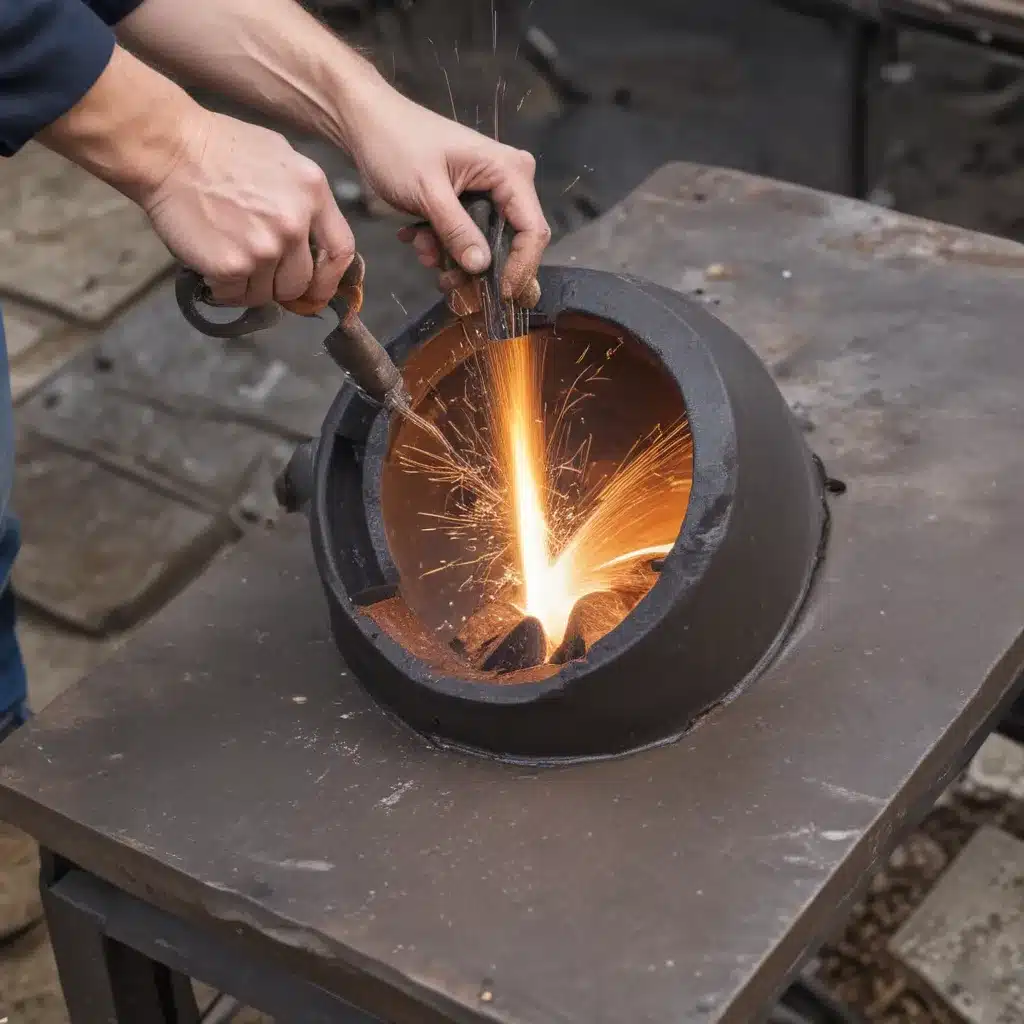
The Challenges of Welding Cast Iron
As a passionate welder, I’ve encountered my fair share of obstacles when it comes to working with cast iron. This notoriously tricky material can be a real headache if you don’t know what you’re doing. But fear not, my friends! I’m here to share my hard-earned wisdom and guide you through the ins and outs of welding cast iron like a pro.
You see, cast iron is a stubborn little bugger. It’s got a high carbon content, which makes it incredibly hard and brittle. Weld that sucker wrong, and you’ll end up with a cracked, distorted mess faster than you can say “slag explosion.” Trust me, I’ve been there, and it’s not a pretty sight.
But you know what they say – where there’s a will, there’s a way. And I’m here to show you how to navigate this treacherous terrain without losing your cool (or your fingers). So, buckle up, grab your welding gear, and let’s dive into the world of cast iron welding!
Preparing the Surface for Welding
The first step to successful cast iron welding is proper surface preparation. This is where the real magic happens, folks. You can’t just slap some beads on there and call it a day – oh no, you’ve gotta do it right.
