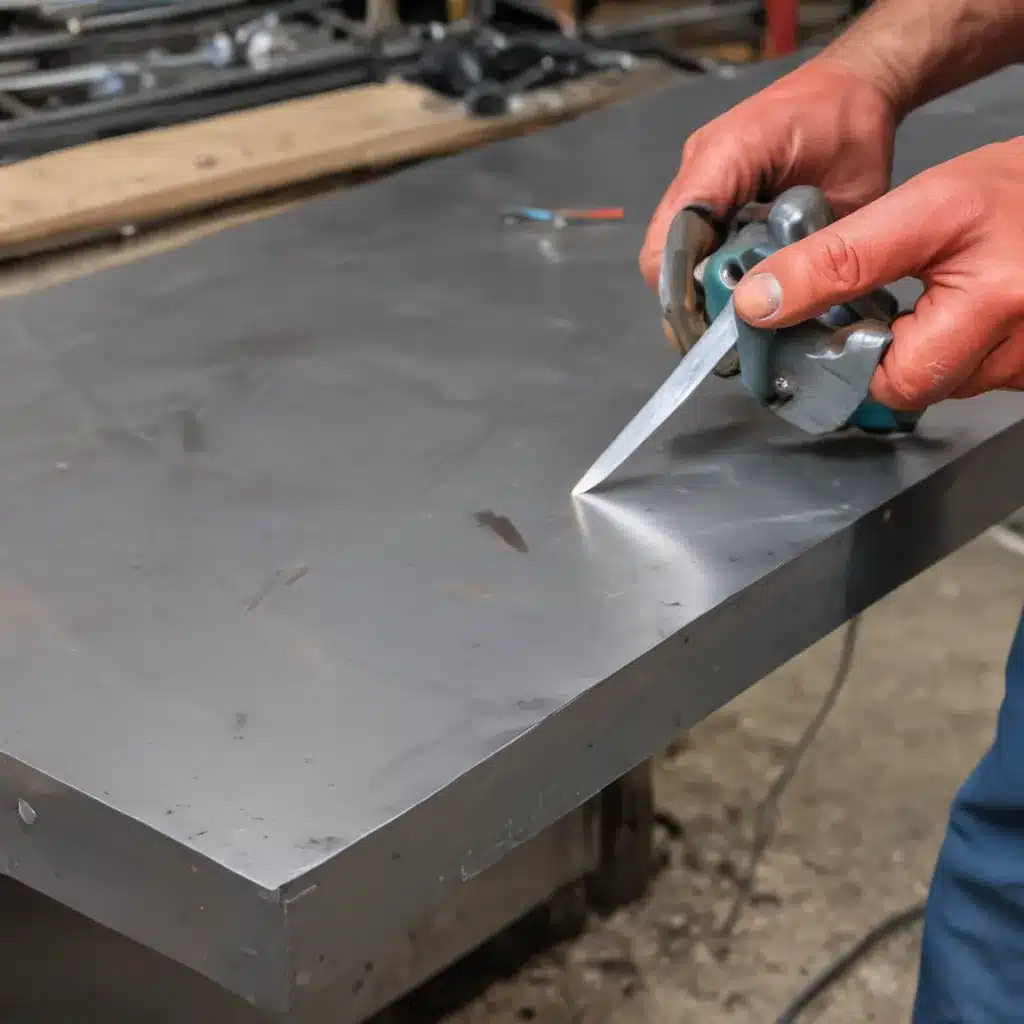
Unlocking the Secrets of Welding Sheet Metal
Have you ever looked at a shiny, seamless metal surface and wondered how on earth it got that way? Well, my friends, the answer lies in the art of welding sheet metal. And let me tell you, it’s not as daunting as it may seem. In fact, with the right tools and a little bit of know-how, you can become a sheet metal welding pro in no time!
Let me start by telling you a little story. When I was just a young, wide-eyed apprentice, I remember watching our resident welding wizard work his magic on a tricky sheet metal project. The way he effortlessly moved the welding torch, the sparks flying, and the metal fusing together – it was like a ballet of pure precision. I was mesmerized, and from that moment on, I knew I had to learn the secrets of welding sheet metal.
Fast forward a few years, and I can proudly say that I’ve mastered the art of sheet metal welding. And let me tell you, it’s not as hard as you might think. With the right tools and a little bit of practice, anyone can become a sheet metal welding pro. So, let’s dive in and explore the ins and outs of this fascinating craft.
Understanding the Fundamentals of Sheet Metal Welding
First and foremost, let’s talk about the basics of sheet metal welding. What exactly is sheet metal, you ask? Well, it’s a thin, flat piece of metal that’s been rolled or pressed into a uniform thickness. It’s commonly used in a wide range of industries, from automotive to construction to, of course, welding.
Now, when it comes to welding sheet metal, there are a few key things to keep in mind. Firstly, the thin nature of the material means that you need to be extra careful with your heat input. Too much heat, and you’ll end up with a warped, distorted mess. Too little, and you won’t get a proper weld. It’s all about finding that sweet spot.
Another important factor is the type of welding process you choose. For sheet metal, the most common options are MIG (Metal Inert Gas) welding and TIG (Tungsten Inert Gas) welding. Both have their own advantages and disadvantages, and the best choice will depend on the specific project you’re working on.
