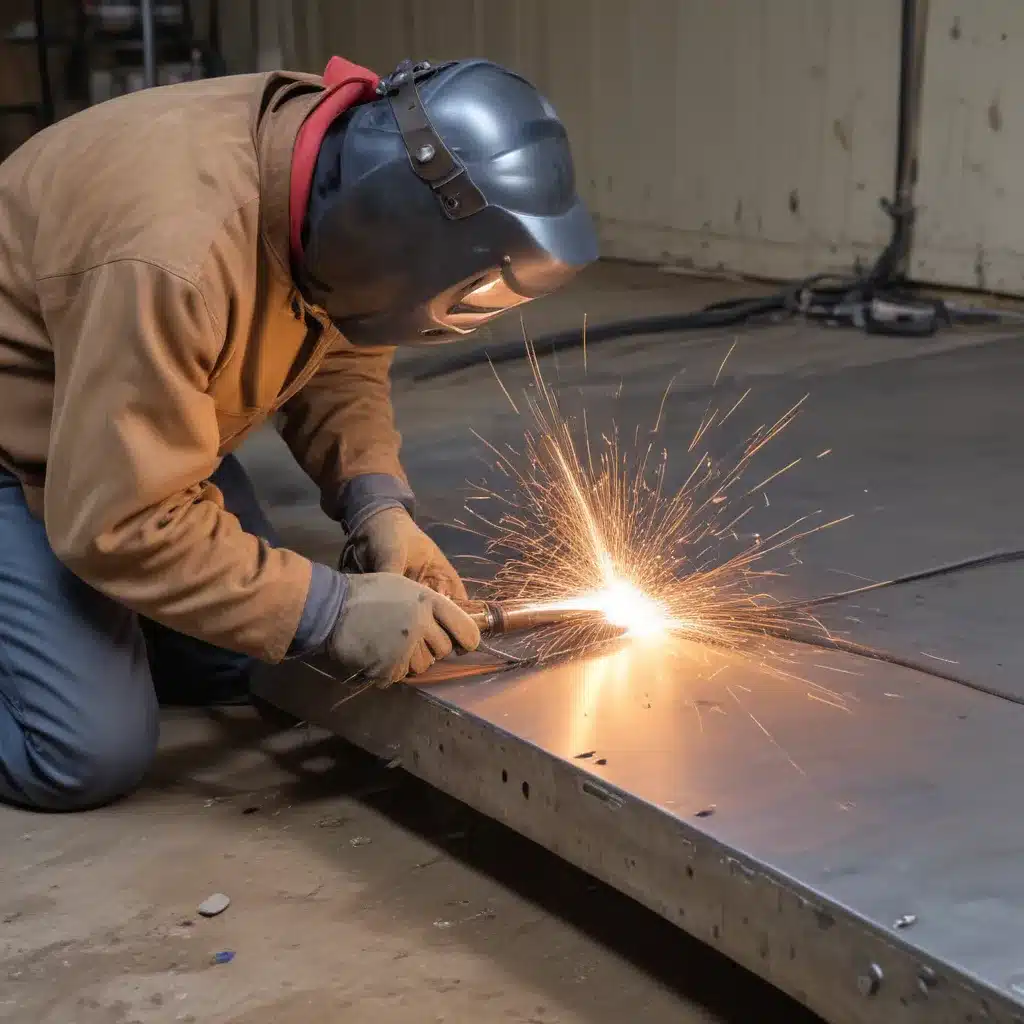
Introduction: The Allure of Welding Sheet Metal
Ah, the art of welding sheet metal – it’s a captivating dance between man and machine, a symphony of sparks and molten steel. As someone who’s been welding for what feels like an eternity (okay, maybe just a few years), I can attest to the sheer joy and satisfaction that comes from fusing two pieces of metal together with nothing but the gentle hum of a gas welder and a steady hand.
You see, welding sheet metal is a unique beast – it requires a delicate touch, a keen eye, and a deep understanding of the material. It’s not like welding thick plates of steel, where you can just muscle your way through. No, with sheet metal, it’s all about finesse, control, and a deft touch. And let me tell you, once you master the art, the possibilities are endless.
The Fundamentals of Gas Welding Sheet Metal
So, what exactly does it take to weld sheet metal with a gas welder? Well, let’s dive in, shall we? First and foremost, you’ll need to get your hands on the right equipment. A good quality gas welder, a steady supply of shielding gas (usually a mixture of argon and carbon dioxide), and some high-quality sheet metal are the essential ingredients.
But it’s not just about having the right tools – it’s also about understanding how they work together. The key to successful gas welding of sheet metal is maintaining the proper balance between the gas flow, the heat input, and the welding speed. Too much heat, and you’ll end up with a warped, distorted mess. Too little heat, and you’ll end up with a weak, inconsistent weld.
It’s all about finding that sweet spot, that perfect harmony between the various elements. And let me tell you, it can take some serious practice to get it just right. But trust me, once you do, it’s a feeling like no other. It’s like riding a bike for the first time, or hitting the perfect golf shot – pure, unadulterated bliss.
Preparing the Metal for Welding
But before we can even think about striking that first arc, we need to make sure our sheet metal is properly prepared. This is a crucial step, and one that many welders often overlook. You see, the surface of the metal needs to be clean, free of any dirt, rust, or paint, in order to ensure a strong, high-quality weld.
