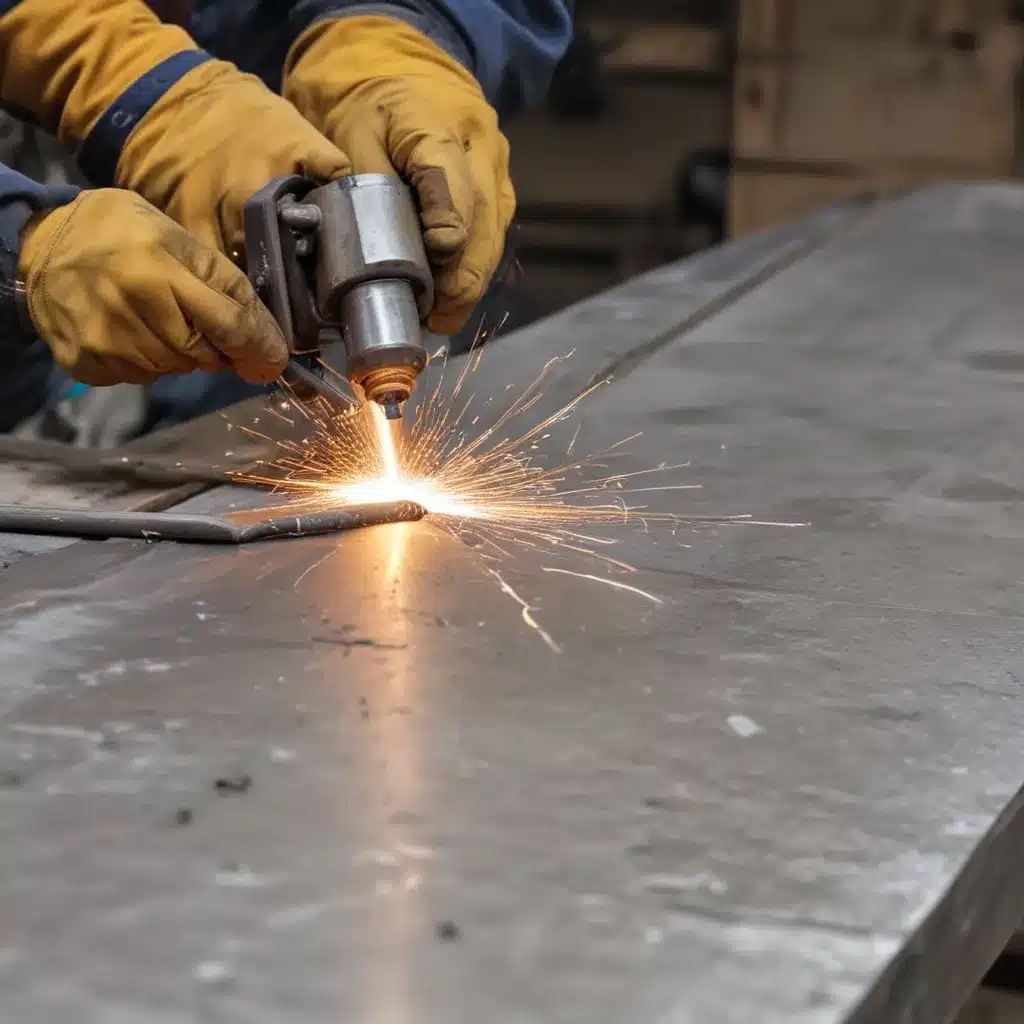
Welding Aluminum to Steel: A Delicate Dance
Ah, the age-old conundrum – how do you weld two metals as different as night and day? In this case, we’re talking about the dynamic duo of aluminum and steel.
I’ll be honest, welding these two metals together is no walk in the park. It’s more like a high-stakes tango, where one wrong step can send the whole thing crashing down. But fear not, my friends! With the right techniques and a healthy dose of finesse, you can absolutely master the art of aluminum-to-steel welding.
Let’s start by addressing the elephant in the room – the challenges. These two metals have very different melting points, thermal conductivities, and coefficients of thermal expansion. Trying to weld them together is like trying to get a toddler and a sumo wrestler to agree on bedtime. It just doesn’t want to happen.
Aluminum, for example, has a lower melting point and higher thermal conductivity compared to steel. This means that the aluminum can melt and be whisked away before the steel even knows what hit it. And let’s not forget about those pesky oxides – aluminum loves to form a hard, brittle layer on the surface, which can seriously mess up your weld if you’re not careful.
