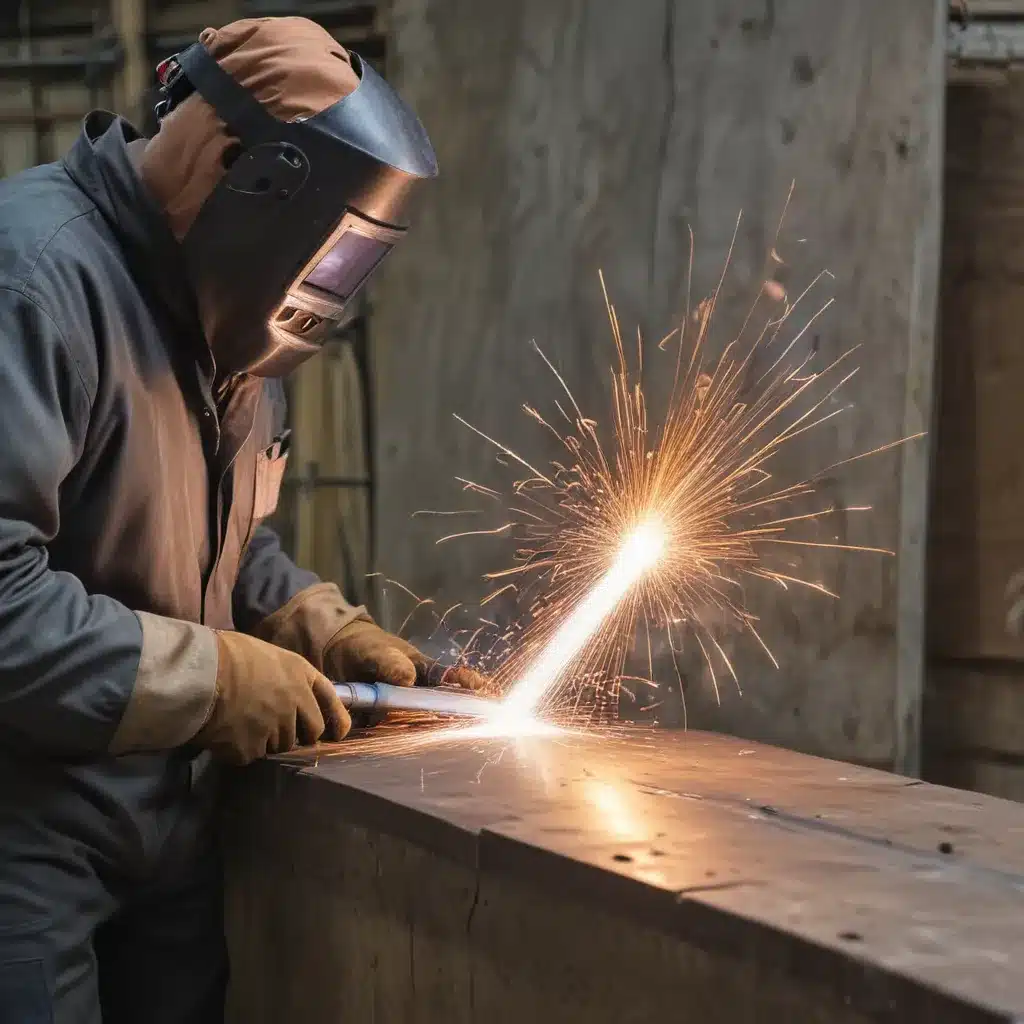
Understanding the Importance of Metal Preparation
As a seasoned welding professional, I can’t stress enough the importance of proper metal preparation. You see, the quality of your welding project doesn’t just depend on your technical skills – it’s also heavily influenced by how well you’ve prepared the surfaces to be joined. Think of it like building a house: you wouldn’t just start hammering nails into a pile of raw lumber, would you? No, you’ve got to lay a strong foundation first.
In the world of welding, that foundation is all about getting the metal surfaces clean, flat, and ready to accept the intense heat and pressure of the welding process. Fail to do this, and you could be in for a world of trouble – from weak, porous welds to unsightly distortion and warping.
But fear not, my friends! In this comprehensive guide, I’m going to walk you through all the essential steps to ensure your metals are primed and prepped for welding perfection. We’ll cover everything from choosing the right tools and techniques to dealing with tricky materials like stainless steel and aluminum. By the time we’re done, you’ll be a metal preparation pro, ready to tackle any welding project that comes your way.
Assessing the Metal Surfaces
The first step in preparing metals for welding is to closely examine the surfaces you’ll be working with. What are we looking for, you ask? Well, let’s start with the obvious – any visible dirt, grease, rust, or other contaminants. These foreign substances can seriously compromise the integrity of your welds, causing everything from porosity to cracking.
