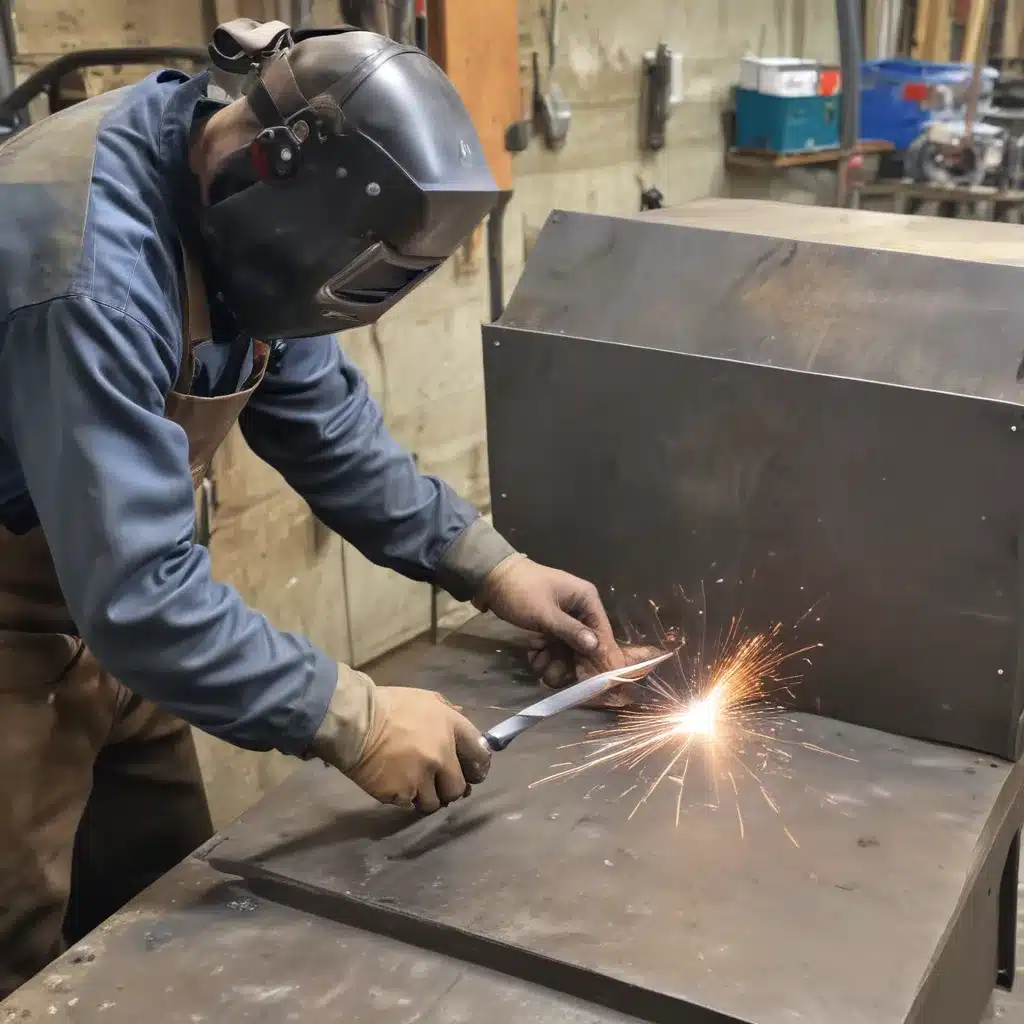
Introduction: The Vital Importance of Proper Preparation
As a beginner welder, I know how tempting it can be to just grab those welding rods, crank up the machine, and start fusing metal together. But let me tell you, my friends – that’s a surefire way to end up with some shoddy, half-baked results that’ll have you cursing like a sailor.
You see, the key to becoming a true welding maestro lies in the preparation. It’s the foundation upon which all your future welding triumphs will be built. And trust me, I’ve learned this the hard way. Back when I first started out, I thought I could just wing it and still produce gorgeous, show-stopping welds. Boy, was I in for a rude awakening.
My early welds looked like a kindergartener had gotten ahold of a welding torch and gone to town on a pile of scrap metal. Spatters everywhere, misaligned joints, you name it. It was a hot mess, let me tell you. But then I realized the error of my ways – I had completely neglected the all-important prep work.
