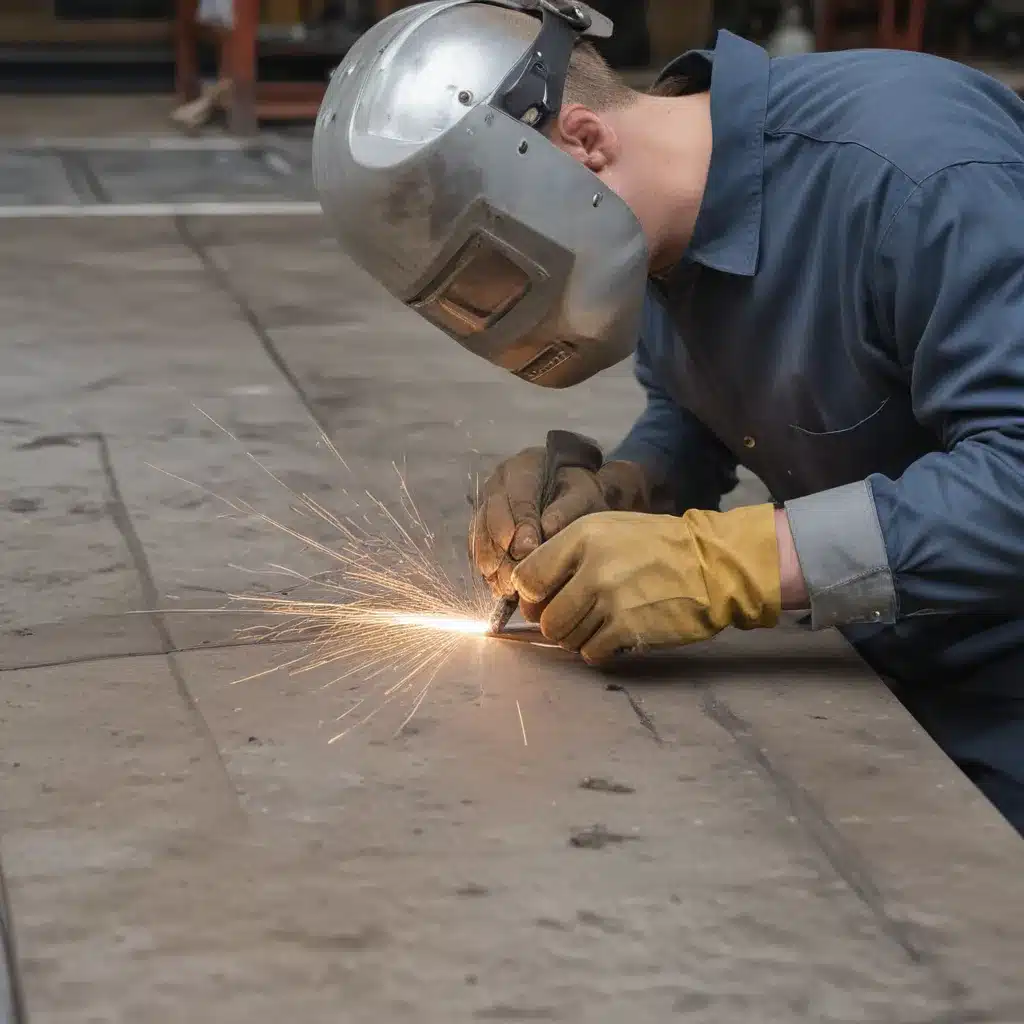
Diving into the World of Aluminum Welding
Ah, the alluring world of aluminum welding – a realm where sparks fly, metal melds, and the possibilities are as endless as the curiosity that draws us in. As a beginner, the prospect of tackling this material can feel both exhilarating and, let’s be honest, a tad intimidating. But fear not, my fellow welding enthusiasts! I’m here to guide you through the ins and outs of aluminum welding, sharing tips, tricks, and a few hard-earned lessons along the way.
You see, I remember the day I first decided to venture into the world of aluminum welding. I had been honing my skills on good ol’ steel for a while, feeling pretty confident in my abilities. But then, the siren call of this lighter, more malleable metal came beckoning. “Come, try me,” it whispered, “I’ll challenge you in ways you’ve never imagined.” Well, challenge accepted! And let me tell you, the journey has been nothing short of exhilarating.
Understanding the Unique Properties of Aluminum
Before we dive into the nitty-gritty of the welding process, it’s crucial to understand the unique properties of aluminum that set it apart from its steel counterparts. Aluminum is a fascinating material – it’s lightweight, corrosion-resistant, and highly conductive, making it a popular choice for a wide range of applications, from aerospace engineering to everyday household items.
But what does this mean for us welders? Well, let’s start with the fact that aluminum has a lower melting point compared to steel. This means we need to be extra mindful of our heat input and controlling the weld pool to avoid burning through the material or creating unsightly warping. Additionally, aluminum is highly reflective, which can make it challenging to see the weld puddle and control the arc.