First and foremost, let’s talk about cleaning. Cast iron has a nasty habit of collecting all sorts of gunk and grime on its surface, and that’s a big no-no when it comes to welding. Think about it – you’re trying to fuse two pieces of metal together, and if there’s a layer of dirt, rust, or oil in the way, it’s not going to work out too well.
So, what’s the solution? Well, you’re gonna want to break out the trusty angle grinder and give that surface a good old-fashioned scrub-down. Remove any paint, scale, or other contaminants until you’ve got a nice, shiny, bare metal surface to work with. Trust me, the extra effort is worth it – you’ll end up with a much stronger, more reliable weld.
But cleaning is just the start. Next up, you’ve gotta think about the weld joint itself. Cast iron has a tendency to warp and distort during the welding process, so you’ll want to make sure your joint is properly prepared to minimize those pesky issues.
One handy trick is to bevel the edges of the joint. This creates a nice, wide groove for the weld metal to fill, and it also helps to distribute the heat more evenly across the surface. And speaking of heat, you’ll want to preheat the area around the joint to about 400-600°F (200-315°C) before you even strike that arc. This helps to reduce the risk of cracking and distortion.
Choosing the Right Welding Process
Now that you’ve got your surface all spick and span, it’s time to think about the welding process itself. When it comes to cast iron, you’ve got a few different options, and each one has its own unique pros and cons.
One of the most common techniques is stick welding, also known as shielded metal arc welding (SMAW). This is a great choice for cast iron because it allows you to lay down some nice, thick beads that can help to bridge those tricky gaps. Plus, the flux-coated electrodes help to protect the weld pool from atmospheric contamination, which is crucial when dealing with cast iron’s finicky nature.
But wait, there’s more! If you’re feeling a bit more adventurous, you could try your hand at gas metal arc welding (GMAW), also known as MIG welding. This process is a bit more high-tech, using a continuous wire feed and a shielding gas to create the weld. The result? A super smooth, consistent bead that can really help to minimize distortion.
And let’s not forget about the good old TIG (tungsten inert gas) welding. This is a precision process that’s perfect for those intricate, delicate cast iron jobs. With TIG, you’ve got more control over the heat input, which can be a real lifesaver when you’re trying to avoid those pesky cracks and warps.
No matter which route you choose, the key is to take it slow and steady. Cast iron welding ain’t no walk in the park, so be patient, keep a close eye on your work, and don’t be afraid to experiment a little. Who knows, you might just discover your new favorite welding technique!
Choosing the Right Filler Metal
Alright, now that we’ve got the prep work and welding process sorted out, let’s talk about the secret weapon in your cast iron welding arsenal: the filler metal.
You see, not all filler metals are created equal when it comes to cast iron. You’ve gotta choose wisely, my friends, or you could be in for a world of trouble. Let me break it down for you:
First up, we’ve got the classic cast iron electrodes. These bad boys are specifically designed for welding cast iron, and they’re loaded with all kinds of goodies like nickel and chromium that can help to counteract the material’s tricky nature. They’re a bit more expensive than your run-of-the-mill filler metals, but trust me, the investment is worth it.
But what if you’re feeling a little adventurous? Well, you could give nickel-based filler metals a try. These have a higher ductility than standard cast iron electrodes, which can help to reduce the risk of cracking. They also tend to have a lower coefficient of thermal expansion, which means they’re less likely to warp and distort during the welding process.
And let’s not forget about the good old-fashioned stainless steel filler metals. Now, I know what you’re thinking – “But wait, isn’t stainless steel a completely different material?” Well, yes and no. The truth is, stainless steel can actually be a pretty decent option for welding cast iron, especially if you’re looking to create a nice, corrosion-resistant weld.
The key is to choose a stainless steel filler metal that’s got a high nickel content – around 10-15% should do the trick. This helps to mimic the properties of cast iron, and it can even give your weld a bit of that signature cast iron look and feel.
Whichever route you choose, the most important thing is to make sure you’re using a filler metal that’s compatible with the specific type of cast iron you’re working with. Consult with your local welding supply shop or do a bit of research to find the perfect match for your project.
Controlling Heat Input and Interpass Temperature
Alright, now that we’ve got the prep work and filler metal sorted out, it’s time to talk about the real nitty-gritty of cast iron welding: controlling that heat input.
You see, when it comes to cast iron, the name of the game is “slow and steady.” If you try to crank up the heat and blaze through those welds, you’re just begging for trouble. We’re talking cracks, warps, and all sorts of other nightmarish scenarios.