From that moment on, I made a solemn vow to never, ever skimp on the preparation stage. And you know what? My welding skills skyrocketed. Suddenly, those welds were smooth, uniform, and practically artwork-worthy. All because I had taken the time to do things right from the start.
So if you’re a beginner welder, or even if you’ve been at it for a while but still struggle with inconsistent results, listen up. In this comprehensive guide, I’m going to walk you through the essential steps of material preparation, from cleaning and clamping to edge preparation and beyond. By the time we’re done, you’ll be a welding prep pro, ready to tackle any project that comes your way with confidence and precision.
Cleaning the Workpiece: The Key to a Flawless Finish
When it comes to welding, the old adage “cleanliness is next to godliness” couldn’t be more true. You see, any dirt, grease, or other contaminants on the surface of your workpiece can wreak absolute havoc on your weld.
Imagine trying to bond two pieces of metal together, but there’s a thin film of oil or rust in between them. It’s like trying to glue two slippery, oily surfaces – the bond just ain’t gonna happen. And even if you do manage to get a weld, it’ll be weak, porous, and prone to cracking down the line.
That’s why the first step in any welding prep work is to thoroughly clean the surface of your materials. Now, I know what you’re thinking – “But Curt, how the heck do I clean these pieces? Do I need some fancy, expensive industrial degreaser?”
Well, fear not, my fellow welding enthusiasts. There are plenty of simple, affordable ways to get those workpieces squeaky clean. For starters, you can’t go wrong with good old-fashioned soap and water. Grab a stiff-bristled brush, some detergent, and give those metals a good scrubbing. This’ll take care of any surface dirt, grease, or grime.
If you’re dealing with something a bit tougher, like rust or stubborn paint, you can step it up a notch with some chemical cleaners. Acetone, mineral spirits, and phosphoric acid-based products all work wonders for cutting through those nasty contaminants. Just be sure to follow the safety instructions and use these chemicals in a well-ventilated area.
And let’s not forget good old elbow grease. Sometimes, a little manual scrubbing with abrasive pads or wire brushes is all it takes to get that surface pristine and ready for welding. The key is to keep scrubbing until you can literally see your reflection in the metal.
Remember, the cleaner your workpiece, the better your weld will turn out. So don’t skimp on this step, my friends. Take the time to get those materials squeaky clean, and you’ll be well on your way to welding perfection.
Clamping and Fixturing: The Unsung Heroes of Welding Prep
Alright, now that we’ve got the cleaning out of the way, let’s talk about another crucial aspect of welding prep: clamping and fixturing. These might not be the most glamorous parts of the process, but trust me, they’re absolutely vital.
You see, when you’re welding, you’re dealing with some seriously high temperatures. We’re talking hundreds, even thousands of degrees Fahrenheit here. And that kind of heat can cause your workpieces to shift, warp, or even move right out of position if they’re not properly secured.
Imagine trying to weld two pieces of metal together, but they’re not clamped down tight. As soon as you strike that arc, those suckers are gonna start dancing all over the place, leaving you with a crooked, misaligned joint. And good luck trying to get a consistent, uniform weld on that mess.
That’s where clamping and fixturing come into play. By securing your workpieces in place with the right tools and techniques, you can ensure that they stay rock-solid during the welding process. This not only gives you better control over the final outcome, but it also helps prevent those pesky distortion issues that can ruin an otherwise flawless weld.
Now, there are all kinds of clamping and fixturing options out there – from simple C-clamps to specialized welding tables with built-in jigs and fixtures. The key is to choose the right tools for the job at hand. For smaller, simpler projects, a few well-placed C-clamps might do the trick. But for larger, more complex fabrications, you might need to bring in the big guns – heavy-duty welding tables, angle plates, or even custom-made fixtures.
And let’s not forget about tack welding, either. By strategically placing a few small tack welds around your joint, you can lock those workpieces in place and prevent any shifting or distortion. It’s like an insurance policy for your weld, ensuring that everything stays perfectly aligned from start to finish.
So don’t underestimate the power of clamping and fixturing, my friends. Take the time to set up your workpieces properly, and you’ll be rewarded with welds that are straight, uniform, and downright gorgeous. Trust me, your future self will thank you.