Choosing the Right Tools for the Job
Alright, now that we’ve got the basics down, let’s talk about the tools you’ll need to get the job done. As I mentioned, you don’t need a fancy, high-tech setup to weld sheet metal. In fact, you can get the job done with some pretty simple, affordable tools.
First and foremost, you’ll need a welding machine. Now, I know what you’re thinking – “But I thought you said this was simple!” Don’t worry, my friend. There are plenty of entry-level welding machines out there that are perfect for sheet metal work. Look for something that’s easy to use, with intuitive controls and a compact design.
Next up, you’ll need a welding torch. This is where the magic happens, folks. Again, there are plenty of user-friendly options out there, from handheld MIG guns to TIG torches. Just make sure to choose one that’s compatible with your welding machine and the thickness of the sheet metal you’ll be working with.
But wait, there’s more! You’ll also need a few other essential items, like a wire brush for cleaning the metal, a clamp to hold the workpiece in place, and some protective gear (because safety first, am I right?). Oh, and don’t forget the all-important welding gloves – trust me, you don’t want to be touching hot metal with your bare hands.
Mastering the Techniques of Sheet Metal Welding
Alright, now that we’ve got the tools and the know-how, it’s time to put it all together and start welding some sheet metal! But before we dive in, let me share a few key techniques that will help you get the perfect weld every time.
First and foremost, preparation is key. Make sure your workpiece is clean, free of any dirt or debris, and properly aligned. You’ll also want to use a clamp or fixture to keep the metal in place – trust me, trying to hold it steady with your bare hands is a recipe for disaster.
Next, it’s all about controlling your heat input. Start with a lower amperage setting and slowly work your way up until you find the sweet spot. You’ll also want to keep the welding torch moving at a steady pace, avoiding any lingering or pausing. Remember, too much heat can warp and distort the metal, so it’s all about finding that perfect balance.
And speaking of the welding torch, the angle at which you hold it is also crucial. For sheet metal, you’ll want to keep the torch at a relatively shallow angle, around 15-20 degrees. This will help you achieve a nice, even weld bead and prevent any undercut or burnthrough.
Putting It All Together: Real-World Sheet Metal Welding Projects
Now that we’ve covered the basics, let’s take a look at some real-world sheet metal welding projects that you can tackle with your newly acquired skills.
One of the most common applications for sheet metal welding is in the world of custom fabrication. Think about all those sleek, modern-looking metal furniture pieces or architectural features – yep, that’s the work of a skilled sheet metal welder.
For example, let’s say you want to create a custom metal bookshelf for your living room. With your trusty welding setup, you can easily fabricate the individual shelves and frames, then assemble them into a one-of-a-kind piece that perfectly fits your space. The key is to take your time, measure everything precisely, and use those clamping techniques we talked about to ensure a rock-solid final product.
Another popular application for sheet metal welding is in the automotive world. Whether you’re repairing a dented fender or custom-building a racing exhaust system, the ability to weld thin, delicate sheet metal can be a game-changer. And let me tell you, there’s nothing quite like the satisfaction of seeing your handiwork roaring down the racetrack or cruising down the street.
But it’s not just about the big, flashy projects, my friends. Even simple household items like custom metal storage bins or decorative wall panels can benefit from some skilled sheet metal welding. The possibilities are truly endless when you have the right tools and techniques in your arsenal.
Perfecting Your Craft: Tips and Tricks for the Aspiring Sheet Metal Welder
Alright, so you’ve got the basics down, you’ve tackled a few projects, and you’re feeling pretty good about your sheet metal welding skills. But don’t get too complacent just yet – there’s always room for improvement!
One of the most important things to remember is that practice makes perfect. The more you weld, the more comfortable and confident you’ll become. So, don’t be afraid to experiment, try new techniques, and challenge yourself with more complex projects.
And speaking of challenging projects, one thing that can really take your sheet metal welding to the next level is the ability to work with different metals. While mild steel might be the most common, don’t be afraid to venture into the world of stainless steel, aluminum, or even exotic alloys. Each material has its own unique properties and challenges, but mastering them will make you a true sheet metal welding rockstar.
Another key tip is to always stay up-to-date on the latest welding technologies and best practices. Attend workshops, read industry publications, and connect with other welding enthusiasts. You never know what new tricks or techniques you might pick up along the way.
And of course, don’t forget the importance of safety. Welding, even with sheet metal, can be a dangerous business if you’re not properly protected. Always wear your PPE (personal protective equipment), work in a well-ventilated area, and never underestimate the power of a good pair of welding gloves.
Unlocking Your Sheet Metal Welding Potential
Well, there you have it, folks – the secrets to welding sheet metal with simple tools. From understanding the fundamentals to mastering the techniques, and even tackling real-world projects, you’re now well on your way to becoming a sheet metal welding superstar.
But remember, the journey doesn’t end here. Welding is an ever-evolving craft, and there’s always more to learn. So, keep practicing, keep experimenting, and keep pushing the boundaries of what’s possible. Who knows, maybe one day you’ll be the one mesmerizing a wide-eyed apprentice with your sheet metal welding prowess.
And if you’re ever in need of some professional-grade welding services, don’t forget to check out Corr Connect. We’ve got a team of seasoned welding experts who can tackle any sheet metal project, no matter how big or small. So, what are you waiting for? Let’s get welding!