advantages it offers, and the techniques you need to wield it like a seasoned pro. Whether you’re a seasoned welder looking to expand your skillset or a newcomer eager to dive into the world of heavy-duty welding, this article has got you covered.
So, let’s get started, shall we? Grab your safety gear, fire up that flux core welder, and let’s dive in!
Understanding the Flux Core Welding Process
To truly harness the power of a flux core welder, we first need to understand the underlying process. Unlike traditional stick welding or MIG welding, the flux core welder utilizes a continuously fed wire electrode that is coated with a flux material. This flux, my friends, is the secret sauce that sets flux core welding apart.
When the wire is fed through the welding gun and comes into contact with the workpiece, an electric arc is generated, melting both the wire and the surrounding metal. The flux coating then begins to decompose, releasing a shielding gas that protects the molten weld pool from atmospheric contaminants. This gas shielding, coupled with the self-cleaning properties of the flux, allows for a strong, high-quality weld even in less-than-ideal conditions.
But the benefits of flux core welding don’t stop there. The flux coating also helps to stabilize the arc, improving overall weld quality and reducing the risk of porosity or other defects. And let’s not forget the versatility – flux core welders can tackle a wide range of materials, from mild steel to stainless steel and even some forms of aluminum.
Advantages of Flux Core Welding
Now that we’ve got the basics down, let’s dive into the key advantages that make flux core welding the go-to choice for heavy-duty applications. Strap in, my friends, because the list is mighty impressive!
Penetration and Strength: One of the primary advantages of flux core welding is its exceptional ability to achieve deep, penetrating welds. The high heat input and self-shielding properties of the flux core wire allow for the creation of robust, structurally sound joints, even on thick, heavy-duty materials.
Portability and Versatility: Flux core welders are typically more portable and self-contained than their MIG or TIG counterparts, making them ideal for on-site work or in applications where access to a dedicated gas supply is limited. And with the ability to weld a wide range of metals, the flux core welder is a true jack-of-all-trades in the welding world.
Ease of Use: Flux core welding is often considered one of the more user-friendly welding processes, particularly for beginners. The continuous wire feed and self-shielding properties of the flux core wire can help to reduce the learning curve, allowing even novice welders to produce high-quality welds with relative ease.
All-Position Welding: One of the standout features of flux core welding is its ability to perform all-position welds. Whether you’re tackling a vertical, overhead, or even a tricky horizontal joint, the flux core welder has got your back, making it an invaluable tool for complex fabrication projects.
Reduced Cleanup: The self-cleaning properties of the flux core wire help to minimize the amount of post-weld cleanup required, saving you time and effort on the job site. Say goodbye to tedious slag removal and hello to a smoother, more efficient welding process.
Clearly, the flux core welder is a force to be reckoned with when it comes to heavy-duty applications. But the real question is, how do you harness this power to its full potential? Let’s dive into the techniques and best practices that will have you welding like a pro in no time.
Mastering Flux Core Welding Techniques
Alright, let’s get down to the nitty-gritty of flux core welding. Like any skilled craft, mastering this technique requires practice, patience, and a keen eye for detail. But fear not, my fellow welding enthusiasts – I’ll be here to guide you every step of the way.
Proper Setup and Preparation: Before you even strike that arc, it’s crucial to ensure your flux core welder is properly set up and your workpiece is prepped for the task at hand. This includes selecting the right wire diameter and gas flow rate, as well as thoroughly cleaning the metal surfaces to remove any contaminants.
Controlling the Welding Speed and Angle: One of the keys to achieving consistently high-quality flux core welds is maintaining the proper welding speed and angle. Move too fast, and you’ll risk incomplete fusion and insufficient penetration. Too slow, and you might end up with excessive weld bead buildup and potential distortion. Finding that sweet spot takes practice, but the payoff is well worth it.
Maintaining the Proper Weld Pool: The weld pool – that molten puddle of metal at the point of the arc – is the heart of the flux core welding process. Keeping that pool the right size and shape is crucial for producing a strong, uniform weld. Pay close attention to the pool’s size and fluidity, and be ready to adjust your technique on the fly to keep it just right.
Mastering Weave Patterns: Flux core welding also allows for the use of various weave patterns to help control the weld bead shape and overall appearance. From the simple stringer bead to more complex weave techniques, experiment with different approaches to find the one that works best for your specific application.
Dealing with Porosity and Spatter: No welding process is perfect, and flux core welding is no exception. One common challenge you may face is the dreaded porosity – those pesky gas pockets that can weaken the weld. Additionally, you’ll need to contend with spatter, the small molten metal droplets that can get scattered around the work area. Proper technique, shielding gas selection, and post-weld cleanup can help minimize these issues.