Another key consideration is the oxide layer that forms on the surface of aluminum. This thin layer can act as a barrier, preventing the weld pool from merging properly. To overcome this, we need to remove the oxide layer before welding, either through mechanical means like brushing or chemical methods like using a flux.
Mastering the Aluminum Welding Process
Now that we’ve got a solid understanding of the unique properties of aluminum, let’s dive into the welding process itself. As a beginner, the first step is to familiarize yourself with the various welding processes available for aluminum. The most common ones are TIG (Tungsten Inert Gas) welding and MIG (Metal Inert Gas) welding.
TIG welding is often considered the “gold standard” for aluminum welding, as it allows for precise control and produces high-quality welds. The downside is that it can be a bit more challenging to master, requiring a steady hand and a keen eye. MIG welding, on the other hand, is a bit more forgiving and can be a great option for beginners. It’s faster and easier to learn, but may not achieve the same level of precision as TIG.
Regardless of the process you choose, the key to successful aluminum welding is all about preparation. Take the time to thoroughly clean the surface, removing any dirt, grease, or oxide buildup. This will ensure a clean, strong weld. You’ll also want to use the appropriate filler metal, which is usually an aluminum-based alloy that closely matches the base material.
Conquering the Challenges of Aluminum Welding
As with any new skill, aluminum welding comes with its fair share of challenges. One of the biggest hurdles I faced as a beginner was managing the heat input. Aluminum has a low thermal conductivity, meaning it doesn’t dissipate heat as quickly as steel. This can lead to excessive melting, warping, and even burnthrough if you’re not careful.
To overcome this, I learned to pay close attention to my travel speed, adjusting it as needed to maintain a consistent weld pool. I also discovered the importance of using the right shielding gas – a mixture of argon and helium works best for aluminum – to ensure proper protection and prevent porosity in the weld.
Another tricky aspect of aluminum welding is managing the weld puddle. Because aluminum is so fluid and reflective, it can be challenging to see and control the puddle, especially when you’re first starting out. I found that using a smaller tungsten electrode and a lower amperage setting helped me to better manage the weld pool and produce cleaner, more consistent welds.
Practical Applications and Real-World Examples
Now that we’ve covered the fundamentals of aluminum welding, let’s explore some practical applications and real-world examples. One of the most common uses for aluminum welding is in the automotive industry, where it’s used to fabricate everything from engine components to lightweight body panels.
Take the case of [Company Name], a renowned custom fabrication shop specializing in high-performance vehicles. They recently took on a project to build a custom exhaust system for a rare sports car. The challenge? The exhaust needed to be lightweight, corrosion-resistant, and strong enough to withstand the extreme heat and vibrations of the engine. Enter the power of aluminum welding.
The team at [Company Name] carefully selected the right aluminum alloy for the job, carefully prepped the surfaces, and used a combination of TIG and MIG welding techniques to create a stunning, functional exhaust system. The result? A lightweight, durable, and visually striking piece that perfectly complemented the car’s sleek design.
But the world of aluminum welding extends far beyond the automotive realm. I’ve seen it used in everything from custom furniture and architectural metalwork to marine applications and even aerospace engineering. The versatility of this material is truly astounding, and the possibilities are limited only by our imagination.
Honing Your Aluminum Welding Skills
As you continue your journey into the world of aluminum welding, remember that practice, patience, and a willingness to learn are key. Don’t be discouraged by the challenges – embrace them as opportunities to grow and improve.
One of the best ways to hone your skills is to start with smaller, simpler projects and gradually work your way up to more complex tasks. Maybe begin with a simple aluminum frame or a small decorative piece. As you gain confidence and experience, you can tackle larger, more intricate projects.
And don’t forget the power of education! Seek out welding workshops, online tutorials, and experienced mentors who can share their knowledge and insights. The more you learn, the more you’ll be able to tackle those tricky aluminum welding challenges with ease.
Conclusion: Embracing the Aluminum Welding Adventure
So, there you have it, fellow welding enthusiasts – a comprehensive guide to conquering the world of aluminum welding as a beginner. From understanding the unique properties of this fascinating metal to mastering the welding process and overcoming the challenges, you’re now armed with the knowledge and tools to embark on your own aluminum welding adventure.
Remember, the journey may not always be smooth sailing, but the sense of accomplishment and the thrill of creating something truly unique with your own two hands is worth every spark and every bead of sweat. So, what are you waiting for? Grab your gear, fire up that welder, and let’s dive into the world of aluminum welding together!
And if you’re looking for a trusted partner to help you with your aluminum welding needs, be sure to check out [COMPANY NAME] at https://www.corrconnect.org/. Their team of skilled welders and fabricators are ready to bring your vision to life, no matter how ambitious or intricate it may be.