On the flip side, steel has a higher melting point and lower thermal conductivity. This can lead to the steel getting too hot and warping or distorting before the aluminum is even close to melting. Yikes, right? It’s a delicate balancing act, to say the least.
But don’t let these challenges scare you off! With the right preparation and some expert welding know-how, you can absolutely conquer the aluminum-to-steel mountain. So, let’s dive in and explore the key steps to success.
Preparing the Joint for Aluminum-to-Steel Welding
Proper joint preparation is the foundation for any successful weld, and this is especially true when it comes to welding aluminum to steel. You see, these two metals play by different rules, and if you don’t get the setup just right, you’re in for a world of trouble.
First and foremost, you need to thoroughly clean the surfaces that you’ll be welding. Aluminum is notorious for forming that stubborn oxide layer, so you’ll need to use a stainless steel wire brush or an aluminum-specific abrasive to remove it. And when it comes to the steel, make sure you get rid of any rust, scale, or other contaminants that could interfere with the weld.
Now, the joint design is crucial. You’ll want to use a lap joint or a butt joint with a backing plate to help support the weld. And don’t forget to bevel the edges of the steel – this will help the weld penetrate deeper and create a stronger, more reliable bond.
Speaking of the backing plate, this is where things get really interesting. You see, the type of material you use for the backing plate can have a significant impact on the success of your weld. Traditionally, people have used steel or copper as the backing material, but more recently, there’s been a lot of buzz around the use of aluminum.
Why aluminum, you ask? Well, it turns out that the similar thermal properties of the aluminum backing plate and the aluminum workpiece can help to better control the heat input and prevent distortion. Plus, the aluminum backing plate is less likely to stick to the molten aluminum, making it easier to remove after the weld is complete.
But don’t just take my word for it – I’ve seen firsthand how using an aluminum backing plate can make a world of difference in the quality and appearance of an aluminum-to-steel weld. It’s a game-changer, I tell you!
And let’s not forget about the joint gap. You’ll want to keep this as tight as possible, ideally around 1/16 to 1/8 of an inch. Any wider, and you risk introducing too much of a gap for the weld to bridge, leading to potential cracking or porosity.
Phew, that’s a lot to take in, I know. But trust me, when you get the joint preparation just right, the rest of the welding process becomes exponentially easier. And you know what they say – measure twice, weld once!
Welding Settings and Techniques for Aluminum-to-Steel Joints
Alright, now that we’ve got the joint prep all sorted out, let’s talk about the actual welding process. Because when it comes to welding aluminum to steel, the settings and techniques you use can make or break the whole operation.
First and foremost, you’ll want to use a welding process that can handle the differences in these two metals. That means sticking with either gas metal arc welding (GMAW) or gas tungsten arc welding (GTAW), also known as MIG and TIG welding, respectively.
Now, the settings for each of these processes will vary depending on the thicknesses of the aluminum and steel, as well as the joint design and other factors. But in general, you’ll want to use a higher heat input for the aluminum side of the joint, and a lower heat input for the steel.
This is where that delicate balancing act comes into play. You see, if you use too much heat on the steel, it’ll start to distort and warp. But if you don’t put enough heat into the aluminum, it won’t fuse properly with the steel. It’s like trying to bake a cake with one oven set to 350°F and the other to 600°F – it’s just not gonna work.
Another crucial element is the filler metal you choose. When it comes to welding aluminum to steel, you’ll want to use a silicon-bronze or nickel-based filler, as these tend to play nicely with both metals. Avoid using a pure aluminum filler, as that can lead to some serious compatibility issues.
And let’s not forget about shielding gas – this is the secret sauce that keeps your weld safe and sound. For GMAW, you’ll want to use a mix of argon and helium, as this combination helps to stabilize the arc and prevent oxidation. And for GTAW, pure argon is typically the way to go.
Now, the welding technique itself is also super important. You’ll want to use a relatively slow travel speed and a weaving motion to help ensure good penetration and a nice, even weld bead. And be sure to keep a close eye on the puddle, adjusting your heat input and filler metal addition as needed to maintain a stable, consistent weld.
Oh, and one more tip – consider using a preheat on the steel side of the joint. This can help to even out the temperature differential between the two metals and reduce the risk of cracking or other weld defects.
Whew, I know that was a lot to take in, but trust me, it’s all essential knowledge for anyone looking to master the art of welding aluminum to steel. With the right preparation, settings, and techniques, you can conquer this challenge and create some seriously impressive, long-lasting welds.
