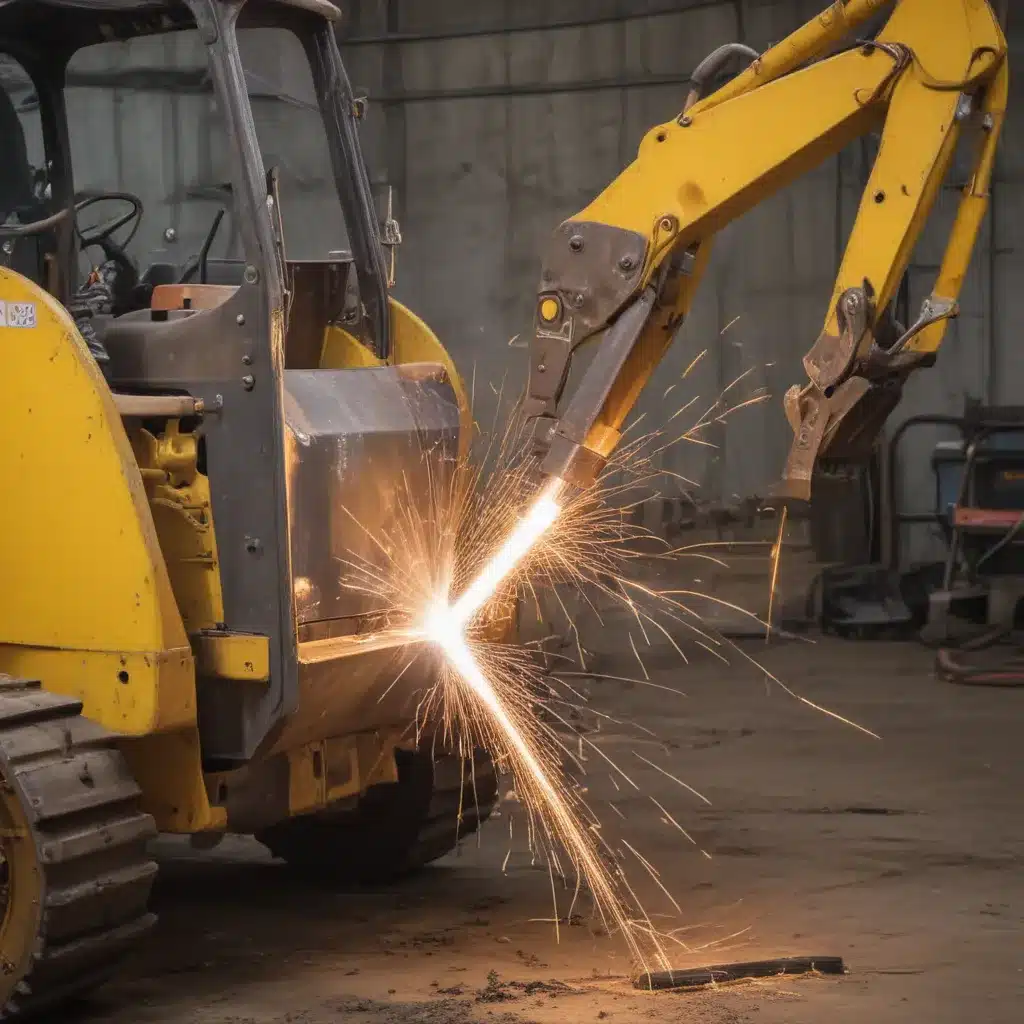
The Art of Taming Steel: Welding Heavy Equipment
Hey there, fellow welding enthusiasts! Today, we’re diving deep into the world of welding heavy equipment, specifically those beastly buckets and blades that move mountains and shape the very earth beneath our feet. If you’re like me, the thought of tackling these hulking hunks of metal gets your heart racing and your creative juices flowing.
So, strap in, because we’re about to embark on a journey that’ll teach you the secrets to conquering even the mightiest of heavy equipment components. From the fundamentals of arc welding to the finer details of custom fabrication, we’ll cover it all. By the time we’re done, you’ll be wielding your welder like a true artist, transforming raw steel into works of functional art.
Mastering Arc Welding for Heavy Equipment
Let’s start with the backbone of our craft: arc welding. This tried-and-true technique is the workhorse of the welding world, and when it comes to heavy equipment, it’s an absolute must-have in your skillset.
Now, I know what you’re thinking – “Arc welding? Isn’t that just for the pros?” Well, my friend, with the right know-how and a little bit of practice, even a beginner can become an arc welding ace. The key is understanding the principles behind it and learning how to control that electric arc like a virtuoso conductor.