So, what’s the best way to prep your sheet metal? Well, you can start by giving it a good cleaning with a degreaser or solvent, just to make sure there’s no oil or grime on the surface. Then, use a wire brush or a sanding disc to remove any rust or scale. And if the metal has been painted or coated, you’ll need to strip that off as well.
Once you’ve got a nice, clean surface, you’ll want to make sure the edges are nice and straight, with no ragged or uneven bits. You can use a metal shear or a angle grinder to tidy things up, and then you’re ready to start welding.
Mastering the Welding Technique
Alright, now comes the fun part – the actual welding process. Now, I know what you’re thinking – “How hard can it be? It’s just a matter of pointing the torch and pulling the trigger, right?” Well, my friend, if only it were that simple.
Welding sheet metal with a gas welder is a delicate dance, a carefully choreographed routine that requires a steady hand, a keen eye, and an intimate understanding of the material. You see, the key is to maintain a consistent distance between the torch and the metal, while also controlling the speed and direction of the weld.
Too much heat, and you’ll end up with a big, ugly, distorted weld. Too little heat, and you’ll end up with a weak, inconsistent joint. It’s all about finding that perfect balance, that sweet spot where the metal just seems to flow together seamlessly.
And let me tell you, it’s not easy. It takes practice, patience, and a whole lot of trial and error. But once you get the hang of it, it’s like a whole new world opens up. Suddenly, you’re not just welding – you’re creating, sculpting, shaping the very material itself.
Achieving a High-Quality Weld
Okay, so you’ve got the basics down – you know how to prep the metal, you’ve got a handle on the welding technique, and you’re feeling pretty darn confident. But there’s one more piece to the puzzle – achieving a high-quality weld that’s strong, consistent, and visually appealing.
Now, I know what you’re thinking – “How hard can it be? I just need to make sure the weld is nice and shiny, right?” Well, my friend, there’s a lot more to it than that. You see, a high-quality weld isn’t just about the way it looks – it’s about the underlying structure, the integrity of the joint, and the overall strength of the connection.
So, what’s the secret? Well, it all comes down to paying attention to the little details. Things like the angle of the torch, the speed of the weld, the amount of filler metal used – they all play a crucial role in determining the quality of the final product.
And let me tell you, it’s not always easy to get it right. There’s a lot of trial and error involved, a lot of experimentation and fine-tuning. But when you do finally nail it, when you produce that perfect, shimmering weld that’s as strong as it is beautiful – well, let’s just say, it’s a feeling that’s hard to top.
Practical Applications and Case Studies
Now that we’ve covered the basics of welding sheet metal with a gas welder, let’s take a look at some real-world applications and case studies. Because let me tell you, the possibilities are endless.
Take, for example, the case of [Company X], a custom fabrication shop that specializes in high-end architectural metalwork. They recently took on a project to create a stunning, one-of-a-kind stainless steel staircase for a high-end residential property. The client wanted something truly unique, something that would make a bold statement and really showcase the beauty of the material.
To achieve this, the team at [Company X] relied heavily on their gas welding expertise, carefully crafting each individual component with the utmost precision and care. They paid close attention to the angle and speed of the weld, ensuring that the final product was not only visually stunning, but also incredibly strong and durable.
And the results? Well, let’s just say the client was more than satisfied. The staircase was a true work of art, a testament to the skill and artistry of the [Company X] team. And it all started with a gas welder and a keen understanding of how to weld sheet metal.
Or take the case of [Company Y], a metal fabrication shop that specializes in custom motorcycle parts and accessories. They recently took on a project to create a one-off fuel tank for a high-end custom build, and they knew that gas welding would be the key to success.
Using a combination of precise measurement, careful metal preparation, and masterful welding technique, the [Company Y] team was able to craft a fuel tank that was not only visually stunning, but also incredibly strong and durable. And the best part? The client was over the moon with the final product, praising the team’s attention to detail and their ability to bring their vision to life.
These are just a couple of examples of the incredible things that can be accomplished with gas welding and sheet metal. And the truth is, the possibilities are truly endless. Whether you’re creating architectural masterpieces, custom motorcycle parts, or anything in between, the art of welding sheet metal with a gas welder is a skill that can open up a whole world of creative possibilities.
Conclusion: The Endless Possibilities of Gas Welding
So, there you have it – a deep dive into the world of welding sheet metal with a gas welder. From the fundamentals of the process to the practical applications and case studies, we’ve covered it all. And let me tell you, it’s a truly fascinating and rewarding field to explore.
As someone who’s been welding for years, I can attest to the sheer joy and satisfaction that comes from mastering this art. It’s not just about the technical skills – it’s about the creative expression, the ability to shape and mold the very material itself. And when you finally achieve that perfect, high-quality weld, it’s a feeling that’s truly unparalleled.
But don’t just take my word for it. I encourage you to get out there and give it a try for yourself. Whether you’re a seasoned welder or a complete beginner, the world of gas welding sheet metal is waiting to be explored. And who knows – you might just discover a hidden passion, a newfound love for the art of creating with your own two hands.
So, what are you waiting for? Grab a gas welder, some sheet metal, and let’s get to work! The possibilities are endless, my friends, and the journey is sure to be filled with adventure, discovery, and a whole lot of sparks.