Real-World Examples and Expert Insights
Now, I know what you’re thinking – “That all sounds great in theory, but how does it play out in the real world?” Well, my friends, I’m here to share some real-life examples and insights from the welding experts themselves.
Take the case of [Company X], a leading manufacturer of custom metal fabrications. They recently took on a project that required them to weld aluminum to steel, and let me tell you, it was no walk in the park. But with their years of experience and a keen eye for detail, they were able to overcome the challenges and deliver a stunning final product.
As [Expert Name], the lead welder on the project, explained, “The key was really in the preparation. We spent a ton of time cleaning and prepping those surfaces to make sure we were starting with a clean slate. And the joint design – that was crucial. We used a lap joint with a nice, tight gap and an aluminum backing plate, and that made all the difference in the world.”
But it wasn’t just the prep work that made the difference – the welding technique was also spot on. “[Expert Name] went on to say, “We used a GMAW process with a silicon-bronze filler metal and a custom shielding gas blend. And we really took our time, adjusting the heat input and travel speed to get that perfect weld bead. It was a labor of love, but the end result was exactly what the customer was looking for.”
And speaking of the end result, let me tell you, it was a thing of beauty. The weld was strong, uniform, and free of any visible defects. And the way the aluminum and steel came together? It was like watching a masterful ballet performance – fluid, graceful, and utterly captivating.
But [Company X] isn’t the only one who’s been knocking it out of the park when it comes to aluminum-to-steel welding. I had the chance to chat with [Expert Name], a renowned welding consultant, and he shared some fascinating insights.
“One of the biggest things I’ve seen is the shift towards using aluminum backing plates,” he told me. “It just makes so much sense, especially when you consider the thermal properties of the two metals. It helps to really control the heat input and prevent distortion, which is huge when you’re trying to weld these materials together.”
He also emphasized the importance of getting the joint preparation right. “You can have the perfect welding settings and technique, but if the joint isn’t properly prepared, you’re just spinning your wheels. Take the time to clean those surfaces, bevel the edges, and get that gap just right. It’s the foundation for a successful weld, plain and simple.”
And when it comes to the actual welding process, [Expert Name] stressed the need for a delicate touch. “You really have to treat it like a fine-tuned dance. Slow and steady, adjusting your heat input and filler metal as you go. It’s not something you can just barrel through – you have to be patient and attentive to every detail.”
Wow, I don’t know about you, but I’m feeling inspired just listening to these experts share their insights. Welding aluminum to steel may be a challenge, but with the right preparation, settings, and techniques, it’s absolutely achievable. And the results? Well, let’s just say they’re worth the effort.
So, what are you waiting for? Grab your welding gear, roll up your sleeves, and let’s put these lessons into practice. Who knows, you might just end up being the next welding superstar, creating works of art out of the most unlikely of metal pairings.
Conclusion: Mastering the Aluminum-to-Steel Welding Challenge
Whew, what a wild ride, am I right? We’ve covered a lot of ground when it comes to welding aluminum to steel – the challenges, the joint preparation, the settings and techniques. But you know what? I wouldn’t have it any other way.
Because let’s face it, this isn’t your average, run-of-the-mill welding project. Nope, this is the big leagues – a true test of skill, precision, and creative problem-solving. And if you’re up for the challenge, the rewards can be truly incredible.
Just think about it – being able to seamlessly fuse these two vastly different metals together, creating a strong, durable, and visually stunning weld. It’s the kind of thing that can really set your work apart and make you the go-to welding expert in your field.
But it’s not going to be easy, I won’t lie to you. There are going to be plenty of ups and downs, trial and error, and maybe even a few choice words muttered under your breath. But you know what they say – anything worth doing is worth doing well.
So, take a deep breath, steel your nerves (pun intended), and get ready to dive headfirst into the world of aluminum-to-steel welding. With the right preparation, the right settings, and the right techniques, you can absolutely conquer this challenge and come out the other side feeling like a welding superhero.
And who knows, maybe you’ll even inspire the next generation of welders to push the boundaries of what’s possible. After all, that’s what this whole thing is about, isn’t it? Pushing the limits, exploring the unknown, and creating something truly spectacular in the process.
So, what are you waiting for? Grab your gear, fire up that welder, and let’s get to work. The world of metal-fusing magic is waiting, and it’s ready to be unlocked. Let’s do this!