Mastering these techniques takes time and practice, but the payoff is well worth it. Imagine the satisfaction of producing flawless, high-strength welds time and time again – it’s the stuff that welding dreams are made of!
Applications and Use Cases for Flux Core Welding
Now that we’ve covered the basics of flux core welding and the techniques required to become a master, let’s take a look at some of the real-world applications where this versatile process truly shines.
Heavy Equipment and Machinery Fabrication: Flux core welding is a go-to choice for the fabrication and repair of heavy equipment like construction machinery, agricultural implements, and industrial vehicles. Its ability to weld thick materials with ease and produce strong, structurally sound joints makes it an invaluable tool in this industry.
Structural Steel Framing: In the world of construction, flux core welding is a staple for fabricating and erecting structural steel frames for buildings, bridges, and other large-scale projects. The deep penetration and all-position welding capabilities of the flux core welder make it an essential part of the modern construction toolkit.
Automotive and Transportation Fabrication: From custom car frames to heavy-duty truck bodies, flux core welding has a prominent role to play in the transportation industry. Its versatility and portability make it a perfect fit for on-site repairs, modifications, and custom fabrication work.
Shipbuilding and Marine Applications: The marine industry, with its unique welding challenges, has long relied on the dependability of flux core welding. Whether it’s fabricating hulls, decks, or other critical components, the flux core welder is a trusted ally in keeping ships and boats seaworthy.
Trailer and Recreational Vehicle Manufacturing: The rugged nature of flux core welds makes it an ideal choice for the fabrication of trailers, campers, and other recreational vehicles. From the frame to the body panels, this welding process helps ensure these machines can withstand the rigors of the open road.
The list goes on and on, my friends. Wherever heavy-duty welding is required, you can bet the flux core welder will be there, ready to tackle the job with power, precision, and unparalleled versatility.
Safety Considerations for Flux Core Welding
Now, before we wrap up this journey through the world of flux core welding, let’s take a moment to address a topic that’s critical to your well-being: safety. After all, what good is mastering this powerful technique if you’re not doing it in a responsible and safe manner?
Personal Protective Equipment (PPE): Proper PPE is an absolute must when wielding a flux core welder. We’re talking heavy-duty gloves, a sturdy welding jacket, and – of course – a top-notch welding helmet with the right lens shade. Neglecting these essential safety measures is a recipe for disaster, my friends.
Ventilation and Fume Control: Flux core welding, like many welding processes, generates a fair amount of fumes and particulates. Ensuring adequate ventilation and the use of proper fume extraction systems is crucial to protect your respiratory health. Trust me, you don’t want to be breathing in those nasty welding fumes.
Electrical Safety: Flux core welders, like all welding equipment, operate on high-voltage electricity. Familiarize yourself with proper grounding techniques, avoid damp or wet work areas, and always be mindful of the potential for electric shock. Safety first, my friends!
Fire Prevention: The intense heat and sparks generated by flux core welding can pose a serious fire risk, especially in areas with flammable materials nearby. Always have a fire extinguisher on hand, and be vigilant about clearing the work area of any potential fire hazards.
Training and Certification: Last but not least, don’t forget the importance of proper training and certification. Flux core welding, while a powerful tool, requires a certain level of skill and knowledge to perform safely and effectively. Invest in the necessary training and stay up-to-date on industry best practices.
By keeping these safety considerations top of mind, you can harness the power of flux core welding with confidence and peace of mind. Remember, a little caution goes a long way in this line of work.
Conclusion: Flux Core Welding – Your Ticket to Heavy-Duty Success
Well, there you have it, my fellow welding enthusiasts – a comprehensive guide to mastering the art of flux core welding for heavy-duty applications. From understanding the underlying process to mastering the key techniques, we’ve covered it all.
Flux core welding is a true powerhouse in the world of industrial and fabrication work, offering unparalleled strength, versatility, and ease of use. Whether you’re tackling a massive construction project or repairing a critical piece of heavy machinery, this welding process has got your back.
So, what are you waiting for? Grab your gear, fire up that flux core welder, and let’s get to work! With the knowledge and skills you’ve gained from this guide, the sky’s the limit. Happy welding, my friends!
And if you’re in need of top-notch welding services for your next heavy-duty project, be sure to check out the experts at corrconnect.org. Their team of skilled welders is ready to tackle any challenge, big or small, with the precision and expertise you can count on.