But it’s not just the surface layer we need to worry about. Beneath that, we also need to consider the overall condition of the metal itself. Are there any nicks, gouges, or other physical defects? These irregularities can disrupt the flow of the welding arc and lead to uneven penetration or warping. And what about the thickness of the metal? Thicker pieces may require more aggressive preparation techniques to ensure proper fusion.
To get a comprehensive understanding of the metal’s condition, I like to start with a good old-fashioned visual inspection. I’ll carefully examine the surfaces, looking for any potential problem areas. Then, I might use a thickness gauge or other measurement tools to get a better sense of the material’s properties. This gives me a solid foundation to build my preparation strategy upon.
Cleaning the Metal Surfaces
Alright, now that we’ve assessed the metal, it’s time to get down and dirty with the cleaning process. This is where the real magic happens, my friends. Because if you don’t get those surfaces squeaky clean, you can kiss your dreams of a perfect weld goodbye.
Now, the specific cleaning techniques you’ll need to use will depend on the type of metal you’re working with and the nature of the contaminants. For example, if you’re dealing with a mild steel covered in light rust and grease, a simple degreaser and some elbow grease might do the trick. But if you’re working with stainless steel and there’s a stubborn layer of oxide buildup, you might need to break out the heavy-duty abrasives.
Personally, I’m a big fan of using a combination of chemical cleaners and mechanical abrasion. I’ll start with a good degreasing solution to remove any oily residues, then follow up with some careful sanding or grinding to get down to clean, bright metal. And don’t forget to protect your airways – those metal particles can be a real hazard if you’re not careful.
Once the surfaces are clean, it’s important to keep them that way. I always make sure to wipe down the metal with a lint-free cloth just before I start welding, just to be absolutely sure there’s no lingering grime or dust. After all, you can’t build a solid structure on a foundation of sand, can you?
Shaping and Aligning the Metal
Alright, now that we’ve got the cleaning out of the way, it’s time to move on to the next critical step in metal preparation: shaping and aligning the surfaces.
You see, even if the metal is spotlessly clean, it still might not be ready for welding. There could be warping, gaps, or other irregularities that need to be addressed before you can get those parts joined together seamlessly.
That’s where tools like clamps, jigs, and positioners come in handy. By carefully positioning and securing the metal components, I can ensure that the surfaces are perfectly aligned and ready for that molten weld pool to work its magic.
But it’s not just about lining things up – we also need to think about the actual shape of the joint. Are we talking a simple butt weld, or do we need to bevel the edges to create a stronger, more penetrating joint? Should we leave a small gap to allow for thermal expansion, or do we need to tightly close that gap for maximum strength?
These are the kinds of questions I’m constantly asking myself as I prepare the metal. And let me tell you, it’s an art form unto itself. It takes a keen eye, a steady hand, and a deep understanding of how different joint configurations behave under the intense heat and forces of welding.
But trust me, it’s all worth it in the end. When those parts are perfectly aligned and ready for welding, you can practically feel the quality and precision radiating off of them. It’s a beautiful thing, my friends, and it’s all thanks to the time and care we put into the prep work.
Selecting the Right Welding Process
Alright, now that we’ve got the metal all cleaned up and prepped for action, it’s time to turn our attention to the welding process itself. Because, let’s be honest, not all welding techniques are created equal – and the one you choose can have a major impact on the success of your project.
Now, I know what you’re thinking – “But I’m the welding expert here, shouldn’t I already know which process is best?” And you’d be absolutely right. But the thing is, the welding process you select isn’t just about your own personal preferences or expertise. It’s also heavily influenced by the specific properties and characteristics of the metal you’re working with.
For example, let’s say you’re tasked with welding some high-strength alloy steel. In a case like that, you might want to consider a process like gas metal arc welding (GMAW), also known as MIG welding. The controlled heat input and deep, penetrating weld pool can help you achieve the necessary strength and integrity without risking distortion or cracking.
On the other hand, if you’re working with thin, delicate materials like aluminum or stainless steel, you might want to lean more towards a process like tungsten inert gas (TIG) welding. The precise control and localized heat input can help you avoid burnthrough and maintain tight tolerances.
And let’s not forget about the role of joint design in all of this. Certain welding processes are better suited for specific joint configurations, so it’s important to take that into account as well. A simple butt joint, for instance, might work just fine with a basic shielded metal arc (stick) weld. But if you’re dealing with a complex multi-pass fillet weld, you might want to consider a semi-automatic or even robotic welding system to ensure consistent quality and productivity.
The key is to keep an open mind and be willing to experiment a bit. After all, the world of welding is constantly evolving, and there’s always something new to learn. So don’t be afraid to step outside your comfort zone and try different techniques – you just might discover a whole new way to tackle those metal preparation challenges.