First and foremost, we need to talk about the different types of arc welding. There’s good old SMAW (Shielded Metal Arc Welding), also known as stick welding, which is a classic go-to for heavy-duty applications. Then there’s GMAW (Gas Metal Arc Welding), or MIG welding, which uses a continuously fed wire electrode and a shielding gas to create a super-strong, high-quality weld.
Now, the real challenge with heavy equipment is the thickness of the metal. These buckets and blades are built to withstand the harshest conditions, which means they’re usually made from some seriously thick, heavy-duty steel. That’s where your welding prowess really comes into play.
You see, with thicker metals, you need to adjust your welding technique to ensure you’re getting full penetration and a rock-solid joint. That means dialing in your amperage, voltage, and wire feed speed just right, and maybe even throwing in a few tricks like preheating the metal or using a multi-pass technique.
But don’t worry, I’ve got your back. Through countless hours of trial and error (and a few singed eyebrows), I’ve learned the ins and outs of welding heavy equipment. And I’m here to share all my hard-earned wisdom with you, my fellow welding enthusiasts.
Mastering Metal Cutting for Heavy Equipment Fabrication
Now that we’ve got the welding part down, let’s talk about another crucial skill for heavy equipment work: metal cutting. After all, you can’t weld something together if you can’t cut it to size in the first place, right?
There are a few different metal cutting techniques that come in handy when dealing with heavy equipment, but the one I tend to reach for is good old-fashioned oxy-fuel cutting. This classic method uses the intense heat of a focused flame to melt and sever through even the thickest of metals.
But oxy-fuel cutting is just the tip of the iceberg. We’ve also got plasma cutting, which uses a concentrated arc of superheated plasma to slice through steel like a hot knife through butter. And for the real precision freaks out there, there’s always the option of CNC (Computer Numerical Control) plasma or laser cutting, where a computer-controlled machine takes care of the cutting for you.
Now, I know what you’re thinking – “Plasma cutting? Laser cutting? That sounds like some high-tech, expensive stuff.” And you’re not wrong. Those advanced cutting techniques can certainly put a dent in your budget. But the end result is often worth it, especially when you’re working with heavy equipment components that require intricate, custom-made parts.
Think about it – those bucket teeth and blade edges don’t just happen by accident. They’re meticulously designed and fabricated to maximize efficiency and durability. And with the help of precision metal cutting, you can create those complex shapes and profiles with pinpoint accuracy.
Of course, that’s not to say you can’t get great results with good old oxy-fuel cutting. With a steady hand, a keen eye, and a little bit of practice, you can work wonders with that trusty torch. The key is knowing which cutting technique is best suited for the job at hand.
Precision Welding for Heavy Equipment
Alright, now that we’ve got the cutting part down, let’s talk about the real magic – precision welding for heavy equipment. This is where the rubber meets the road, where your welding skills are put to the ultimate test.
You see, when it comes to heavy equipment, there’s no room for error. These machines are the backbone of our infrastructure, and they need to be built to withstand the toughest conditions imaginable. That’s why precision welding is so crucial – it’s the difference between a bucket that lasts for years and one that crumbles under the strain.
Now, I know what you’re thinking – “Precision welding? Isn’t that just for the big-shot fabrication shops with all the fancy equipment?” Well, my friend, I’m here to tell you that with the right techniques and a little bit of know-how, even a small-time welding operation can produce work that’s every bit as precise and durable as the big guys.
The key is all about attention to detail. We’re talking meticulously cleaning the metal, perfectly aligning the parts, and dialing in our welding parameters to a tee. And when it comes to heavy equipment, we need to take it a step further – things like pre-heating the metal, using the right filler materials, and applying strategic weld sequencing can make all the difference.
But it’s not just about the technical stuff, you know? Precision welding is also an art form. It’s about understanding the unique challenges of each heavy equipment component, and then using your welding prowess to create a seamless, beautiful finished product.
I remember this one time when I was working on a bucket for a massive excavator. The client wanted a custom design that would maximize the bucket’s capacity and improve its efficiency. It was a real challenge, but I was determined to knock it out of the park.
After hours of meticulous planning and painstaking welding, I stepped back and looked at my creation. And let me tell you, I felt a sense of pride and accomplishment that I’ll never forget. That bucket was a work of art – perfectly balanced, incredibly strong, and a testament to the power of precision welding.
Custom Fabrication for Heavy Equipment
Now, if there’s one thing I love about the world of heavy equipment, it’s the endless possibilities for custom fabrication. These machines are the backbone of our infrastructure, and each one has its own unique needs and requirements. That’s where the true artistry of welding and fabrication comes into play.