Edge Preparation: The Secret to Seamless Joints
Alright, now that we’ve tackled the cleaning and clamping aspects of welding prep, let’s move on to another crucial step: edge preparation. This might seem like a minor detail, but let me tell you, it can make all the difference in the world when it comes to the quality and appearance of your final weld.
You see, the edges of your workpieces play a huge role in how well the weld will penetrate and fuse the two pieces together. If those edges are all jagged, uneven, or improperly prepared, you’re just asking for trouble.
Imagine trying to weld two pieces of metal together, but the edges are all rough and uneven. As you strike that arc, the molten metal is going to struggle to flow smoothly between the gaps and irregularities, leaving you with a weld that’s full of voids, undercuts, and other unsightly defects.
But when you take the time to properly prepare those edges, magic happens. The weld pool will flow seamlessly, filling in all the gaps and creating a strong, uniform fusion between the two pieces. And the end result? A weld that’s not only structurally sound, but also downright beautiful to look at.
Now, there are a few different ways to go about edge preparation, depending on the thickness and type of material you’re working with. For thinner, lighter-gauge metals, a simple grinding or filing job might do the trick, rounding off any sharp edges and creating a nice, clean surface for the weld to latch onto.
But for thicker, heavier materials, you might need to step it up a notch with some more advanced techniques. That’s where things like beveling, chamfering, and joint preparation come into play. By carefully shaping and preparing the edges of your workpieces, you can create the perfect joint geometry for your particular welding application.
And let’s not forget about weld joint type, either. Depending on the structural requirements of your project, you might need to use a specific joint configuration, like a butt joint, lap joint, or T-joint. Each one has its own unique edge preparation requirements, so be sure to do your research and choose the right approach for the job.
Trust me, friends, taking the time to properly prepare those edges is gonna pay off big time in the long run. Your welds will be stronger, more consistent, and downright sexier than you ever thought possible. So don’t skimp on this step, and get ready to impress the socks off everyone who lays eyes on your handiwork.
Preheating and Interpass Temperature Control: The Secret Weapons of Welding Prep
Alright, now that we’ve covered the basics of cleaning, clamping, and edge preparation, let’s dive into a couple of more advanced welding prep techniques: preheating and interpass temperature control.
Now, I know what you’re thinking – “Preheating? Interpass temperature? That sounds like some fancy, high-tech stuff that’s way over my head as a beginner welder.” But trust me, my friends, these techniques are absolute game-changers, and they’re actually not that complicated to master.
Let’s start with preheating. Essentially, this involves heating up your workpieces to a specific temperature before you even strike that first arc. And the reason we do this is to help manage the heat input during the welding process.
You see, when you weld, you’re introducing a ton of heat into the metal. And if that heat isn’t managed properly, it can lead to all sorts of nasty issues, like distortion, cracking, and even solidification problems in the weld. But by preheating your workpieces, you can help control that heat input and ensure that everything stays nice and stable.
Imagine trying to weld two thick, heavy-duty steel plates together without any preheating. As soon as you strike that arc, the intense heat is gonna cause those plates to start warping and distorting like crazy. But if you’ve preheated those pieces ahead of time, the metal is already nice and toasty, so it can better withstand the additional heat input from the welding process.
And the benefits of preheating don’t stop there. It can also help improve the overall quality and structural integrity of your welds. By keeping the metal at an elevated temperature, you’re encouraging better fusion, less porosity, and a tighter, more uniform grain structure in the weld.
But preheating is just the tip of the iceberg when it comes to temperature control in welding. There’s also the whole concept of interpass temperature, which is all about monitoring and maintaining the temperature of the workpiece between successive weld passes.
You see, as you lay down weld after weld, that heat is gonna start building up in the metal. And if you’re not careful, that can lead to all sorts of problems, like excessive distortion, cracking, or even metallurgical changes that weaken the overall structure.
That’s where interpass temperature control comes into play. By carefully monitoring the temperature of the workpiece and making adjustments as needed, you can keep that heat in check and ensure that each weld pass is being laid down under optimal conditions.