Dealing with Tricky Materials
Now, I know what you’re thinking – “Okay, I get it, metal preparation is important. But what about those trickier materials, like stainless steel and aluminum? Surely they require some special handling, right?”
Bingo! You’re absolutely right. When it comes to metals like stainless and aluminum, the preparation process can be a whole different ballgame. These materials often have unique properties and characteristics that require a more specialized approach.
Let’s start with stainless steel. Now, this stuff is known for its corrosion resistance and durability, which is great. But that same resistance can also make it a real bear to work with when it comes to welding. You see, stainless steel has a tendency to form a tough, protective oxide layer on the surface, and that layer can be a real pain to remove.
That’s why I always make sure to use a combination of mechanical and chemical cleaning methods when prepping stainless steel for welding. Sanding, grinding, and even pickling (using an acid solution) can help strip away that stubborn oxide and get down to the clean, bare metal. And when it comes to joint alignment, I’m even more meticulous – those tight tolerances are crucial to prevent cracking and porosity.
And then there’s aluminum. Now, this lightweight wonder metal has its own unique set of challenges. For one thing, it’s incredibly reactive, which means it can easily become contaminated by things like oil, grease, and even the moisture in the air. And that contamination can lead to all sorts of welding issues, from porosity to lack of fusion.
To combat this, I always make sure to use specialized aluminum-specific cleaners and degreasers. And when it comes to the actual welding process, I tend to favor TIG over other techniques, as the precise heat input and inert gas shielding can help me avoid those pesky contamination problems.
But that’s not all – aluminum also has a much lower melting point compared to steel, which means I have to be extra careful when it comes to joint alignment and fit-up. Too much of a gap, and I risk blowing through the base metal. Too tight, and I might end up with cracking or distortion. It’s a real balancing act, let me tell you.
The moral of the story? When it comes to these tricky materials, there’s no such thing as being too thorough with your metal preparation. It takes a bit more time and effort, sure, but trust me, it’s worth it in the end. After all, you can’t build a masterpiece without first laying a solid foundation, can you?
Putting It All Together
Alright, so we’ve covered a lot of ground here – from the importance of metal preparation to the specific techniques and challenges involved. But now it’s time to step back and look at the big picture. Because when it comes to welding, it’s not just about the individual steps – it’s about how all those pieces fit together to create a seamless, high-quality final product.
You see, metal preparation isn’t just a one-and-done kind of thing. It’s an ongoing process that needs to be carefully integrated into every stage of the welding project. From the initial assessment and cleaning, all the way through to the final shaping and alignment, it’s a constant cycle of evaluation and refinement.
And that’s where the true skill of the experienced welder really shines through. It’s not just about mastering the technical aspects of the job – it’s about developing that intuitive feel for how all the different elements work together.
Take joint design, for example. A skilled welder won’t just blindly follow a blueprint – they’ll actively assess the specific requirements of the project and adapt their preparation techniques accordingly. Maybe they need to bevel the edges a bit more to ensure proper penetration. Or perhaps they need to incorporate a specific clamping setup to maintain tight tolerances. It’s all about that keen eye for detail and the ability to think a few steps ahead.
And then there’s the matter of material selection. As we’ve discussed, different metals have different properties and characteristics, which means the preparation process needs to be tailored to each one. A one-size-fits-all approach just won’t cut it. The seasoned welder knows this, and they’re always on the lookout for ways to optimize their techniques to match the specific demands of the job.
At the end of the day, successful metal preparation is all about striking the right balance – between the art and the science, the theory and the practice. It’s about blending technical expertise with creative problem-solving, and always keeping that end goal in mind: a weld that’s as strong, durable, and aesthetically pleasing as it can possibly be.
And you know what? That’s the kind of welding I live for. The kind where I can take a raw slab of metal, wrangle it into submission, and transform it into something truly remarkable. It’s a challenge, to be sure, but it’s also an immensely rewarding one. Because when I step back and admire that flawless, shimmering weld, I know that I didn’t just slap some metal together – I created a masterpiece.
So if you’re a fellow welding enthusiast, or perhaps a curious newcomer to the trade, I encourage you to embrace the art of metal preparation. Dive in, get your hands dirty, and discover the joy of crafting that perfect foundation for your welding projects. Trust me, the payoff is well worth the effort.
And if you’re ever in need of some top-notch welding services, be sure to check out https://www.corrconnect.org/. We’re a team of seasoned professionals who take metal preparation as seriously as the welding itself. So whether you’ve got a simple repair job or a complex custom fabrication, we’ve got the skills and the know-how to make it happen. Drop us a line and let’s get started!