Imagine you’re tasked with creating a custom set of reinforced bucket teeth for a massive mining excavator. Or maybe you need to design and fabricate a specialized blade for a snowplow that can handle the toughest winter conditions. These are the kinds of challenges that get my creative juices flowing, and I’ll bet they do the same for you.
You see, when it comes to custom fabrication for heavy equipment, the sky’s the limit. We’re not just talking about minor modifications or replacement parts – we’re talking about truly innovative, one-of-a-kind solutions that push the boundaries of what’s possible.
And let me tell you, there’s nothing quite like the feeling of taking a raw piece of metal and turning it into something that’s both incredibly functional and visually stunning. It’s like sculpting with steel, each weld and cut a deliberate stroke of the chisel, shaping the form and function of the final product.
Now, I know what you’re thinking – “Custom fabrication? That sounds expensive and time-consuming.” And you’re not wrong. Creating truly custom heavy equipment components can be a complex and resource-intensive process. But the payoff is worth it, both for the client and for the skilled welder-fabricator.
Think about it – when you deliver a custom-built bucket or blade that outperforms the competition, you’re not just earning a satisfied customer. You’re also establishing yourself as a master of your craft, a true artisan in the world of heavy equipment. And that kind of reputation is worth its weight in gold.
So, if you’re the kind of welder who thrives on a challenge, who gets a kick out of pushing the boundaries of what’s possible, then custom fabrication for heavy equipment is where you need to be. It’s a world of limitless potential, where your creativity and technical skills can truly shine.
The Future of Welding Heavy Equipment
As we wrap up our journey through the world of welding heavy equipment, I can’t help but feel a sense of excitement for the future. Because let me tell you, the innovations happening in this industry are nothing short of mind-blowing.
Just think about it – the materials, the techniques, the technology. It’s all evolving at a breakneck pace, and the possibilities are truly endless. Who knows what kinds of cutting-edge welding processes or precision fabrication methods we’ll be using a decade from now?
And let’s not forget about the impact of automation and robotics. While I’ll always have a soft spot for the human touch, there’s no denying the power of these high-tech tools. Imagine a future where CNC plasma cutters and robotic welding cells churn out custom heavy equipment components with pinpoint accuracy and lightning-fast efficiency.
But you know what really gets me fired up? The potential for sustainability and environmental responsibility. As we strive to build a greener, more sustainable future, the welding industry is stepping up to the plate. We’re seeing advancements in things like energy-efficient welding machines, recycled and renewable welding materials, and even the use of alternative energy sources like solar and wind power.
It’s all about finding ways to reduce our carbon footprint, to be more mindful of the impact we have on the world around us. And let me tell you, that’s a challenge that I’m more than happy to take on. Because at the end of the day, we’re not just welders – we’re stewards of the planet, caretakers of the equipment that keeps our infrastructure strong and our communities thriving.
So, as we look to the future, let’s embrace the changes, the innovations, and the opportunities that lie ahead. Because the world of welding heavy equipment is only going to get more exciting, more challenging, and more rewarding. And I don’t know about you, but I can’t wait to see what the future has in store.
Conclusion: Unlocking the Potential of Heavy Equipment Welding
Well, there you have it, my fellow welding enthusiasts – a deep dive into the world of welding heavy equipment, from the fundamentals of arc welding to the cutting-edge of custom fabrication. And let me tell you, it’s been one heck of a journey.
Throughout this exploration, we’ve touched on the essential skills and techniques that every heavy equipment welder needs to have in their arsenal. We’ve covered the nuances of arc welding, the art of metal cutting, the precision required for top-notch welding, and the boundless possibilities of custom fabrication.
But more than that, we’ve delved into the true spirit of what it means to be a welder in this industry. It’s about so much more than just laying down a solid bead – it’s about problem-solving, creativity, and a relentless pursuit of perfection. It’s about taking raw materials and transforming them into the backbone of our infrastructure, the tools that move mountains and shape the world around us.
And as we look to the future, it’s clear that the world of heavy equipment welding is only going to become more exciting, more challenging, and more rewarding. With advancements in technology, materials, and sustainability, the possibilities are truly endless.
So, if you’re the kind of welder who thrives on a challenge, who’s always looking to push the limits of what’s possible, then this is the industry for you. Strap in, sharpen your skills, and get ready to unleash your inner metal sculptor. Because trust me, the rewards of mastering heavy equipment welding are more than worth it.