Now, I know what you’re thinking – “But Curt, how the heck do I know what the right preheating and interpass temperatures should be?” Well, my friends, that’s where a little bit of research and planning comes in. Different materials, thicknesses, and welding processes will all have their own specific temperature requirements, so you’ll need to do your homework.
But trust me, once you get the hang of these temperature control techniques, your welding game is gonna be taken to a whole new level. Your welds will be stronger, more consistent, and downright bulletproof. So don’t be afraid to embrace the power of preheating and interpass temperature control – it’s like the secret weapon of the welding world.
Shielding Gas Selection: The Unsung Hero of Welding Prep
Alright, we’ve covered a lot of ground so far when it comes to welding prep, but there’s one more crucial element I want to talk about: shielding gas selection. Now, I know this might not seem as exciting as some of the other topics we’ve discussed, but trust me, this is a biggie.
You see, the shielding gas you choose for your welding process can have a huge impact on the quality, appearance, and even the structural integrity of your final weld. And as a beginner welder, it’s important to understand the different types of shielding gases and how they can affect your welding performance.
Now, the primary function of a shielding gas is to, well, shield the weld pool from the surrounding atmosphere. You see, when you’re welding, that molten metal is incredibly reactive, and it can easily get contaminated by oxygen, nitrogen, or other gases in the air. This can lead to all sorts of problems, like porosity, inclusions, and even embrittlement of the weld.
But by enveloping the weld pool in a protective shielding gas, you can keep those pesky atmospheric contaminants at bay and ensure that your weld turns out strong, pure, and flawless. And the type of gas you choose can have a big impact on the overall characteristics of your weld.
For example, let’s say you’re working with a MIG welding process. You might choose to use a shielding gas that’s primarily made up of argon, with a small percentage of carbon dioxide or oxygen added in. This combination can help you achieve a deep, penetrating weld with a nice, clean appearance.
On the other hand, if you’re doing some TIG welding on thinner materials, you might opt for a pure argon shielding gas. This will give you a more focused, controlled arc that’s perfect for precision work and delicate welds.
And the list goes on – there are all sorts of specialty shielding gas mixes out there, each with their own unique properties and applications. The key is to do your research, understand the different gas types, and choose the one that’s best suited for the specific welding job you’re tackling.
Now, I know what you’re thinking – “But Curt, how the heck do I know which shielding gas to use?” Well, my friends, that’s where a little bit of trial and error comes in. Start by experimenting with some of the more common gas mixes, and pay close attention to how they affect the appearance, penetration, and overall quality of your welds.
And don’t be afraid to ask for advice, either. Reach out to experienced welders, consult your equipment manufacturer, or even check with the folks at https://www.corrconnect.org/ – they’ve got a wealth of knowledge when it comes to all things welding.
Trust me, once you get the hang of shielding gas selection, your welding game is gonna be taken to a whole new level. Those welds will be stronger, cleaner, and downright sexier than you ever thought possible. So don’t sleep on this important aspect of welding prep – it could be the difference between a shoddy, amateurish weld and a work of art.
Conclusion: Embrace the Power of Proper Welding Preparation
Well, there you have it, my fellow welding enthusiasts – the essential steps of material preparation for the beginning welder. From cleaning and clamping to edge prep and temperature control, we’ve covered all the key elements that will help you take your welding skills to new heights.
Now, I know it might seem like a lot to remember, but trust me, once you get these techniques down, they’ll become second nature. And the payoff is well worth the effort, I can assure you. Imagine the look on your friends’ and family’s faces when they see the gorgeous, professional-grade welds you’re cranking out. It’ll be like watching a master chef whip up a Michelin-starred meal.
But the real satisfaction, of course, will come from the sense of pride and accomplishment you’ll feel every time you step back and admire your handiwork. There’s just something so deeply rewarding about taking the time to do things right, to sweat the small stuff, and to produce a final product that’s not just functional, but downright beautiful.
So don’t be afraid to dive in, my friends. Embrace the power of proper welding preparation, and let your inner welding artist shine. With a little practice and a whole lot of attention to detail, you’ll be churning out welds that’ll have everyone in awe.
And who knows – maybe one day, you’ll even be the one giving advice to the next generation of welding rookies, sharing the secrets of material prep that you’ve honed to perfection. The welding world is your oyster, my friends, so go out there and make it shine.