Instead, you’ve gotta take your time and be really mindful of that heat input. Start by keeping your welding current on the lower end of the recommended range – we’re talking around 100-150 amps for most cast iron jobs. And be sure to take plenty of breaks in between passes to let that weld pool cool down.
But it’s not just about the current, my friends. You’ve also gotta pay close attention to that interpass temperature. This is the temperature of the weld area in between each successive pass, and it’s crucial for keeping those cast iron demons at bay.
The ideal interpass temperature for cast iron welding is around 200-400°F (95-205°C). Anything hotter, and you’re just asking for trouble. Too cool, and you risk cracking and distortion. It’s all about finding that sweet spot.
Now, I know what you’re thinking – “But how the heck do I keep track of all that?” Well, my friend, that’s where your trusty temperature-indicating crayons come in. These handy little tools can help you keep an eye on that interpass temperature without having to break out the infrared thermometer.
Just run the crayon along the weld area, and it’ll leave a nice, visible mark that tells you exactly where you’re at. If the mark is still there, you know you’re good to go. But if it’s disappeared, it’s time to take a break and let that sucker cool down.
Trust me, taking the time to really dial in that heat input and interpass temperature is the key to successful cast iron welding. It might seem like a hassle, but it’s worth it – I promise your finished weld will be stronger, more durable, and (most importantly) crack-free.
Dealing with Distortion and Cracking
Alright, so you’ve followed all the steps, you’ve got your heat input and interpass temperature dialed in, and you’re feeling pretty confident about your cast iron welding skills. But wait, what’s that? A crack? Or maybe a nasty little warp in your workpiece?
Don’t panic, my friends – this is all part of the cast iron welding game. Even the best of us have had to deal with these pesky little buggers from time to time. But fear not, I’ve got some tricks up my sleeve to help you conquer those distortion and cracking demons.
First and foremost, let’s talk about that cracking problem. As I mentioned before, cast iron is notorious for its brittleness, and that means it’s really susceptible to cracking during the welding process. But there are a few things you can do to mitigate the issue.
One of the most important is to make sure you’re using the right filler metal. As we discussed earlier, nickel-based or stainless steel fillers can be a great way to add some extra ductility to your weld. And don’t forget about that preheat – keeping the base metal nice and toasty can go a long way in preventing those dreaded cracks.
But what about distortion? That’s a whole other beast to tackle, my friends. Cast iron’s high thermal expansion coefficient means it’s just begging to warp and twist as it heats up and cools down during welding. And let me tell you, trying to straighten out a warped cast iron part is no easy feat.
That’s why it’s so important to really focus on your welding technique. Keep those beads small and evenly spaced, take your time, and be super mindful of that heat input. And don’t be afraid to throw in a few strategic tack welds to help hold everything in place.
And let’s not forget about the good old-fashioned clamping and fixturing. Yep, that’s right – sometimes you’ve just gotta get a little brute force involved. Clamp that sucker down tight and watch as those warps and twists magically disappear.
Of course, even with all these precautions, you might still end up with a little bit of distortion or cracking. But hey, that’s all part of the cast iron welding journey, right? Just remember to stay calm, think critically about the problem, and don’t be afraid to experiment until you find a solution that works.
Who knows, maybe you’ll even discover a whole new trick that the rest of us haven’t thought of yet. After all, that’s the beauty of this crazy world of welding – there’s always more to learn, and the journey is half the fun.
Conclusion: Embracing the Challenge of Cast Iron Welding
Well, there you have it, my friends – the secret sauce to successful cast iron welding. It might be a bit of a roller coaster ride, but trust me, the payoff is worth it.
Think about it – when you finally nail that perfect cast iron weld, free of cracks and distortion, it’s like a little victory dance in your workshop. You feel like a true master of your craft, and you can’t wait to show off your handiwork to the world.
And let’s not forget the sheer sense of accomplishment that comes with tackling something as stubborn and challenging as cast iron. It’s like climbing a mountain, my friends – the view from the top is just that much sweeter.
So, don’t be afraid to dive in, get your hands dirty, and embrace the cast iron welding challenge. Who knows, you might just discover a new passion (and a few more tricks up your sleeve) along the way.
And if you ever find yourself in a bind, remember – I’m always here, ready and willing to share my hard-earned wisdom and maybe even a few terrible puns. After all, that’s what friends are for, right?
So, what are you waiting for? Grab your gear, fire up that welder, and let’s get to work on conquering the cast iron beast, one weld at a time. The adventure awaits!